Procurement Glossary
Lot size optimization: definition & important aspects for buyers
The optimum batch size determines costs and efficiency in procurement and has a direct influence on the company's success. This structured overview shows you the most important methods and levers for cost-optimized order quantities in Procurement.
Batch size optimization in a nutshell:
Lot size optimization is the systematic determination of the economically optimal order quantity, taking into account opposing costs such as ordering costs and storage costs. For Procurement , this enables a balance between minimum total costs and maximum security of supply, while at the same time avoiding excess stock.
Example: An automotive supplier optimizes its order quantity for standard screws from 1,000 pieces per week to 4,000 pieces per month, thereby reducing its total annual costs by EUR 2,400 through savings in order processing and transport costs while maintaining the same level of supply security.
Optimal batch sizes in Procurement
Lot size optimization is a fundamental concept in the field of production and procurement planning. It deals with determining the optimum order quantity or production quantity in order to minimize overall costs. Various factors such as storage costs, ordering costs, set-up costs and capital commitment must be taken into account. Finding the right batch size is a complex task that has a significant impact on a company's profitability. This guide presents the most important aspects of batch size optimization, various calculation models and practical application examples.
What is batch size optimization?
Batch size optimization refers to the determination of the optimal order or production quantity in order to minimize the total costs in the procurement and production process. This involves balancing inventory ratios and ordering costs. The aim is to increase efficiency in materials management and to make optimum use of resources and costs by adjusting batch sizes.
Core elements of batch size optimization
Significance for Procurement
In Procurement , lot size optimization is essential to reduce costs and increase supply chain efficiency. By optimizing lot sizes, companies can reduce inventory levels and free up capital without jeopardizing their ability to deliver. This leads to a leaner inventory, lower warehousing costs and improved flexibility in procurement.
Lot size optimization: From static to dynamic methods
Building on the theoretical foundations of batch size optimization, the practical application is crucial for the efficiency of procurement and production processes. The correct determination of order or production quantities directly influences a company's inventory costs and ability to deliver. In an increasingly dynamic market environment with fluctuating demand, the adaptation of traditional methods to modern, flexible approaches is becoming ever more important.
Old: Traditional batch size planning
Traditional approach: In traditional batch size planning, fixed order quantities are calculated, often using the Andler formula. This method assumes constant requirements and fixed cost structures. Companies use it to reduce the number of orders through larger batch sizes and thus minimize ordering and set-up costs. The tools used are usually simple tables or calculation models integrated into ERP systems. However, these rigid processes often lead to high stock levels, increased capital commitment and a lack of flexibility in the event of fluctuations in demand.
New: Dynamic batch size optimization
Dynamic lot sizing: Modern lot size optimization relies on dynamic models that incorporate current market data and forecasts. Advanced Planning and Scheduling (APS) systems are used to flexibly adapt lot sizes to changing requirements. Key innovations such as real-time data analysis, AI-based demand forecasts and the inclusion of variable costs enable more precise control. This leads to lower stock levels, as production or orders are only placed as required. In addition, responsiveness to market changes and service levels to customers are improved.
Practical example: Automotive industry
An automotive supplier implemented dynamic batch size optimization with the help of an AI-supported APS system. The changeover reduced the average stock level by 35%, which corresponded to a capital release of 2 million euros. At the same time, the delivery reliability increased to 98%. The flexibility in production enabled faster adaptation to customer requirements, reducing throughput times by 20%. Overall, this led to an annual cost saving of 500,000 euros and a considerable strengthening of the market position.
Conclusion on batch size optimization
Batch size optimization is an indispensable tool for efficient supply chain management. By systematically calculating optimal order and production quantities, it enables significant cost savings while ensuring delivery capability. While the classic Andler formula serves as a basis, modern challenges such as fluctuating demand and complex supplier relationships increasingly require dynamic, AI-supported solutions. The success of batch size optimization depends largely on precise data, regular adjustments and good system integration.
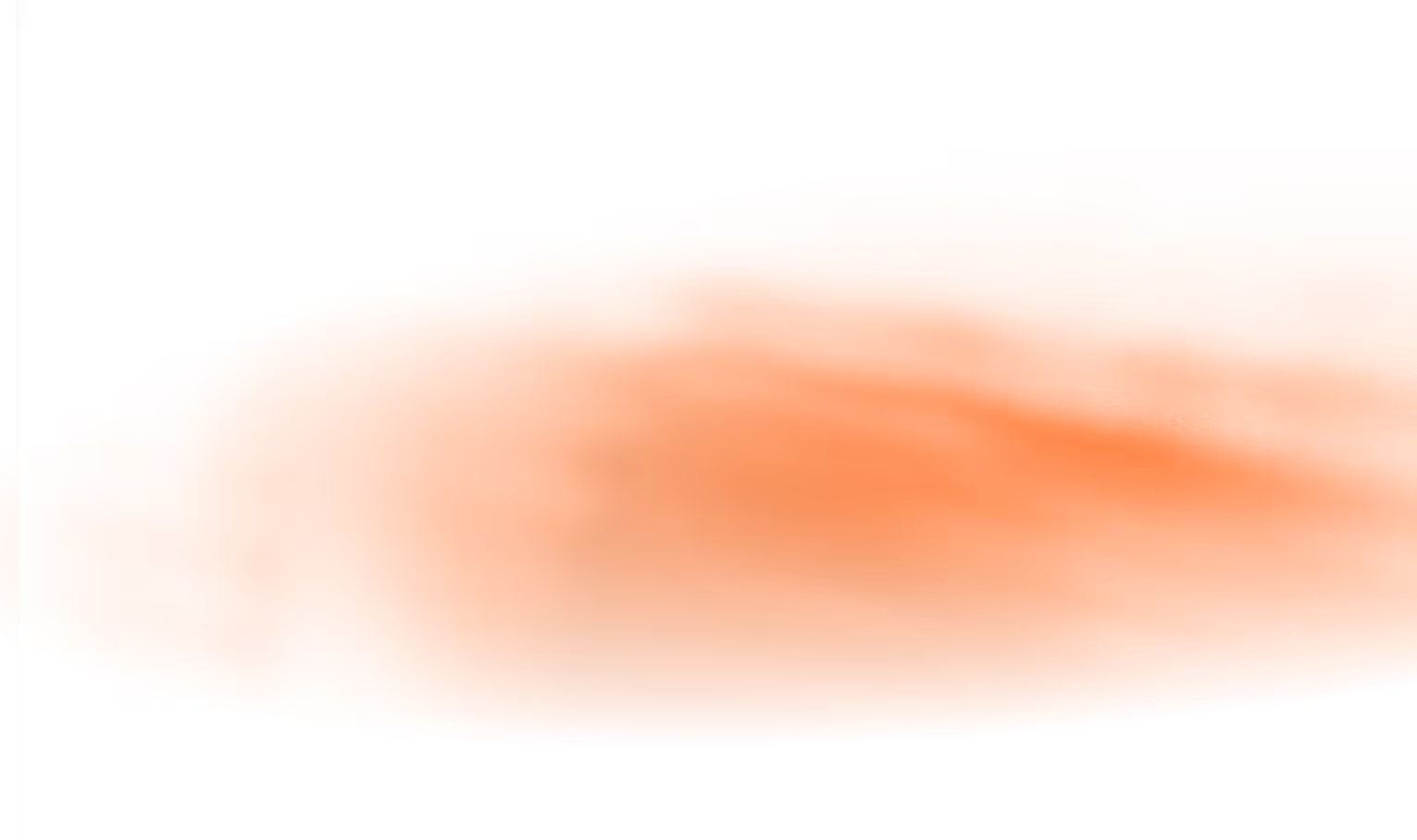
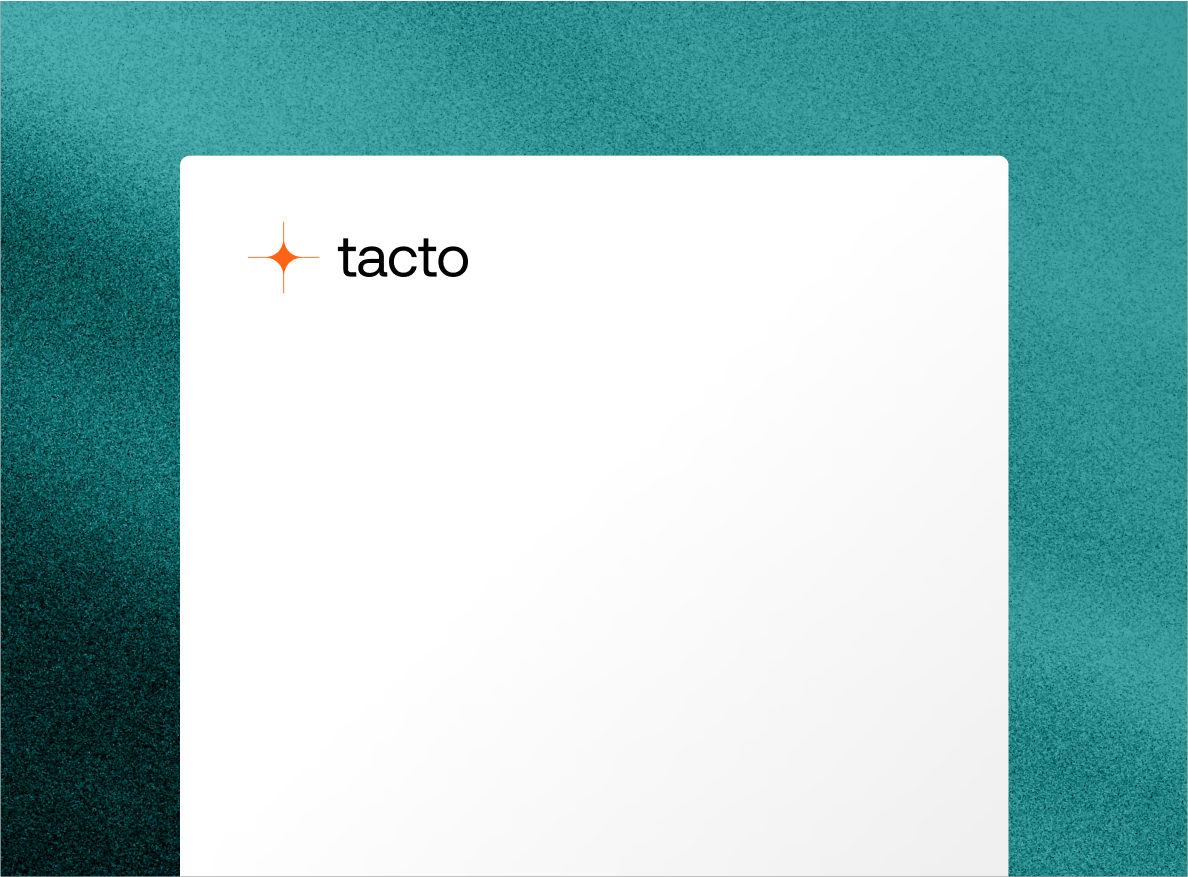