Procurement Glossary
Delivery date tracking: Definition and important aspects for buyers
Systematic tracking of delivery dates not only ensures that goods are received on time, but also enables proactive action to be taken in the event of impending delays. This structured overview shows how Procurement minimizes delivery risks and optimizes supply security through effective deadline tracking.
Delivery date tracking in a nutshell:
Delivery date tracking is the systematic monitoring and documentation of agreed delivery dates and their actual compliance by suppliers. It enables Procurement to proactively manage the availability of goods and identify potential supply bottlenecks at an early stage.
Example: An automotive supplier implements a digital tracking system that automatically queries the status of 200 critical components 14 days before the agreed delivery date and triggers an escalation in the event of a 3-day delay, increasing on-time delivery from 82% to 95% within 6 months.
Introduction to delivery date tracking
Delivery date tracking is an essential part of modern supply chain management and logistics. It enables companies to monitor the current status of their orders in real time and ensure that goods are available at the right place at the agreed time. In times of global supply chains and just-in-time production, the precise tracking and monitoring of delivery dates is becoming increasingly important. Effective delivery date tracking makes a significant contribution to optimizing warehousing, avoiding production interruptions and improving customer satisfaction. In this guide, you will learn about the most important aspects of delivery date tracking, from basic concepts to modern digital tracking solutions.
What is delivery date tracking?
Delivery date tracking is an essential process in procurement that is used to monitor the agreed delivery dates of orders and ensure that goods and services arrive on time. It enables companies to recognize delays in delivery at an early stage and react accordingly.
Importance of delivery date tracking in procurement
In today's globalized and fast-paced economy, timely delivery of materials and services is critical to the smooth running of business processes. Effective delivery date tracking helps companies to achieve this:
- Avoid production downtime: Ensuring that all required materials are available on time.
- increase customer satisfaction: Punctual delivery makes it possible to fulfill customer orders on time.
- reduce costs: Avoiding rush orders and additional logistics costs through proactive planning.
- Strengthen supplier relationships: Improve the reliability of supplier evaluation through regular communication and feedback.
Practical implementation of delivery date tracking
Companies should use systematic processes and suitable tools for efficient delivery date tracking:
- Use automated ordering systems: Use ERP systems to automatically monitor delivery dates.
- Regular communication with suppliers: Continuous exchange of information on delivery status and proactive problem solving.
- Create key figures and reports: Monitoring delivery performance using KPIs to identify bottlenecks at an early stage.
- Manage risk: Plan for buffer times and identify alternative suppliers to minimize uncertainties.
Delivery date tracking is a key tool in supply chain management that helps companies to organize their supply chains efficiently and secure competitive advantages.
Delivery date tracking: From manual control to real-time tracking
Delivery date tracking is a key element in the procurement process to ensure smooth production processes and customer satisfaction. Traditionally, delivery dates were monitored manually, which often led to delays and a lack of transparency. In view of increasing demands for flexibility and speed, a shift towards more efficient methods is inevitable.
Old: Manual delivery date tracking
Traditional approach: In traditional procurement practice, delivery date tracking was mainly carried out manually. Buyers created delivery schedules in spreadsheet programs and communicated with supplier management by phone or email. Status monitoring was based on regular inquiries and delays were often only recognized late. This method was time-consuming and error-prone. In addition, the lack of real-time data led to inaccurate forecasts and impaired the ability to react to delivery bottlenecks.
New: Real-time delivery date tracking
Real-time tracking: Modern approaches rely on digital platforms and automated systems to optimize delivery date tracking. By integrating ERP systems and using technologies such as EDI (Electronic Data Interchange) and IoT (Internet of Things) sensors, delivery information is recorded and processed in real time. This allows companies to view the status of orders at any time, react proactively to deviations and increase transparency in the supply chain. The introduction of AI-supported analysis tools also enables the prediction of potential delays and the implementation of preventative measures. This leads to a reduction in processing times of up to 30% and significantly increases adherence to delivery dates.
Practical example: Automotive industry
A leading car manufacturer implemented a cloud-based real-time tracking system for its suppliers. By connecting the suppliers directly to the central ERP system, delivery data was transferred automatically. This enabled an immediate response to delays and optimal production control. production control. Within a year, the manufacturer was able to increase its on-time delivery reliability from 85% to 98% and reduce stock levels by 20%, resulting in significant cost savings.
Conclusion on delivery date tracking
Delivery date tracking is an indispensable tool in modern supply chain management. It not only enables precise monitoring of delivery dates, but also makes a significant contribution to cost savings and customer satisfaction. By using digital tools, proactive monitoring and close collaboration with suppliers, companies can optimize their supply chains and secure competitive advantages. The key to success lies in the consistent implementation and continuous improvement of processes.
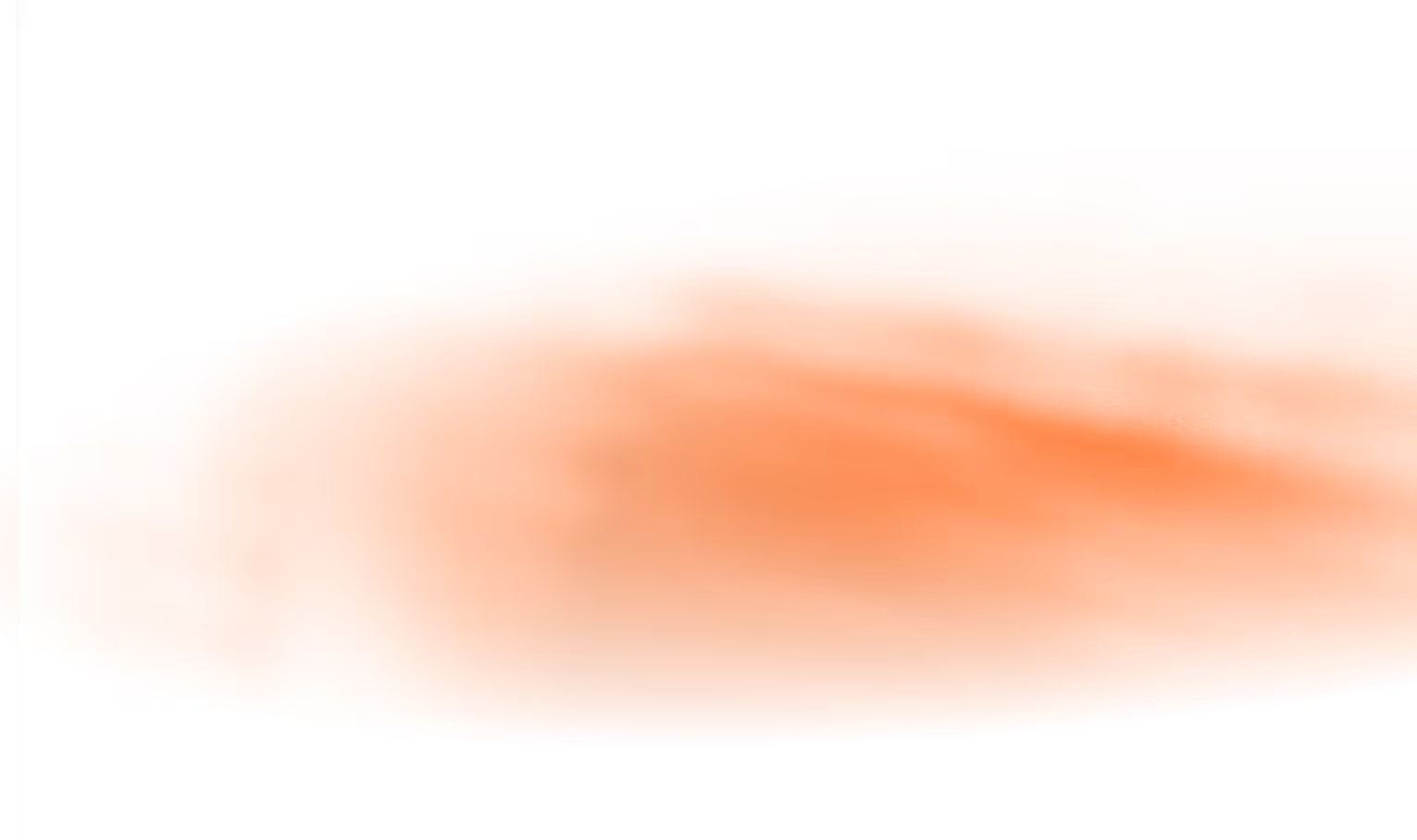
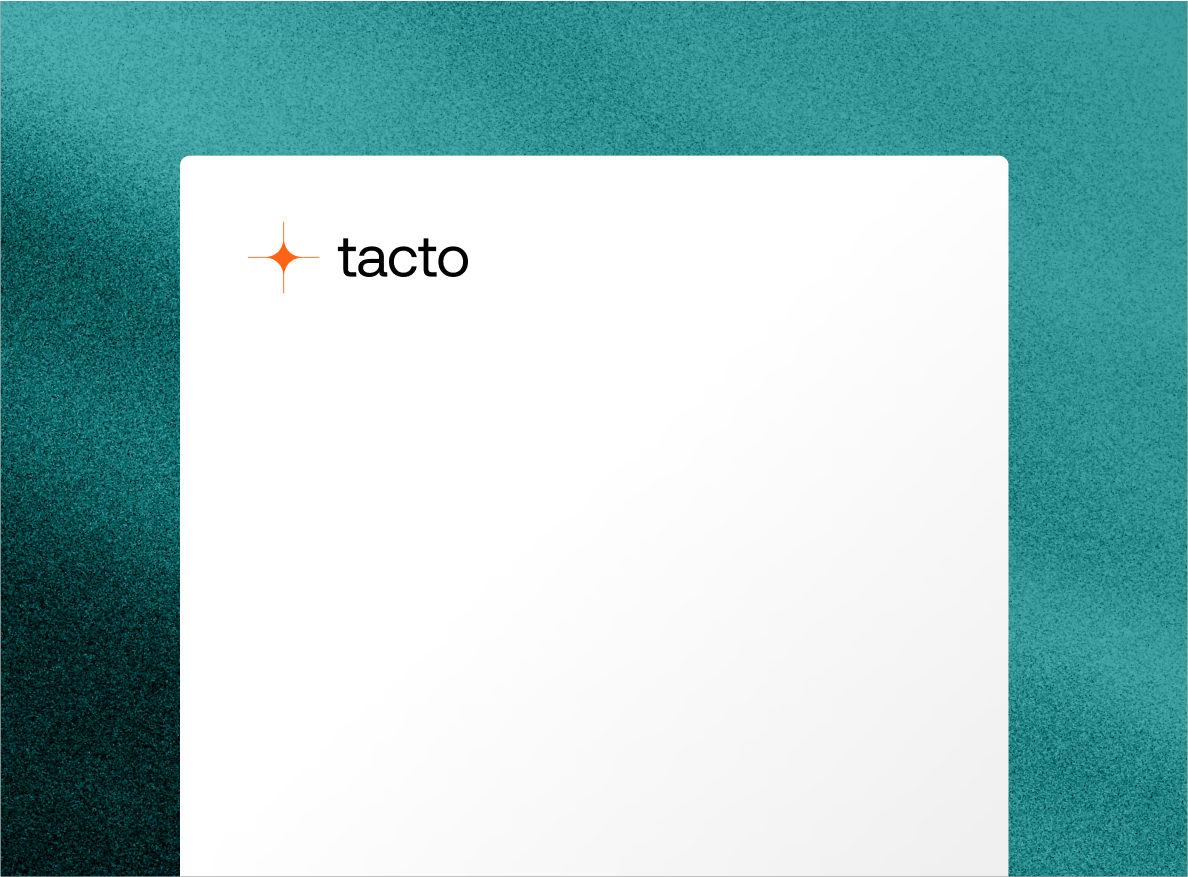