Procurement Glossary
Quality agreement: definition & important aspects for buyers
Quality agreements create binding standards between suppliers and purchasers and thus ensure sustainable product quality throughout the entire value creation process. This structured guide shows you how you as a buyer can design effective quality agreements and thus minimize risks and optimize processes.
Quality agreement in a nutshell:
A quality agreement is a binding contract between the customer and supplier that defines specific quality requirements, test procedures and responsibilities. For Procurement , it is a central instrument for quality assurance and minimizes potential quality risks in the supply chain.
Example: An automotive supplier concludes a quality agreement with its metal parts supplier that stipulates a maximum defect rate of 50 ppm, requires monthly quality reports and provides for a penalty of EUR 5,000 per incident in the event of non-compliance.
Quality agreement: A guide to effective supplier management
The quality agreement, also known as a quality agreement or QAA (quality assurance agreement), is an essential instrument in modern quality management. It is a binding contract between a company and its suppliers or service providers that defines the quality requirements and standards for products or services. At a time when quality and reliability have become decisive competitive factors, the quality agreement is becoming increasingly important. It serves as the basis for transparent and effective cooperation and helps to minimize quality risks and optimize processes. In this guide, you will learn all the important aspects of designing, implementing and monitoring quality agreements.
What is a quality agreement?
A quality agreement is a contractual document between a company and its supplier that defines specific quality requirements for products or services. It serves as a basis for ensuring that the materials or services supplied meet the defined standards, thus guaranteeing product quality and customer satisfaction. Clear specifications avoid misunderstandings and enable smooth cooperation.
Core elements of a quality agreement
Significance for Procurement
In the procurement process, the quality agreement plays a crucial role in ensuring delivery quality and building long-term partnerships with supplier management. It enables buyers to communicate clear expectations and create legal certainty. By defining quality criteria, costs for rework can be reduced and efficiency in the supply chain can be increased.
Quality agreement: from reactive control to proactive partnership
A quality agreement is a key element in raising cooperation between companies and supplier management to a high level of quality. In practice, it ensures that products and services meet the agreed standards and therefore fulfill the expectations of the end customer. With the increasing complexity of supply chains and rising quality demands, the need for more efficient approaches is growing. As a result, the traditional, often reactive approach is evolving into a proactive partnership that defines quality as a common goal.
Old: Reactive quality control
Traditional approach: In traditional practice, quality agreements were static documents that were rarely updated. Quality inspections were mainly carried out at the end of the production process or after receipt of goods by the customer. Manual inspection steps were mainly carried out, supported by simple checklists and paper documentation. This approach was time-consuming and error-prone. Challenges such as delayed defect detection, high rework costs and a lack of flexibility in the face of changes characterized the traditional approach and put a strain on the business relationship between buyer and supplier.
New: Proactive Quality Partnership
Quality Partnership: The modern approach defines the quality agreement as a dynamic, collaborative partnership. The focus is on innovative technologies such as digital platforms, real-time data analysis and joint quality assurance agreements. Suppliers and companies work closely together, share quality data and focus on transparent communication. Key improvements include the early involvement of suppliers in development processes, continuous improvement loops and joint training programs. This leads to a reduction in quality defects, faster response times in the event of problems and greater innovative strength thanks to pooled expertise.
Practical example: Pharmaceutical industry strengthens quality networks
A global pharmaceutical company implemented a quality partnership with its most important raw material suppliers. By sharing a digital quality portal, quality deviations were reduced by 40%. Regular virtual meetings enabled a rapid exchange of information and proactive problem solving. In addition, the time-to-market of new products was reduced by 25% as suppliers were involved in R&D processes at an early stage. This cooperative model led to higher quality standards, cost savings in the double-digit million range and strengthened the competitive position of all parties involved.
Conclusion on the quality agreement
Quality agreements are indispensable instruments for successful cooperation between companies and suppliers. They not only create clear standards and legal certainty, but also make a significant contribution to risk minimization and cost savings. Increasing digitalization will further optimize these agreements through AI-supported systems and real-time monitoring. Both precise specifications and a trusting partnership between all parties involved are crucial for long-term success.
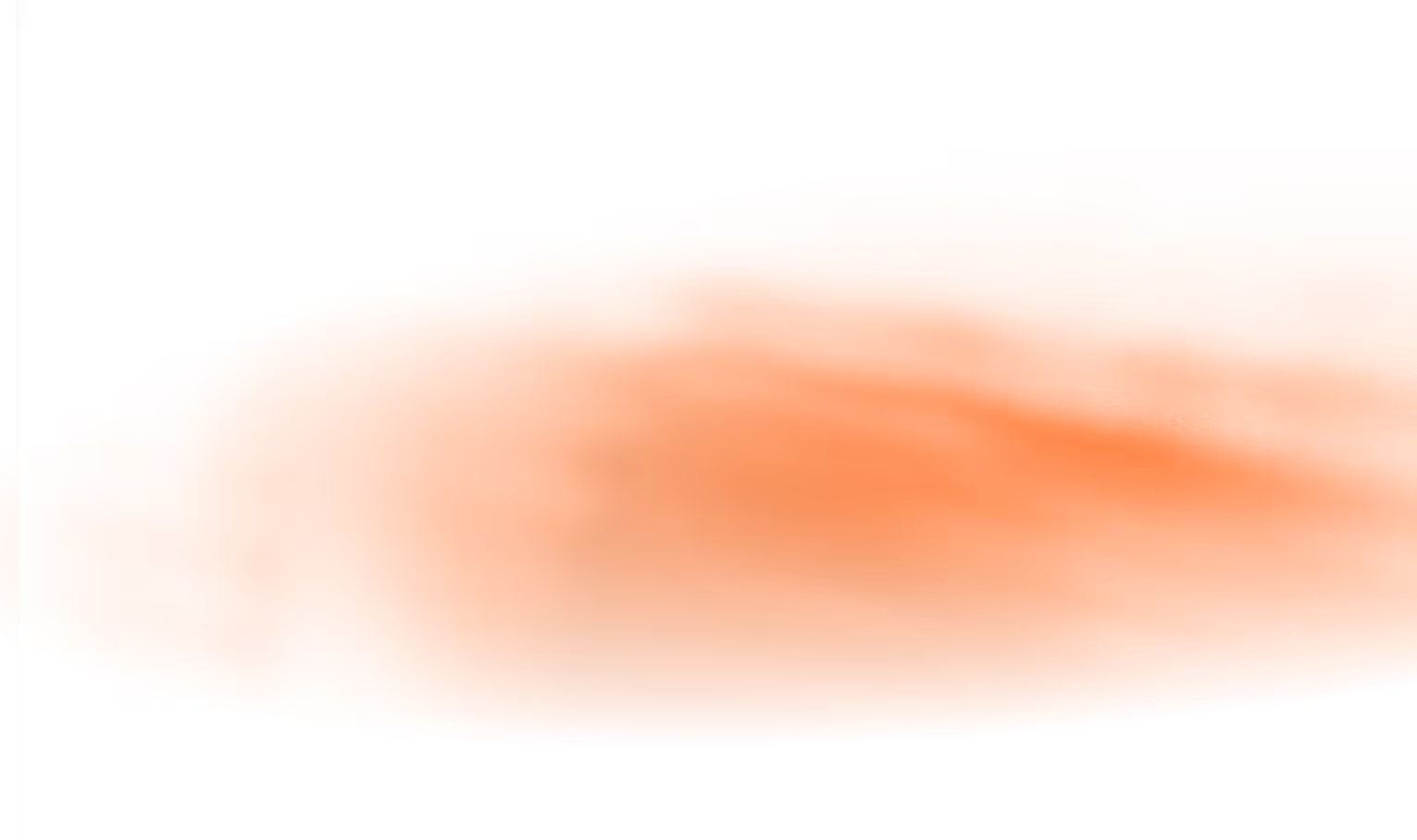
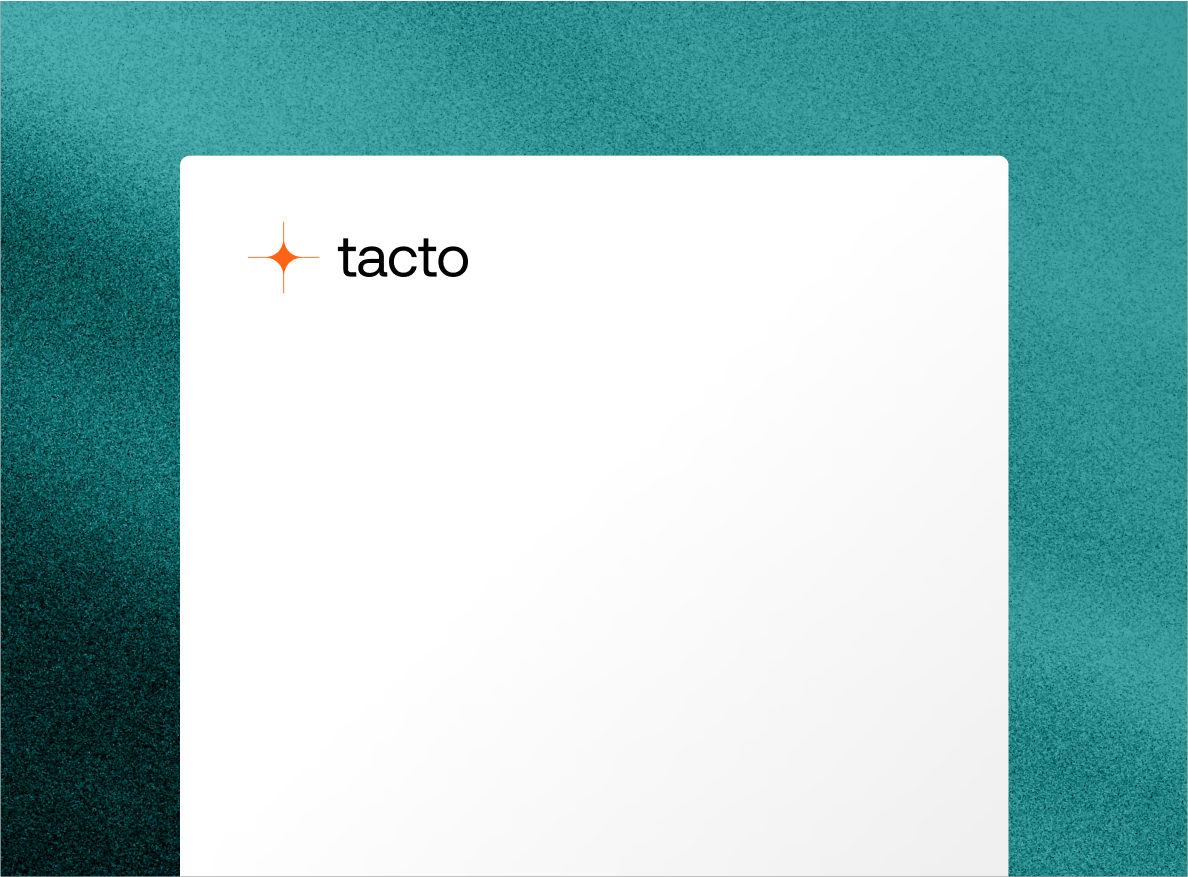