Procurement Glossary
Disposition in Procurement: definition, tasks & types
Material planning in Procurement is a fundamental process of operational procurement management and plays a central role in successful corporate management. It comprises the systematic planning, control and monitoring of material stocks and ordering processes in order to ensure an optimal supply for production or retail. In times of global supply chains and increasing market volatility, efficient replenishment is becoming increasingly important. This guide provides a comprehensive insight into the principles, methods and challenges of modern MRP planning as well as practical approaches to optimizing procurement processes.
What is scheduling in Procurement?
Procurement scheduling controls the optimal supply of materials and services and thus forms the backbone for smooth company processes.
- MRP refers to the systematic planning, control and monitoring of material flows and inventories in order to optimally cover production requirements.
- Scheduling is of central importance in the optimization of logistical, production and business processes.
- It is essential for Procurement in order to guarantee security of supply with minimal storage costs and to avoid production bottlenecks.
- Materials planning in Procurement ensures that the right materials are available in the right quantity at the right place at the right time.
Disposition in procurement
Tasks of scheduling in Procurement
The overarching task of scheduling in Procurement is to ensure the optimal supply and management of resources in a company in order to ensure that business and, in particular, production processes run smoothly. This includes the following tasks:
- Demand analysis: Determination of current and future material requirements based on sales forecasts and production plans
- Order planning: Determination of optimal order quantities and times, taking delivery times and storage capacities into account
- Inventory management: monitoring and control of stock levels to avoid bottlenecks and overstocking
- Supplier coordination: coordination with suppliers regarding delivery dates, quantities and quality assurance
Types of disposition
MRP can be divided into five different types. All of them are relevant for MRP in Procurement , but in particular material, goods and requirements-based MRP.
- Materials planning: management, planning and allocation of materials and raw materials for a smooth production process
- Goods disposition: distribution of preliminary products or goods for production or the end customer
- Financial planning: Management and allocation of financial resources in order to have sufficient capital for the operating business in all areas of the company
- Personnel scheduling: Planning and allocation of personnel in order to have enough employees in areas where they are needed
- Demand-driven scheduling: planning of material or resource requirements according to current and future demand
Importance of scheduling for Procurement
Materials planning is a central element in Procurement and makes a significant contribution to a company's efficiency and competitiveness. Effective replenishment enables purchasing processes to be optimized, costs to be reduced and delivery capacity to be increased. It makes it possible to react quickly to market changes and keep the supply chain stable.
- Cost optimization: Reduction of warehousing and procurement costs through needs-based planning
- Process reliability: Ensuring smooth production processes by avoiding material bottlenecks
- Competitive advantage: Increased responsiveness to customer requirements and market trends
Scheduling in Procurement: from manual planning to AI-supported scheduling
Scheduling in Procurement is at the heart of effective procurement management, and its practical implementation is crucial to a company's competitiveness. In a world of increasingly complex supply chains and growing market dynamics, traditional replenishment often no longer meets the requirements. A shift towards modern, automated approaches is therefore essential in order to increase efficiency and optimize costs.
Traditional approach: Manual disposition
- Determination of requirements by dispatchers using spreadsheets or simple ERP systems
- Based on historical consumption data and personal experience
- Manual definition of order quantities and times
- High personnel costs
- Limitations: Susceptibility to human error, lack of real-time data , limited responsiveness to short-term market changes and safety stock levels often led to increased inventory costs
New: AI-supported scheduling
- Artificial intelligence to make demand forecasts more precise and efficient
- Integration of real-time data from various sources such as sales, production and inventory
- Dynamic adjustment of order quantities and times by the AI
- Self-learning algorithms that recognize consumption patterns and plan ahead for future needs
- Advantages: Reduction of stock levels by up to 30%, faster response times to market changes and minimization of supply bottlenecks
Practical example: Automotive industry
A leading automotive manufacturer implemented an AI-supported scheduling system in its purchasing purchasing controlling. By analyzing real-time consumption data and taking into account external factors such as supplier reliability and market trends, the company was able to reduce its inventory levels by 25%. At the same time, the rate of material shortages fell by 40%. The more efficient scheduling led to cost savings of over 15 million euros annually and significantly increased flexibility within the supply chain.
Conclusion on disposition in Procurement
Material planning in Procurement is an indispensable strategic process for a company's success. Precise planning and control of material procurement not only optimizes costs and secures production processes, but also strengthens competitiveness. Increasing digitalization and AI-supported solutions are opening up new opportunities for even more efficient and forward-looking planning. The balance between security of supply, cost efficiency and flexibility in inventory management remains crucial.
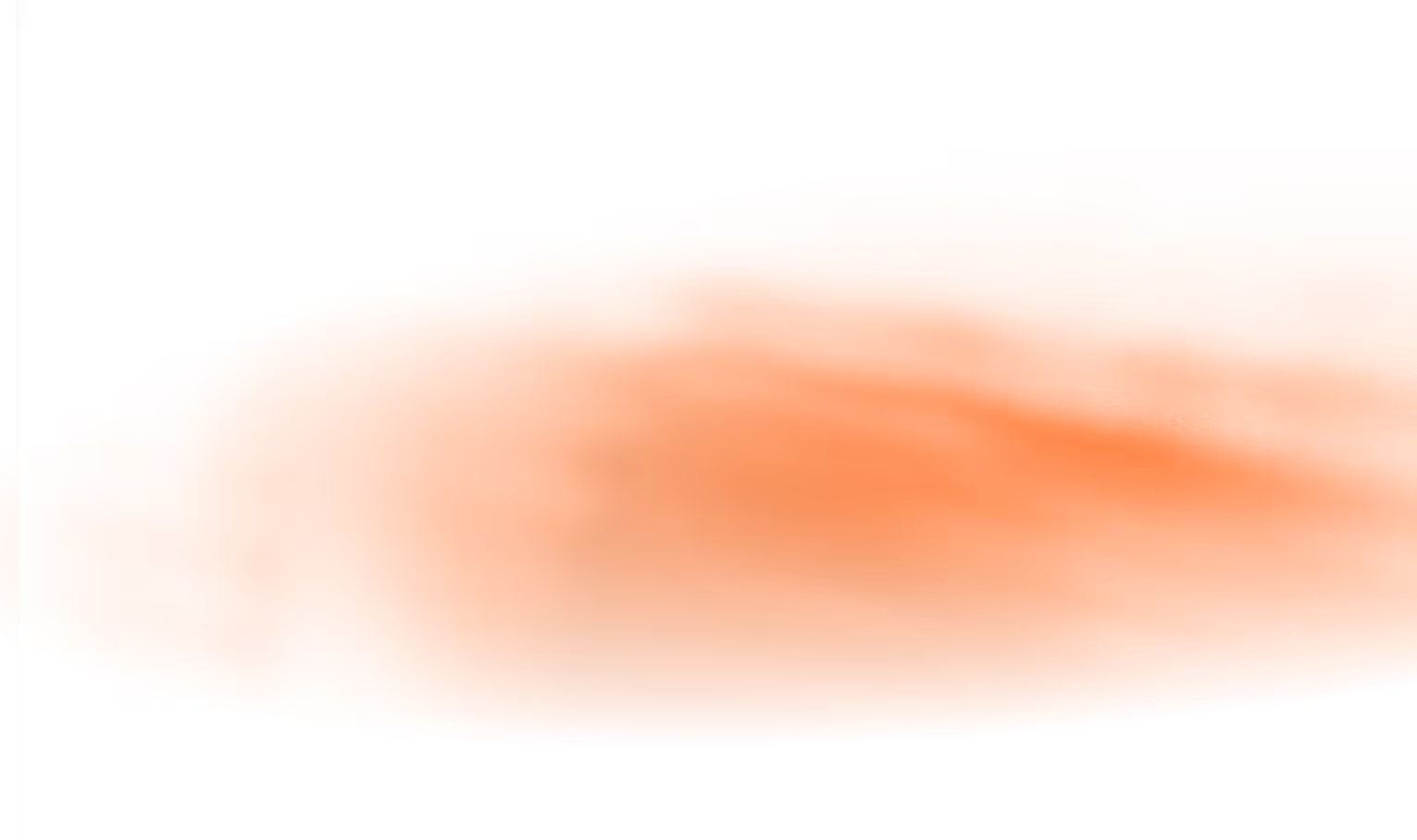
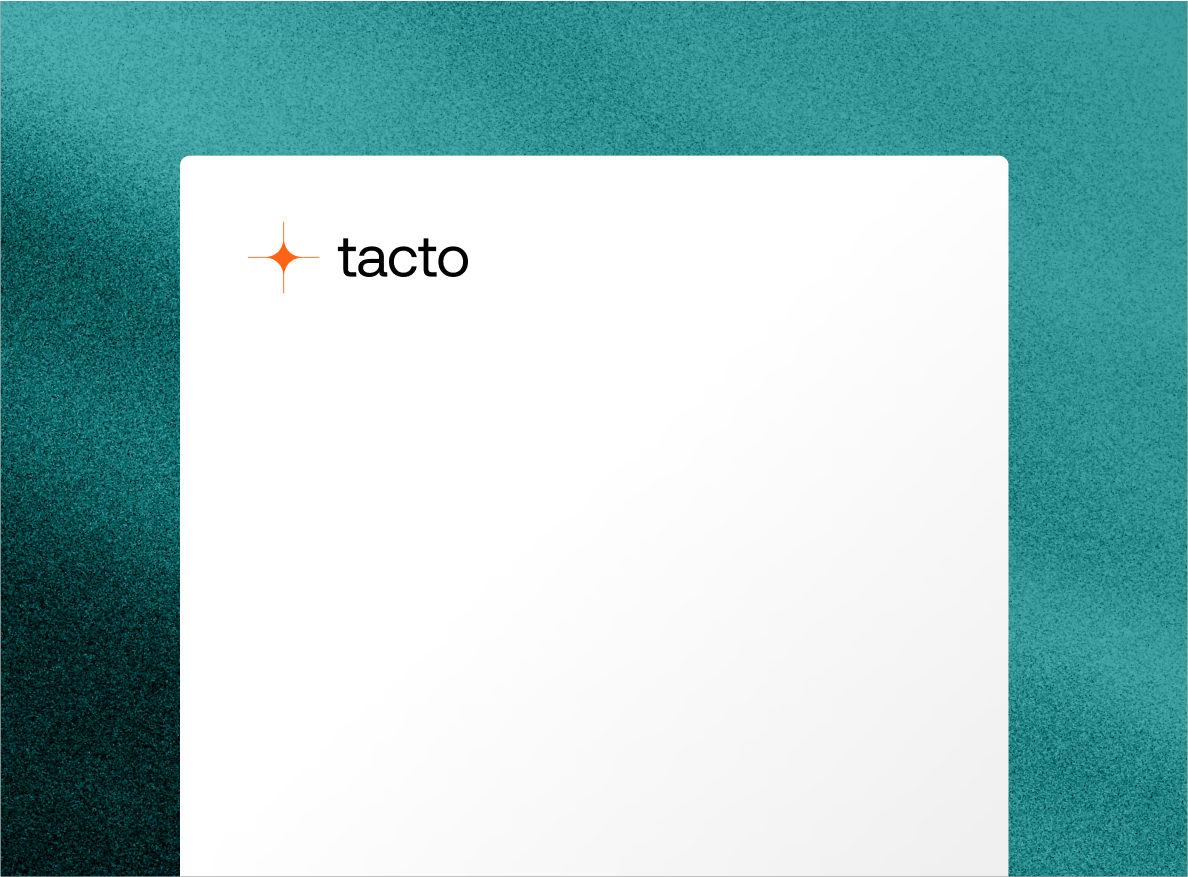