Procurement Glossary
Vertical integration: definition & important aspects for buyers
Vertical integration enables companies to strategically control their value chain and thus create decisive competitive advantages through greater efficiency and independence. This structured overview shows the various forms of integration and their significance for modern procurement strategies in Procurement .
Vertical integration in a nutshell:
Vertical integration describes the expansion of corporate activities along the value chain by taking over upstream or downstream production or trading stages. For Procurement , this means a fundamental realignment of the procurement strategy, as previous external supplier relationships are replaced by internal service relationships.
Example: A car manufacturer takes over an important supplier of electric motors for 250 million euros, thereby transferring 30% of the previous outsourcing to in-house production and reducing dependence on external suppliers.
Introduction to vertical integration
Vertical integration is an important corporate strategy in which a company combines different stages of the value chain under one roof. This strategy enables companies to gain more control over their production and distribution processes and reduce their dependence on external partners. Vertical integration can take place both in the direction of raw material extraction (backward integration) and in the direction of the end customer (forward integration). In this introduction, we will take a closer look at the various aspects of vertical integration, its advantages and disadvantages and its strategic importance for modern companies.
What is vertical integration?
Vertical integration refers to the incorporation of upstream or downstream production stages into a company. This involves a company taking over activities along the value chain that were previously carried out by suppliers or customers. The aim is to gain more control over the production process, reduce costs, increase efficiency and reduce dependencies on external partners.
Core elements of vertical integration
Significance for Procurement
Vertical integration has a significant impact on Procurement . It makes it possible to increase security of supply by covering critical supplier functions internally. In addition, costs can be reduced as external margins are eliminated and economies of scale can be utilized. Direct control over production steps means that quality can be improved and processes can be flexibly adapted to market changes.
Vertical integration: From fragmented supply chains to vertically integrated processes
Building on the theoretical concept of vertical integration, it is becoming clear in practice how crucial this strategy is for modern companies. In the face of globalized markets and increasing competitive dynamics, vertical integration enables greater control over the value chain. The practical significance lies in the ability to achieve risk management, reduce costs and react quickly to market changes. A transformation from traditional to integrated processes is therefore becoming a necessity in order to remain competitive in the long term.
Old: Fragmented supply chains
Traditional approach: In traditional business models, supply chains are often fragmented, with each link in the chain operated by specialized external partners or supplier management. Companies focus on their core competencies and rely on third parties for upstream or downstream processes. However, this practice leads to several challenges: Coordination between different partners can be complex and time-consuming, limiting responsiveness to market changes. In addition, dependence on external suppliers increases the risk of supply bottlenecks and quality problems. Fragmented supply chains also make it difficult to implement holistic quality and sustainability standards, as control over external processes is limited.
New: Vertical integration
Vertical integration: The modern implementation of vertical integration means that companies integrate upstream or downstream processes into their own organization. This integrated approach means that key processes are controlled internally, which increases efficiency and reduces costs. Innovative technologies such as digital supply chain and data analytics play a crucial role in this. They enable seamless integration of the value creation stages and promote transparency along the entire chain. Practical benefits include an improved quality assurance agreement through direct control, faster time-to-market through shortened development cycles and increased customer loyalty through individual customization options. Vertical integration thus creates a dynamic and adaptable business process that meets current market requirements.
Practical example: Automotive industry
A leading car manufacturer has integrated the production of electric motors into its own value chain instead of sourcing them from external suppliers. This vertical integration enabled the company to reduce production costs for electric motors by 18% and shorten the development time for new models by 25%. At the same time, the energy efficiency of the vehicles improved by 15%, resulting in higher customer satisfaction and an increase in market share in the electric vehicle segment. Direct control over a critical component also made it possible to implement innovations more quickly and respond more flexibly to customer requirements.
Conclusion on vertical integration
Vertical integration is an important strategic option for companies seeking more control over their value chain. Despite high investment costs and increasing complexity, it offers decisive advantages such as cost savings, improved quality control and increased security of supply. Success depends largely on careful planning, effective integration management and strategic alignment. Especially in times of uncertain supply chains and increasing sustainability requirements, vertical integration is becoming increasingly important.
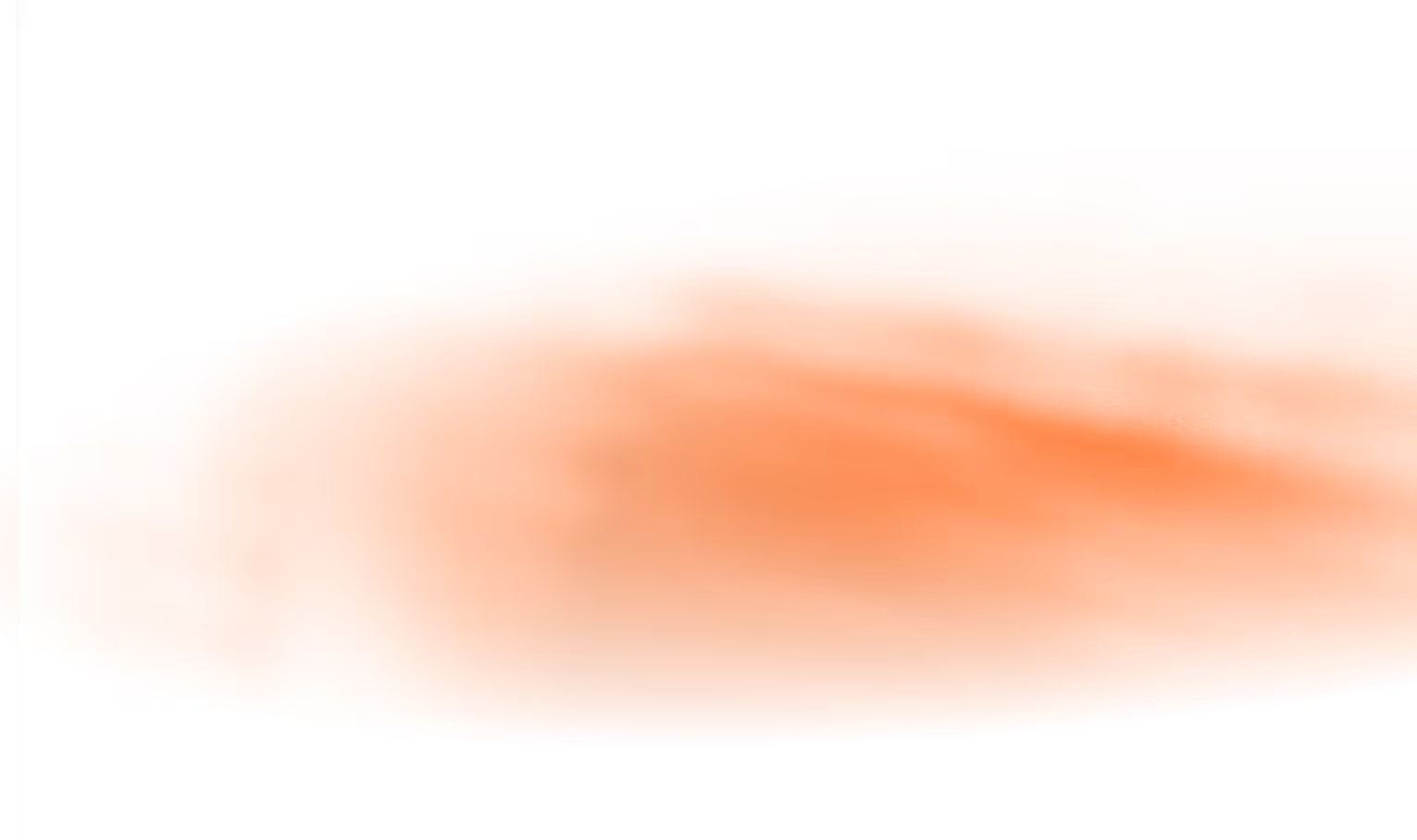
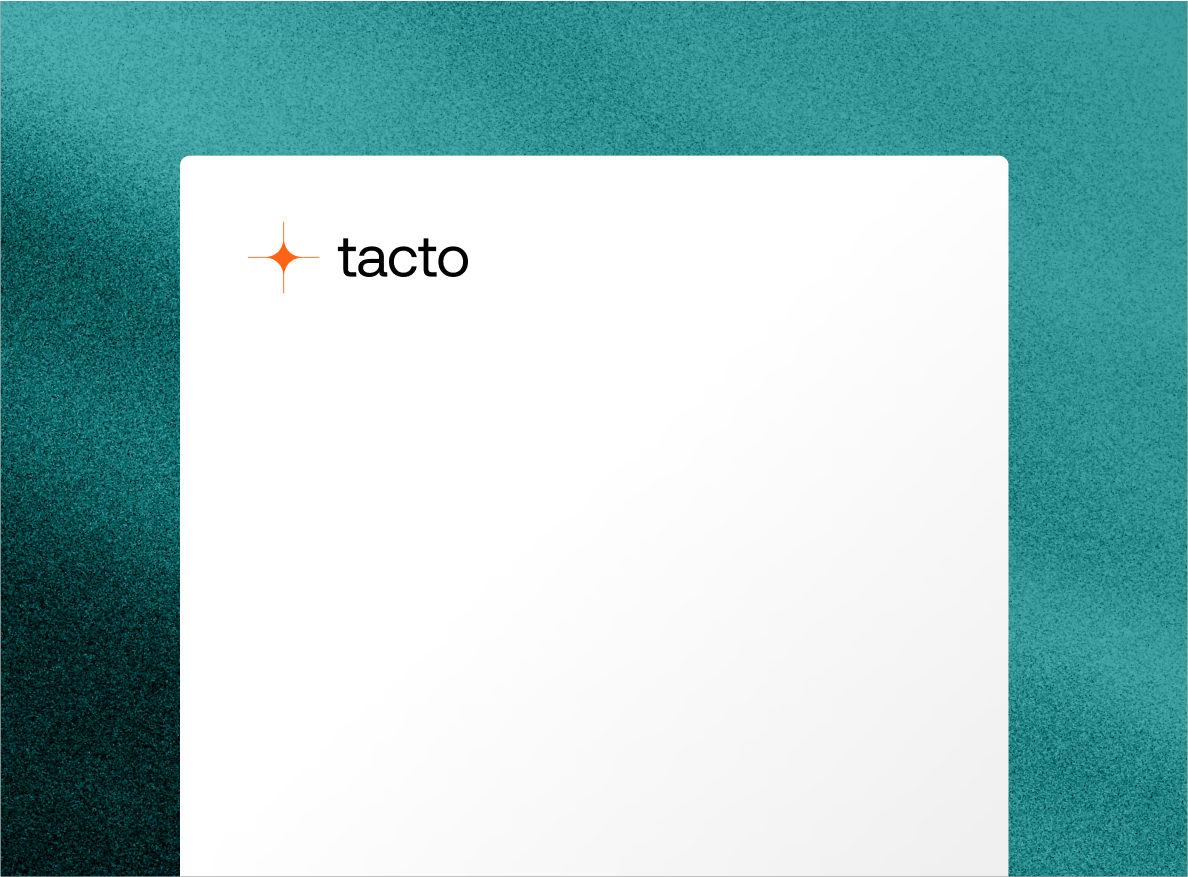