Procurement Glossary
Reshoring: definition & important aspects for buyers
Reshoring is becoming an important trend in the global economy as companies relocate their production back to their home markets to reduce costs and minimize risk. This structured overview highlights the key drivers and challenges of reshoring and provides specific recommendations for buyers on how to successfully manage reshoring.
Reshoring in a nutshell:
Reshoring describes the strategic relocation of production and procurement activities that were previously outsourced abroad back to the country of origin. For Procurement , this means realigning the supplier structure with a focus on domestic markets in order to make supply chains more robust and reduce dependencies.
Example: A German automotive supplier relocates its electronic component production from China back to Germany in 2023 and invests EUR 50 million in a new production facility, reducing delivery times from 12 to 3 weeks and increasing supply security.
Introduction to reshoring
Reshoring is a current and important topic in the global economic landscape. It describes the process of relocating production sites from abroad back to a company's home country. This trend has become increasingly important in recent years, particularly due to global crises such as the COVID-19 pandemic and geopolitical tensions. German companies are increasingly rethinking their global supply chains and production strategies in order to minimize risks and increase security of supply. In this analysis, we look at the most important aspects of reshoring, its opportunities and challenges and its significance for the German economy.
What is reshoring?
Reshoring refers to the process by which companies return their production or procurement strategies that were previously relocated abroad to their home country or closer to their main sales market. The reasons for this are often higher transportation costs, increasing quality requirements, risks in global supply chains or political uncertainties. By reshoring, companies can strengthen control over their processes, increase flexibility and respond better to market changes.
Core elements of reshoring
- Relocation: Returning production and procurement to Germany or nearby countries.
- Supply chain optimization: Simplification of the supply chain by reducing intermediate stations and transport routes.
- Quality improvement: Improving product quality through proximity to development centers and strict standards.
- Risk minimization: Reduction of geopolitical risks and dependencies on foreign markets.
Importance of reshoring for Procurement
In Procurement , reshoring plays a central role in the realignment of procurement strategies. By shifting procurement back to the domestic market, buyers can make supply chain resilience more transparent and intensify supplier relationship management. This leads to increased flexibility and faster responsiveness to market demands. Reshoring also enables better control of compliance guidelines and sustainability standards.
- Local supplier development: Establishing and maintaining partnerships with regional suppliers.
- Cost-benefit analysis: Analysis of total costs, taking quality and logistics aspects into account.
- Sustainable procurement: promotion of environmentally friendly practices and compliance with legal regulations.
Reshoring: from offshoring to local production
Reshoring is becoming increasingly important in the global economy. While companies used to relocate production sites abroad to take advantage of low labor costs, they are now recognizing the benefits of returning to local manufacturing. This change is based on the need to shorten supply chains, raise quality standards and respond more flexibly to market changes. The transition from offshoring to reshoring represents a strategic shift that brings both challenges and opportunities.
Old: Offshoring
Traditional approach: In recent decades, many companies have relied on offshoring by relocating production processes to countries with lower production costs. In practice, this meant setting up complex global supply chains and working with foreign manufacturing partners. Tools such as global sourcing and international logistics networks were used intensively to reduce costs and achieve competitive advantages. However, long transportation routes led to increased delivery times and risks such as political instability, currency fluctuations and quality problems. In addition, cultural and language barriers made communication and cooperation with foreign suppliers more difficult, which impaired the flexibility and responsiveness of companies.
New: Reshoring
Reshoring: In the modern approach, companies relocate production and procurement activities back to their home country, supported by technological innovations such as automation and digitalization. By using robotics and Industry 4.0 technologies, companies can produce more efficiently and compensate for higher labor costs. In practice, this leads to significantly shortened supply chains, reduced transportation costs and improved control over production processes. Companies benefit from increased flexibility by being able to react more quickly to customer needs and offer customized products. In addition, risks arising from global events such as trade conflicts or pandemics are minimized and a contribution is made to local economic development.
Practical example: Automotive industry
A German automotive supplier decided to relocate the production of electronic components from Asia back to Germany. By investing in highly automated production facilities, the company was able to reduce production costs by 15%. Delivery times were reduced from eight to two days, resulting in improved just-in-time delivery to car manufacturers. In addition, product quality increased, which was reflected in a 40% reduction in the reject rate. Overall, the company's competitiveness on the European market improved considerably and over 200 new jobs were created in the region.
Conclusion on reshoring
Reshoring is becoming a key strategic tool for forward-looking companies. Reshoring production and procurement activities not only enables better control over quality and supply chains, but also creates competitive advantages through greater flexibility and customer proximity. Despite initial challenges such as high investment costs and a shortage of skilled workers, the long-term benefits outweigh the costs: shorter delivery times, increased product quality and improved sustainability. For Procurement , this means a new focus on local partnerships and the integration of modern technologies.
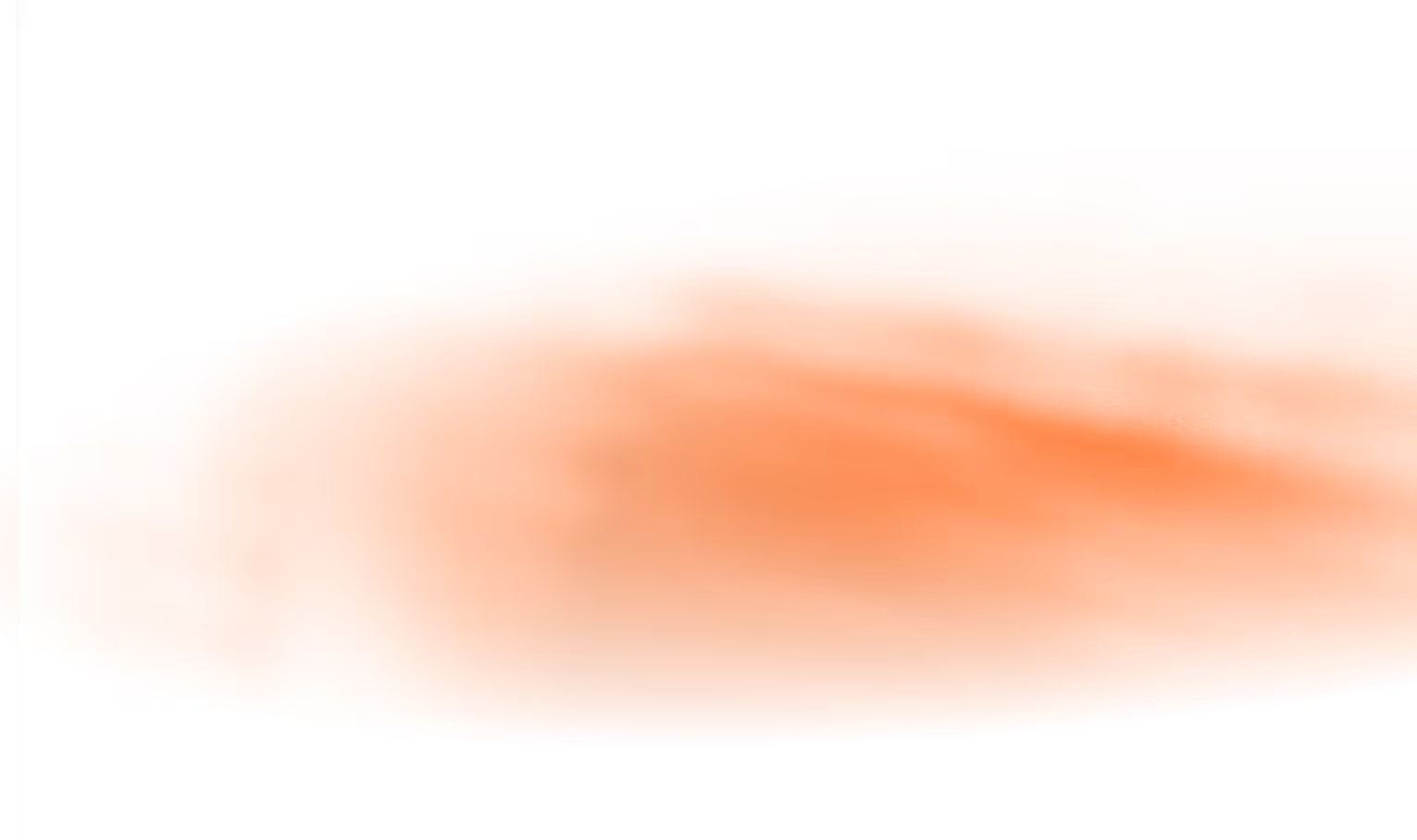
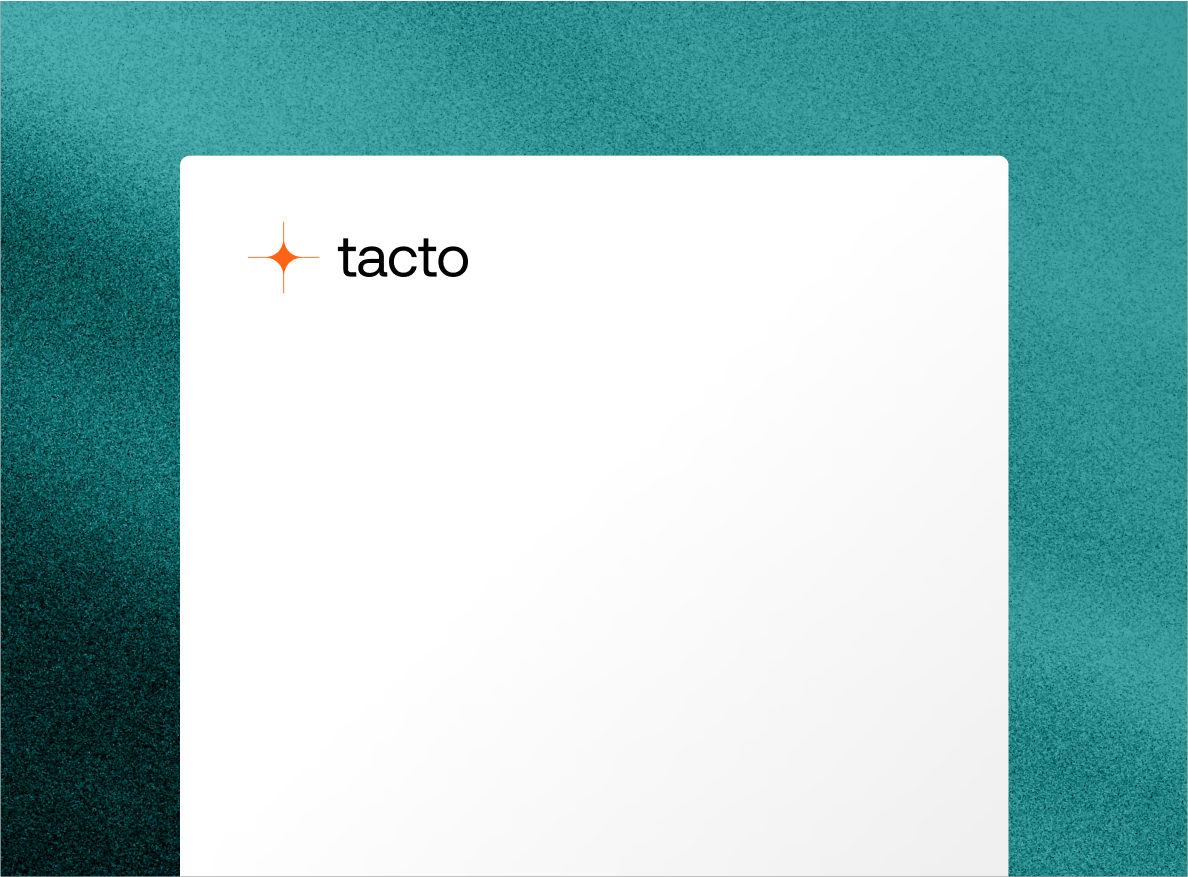