Procurement Glossary
Process organization: definition & important aspects for buyers
As a core element of process management, process organization creates the basis for efficient and smooth workflows in companies. This structured overview shows how you can shorten throughput times and sustainably reduce costs by optimizing your purchasing processes.
Process organization in a nutshell:
The process organization defines the temporal and spatial structuring of work processes as well as their logical sequence and dependencies. In Procurement , it enables the efficient processing of procurement procedures through clearly defined process flows and minimizes throughput times and sources of error.
Example: A medium-sized company optimizes its ordering process through a new workflow organization, which reduces the lead time of standard orders from an average of 5 working days to 2 working days by streamlining approval processes and clearly defining interfaces between Procurement, the specialist department and suppliers.
Process organization in purchasing controlling
Process organization is a fundamental component of organizational management in companies. It deals with the temporal and spatial structuring of work processes and their optimal design. In contrast to the organizational structure, which deals with hierarchical structures, the process organization focuses on the dynamic aspects of work processes. It determines how individual activities are coordinated and harmonized to ensure an efficient workflow. In this introduction, we will take a closer look at the most important concepts, methods and tools of process organization and work out their significance for the success of a company.
What is process organization?
The process organization deals with the design and optimization of Procurement processes within a company. It determines the order in which tasks are completed, who is responsible for them and which resources are used. The aim is to structure workflows efficiently and effectively in order to save time and costs and improve the quality of results.
Core elements of the process organization
- Process analysis: Examination of existing processes to identify weak points
- Process design: development of new or optimized processes
- Use of resources: Effective allocation of personnel, machines and materials
- Communication: Ensuring a smooth flow of information between the parties involved
Importance of process organization in Procurement
In procurement, process organization is crucial for the efficiency of purchasing processes. Clearly defined processes can shorten procurement cycles, reduce costs and optimize supply chain resilience. An efficient process organization supports buyers in achieving strategic goals and securing competitive advantages.
- Cost reduction: Reduction of process costs through efficient workflows
- Time savings: speeding up ordering and delivery processes
- Quality improvement: improving process quality and compliance
Process organization: From sequential process design to agile workflows
Building on the theoretical understanding of process organization, it becomes clear how crucial its practical implementation is to a company's success. Traditionally, process costs have been linear and rigid, which can lead to inefficiencies in a fast-paced business world. The need to respond more quickly to market changes and make optimal use of internal resources requires a shift towards flexible process structures. This need for transformation enables companies to be more agile and competitive.
Old: Sequential process design
Traditional approach: In the traditional process organization, work processes are planned and implemented strictly sequentially. Each process step follows the previous one, with clearly defined tasks and responsibilities. Although this linear structure enables quality control and predictability, it often leads to long lead times and limited adaptability. Changes in the market or internal deviations can only be taken into account with difficulty and slowly in the existing processes. In addition, resources are not always used optimally, as rigid processes offer little scope for increasing efficiency.
New: Agile workflows
Agile workflows: Modern process organization relies on agile methods that focus on flexibility and continuous improvement. Processes are divided into iterative cycles, allowing teams to react quickly to changes. Self-organized teams use tools such as Scrum or Kanban systems to make workflows transparent and identify bottlenecks at an early stage. Digital platforms enable real-time communication and collaborative work across departmental boundaries. These innovative steps lead to more efficient processes, shorter response times and greater employee satisfaction, as responsibility and decision-making authority are decentralized.
Practical example: Agile transformation in software development
A medium-sized software company switched from a traditional sequential process design to agile workflows. By introducing scrum teams and daily stand-up meetings, the company was able to reduce the time-to-market of new products was reduced by 30%. The error rate in delivered software solutions fell by 20% thanks to regular feedback and adjustments during the development phases. Employees reported higher motivation and commitment, which was reflected in a 15% increase in productivity. Overall, the agile process organization led to a better competitive position and increased customer satisfaction.
Conclusion on process organization
Process organization is an indispensable tool for optimizing purchasing processes. Clear structures, standardized procedures and efficient communication channels not only reduce costs and shorten throughput times, but also sustainably improve the quality of procurement processes. Success depends largely on consistent implementation, the involvement of all those involved and a willingness to continuously adapt. In view of digitalization and new technologies, the importance of a well-thought-out process organization will continue to increase.
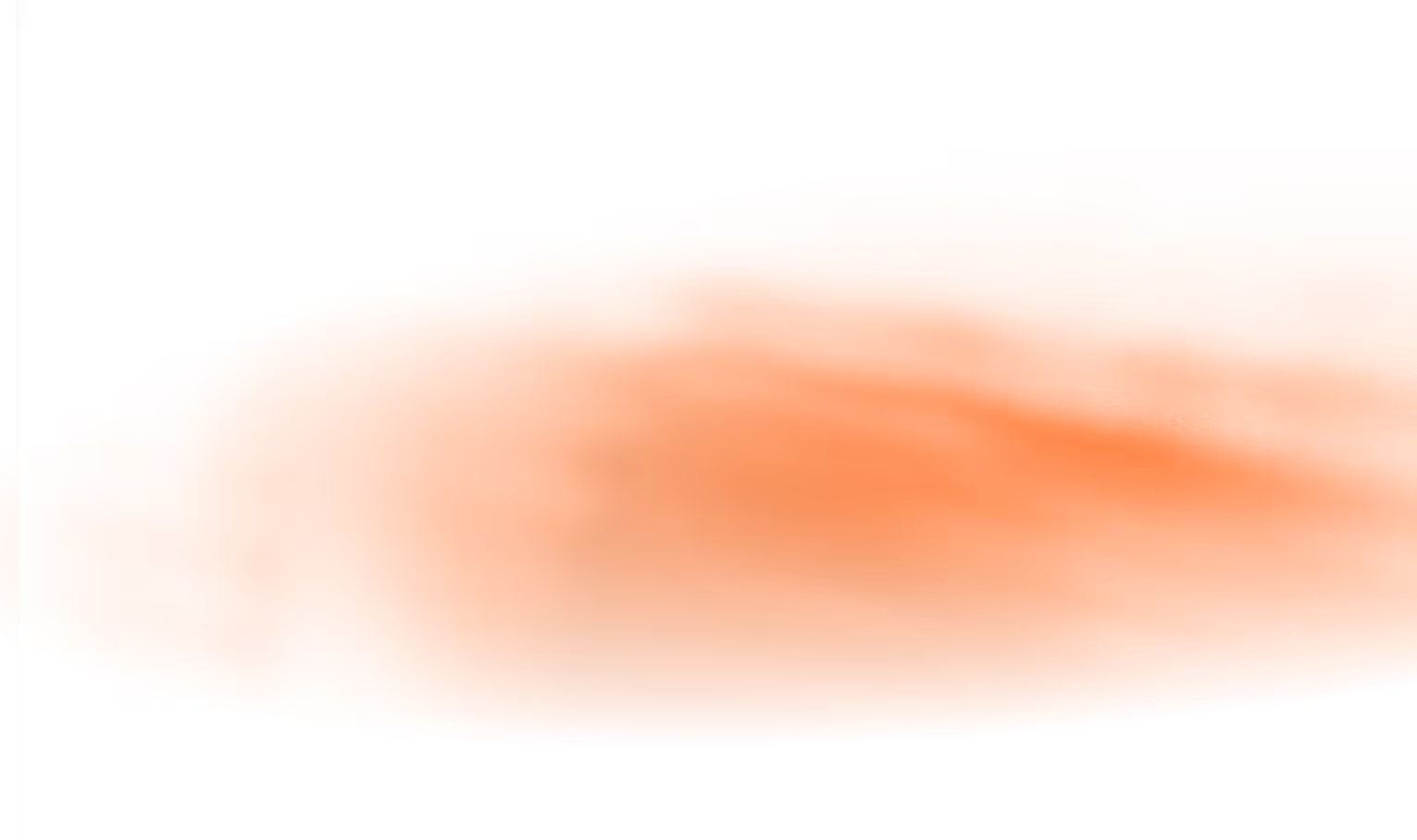
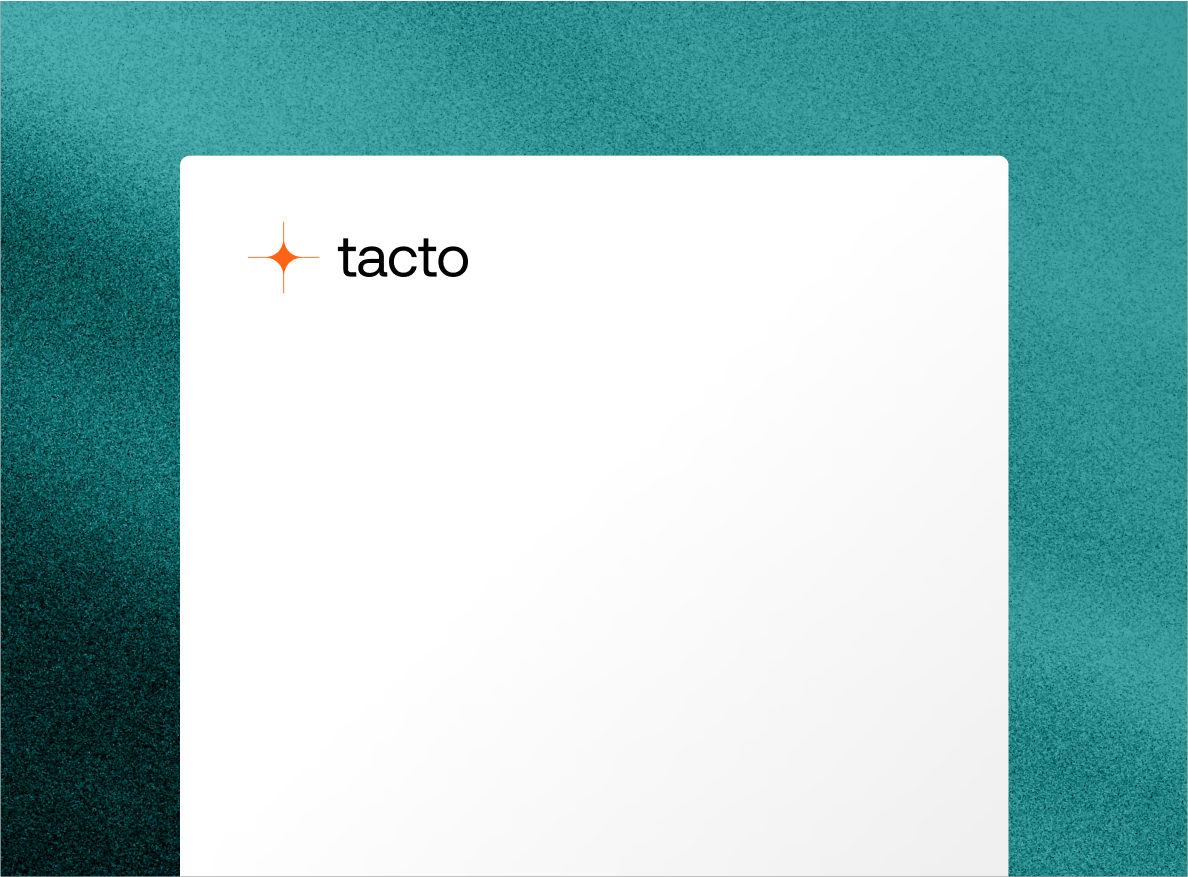