Procurement Glossary
Bill of materials: Definition & important aspects for buyers
As a central planning tool, the bill of materials forms the foundation for efficient procurement and production processes in companies. This structured overview shows how Procurement can use the bill of materials to plan material requirements optimally and control costs transparently.
Parts list to the point:
A bill of materials is a structured list of all components, assemblies and materials required to manufacture an end product. For Procurement , it serves as an essential planning basis for material procurement, cost calculation and timely coverage of requirements.
Example: The parts list for an office chair comprises 27 individual parts, including 1 frame, 5 castors, 1 gas pressure spring, 2 armrests and 12 connecting elements, whereby Procurement determines a total material requirement of 485 euros per chair based on the precise list and can plan the procurement accordingly.
Parts list - An introduction
The bill of materials is a fundamental tool in production planning and materials management. It represents a structured list of all components, assemblies and raw materials required for the manufacture of an end product. As a central document in production planning, the bill of materials enables precise material requirements planning, cost calculation and process control. In this guide, we will take a closer look at the different types of BOMs, their importance for production and the most important aspects of their creation and management. We will also look at modern digital solutions and their integration into ERP systems.
What is a parts list?
A bill of materials is a detailed list of all components and materials required to manufacture an end product. It lists all individual parts, assemblies and raw materials with their respective quantities. As a central document in production control, the bill of materials forms the basis for material planning, production and cost calculation.
Core elements of a parts list
Importance of the bill of materials in Procurement
For Procurement , the bill of materials is an indispensable tool for planning exact material requirements and designing efficient procurement processes. It enables the early identification of required materials, supports supplier selection and helps to reduce costs by optimizing order quantities. It also contributes to transparency in the supply chain and facilitates risk management.
Parts list: From manual documentation to intelligent digital parts lists
The bill of materials is the central element for efficient production and effective Procurement, as it lists every component and material of a product in detail. Based on theoretical principles, it enables precise requirements planning and control in all areas of the company. However, in the face of increasing product complexity and accelerated market requirements, traditional management is reaching its limits. The need for a transformation towards digital solutions is becoming increasingly clear in order to optimize processes and remain competitive.
Old: Manual parts list management
Traditional approach: In the past, parts lists were often created manually and kept in paper-based form or simple tables. This manual documentation took a considerable amount of time to create and update. Changes to the product design had to be manually entered into all copies of the BOM, increasing the risk of errors and inconsistencies. Communication between Development, Procurement and Production was fragmented and delays were commonplace. The lack of transparency also made it difficult to react quickly to short-term change requests or market analysis.
New: Intelligent digital parts list
Bill of Materials (BOM): Modern companies rely on digital bills of materials that are integrated intelligently and networked into ERP and PLM systems. Through digitalization, BOMs are generated automatically and updated in real time, enabling seamless collaboration between all departments. Innovations such as cloud-based platforms and AI-supported analyses optimize data management and enable just-in-time deliveries. The benefits are numerous: error rates are reduced by up to 95%, the product development cycle is shortened by an average of 30% and transparency across the entire product life cycle is significantly increased.
Practical example: Mechanical engineering company
An internationally active mechanical engineering company implemented digital parts list management in its ERP system. This integration reduced the time needed to create parts lists from 5 days to just a few hours. The error rate in production fell by 40% as all departments were able to access up-to-date data at all times. In addition, the improved data quality led to savings of 10% in material costsas Procurement was able to carry out more precise requirements planning and better negotiations with suppliers.
Conclusion on the parts list
Parts lists are a fundamental tool for efficient production and procurement management. Thanks to their detailed listing of all components, they ensure precise material planning and cost control. Despite challenges such as complexity management and up-to-dateness assurance, modern, digital solutions offer new opportunities for even more efficient BOM management. The trend towards AI-supported, dynamic systems will further increase the strategic importance of BOMs in the future.
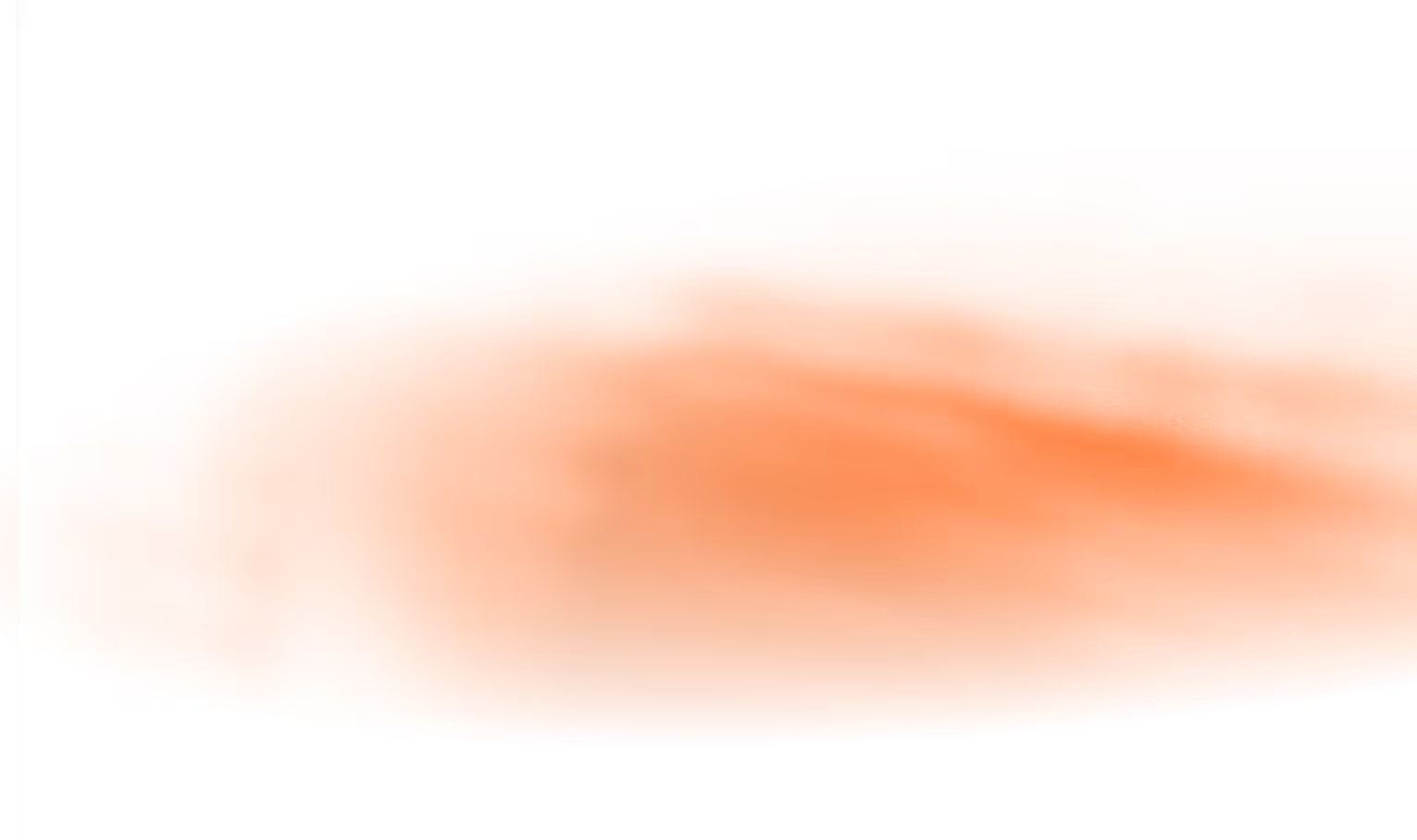
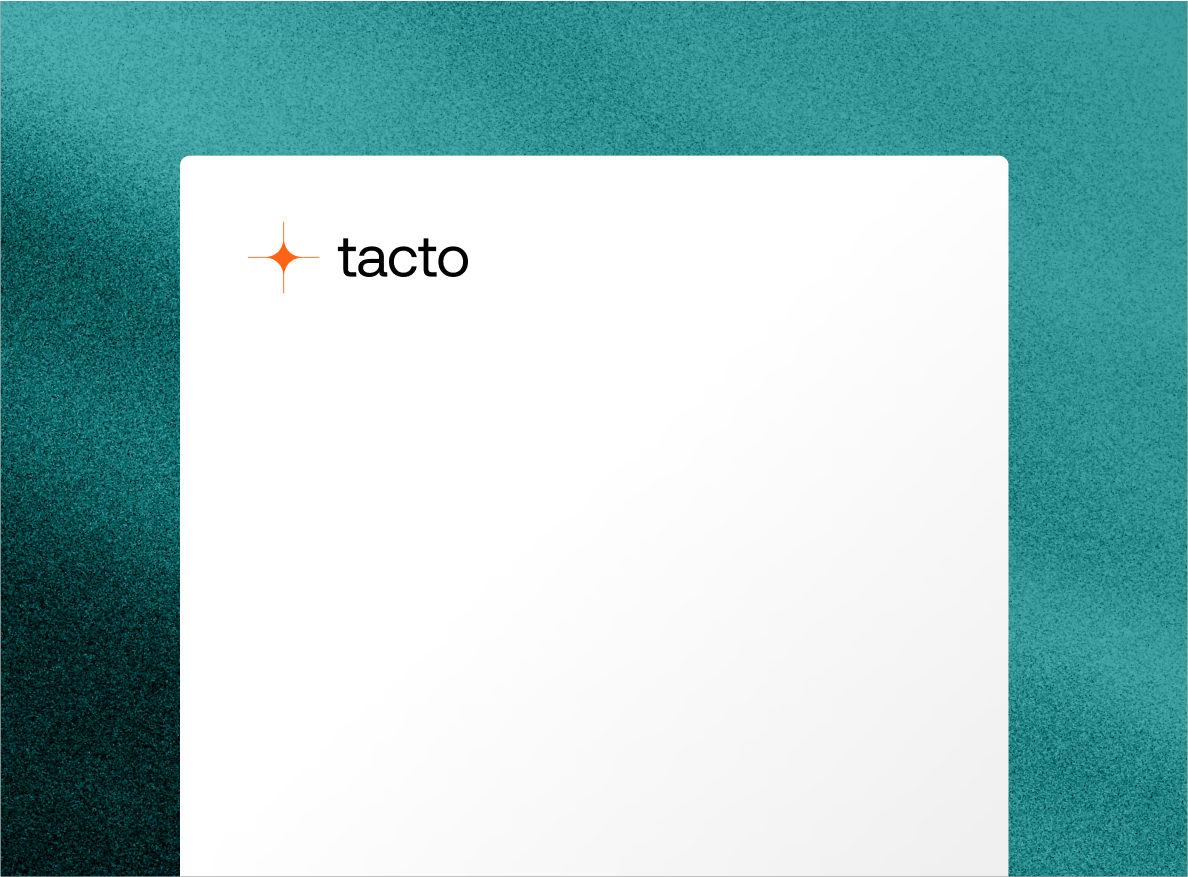