Procurement Glossary
In-house production depth: definition & important aspects for buyers
The depth of in-house production has a decisive impact on the company's success and influences key make-or-buy decisions as well as strategic positioning on the market. This structured overview shows how Procurement can find the optimal balance between in-house production and external procurement, thereby securing competitive advantages.
In-house production depth in a nutshell:
The in-house production depth describes the percentage of added value that a company generates itself in relation to the total added value of a product. For Procurement , this is a key indicator for make-or-buy decisions and strategic supplier selection.
What proportion of the added value should I create myself? What is the optimum in-house production depth? And what influence does the in-house production depth have as a key figure for future make-or-buy decisions?
Find out more in our white paper: Optimal in-house production depth - Strategic decision-making aid for production companies
Introduction to in-house production depth
In-house production depth, also known as vertical integration or value added depth, is an important strategic parameter in the production industry. It describes the share of a company's own value added in the total value of a product and is therefore a decisive indicator for the vertical integration of a company. Determining the optimal in-house production depth is a complex business decision that has far-reaching effects on costs, quality and flexibility. This paper takes a closer look at the various aspects of in-house production depth, its significance for corporate management and current trends and challenges.
What is the in-house production depth?
In-house production depth refers to the proportion of value added that a company generates itself through its own production processes instead of sourcing parts or services from external suppliers. It provides information on how much a company produces internally and how much it relies on external suppliers. A high in-house production depth means that many production steps take place in-house, while a low depth indicates greater outsourcing of processes.
Core elements of in-house production depth
Significance for Procurement
For Procurement , in-house production depth has a significant impact on procurement strategies and supplier relationship management. A change in vertical integration requires adjustments in supplier selection, contract design and supply chain management. Buyers must weigh up which components are strategically important and whether in-house production or purchasing offers advantages.
In-house production depth: from complete in-house production to agile value creation networks
Building on the theoretical understanding of in-house production depth, it becomes clear how decisive the design of value creation depth is for a company's success. In practice, it directly influences a company's flexibility, cost structure and ability to innovate. The shift from traditional production models to modern approaches reflects the need to adapt to dynamic market conditions and increasing customer requirements.
Old: Complete in-house production
Traditional approach: Historically, many companies relied on a high level of in-house production and produced as many components as possible internally. This gave them full control over quality, delivery times and proprietary technologies. Typical features of this approach were extensive investments in in-house production facilities and personnel. However, this led to high fixed costs, low flexibility and difficulties in adapting quickly to market analysis. In addition, innovation was often limited by internal capacity constraints.
New: Agile Supply Networks
Agile supply networks: The modern approach reduces in-house production depth in favor of flexible value creation networks. Companies focus on their core competencies and cooperate with specialized partners for other production steps. The use of digital technologies and real-time data makes supply chains more transparent and efficient. This leads to increased agility, cost savings and the ability to react quickly to market trends. Innovation can be accelerated through access to external expertise, while risk management is better distributed.
Practical example: Automotive industry
A leading car manufacturer has significantly reduced its in-house production depth by outsourcing the production of components such as electronic systems and seats to specialized suppliers. This strategy enabled the company to reduce its fixed costs by 20% and make production more flexible. The time-to-market for new models was reduced by 25%, giving the company a competitive advantage. The manufacturer also benefited from innovations from partner companies, which increased vehicle quality and customer satisfaction.
Conclusion on in-house production depth
In-house vertical integration is a key strategic tool for companies that determines the balance between internal production and external sourcing. Optimal vertical integration requires careful analysis of costs, core competencies and market requirements. While high in-house production depths offer more control and know-how protection, lower depths enable greater flexibility and cost savings. Success lies in the dynamic adaptation of vertical integration to changing market conditions and technological developments.
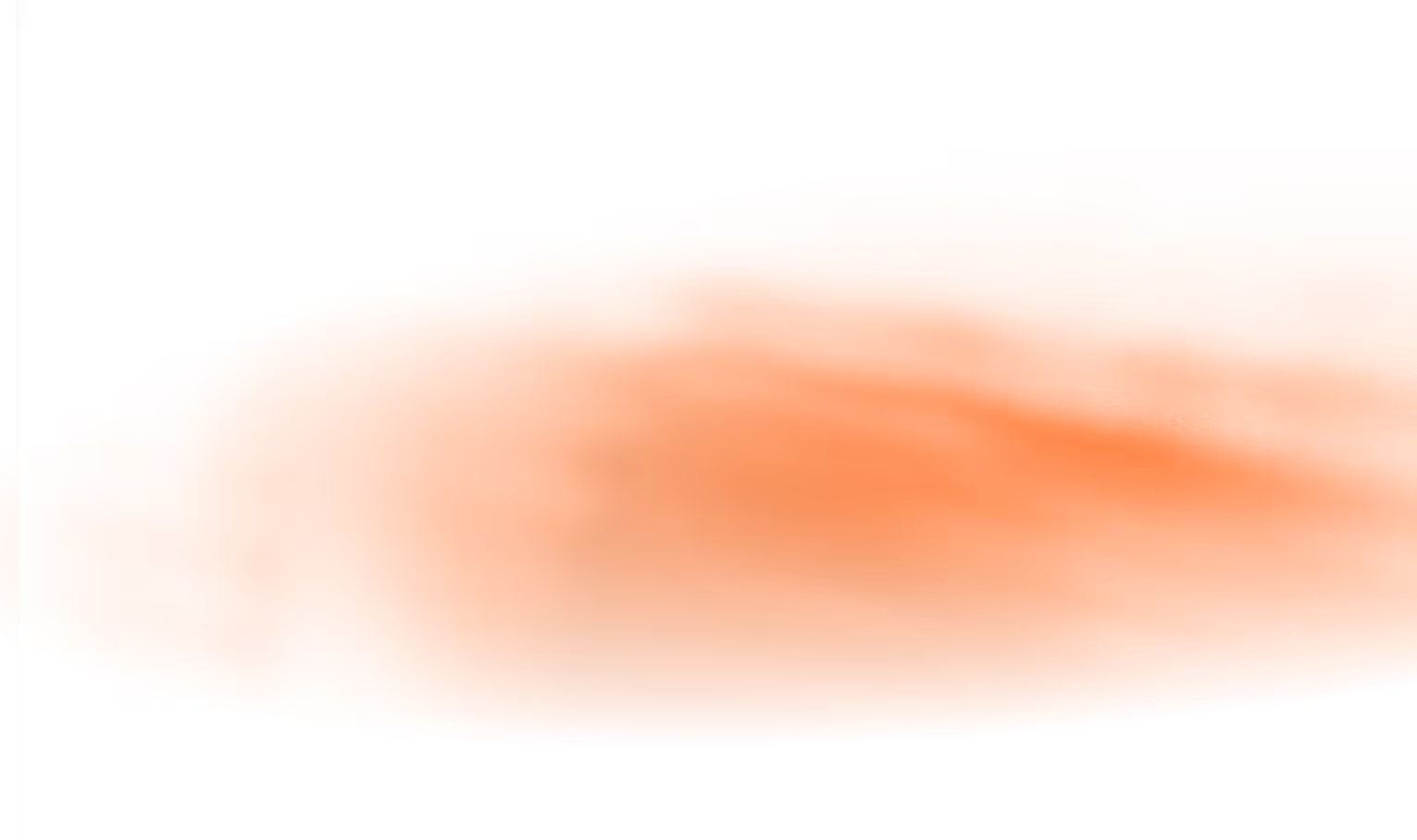
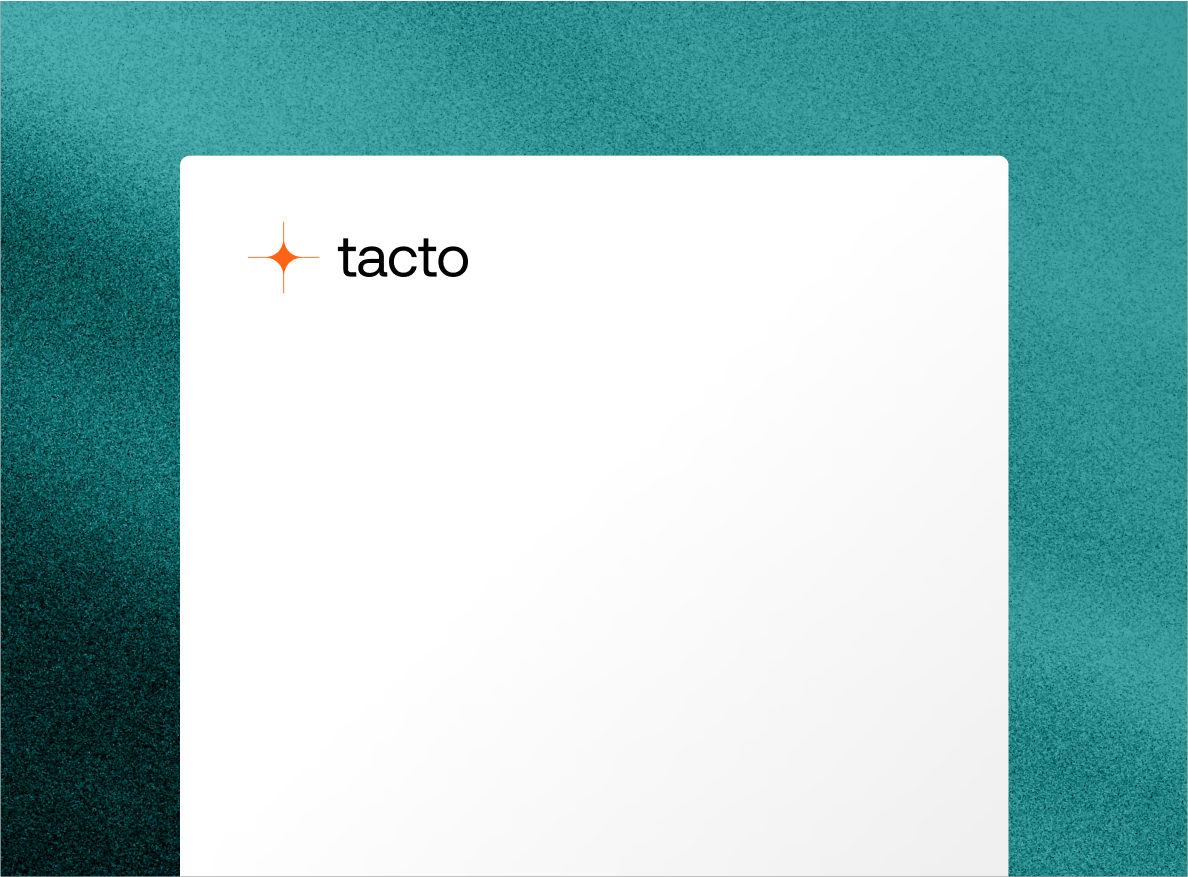