Procurement Glossary
Contract manufacturing: Definition & important aspects for buyers
Contract manufacturing enables companies to establish flexible production without having to build up their own production capacities, thus creating important competitive advantages in dynamic markets. This structured overview shows how Procurement can optimize costs and at the same time ensure quality and delivery reliability by selecting and managing contract manufacturers correctly.
Contract manufacturing in a nutshell:
Contract manufacturing describes the outsourcing of production steps to external service providers who manufacture components or products according to specific specifications. For Procurement , this enables flexible capacity management and cost control without the need for in-house production investments.
Example: An automotive supplier commissions a specialized contract manufacturer with the CNC machining of 10,000 aluminium components per quarter at a unit price of 12 euros, saving 15% in costs compared to in-house production and avoiding investments of 450,000 euros.
Introduction to purchasing controlling for contract manufacturing
Contract manufacturing is an important concept in modern production management and represents a strategic option for companies to flexibly organize their production processes. Contract manufacturing is a form of production in which a client transfers the manufacture of products or components to an external service provider (contract manufacturer). The client usually provides the know-how, specifications and often also the necessary materials, while the contract manufacturer carries out the actual production. This form of cooperation is becoming increasingly important in an increasingly globalized economy and offers companies the opportunity to flexibly expand their production capacities without having to set up their own production facilities.
What is contract manufacturing?
Contract manufacturing, also known as contract production, refers to a production process in which one company (the contractor) manufactures products or components on behalf of another company (the client). The client usually supplies the materials and specifications, while the contractor provides the production capacity and technical expertise. This model enables companies to outsource production processes and concentrate on their core competencies.
Core elements of contract manufacturing
- Client-contractor relationship: Clear definition of responsibilities and expectations between the parties.
- Provision of materials: The client usually provides the raw materials or intermediate products.
- Technical know-how: Use of the contractor's specialized manufacturing expertise.
- Contract design: Detailed agreements on quality standards, production times and costs.
Importance of contract manufacturing in Procurement
In procurement, contract manufacturing plays a decisive role in the strategic orientation of companies. By outsourcing production processes, procurement costs can be reduced, production capacities can be flexibly adapted and market requirements can be met more quickly. It also enables buyers to benefit from specialized expertise and minimize risks in the supply chain.
- Cost optimization: Reduction of production costs by using external production capacities.
- Flexibility: Adaptation to fluctuating demand without having to invest in equipment.
- Focus on core competencies: concentration on strategic business areas instead of operational production activities.
Contract manufacturing: From traditional contract manufacturing to integrated value-added partnership
Contract manufacturing has established itself as an important component of modern production strategies. Originally, it was mainly used to outsource individual production steps in order to save costs and relieve capacity. However, with increasing quality demands and more complex product requirements, it became clear that traditional methods were reaching their limits. The need arose to switch from simple contract manufacturing to in-depth partnerships in order to increase flexibility and efficiency.
Old: Traditional contract manufacturing
Traditional approach: In traditional contract manufacturing, specific manufacturing tasks were outsourced to external companies that produced according to the client's exact specifications. This collaboration was often characterized by rigid contractual conditions and little communication. Tools such as fax and telephone dominated the exchange of information, while processes were manual and isolated. The main characteristics were limited flexibility, long lead times for orders and a lack of real-time transparency. This often led to delays, increased safety stock and limited responsiveness to market changes.
New: Integrated Contract Manufacturing
Integrated contract manufacturing: The modern approach transforms contract manufacturing into a close value-added partnership. By using digital technologies such as ERP systems, IoT and cloud-based platforms, clients and contract manufacturers are seamlessly connected. Real-time data enables synchronized production control, while AI-supported analysis tools facilitate forecasts and adjustments in supply chain visibility. Leaps in innovation such as additive manufacturing and automated quality inspection increase flexibility and reduce error rates. Practical benefits include shorter delivery times of up to 50%, cost savings through just-in-time delivery and greater customer satisfaction thanks to customizable products.
Practical example: Electronics industry
A medium-sized electronics manufacturer integrated its contract manufacturers via a shared supply chain platform. Real-time data exchange enabled production capacity utilization to be optimized and warehousing to be reduced by 35%. The introduction of automated quality checks led to a 20% reduction in the error rate. Overall, the company was able to reduce its lead times by 40% and cut production costs by 15%, resulting in increased competitiveness in the global market.
Conclusion on contract manufacturing
Contract manufacturing is an essential strategic instrument in modern procurement. It enables companies to react flexibly to market requirements, optimize costs and benefit from external expertise. Success depends largely on the careful selection of partners, precise contract design and effective quality management. Despite challenges such as know-how protection and dependency risks, contract manufacturing offers considerable opportunities for future-oriented companies, especially in the context of digital transformation.
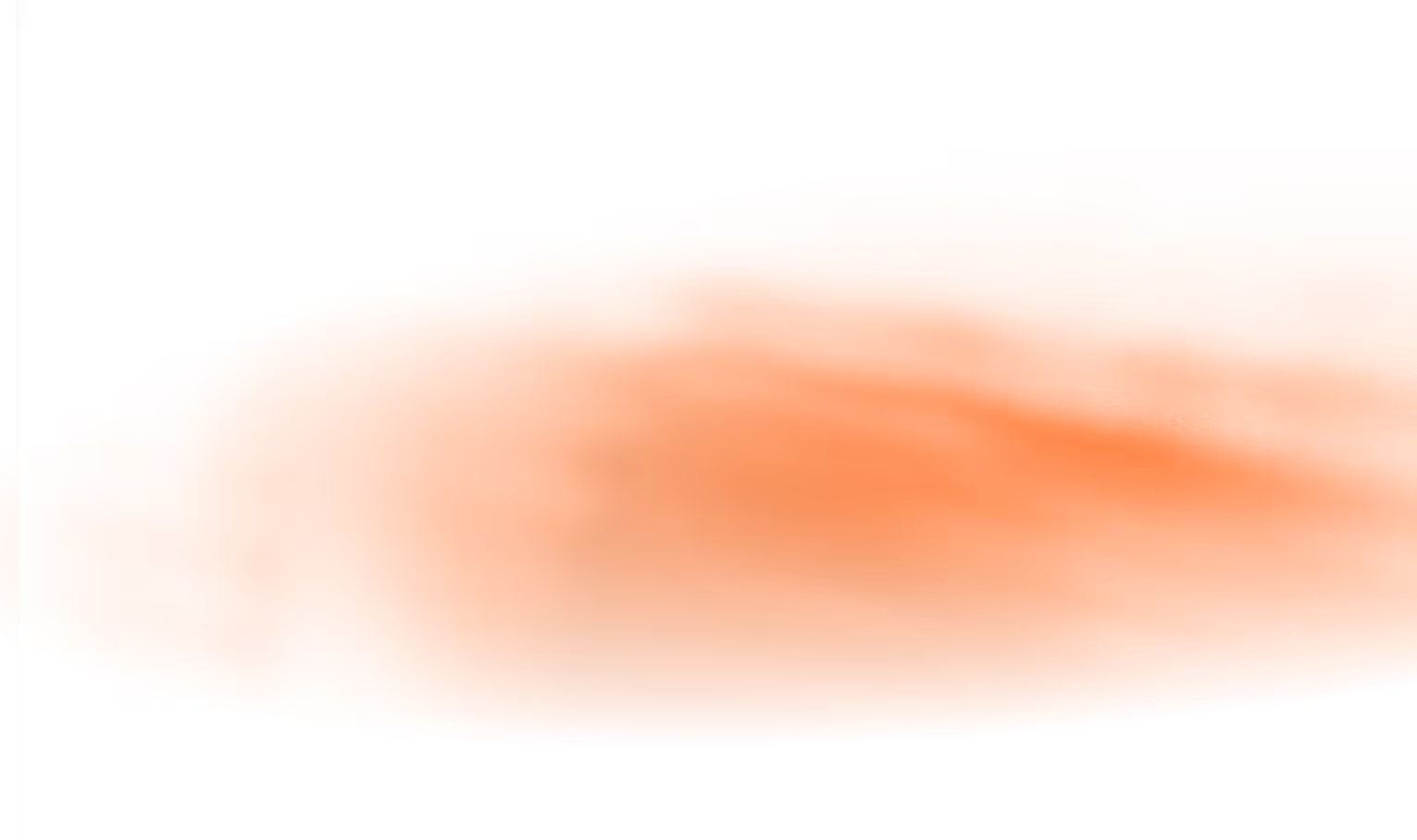
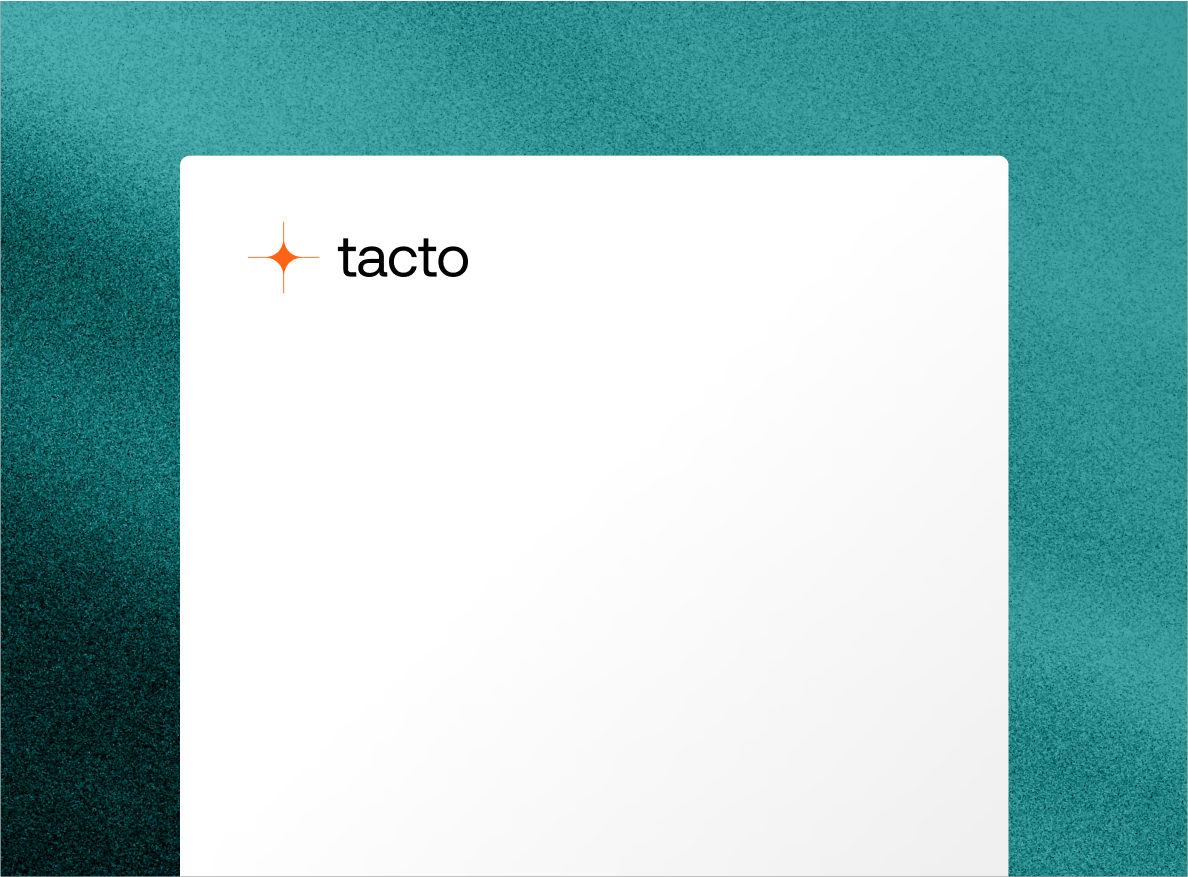