Procurement Glossary
Consignment stock: definition and important aspects for buyers
Imagine having a fully stocked warehouse on site, but only having to pay for it when you actually use the materials - this is exactly the principle of a consignment warehouse. This modern form of warehousing is revolutionizing traditional procurement by combining the advantages of high material availability with optimized working capital. For purchasers, this opens up a clever opportunity to increase their security of supply and at the same time reduce the amount of capital tied up.
What is a consignment warehouse?
A consignment warehouse is a physical warehouse on the customer's premises in which the supplier holds goods for its own account and at its own risk. The transfer of ownership and invoicing only takes place when the goods are actually removed by the customer. The stored materials remain the legal property of the supplier until they are consumed, while the customer has physical control and direct access to the goods.
Introduction to the consignment warehouse
In strategic Procurement , consignment warehouses are an important tool for optimizing the supply chain and working capital. For the procuring company, this model offers the advantage of high material availability with a simultaneous reduction in capital commitment, as payment is only made when the material is actually consumed. In return, the supplier benefits from close customer loyalty and can optimize its production and delivery planning through direct consumption data. Clearly defined processes for stock management, withdrawal bookings and invoicing as well as a transparent agreement on minimum stock levels, subsequent deliveries and potential excess stock are crucial to success. Modern IT systems and automated reporting systems support efficient processing and ensure the necessary transparency for both parties.
Advantages and disadvantages of consignment warehouses
Advantages for the buyer:
- Optimized working capital through later invoicing and payment, as ownership is not transferred until the goods are removed.
- Increased supply security thanks to guaranteed material availability directly on site, which minimizes supply bottlenecks.
- Reduced process costs, as ordering procedures, incoming goods inspections and storage processes are simplified.
- Reduced storage risks, as quality defects and obsolescence remain with the supplier until removal.
Advantages for the supplier:
- Stronger customer loyalty through closer integration into the customer's supply chain.
- Better planning thanks to a direct view of consumption data and inventory trends.
- Possibility to optimize your own production through improved demand forecasts.
Disadvantages for the buyer:
- Higher administrative effort for inventory management and withdrawal postings.
- Need for suitable storage space and corresponding infrastructure.
- Responsibility for proper storage and safety of goods.
Disadvantages for the supplier:
- Longer capital commitment due to later transfer of ownership.
- Increased risk due to lack of direct control over the stored goods.
- More complex accounting and inventory processes for externally stored inventories.
The decision for or against a consignment warehouse should therefore be made after careful consideration of these aspects and taking into account the specific situation of both parties.
Decisive factors for or against consignment warehouses
Material characteristics:
- High and regular consumption of the material
- Stable products with a low risk of obsolescence
- Standardized items with good shelf life
- Critical materials with high importance for production
supplier relationship:
- Long-term, stable partnership
- Sufficient financial stability of the supplier
- Readiness for procedural and technical integration
- Geographical proximity for efficient subsequent deliveries
Internal requirements:
- Available and suitable storage space
- IT systems for inventory management and withdrawal bookings
- Clear processes for goods withdrawal and posting
- Qualified personnel for warehouse processing
Economic aspects:
- Significant optimization potential for working capital
- Sufficient material volume for profitability
- Proportionate process and implementation costs
- Measurable advantages in the total cost view
Legal and organizational framework conditions:
- Clear contractual regulations possible
- Clear responsibilities can be defined
- Insurance cover provided
- Compliance requirements can be met
The introduction of a consignment warehouse makes particular sense if the majority of these factors can be assessed positively and both parties can clearly benefit from the implementation.
Consignment warehouse: from traditional model to vendor managed inventory
The consignment warehouse has long been a tried and tested concept for ensuring the security of supply and reduce capital commitment. In practice, it enables companies to access materials immediately without having to purchase them in advance. In view of advancing digitalization and increasing demands on supply chains however, it is becoming clear that traditional models are reaching their limits. A transformation towards more efficient and integrated approaches such as Vendor Managed Inventory is therefore necessary in order to remain competitive.
Old: Traditional consignment warehouse
In traditional consignment warehouses, goods are stored at the customer's premises but remain the property of the supplier until they are removed. The customer reports its consumption manually or periodically to the supplier, who then replenishes the stocks. This process is often characterized by manual data exchange, telephone coordination or simple e-mail communication. The lack of real-time transparency leads to challenges such as overstocking, stock shortages and increased administrative effort. In addition, manual recording leads to errors that impair efficiency.
New: Vendor Managed Inventory (VMI)
The modern VMI approach integrates suppliers closely into the customer's warehousing processes. The use of electronic data interchange (EDI) and networked IT systems gives the supplier real-time access to inventory and consumption data. This enables proactive control of replenishment processes, with the supplier taking responsibility for inventory optimization optimization. Automated ordering processes reduce administrative effort and minimize the risk of stock shortages or overstocking. The increased transparency strengthens cooperation and promotes a strategic partnership between both parties.
Conclusion on the use of consignment warehouses
Consignment warehouses are an effective tool for companies to optimize their material supply and improve working capital at the same time. Although they require a certain amount of administrative effort and clear process structures, they offer significant strategic advantages for both buyers and suppliers through closer cooperation and improved planning. Successful implementation depends largely on the careful selection of suitable materials and suppliers as well as the professional design of operational processes. In times of increasingly complex supply chains, consignment warehouses are therefore gaining in importance as a strategic tool in modern supply chain management.
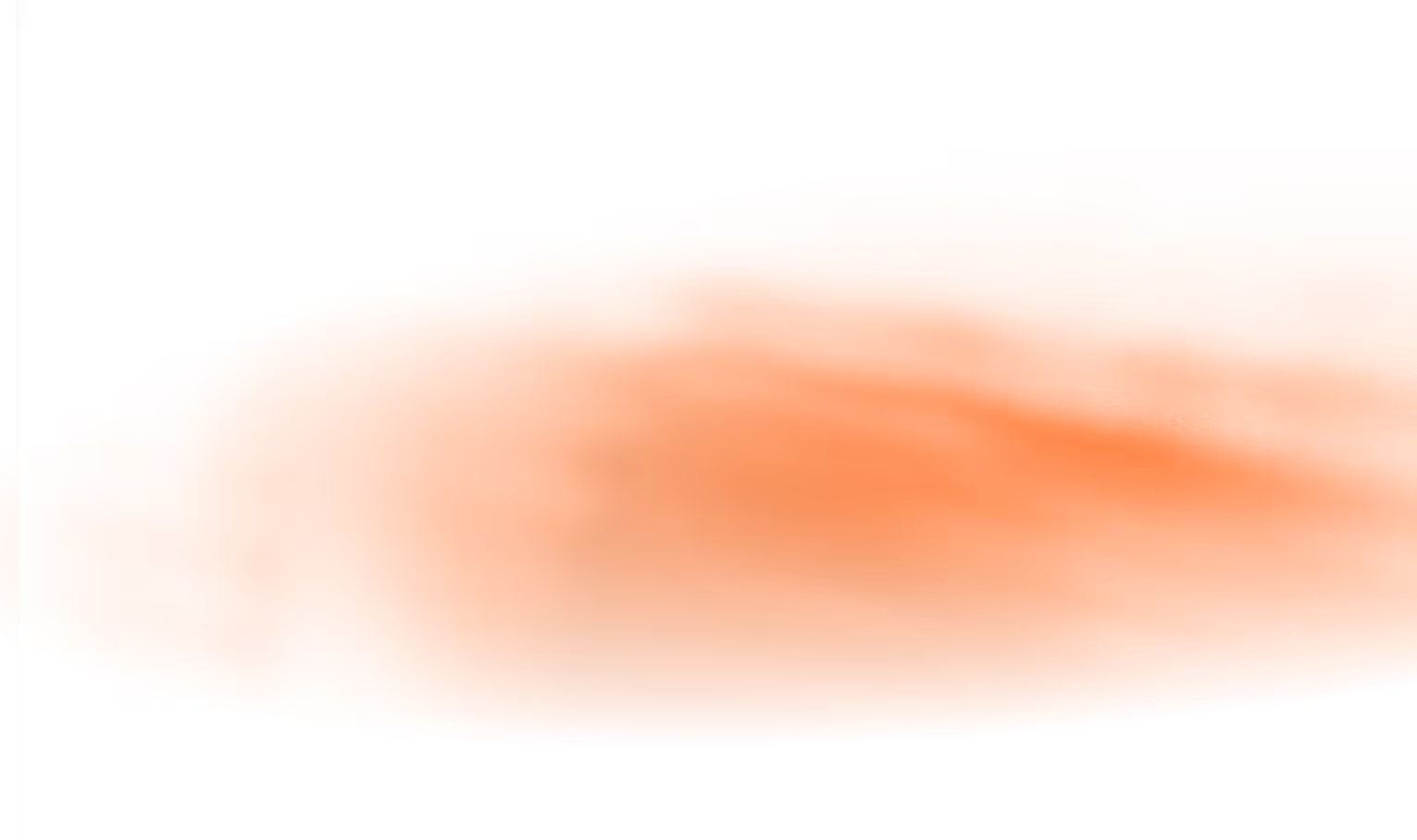
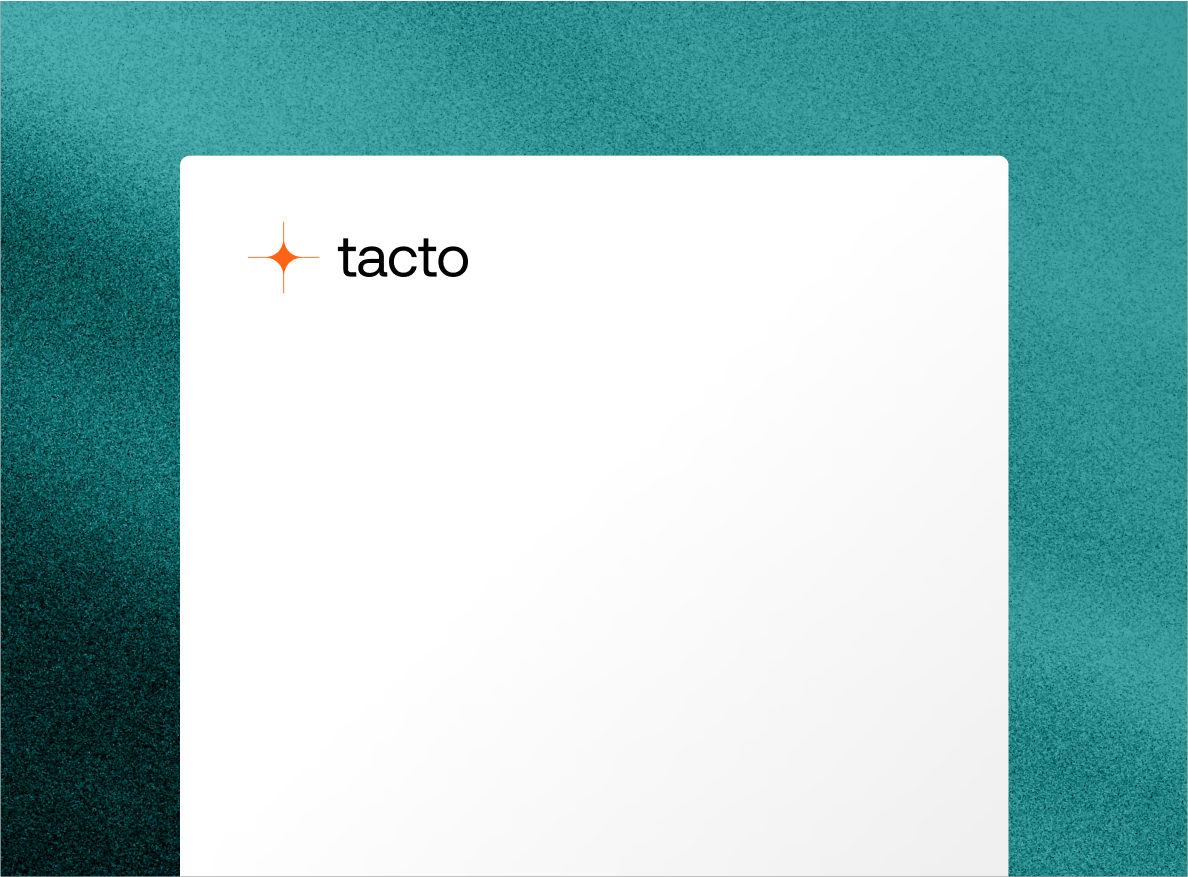