Procurement Glossary
Quality inspection: definition & important aspects for buyers
As a central element of quality management, quality testing ensures the reliability of products and services along the entire value chain. This structured overview shows you the most important methods and tools for effective quality assurance in Procurement, which you can use to minimize risks and increase customer satisfaction.
Quality inspection in a nutshell:
A quality inspection is a systematic process for checking and evaluating products, services or processes based on defined quality standards. For Procurement , it is an essential tool for ensuring supplier quality and minimizing quality risks in the supply chain.
Example: An automotive supplier carries out a 100% incoming goods inspection when receiving critical components, in which each part is checked for 15 defined quality characteristics within 24 hours of delivery, reducing the error rate in production from 3.2% to 0.4%.
Quality inspection: An introduction
Quality testing is an essential part of modern quality management and plays a central role in ensuring product quality and customer satisfaction. It comprises systematic inspections and controls that serve to check and ensure compliance with specified quality standards. In today's world, where quality is a decisive competitive factor, professional quality testing is becoming increasingly important. This guide provides a comprehensive overview of the various aspects of quality inspection, from basic methods to modern inspection procedures and their practical application in day-to-day operations.
What is quality inspection?
Quality inspection is a systematic process to ensure that procured products or services meet the defined quality standards and specifications. In Procurement , it includes the inspection of incoming goods or services in order to identify defects at an early stage and ensure compliance with quality management in Procurement. This helps to minimize product defects and increase customer satisfaction.
Core elements of the quality inspection
Importance of quality inspection in Procurement
In the procurement process, quality inspection is crucial for ensuring that supplier evaluation complies with the agreed standards. It helps buyers to minimize risk management by identifying and resolving quality issues at an early stage. Effective quality inspection can reduce costs for rework, returns and production downtime, which in turn increases efficiency and adds value to the business.
Quality inspection: from manual control to automated quality assurance
Quality inspection is an indispensable part of the procurement process and ensures that delivered goods meet the defined specifications. Based on its theoretical importance in Procurement , it ensures end customer satisfaction and protects against costly errors. In practice, the shift towards more complex products and higher quality requirements means that traditional methods are reaching their limits. There is therefore an urgent need for more efficient and precise inspection procedures.
Old: Manual quality control
Traditional approach: In traditional quality inspection, checks are mainly carried out manually. Trained employees check the incoming goods visually or with simple measuring tools for defects and deviations. Tools such as calipers, inspection gauges and checklists are used. This process is time-consuming and heavily dependent on the care and experience of the staff. There is also a high risk of human error and the documentation is often paper-based, which makes traceability more difficult and creates sources of error.
New: Automated Quality Assurance
Automated Quality Assurance: Modern quality inspection relies on automated systems that work with the help of technologies such as image processing, sensor technology and AI in Procurement. By using high-speed cameras and machine learning algorithms, products can be checked in real time and with maximum precision. These innovations enable seamless inspection without human intervention. The results are recorded digitally and integrated directly into quality management. This leads to a significant increase in efficiency, a reduction in inspection times of up to 80% and a minimization of error rates to almost zero.
Practical example: Implementation in electronics production
An electronics manufacturer introduced an automated optical inspection system to its production line. By switching from manual spot checks to 100% automated inspections, the failure rate fell by 65%. The inspection time per unit was reduced from 2 minutes to 15 seconds. In addition, the early detection of defects has reduced rejects by 30%. The investment in the system paid for itself within a year thanks to the increased product quality and production efficiency.
Conclusion on supplier evaluation
Quality inspection is an indispensable part of the modern procurement process. It not only ensures product quality, but also contributes significantly to risk minimization and cost savings. Thanks to standardized processes, qualified personnel and digital innovations, quality inspection is constantly evolving - from a pure control function to preventive, data-supported quality management. Success lies in the balance between thorough inspection and efficient execution, supported by modern technologies such as AI and IoT.
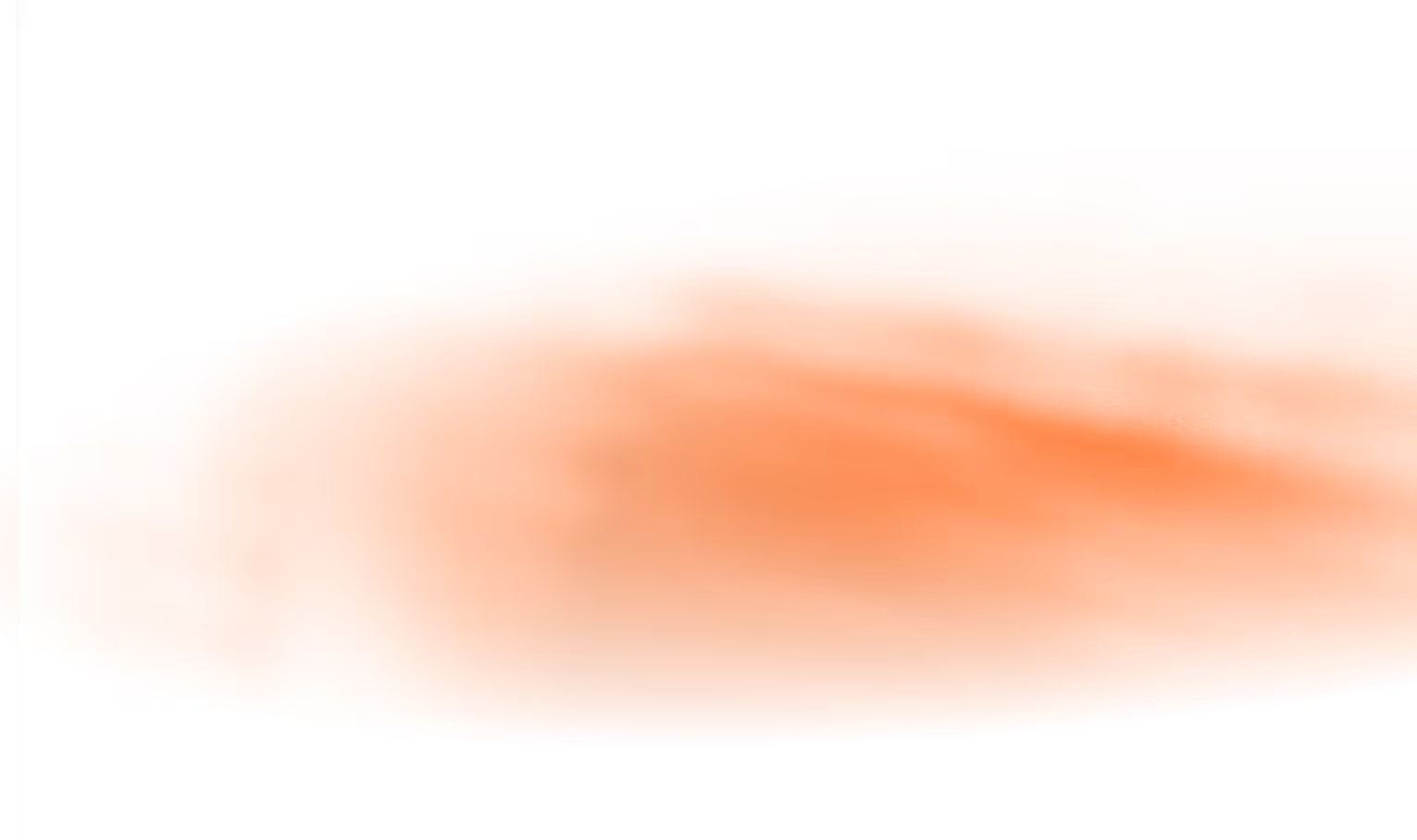
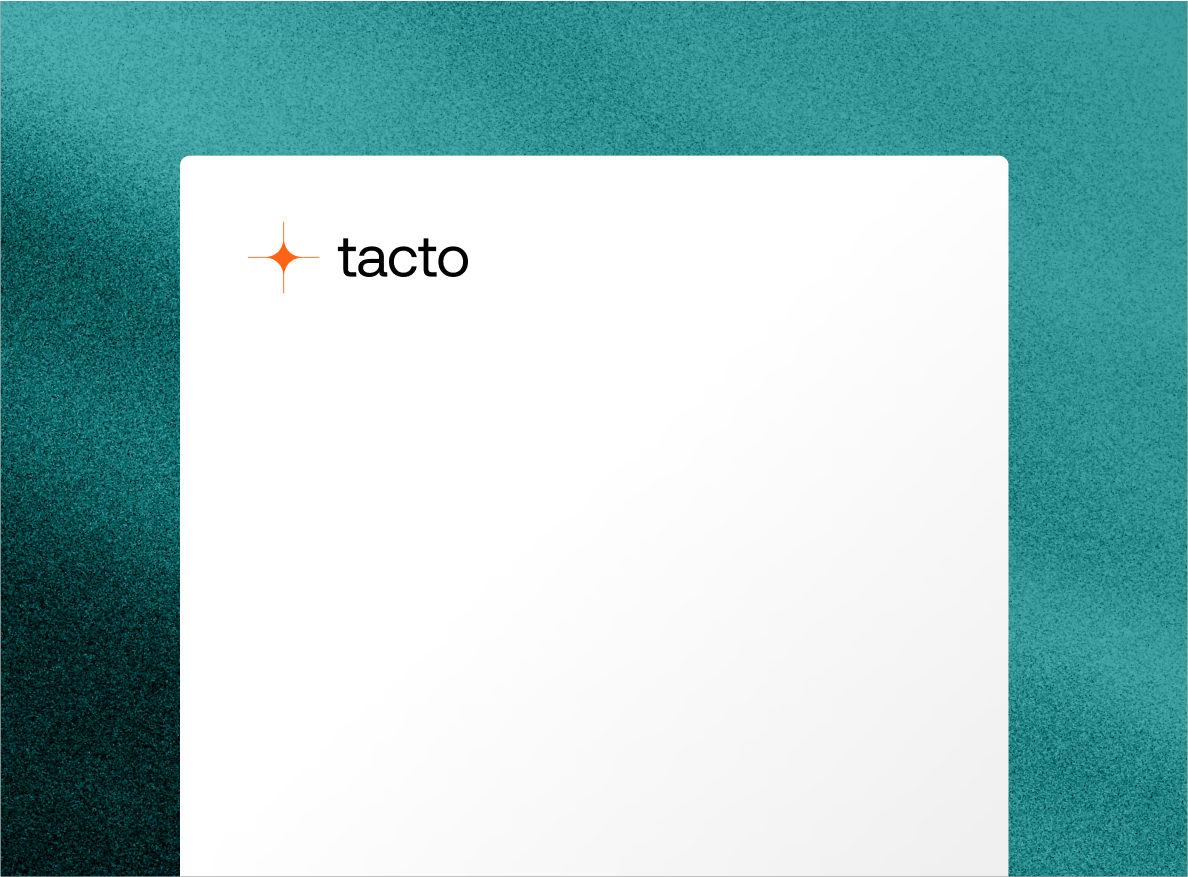