Procurement Glossary
Incoming goods inspection: definition & important aspects for buyers
Systematic incoming goods inspection ensures the quality of purchased goods and protects against delivery errors that could jeopardize the company's success. This overview shows you the most important inspection steps and control mechanisms with which you can minimize risks in Procurement and optimize supplier relationships.
Incoming goods inspection in a nutshell:
The incoming goods inspection is a systematic control process for checking incoming deliveries with regard to quantity, quality and compliance with the order. It is essential for Procurement in order to evaluate supplier performance, ensure quality standards and avoid subsequent complaints.
Example: An automotive supplier carries out a three-stage incoming goods inspection for every delivery of metal parts within 24 hours: Quantity inspection of 1,000 parts, visual inspection of 50 random samples and dimensional inspection of 10 parts according to defined tolerance limits of ±0.1mm.
Incoming goods inspection: Efficient management of incoming goods
Incoming goods inspection is an essential process in the quality assurance and logistics of companies. It ensures that incoming goods meet the agreed quality standards and are delivered in the right quantity, at the right time and to the right place. A thorough incoming goods inspection is of fundamental importance for the entire value chain, as it plays a key role in preventing production downtime, quality defects and customer complaints. In this guide, you will learn all the important aspects of incoming goods inspection, from the legal basis and the various inspection methods to modern digital solutions for efficient implementation.
What is the incoming goods inspection?
The incoming goods inspection is an essential process in procurement management in which delivered goods are checked for quality, quantity and compliance with the order conditions. The aim is to ensure that the delivered products meet the defined specifications and are free from defects. This step prevents defective or non-conforming goods from entering the production process or being forwarded to customers.
Core elements of the incoming goods inspection
Significance for Procurement
In Procurement , the incoming goods inspection plays a decisive role in quality assurance and customer satisfaction. It makes it possible to identify supplier errors at an early stage and initiate appropriate complaints. An effective incoming goods process can reduce costs caused by faulty products and strengthen relationships with reliable suppliers.
Incoming goods inspection: from manual inspection to automated quality inspection
Incoming goods inspection is a crucial process to ensure the quality inspection of delivered goods and thus guarantee production and customer satisfaction. Building on the theoretical importance of this inspection, in practice it is essential to optimize the efficiency and accuracy of this process. With increasing demands and ever more complex supply chains, there is an urgent need to rethink traditional methods and implement modern technologies.
Old: Manual incoming goods inspection
Traditional approach: In the classic incoming goods inspection, incoming goods are checked manually by employees. This involves manually comparing delivery bills and orders, counting the quantities and visually checking the quality. Tools such as paper checklists and simple measuring devices are used. This method is time-consuming, error-prone and does not provide real-time information for downstream processes. It can also lead to delays in production control if defects are only detected late.
New: Automated incoming goods inspection
Automated Goods Receipt Inspection: This modern approach integrates digital technologies and automated systems into the goods receipt process. With the help of RFID tags, barcode scanners and networked sensors, goods are automatically recorded on arrival and relevant data is transferred to the ERP system in real time. AI-supported algorithms analyze quality data and identify potential deviations immediately. This leads to a significant reduction in inspection times, increases accuracy and enables proactive decisions. The improved transparency also promotes collaboration with suppliers and optimizes the entire supply chain.
Practical example: Automated testing in the automotive industry
A leading automotive manufacturer implemented an automated incoming goods inspection using RFID technology. The real-time recording of deliveries reduced the inspection time by 60%. Quality deviations were detected at an early stage, which led to a reduction in complaint management by 30 %. The increase in efficiency resulted in annual cost savings of over 500,000 euros and improved production planning.
Conclusion on the incoming goods inspection
Incoming goods inspection is an indispensable part of modern quality management. It not only ensures product quality and reduces costs, but also enables continuous evaluation and optimization of supplier relationships. Due to increasing digitalization and automation, incoming goods inspection is constantly evolving and becoming even more efficient. Success lies in the balance between thorough inspection, time efficiency and strategic further development of the inspection processes.
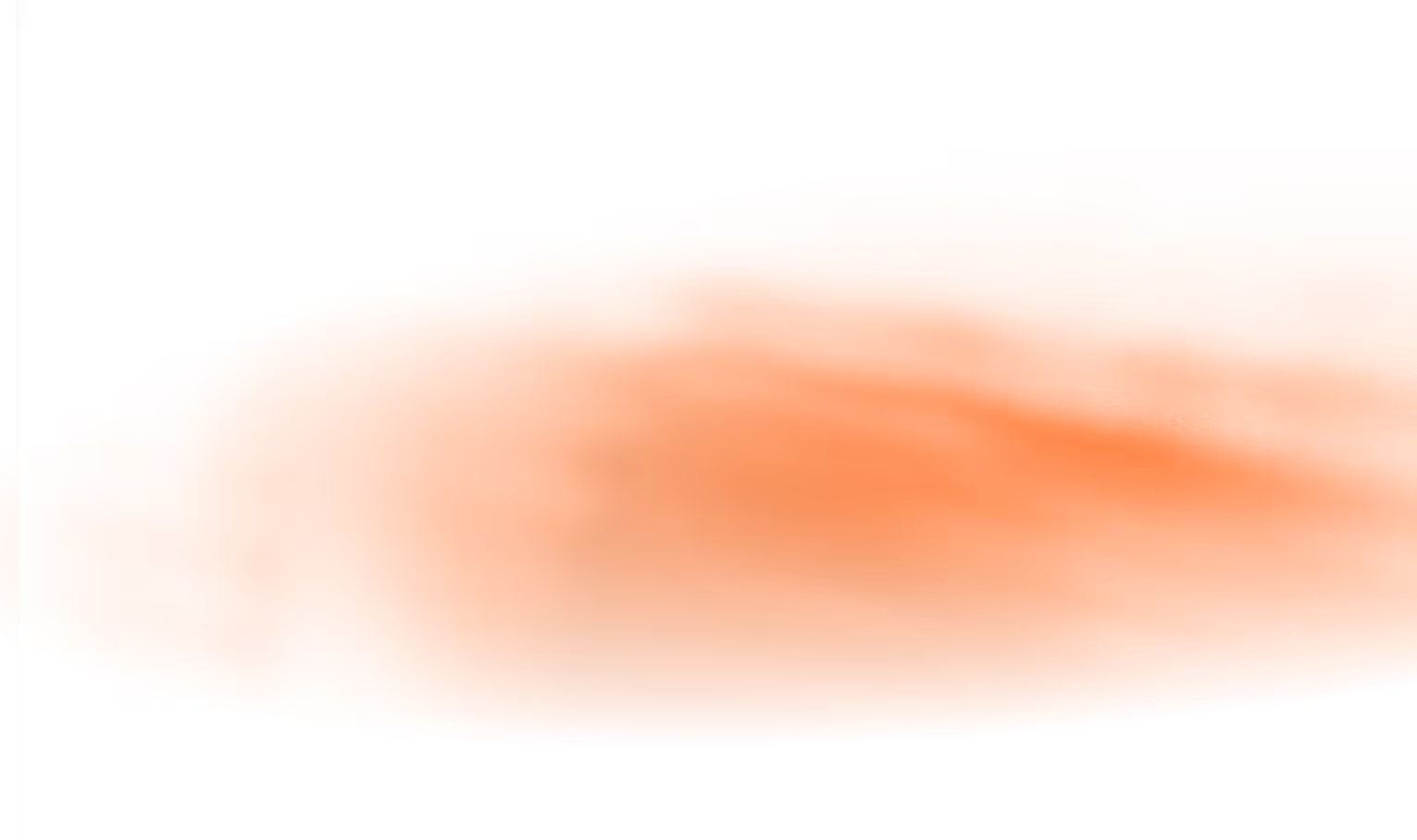
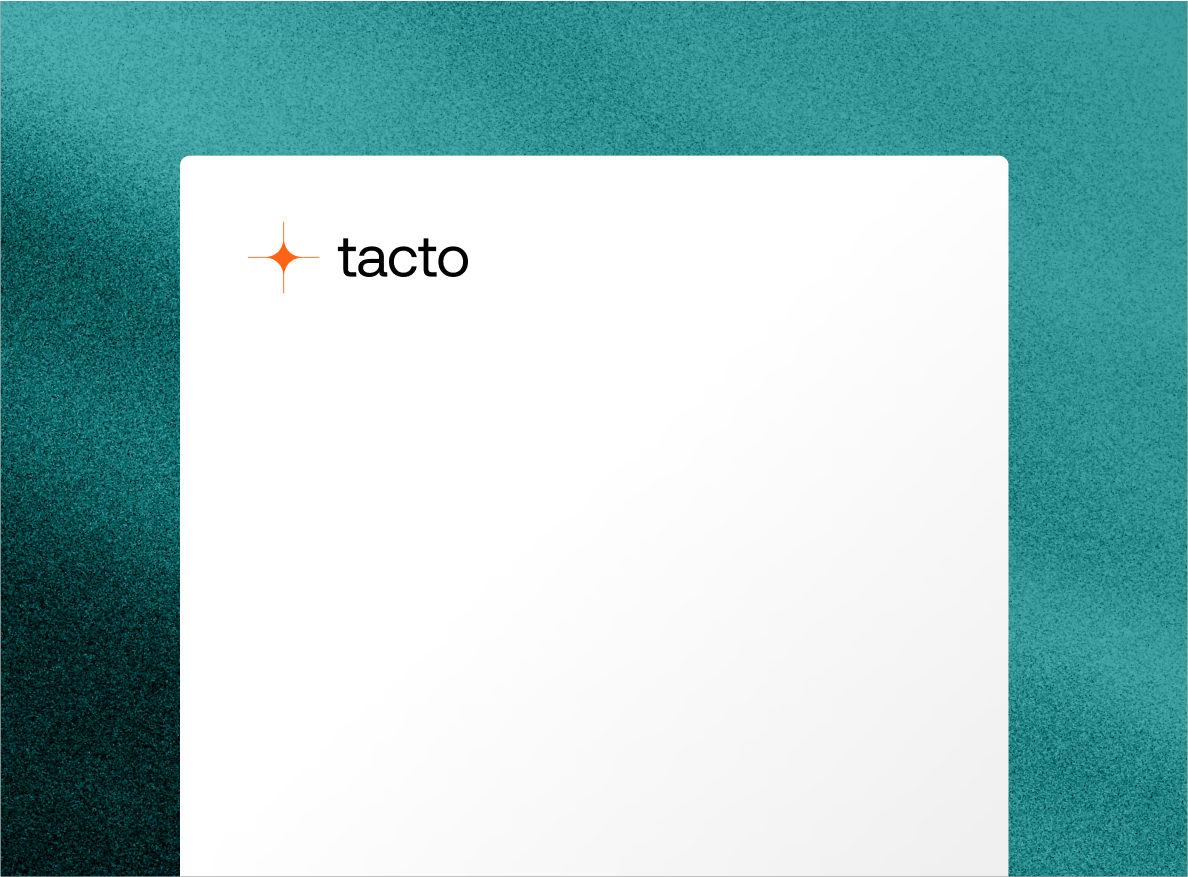