Procurement Glossary
Delivery capability: definition & important aspects for buyers
The ability to deliver is crucial to the success of the entire value chain and is becoming increasingly strategically important in volatile markets. This structured overview shows you the most important levers and methods that you as a buyer can use to sustainably improve your company's security of supply.
Delivery capability in a nutshell:
Delivery capability describes the ability of a supplier to provide ordered goods in the desired quantity and quality at the agreed time. For Procurement , it is a key performance indicator in supplier selection and evaluation, as it directly influences security of supply and production stability.
Example: An automotive supplier achieves a delivery capability of 98.5% by delivering 197 of 200 order items per month on time, in full and in the required quality, which is documented by monthly supplier performance monitoring.
Delivery capability - An introduction
Delivery capability is a key performance indicator in modern corporate management and logistics. It describes a company's ability to fulfill customer orders on time and in the desired quantity and quality. In times of global supply chains and rising customer expectations, optimizing delivery capability is becoming increasingly important. A high delivery capability contributes significantly to customer satisfaction and is an important competitive factor. This guide takes a closer look at the various aspects of delivery capability, their measurement and optimization options, as well as the challenges involved in practical implementation.
What is meant by delivery capability?
Supply capability refers to the ability of a supplier or manufacturer to deliver products or services on time, in the desired quantity and quality. It is a key criterion for the performance and reliability of a supplier and has a significant influence on the efficiency of the entire supply chain. A high level of supply capability ensures that business processes run smoothly and customer requirements can be met.
Core elements of delivery capability
Importance of delivery capability in Procurement
For the Procurement the delivery capability of a supplier management system is crucial in order to ensure a reliable supply and avoid production downtimes or delays. A high delivery capability contributes to the optimization of stock levels, reduces costs by minimizing rush orders and strengthens the company's competitive position through increased customer satisfaction.
Delivery capability: from traditional planning to real-time transparency
The ability to deliver is a decisive competitive factor that can determine the success or failure of a company. While static planning processes were previously used to ensure delivery capability, today's dynamic market situation requires more flexible approaches. In order to meet the increasing demands and at the same time increase efficiency and customer satisfaction, a change from traditional methods to modern, data-driven solutions is necessary.
Old: Traditional requirements planning
Traditional approach: In traditional practice, supply capability was based on long-term demand forecasts and high safety stock levels. Companies used historical sales data to plan future demand analysis, but this often led to inaccuracies. Manual coordination with suppliers was time-consuming and delays in communication could quickly lead to supply bottlenecks or overstocks. There was also a lack of transparency along the supply chain, which limited the ability to react to unexpected events.
New: Real-time supply chain management
Real-time supply chain management: Modern approaches rely on the integration of real-time data and advanced technologies to improve supply capability. By using IoT devices, cloud platforms and artificial intelligence, companies can monitor their supply chains in real time. This enables proactive adaptation to changes in demand and potential disruptions. Automated processes and close collaboration with suppliers increase transparency and reduce lead times. As a result, stock levels can be optimized and delivery times shortened, which ultimately increases customer satisfaction.
Practical example: Digitalization in the electronics industry
A global electronics manufacturer implemented a real-time supply chain management system that significantly increased its ability to deliver. By networking all suppliers and monitoring stock levels in real time, the company was able to reduce delivery times by 40%. At the same time, stock levels fell by 25%, resulting in cost savings of several million euros. The adherence to delivery dates for customer deliveries rose to 99%, which contributed to improved customer satisfaction and an increase in market share.
Conclusion on delivery capability
Delivery performance is a key success factor in modern Procurement and supply chain management. Systematic monitoring, clear key figures and digital solutions allow delivery performance to be continuously monitored and improved. A high delivery capability not only reduces costs and risks, but also strengthens the company's competitive position. For forward-looking companies, the integration of AI and blockchain technologies is becoming increasingly important in order to further optimize supply capability and ensure transparency in the supply chain.
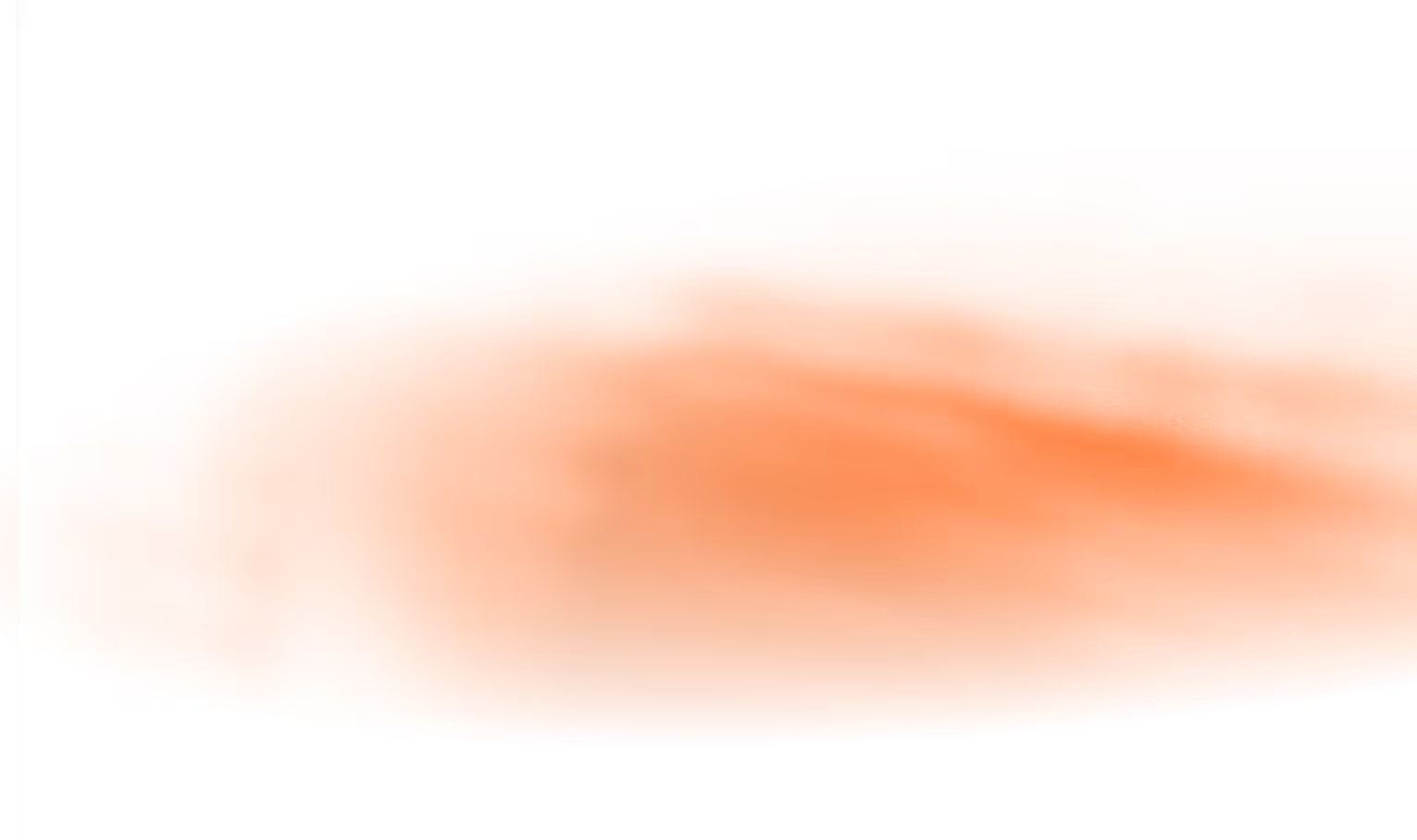
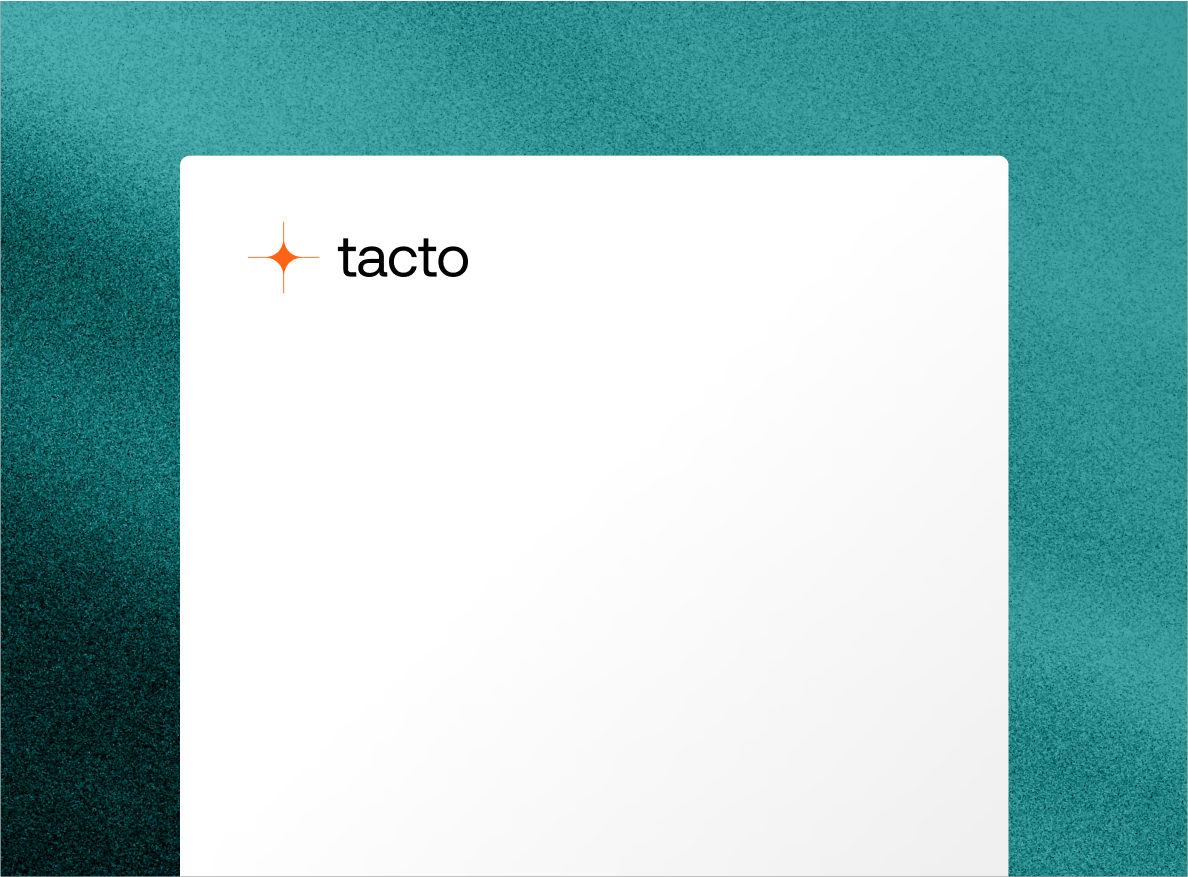