Procurement Glossary
Inventory management: definition & important aspects for buyers
Systematic inventory management not only ensures the availability of materials, but also forms the foundation for efficient business processes and cost savings. This structured overview shows you the most important methods and tools for optimal inventory management in Procurement and supports you in finding the right balance between security of supply and capital commitment.
Inventory management in a nutshell:
Inventory management is the systematic recording, monitoring and control of all available materials, components and finished products in the company. It is essential for Procurement in order to ensure security of supply and at the same time minimize capital commitment through optimal inventory levels.
Example: An automotive supplier uses a digital inventory management system to carry out daily checks on its 2,500 article items and has been able to reduce its average stockholding from 45 to 28 days, which means a cost saving of 120,000 euros per year.
Inventory management: An introduction
Inventory management is a fundamental component of modern company management and logistics. It deals with the systematic recording, monitoring and control of stock levels in a company. Efficient inventory management is crucial for optimizing warehousing costs, ensuring delivery capability and avoiding overstocks or bottlenecks. This introduction highlights the most important aspects of inventory management, from the basic concepts and various methods of inventory recording to modern digital solutions and their practical application in day-to-day business.
What is inventory management?
Inventory management refers to the systematic recording, monitoring and management of all of a company's stock. It includes the continuous documentation of goods movements - i.e. receipts and issues - as well as the updating of inventory data in real time. The main objective of inventory management is to ensure optimal stock levels in order to avoid both excess stock and stock shortages, thereby minimizing costs and ensuring delivery capability.
Core elements of inventory management
Significance for Procurement
Efficient inventory management is essential for Procurement in order to identify requirements in good time and optimally control procurement processes. It makes it possible to plan orders in line with demand, reduce storage costs and avoid supply bottlenecks. Accurate inventory data enables buyers to make informed decisions, develop strategic purchasing plans and make business processes more efficient overall.
Inventory management: from manual recording to real-time inventory management
Inventory management plays a decisive role in the efficiency and competitiveness of a company. Building on the theoretical basis, it enables not only the monitoring of stock levels, but also the optimization of procurement logistics processes. In practice, there is increasing pressure to manage inventory more accurately and quickly in order to reduce costs and meet customer needs. It is therefore essential to evolve from traditional to modern methods.
Old: Manual inventory management
Traditional approach: With manual inventory management, stock levels were recorded through regular physical inventories. Employees counted goods by hand and documented the data in paper form or simple spreadsheets. This method was time-consuming and prone to errors such as counting errors or transcription errors. In addition, delays in updating inventory data led to inefficiencies in procurement and production, as decisions were based on outdated information. Challenges such as high storage costs and a lack of transparency were therefore the order of the day.
New: Real-Time Inventory Management
Real-time inventory management: Modern inventory management systems use digital technologies to record and manage stock in real time. By using ERP systems linked to barcode scanners or RFID tags, goods movements are automatically recorded and immediately updated in the system. This enables precise monitoring of stock levels and a rapid response to changes. An innovative feature is the integration of IoT devices that trigger automatic orders when certain thresholds are reached. The benefits are a reduction in stock levels of up to 30%, minimized stock shortages and an improved supply chain through accurate forecasting.
Practical example: Automated inventory management in retail
A large retailer implemented a real-time inventory management system with RFID technology in its stores. This reduced inventory time by 90%, from 8 hours to less than 1 hour per store. Inventory accuracy increased to over 98%, resulting in a 5% increase in sales due to reduced stock-outs. In addition, the logistics costs were reduced by 15% as excess stock was identified and reduced at an early stage.
Conclusion on inventory management
Efficient inventory management is essential for modern companies. The combination of digital technologies, automated processes and precise analysis methods enables optimal inventory management, cost reduction and the ability to deliver. The trend towards AI-supported systems and IoT solutions will continue to revolutionize inventory management and open up new potential for optimization. However, careful implementation of the systems and continuous employee training remain crucial for success.
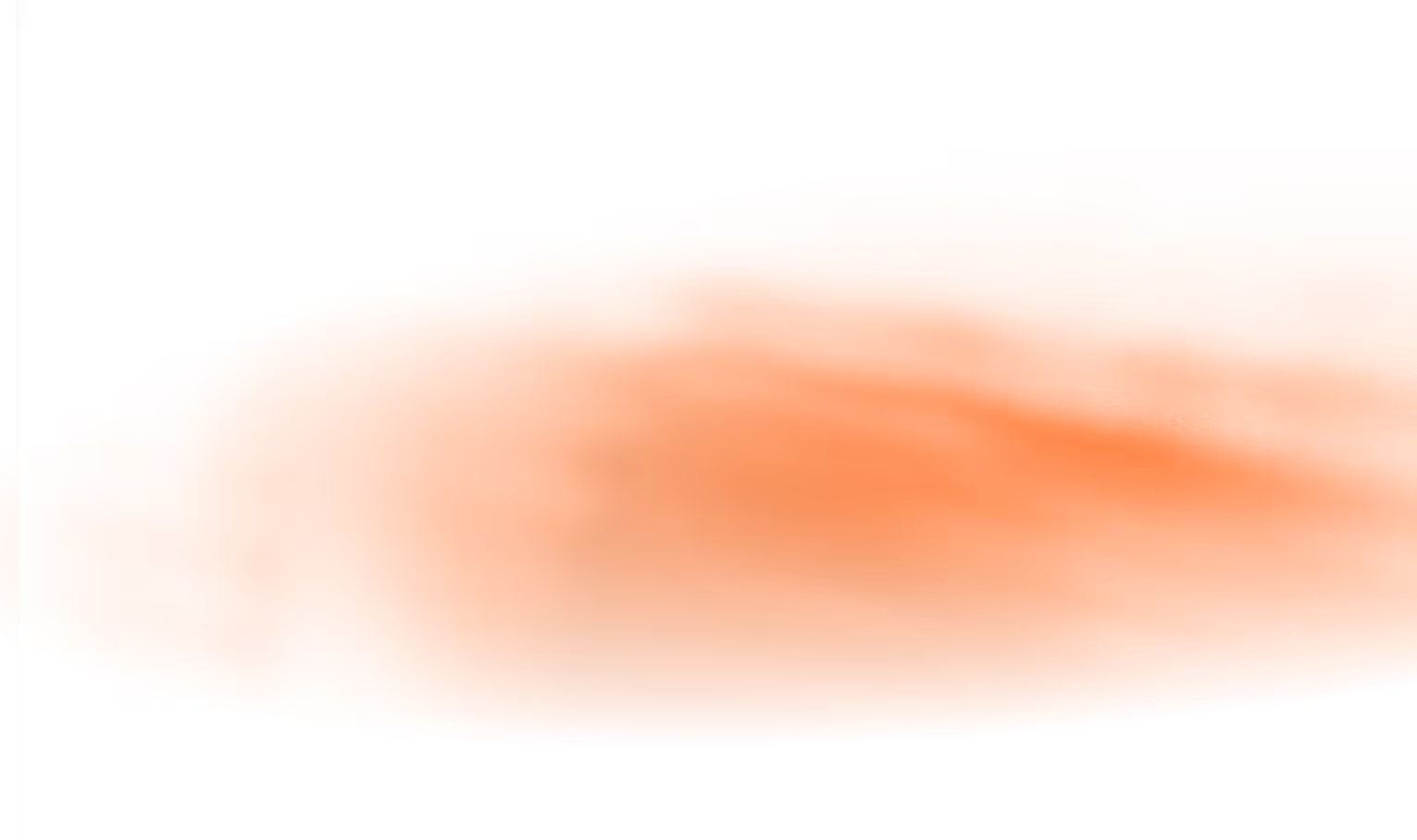
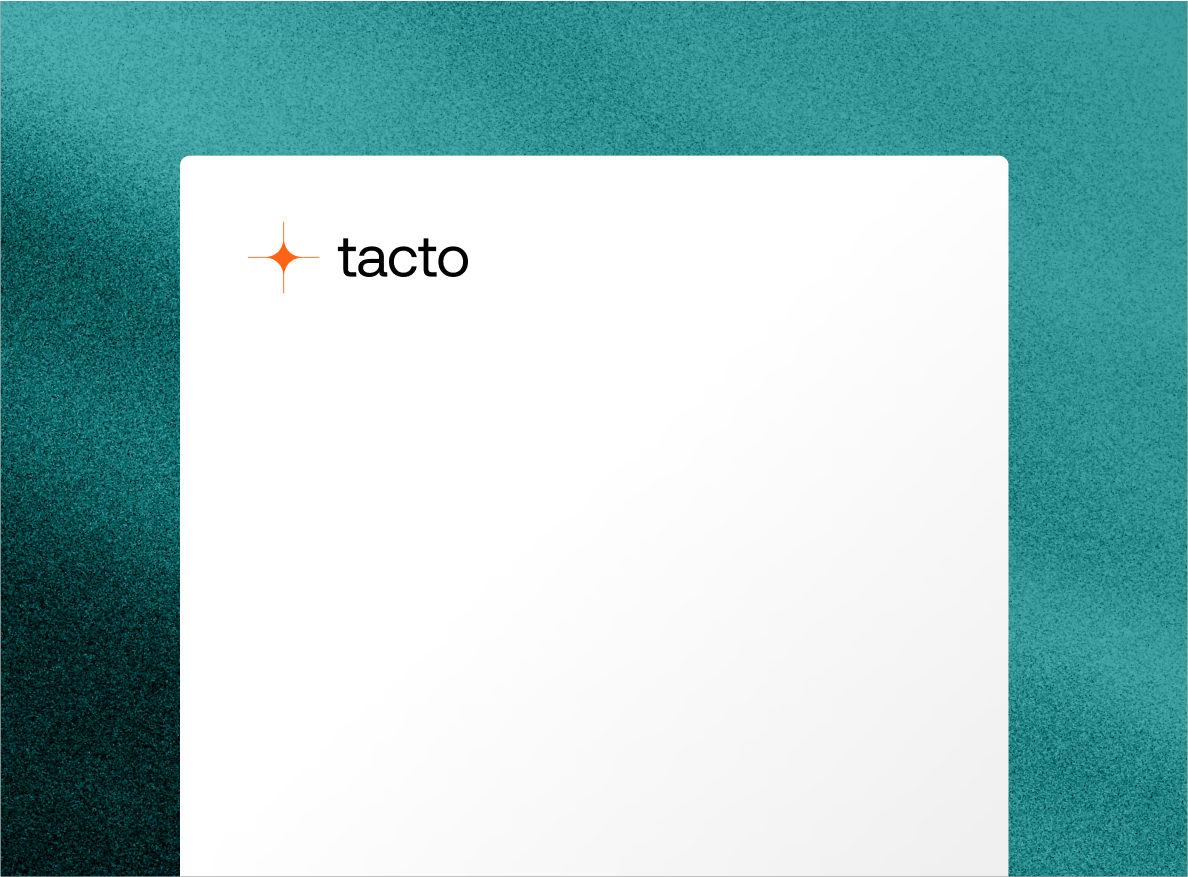