Procurement Glossary
Standardization: Definition & important aspects for buyers
As a central lever, standardization creates efficiency and cost savings through uniform processes, specifications and interfaces in companies. The following overview shows how Procurement reduces complexity through systematic standardization and generates measurable value contributions for the company.
Standardization in a nutshell:
Standardization describes the systematic standardization of products, processes and specifications according to defined rules and norms. For Procurement , this enables a reduction in the number of variants, simplified procurement processes and improved negotiating positions thanks to greater bundling of requirements.
Example: By standardizing its screw types, an automotive supplier reduces the number of variants from 200 to 50 types, which leads to a 23% reduction in procurement costs and reduces annual storage costs by EUR 45,000.
Standardization: An introduction
Standardization is a fundamental process in modern business and industry that aims to establish uniform norms, rules and procedures. It plays a central role in the optimization of work processes, quality assurance and international cooperation. The introduction of standards simplifies processes, reduces costs and ensures compatibility between different systems and products. In this introduction, we will highlight the most important aspects of standardization, explain its significance for companies and organizations and discuss current developments and challenges in this area.
What is standardization?
Standardization refers to the process of standardizing products, services, processes or methods based on defined norms and specifications. In Procurement , this means that similar materials or services are procured according to uniform criteria. The aim is to increase process optimization in Procurement, reduce costs and guarantee quality standards.
Core elements of standardization
Importance of standardization in Procurement
In procurement management, standardization plays a central role in cost efficiency and process optimization. Uniform standards allow purchasing volumes to be bundled, volume discounts to be used and supplier relationship management to be consolidated. It also makes it easier to compare offers and promotes consistent product and service quality.
Standardization: From individual solutions to digital uniformity
Standardization has become an essential factor for increasing efficiency and reducing costs in purchasing controlling. Building on the theoretical foundation of standardizing processes, products and services, practical implementation is becoming increasingly important. Companies are faced with the challenge of dealing with increasing complexity and individual customer requirements. The transition from individual, fragmented solutions to standardized processes is necessary in order to optimize the value chain and achieve sustainable competitive advantages.
Old: Individual procurement without standards
Traditional approach: In traditional procurement logistics, products and services were often purchased without uniform specifications and standards. Each department or business unit acted autonomously, which led to a variety of different processes and supplier relationships. Manual ordering processes, paper-based documentation and personal agreements dominated everyday life. This fragmentation led to inconsistent quality standards, increased process costs and a lack of transparency. The lack of bundling of requirements prevented economies of scale, and the variety of suppliers made management more difficult and increased the risk of disruptions in the supply chain.
New: Digital standardization in Procurement
Digital Standardization: The modern approach relies on digital technologies to effectively implement standardization in Procurement . By using e-procurement systems and central databases, processes are automated and uniform specifications are implemented company-wide. Key innovations such as electronic catalogs, automated order approvals and digital contract management tools enable increased efficiency. Digitization facilitates the consolidation of suppliers and the bundling of requirements, which leads to considerable cost savings. Practical benefits include a reduction in process costs of up to 30%, shorter lead times and improved quality assurance thanks to clear specifications and standards.
Practical example: Implementation of e-procurement at an industrial company
A leading industrial company decided to transform its purchasing processes through digital standardization. With the introduction of an e-procurement system, all orders were processed centrally via one platform. This resulted in a 50% reduction in procurement time and a 20% cost saving in the first year. Thanks to the standardized specifications, the quality defects in supplied materials fell by 35%, which significantly reduced production losses. The number of suppliers was consolidated from 500 to 200, which made supplier management more efficient. Overall, the measure led to an increase in competitiveness and sustainably improved business processes.
Conclusion on standardization
Standardization in Procurement is an essential lever for saving costs and increasing efficiency. By standardizing products, processes and specifications, companies can not only achieve volume discounts and optimize inventories, but also sustainably improve the quality of their procurement processes. The success of standardization depends largely on careful process analysis, the involvement of all stakeholders and the balance between standardization and the necessary flexibility. In view of the digital transformation, the importance of standardized processes will continue to increase.
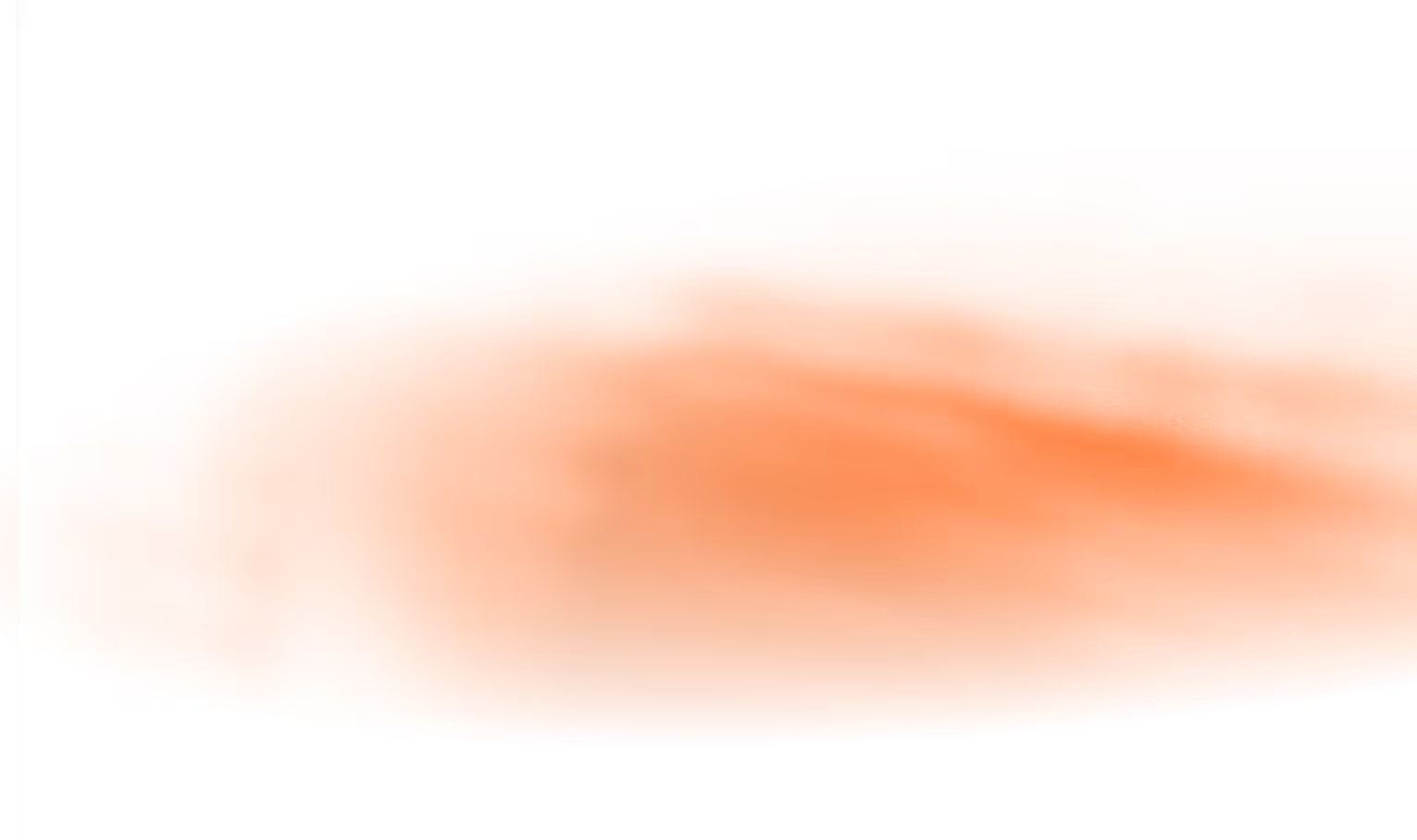
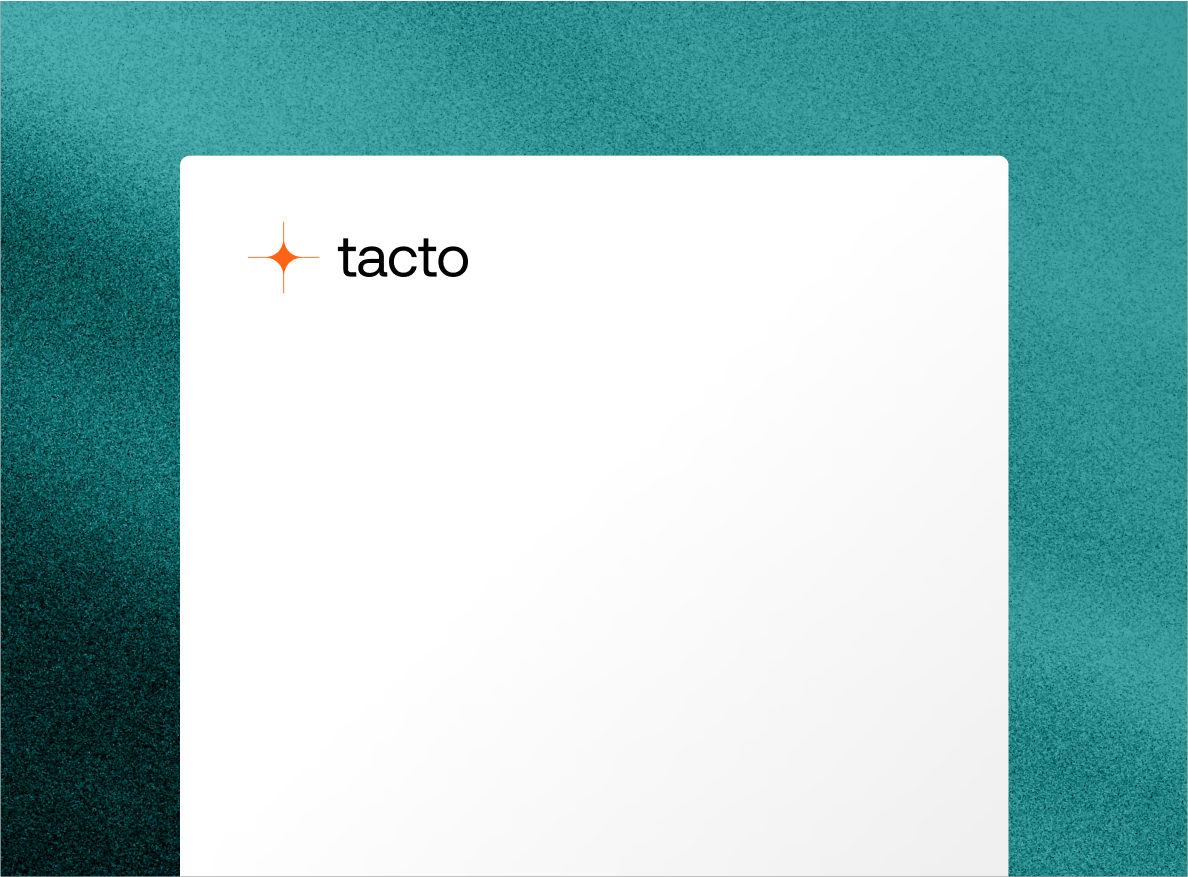