Procurement Glossary
Order management: definition, implementation & recommended software
Order management forms the backbone of efficient procurement and plays a key role in determining costs, delivery capability and customer satisfaction within the company. This structured overview shows you how to optimize your purchasing performance and achieve measurable success through systematic ordering processes.
Order management in a nutshell:
Order management comprises the systematic planning, implementation and control of all activities in connection with the procurement of goods and services. For Procurement , it is a central instrument for optimizing the ordering process, reducing process costs and ensuring the timely supply of materials.
Example: A medium-sized company implements a digital order management system that reduces the processing time for standard orders from an average of 3 days to 4 hours and cuts process costs by 65% by automatically triggering orders when stock levels fall below a defined minimum.
Order management: An introduction
Order management is a fundamental process in modern business management that involves the systematic planning, implementation and monitoring of ordering processes. It forms an important interface between Procurement, warehousing and supplier management. Efficient order management is crucial for optimizing the supply chain and ensuring a continuous supply of goods and materials. This introduction highlights the key aspects of order management, from basic concepts and modern technologies to practical implementation strategies and optimization options.
What is order management?
Order management comprises the planning, control and monitoring of all activities related to the procurement of goods and services in a company. It ensures that the required materials are available at the right time, in the right quantity and quality and at optimum cost. Effective order management optimizes procurement processes, reduces inventories and improves cooperation with supplier management.
Core elements of order management
Significance for Procurement
Order management is an essential part of the purchasing process and contributes significantly to a company's efficiency and competitiveness. Structured ordering processes can reduce costs, shorten delivery times and improve the quality of products and services. It also enables better control over expenditure and stock levels as well as a stronger negotiating position with suppliers.
Order management: from manual processes to e-procurement
Order management plays a decisive role in the control of procurement processes within a company. Building on the theoretical basis, which describes the process from determining requirements to invoice verification, practical implementation is becoming increasingly important. In today's business world, efficiency and speed are required, which necessitates a change from traditional to modern approaches in ordering.
Old: Manual ordering system
Traditional approach: In traditional order management, orders were often processed manually. Employees created purchase requisitions on paper or in simple spreadsheets. Supplier communication took place by phone, fax or email. This process was time-consuming and error-prone, as data had to be entered manually and recorded multiple times. The lack of system integration led to delays and a lack of transparency in the procurement process. Process costs were also high, as many resources were tied up in administrative tasks.
New: E-Procurement
E-procurement: With the modern approach of e-procurement, order management is digitized and automated. Companies use specialized software solutions that are integrated into their ERP systems to create, send and track orders electronically. Innovative technologies such as cloud computing and mobile applications enable location-independent access and real-time information. Standardization and automated workflows reduce errors and speed up processes. Practical benefits include a cost reduction of up to 30% in procurement, shorter lead times and better control over expenditure. The use of e-procurement also contributes to sustainability, as paper consumption is significantly reduced.
Practical example: Automotive industry
A large car manufacturer implemented an e-procurement system to optimize its ordering process. Digitization enabled orders to be generated automatically from production plans and sent directly to suppliers. This led to a 40% reduction in order processing time. Process costs fell by 25% as less manual intervention was required. In addition, supplier communication improved, resulting in a 15% reduction in delivery delays. Overall, the company achieved savings of over 10 million euros per year and significantly increased its efficiency in the supply chain.
Conclusion on the optimization of order management
Effective order management is a key success factor for companies today. The combination of digital processes, strategic supplier relationships and intelligent inventory management can reduce costs and increase efficiency. The trend towards complete digitalization and AI integration will further increase the opportunities for optimization. Companies should therefore make targeted investments in modern order management systems and the corresponding employee qualifications in order to secure their long-term competitiveness.
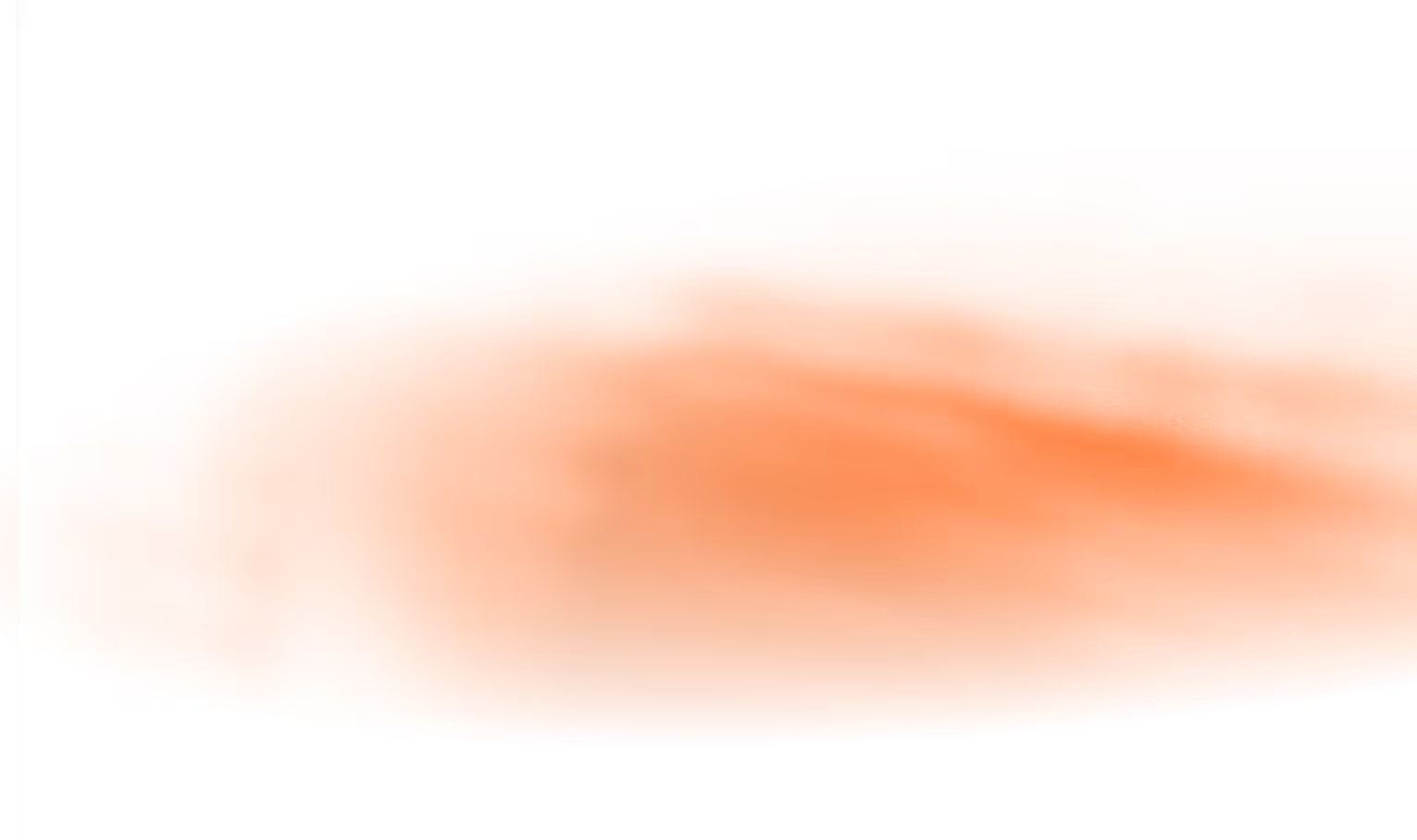
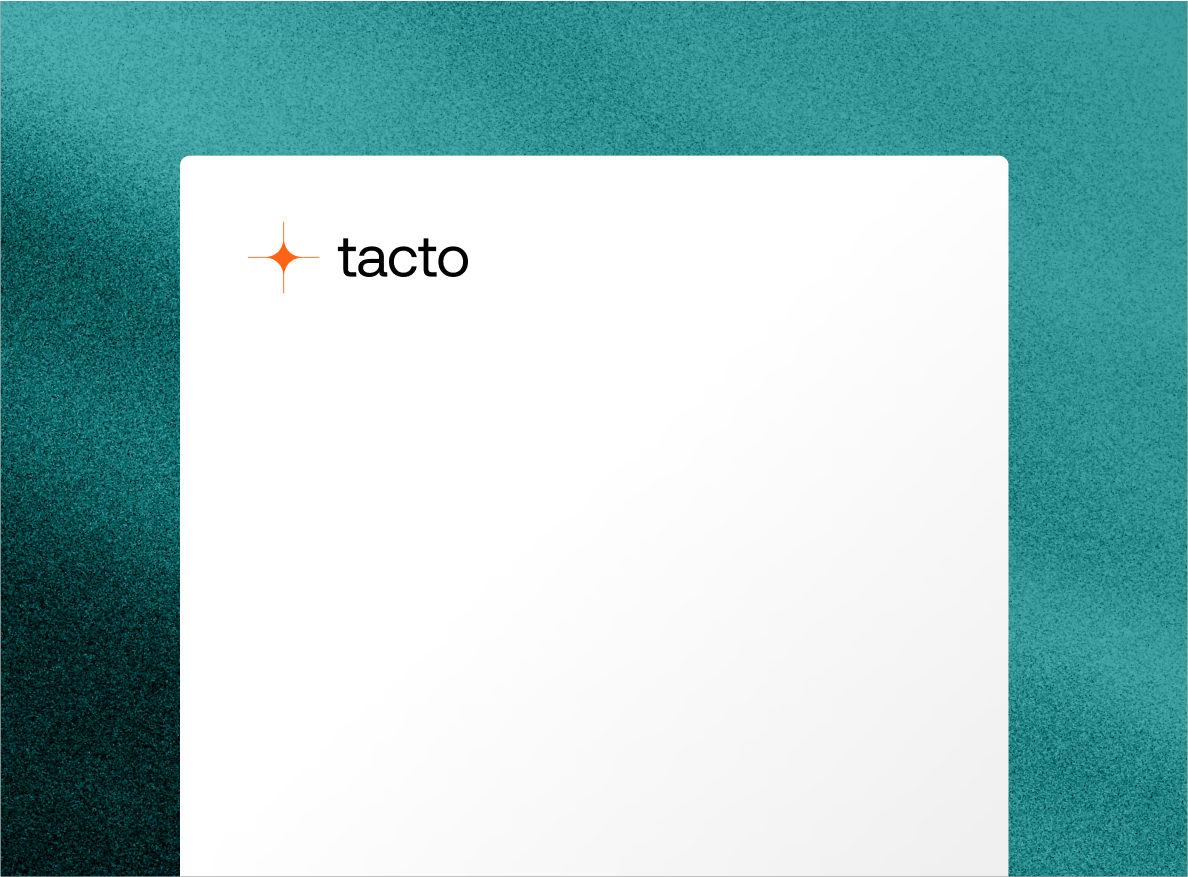