Procurement Glossary
Delivery schedule: Definition & important aspects for buyers
A delivery schedule controls the timely supply of materials and creates planning security for suppliers and customers in the supply chain. This structured overview shows how you as a buyer can ensure security of supply and reduce costs at the same time by optimizing your delivery schedule.
Delivery schedule in a nutshell:
A delivery schedule is a binding agreement between the buyer and supplier on quantities and dates of recurring material deliveries over a defined period of time. For Procurement , this enables optimized inventory planning, reduced administrative costs and a secure supply with simultaneous flexibility of call-offs.
Example: An automotive supplier agrees a 12-month delivery schedule with its steel supplier with weekly deliveries of 2,000 kg of sheet steel each, whereby the specific call-off quantities can be adjusted up or down by up to 20% and the binding purchase quantity is fixed 4 weeks in advance.
Introduction to the delivery schedule
The delivery schedule is an essential tool in modern supply chain management and production planning. It defines binding quantities and deadlines for the delivery of materials, components or finished products between suppliers and customers. In the increasingly globalized and networked business world, precise delivery planning is becoming more and more important, as it contributes significantly to optimizing warehousing, reducing production interruptions and improving the cost situation. In this guide, you will learn about the most important aspects of supply planning, from the basics to modern digital solutions and practical implementation strategies.
What is a delivery schedule?
A scheduling agreement is a long-term framework agreement in Procurement between a buyer and a supplier for the delivery of goods or services in specified quantities and at specified times. Instead of placing individual orders, materials or products required on a regular basis are procured by call-off order via the scheduling agreement. This enables a continuous supply, improves planning reliability and reduces the administrative effort involved in the procurement process.
Core elements of a delivery schedule
Importance of scheduling agreements in Procurement
In strategic Procurement , scheduling agreements are an essential tool for optimizing procurement processes. They increase efficiency by reducing administrative effort and enabling better cost control. Thanks to long-term planning, companies benefit from more stable supply relationships, volume discounts and improved security of supply. In addition, delivery schedules promote cooperation with suppliers and help to minimize risk.
Delivery schedule: From manual planning to digital real-time control
Building on the understanding of the scheduling agreement as a long-term framework agreement, its practical implementation is crucial for efficient procurement processes. The supply plan ensures a continuous supply of materials, reduces stock levels and strengthens collaboration with suppliers. However, with increasing market volatility and complex supply chains, there is a need to move from traditional to modern, digital methods.
Old: Manual scheduling agreement processing
Traditional approach: Traditionally, delivery schedules were created and managed manually. Dispatchers created demand forecasts at regular intervals based on historical data and updated these in spreadsheets. Communication with suppliers took place by telephone, fax or e-mail. Changes in requirements were often transmitted with a delay, which led to over- or under-deliveries. Manual data entry was prone to errors and the lack of real-time information made it difficult to react flexibly to market changes. In addition, the increased administrative effort led to high process costs and longer lead times.
New: Automated scheduling agreement control with EDI
Electronic Data Interchange (EDI): Modern companies rely on automated delivery schedule processes using EDI. By electronically linking the ERP systems of buyers and suppliers, demand data is exchanged in real time. Delivery call-offs, confirmations and change notifications are carried out automatically, which considerably shortens response times. EDI minimizes manual intervention, reduces errors and increases process speed. The increased transparency enables better coordination and planning along the entire supply chain. In addition, the integration of just-in-time and just-in-sequence deliveries can further reduce stock levels and optimize production processes.
Practical example: Automotive supplier
An automotive supplier implemented EDI for delivery schedule processing with its main customers. The real-time transmission of demand data increased delivery capability to 99%. Inventory costs were reduced by 15% as safety stocks were reduced and production plans could be designed more precisely. In addition, administrative costs fell by 25% as manual coordination processes were eliminated. The increased efficiency led to annual cost savings of 500,000 euros and significantly strengthened the company's competitiveness.
Conclusion on supplier evaluation
Scheduling agreements are an indispensable tool in modern purchasing, enabling efficiency, planning reliability and cost savings. By combining long-term framework agreements and flexible call-off orders, companies optimize their procurement processes and strengthen supplier relationships at the same time. In view of the digital transformation and new technologies, delivery schedules are becoming even more dynamic and intelligent, which further increases their strategic importance for the company's success.
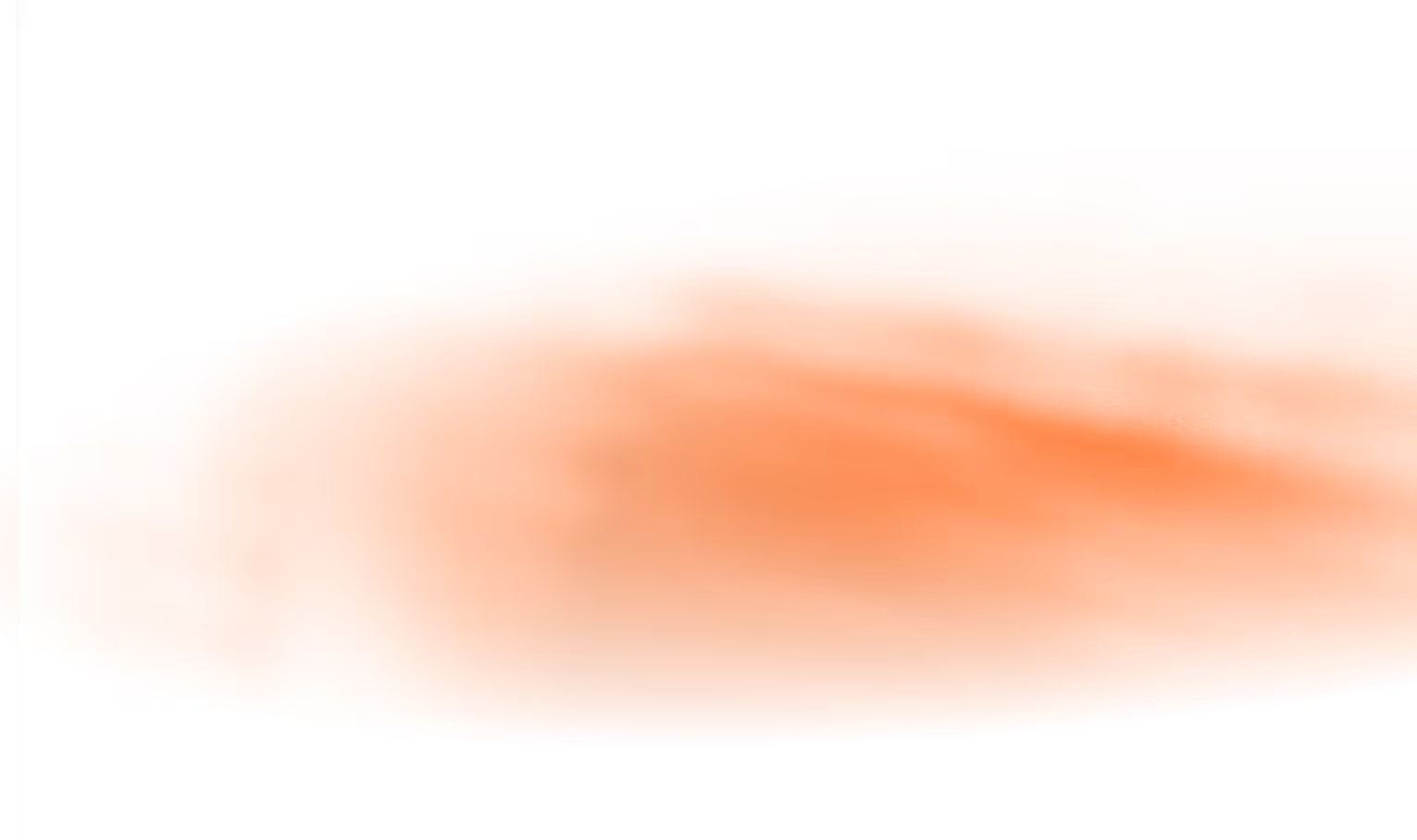
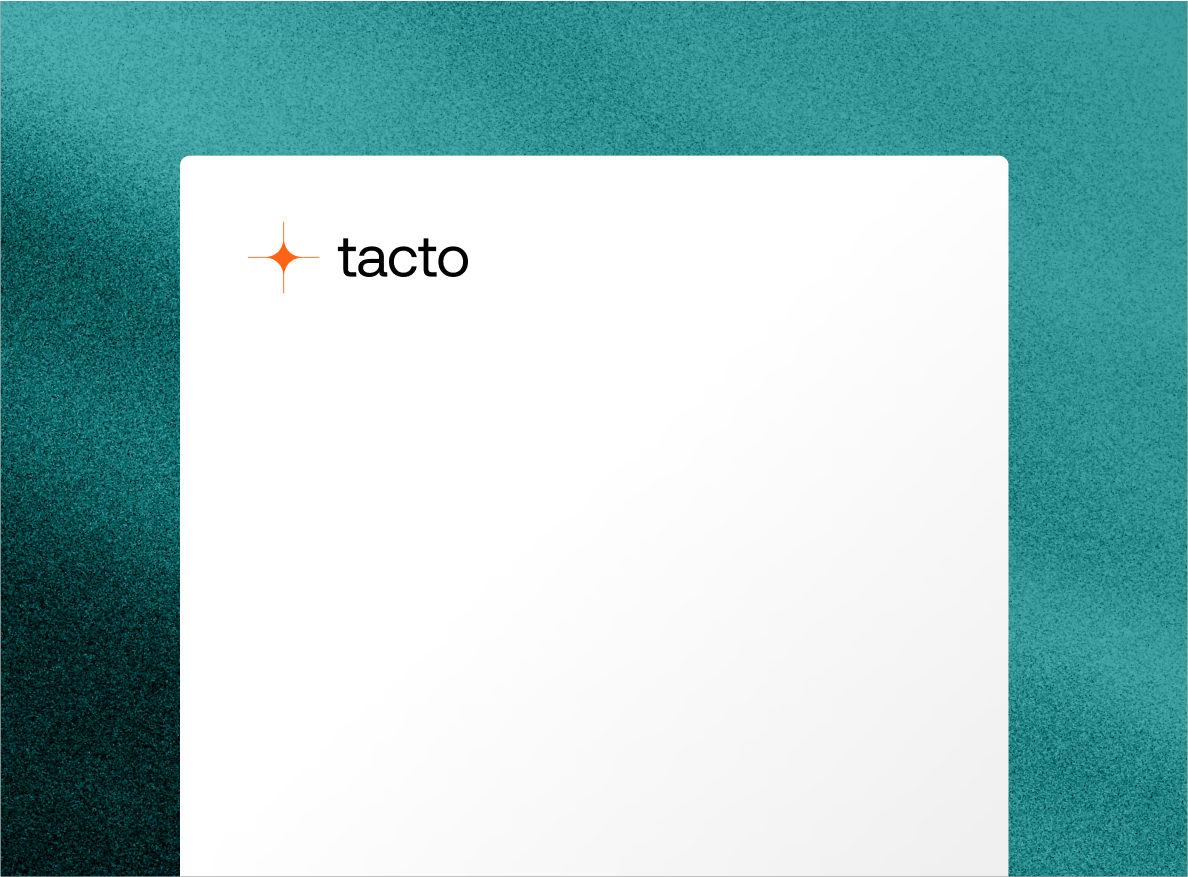