Procurement Glossary
Kanban system: definition & important aspects for buyers
The Kanban system is revolutionizing procurement through demand-driven processes, reduced storage costs and symbiotic supplier integration - a method that not only minimizes inventories but also maximizes the agility of supply chains in volatile markets.
What is a Kanban system?
A Kanban system is a pull-based control method for material flow and production in which the actual consumption of goods triggers replenishment. Developed at Toyota in the 1940s, it replaces classic push planning with a self-regulating logic: every withdrawal process automatically generates a reorder impulse that prompts suppliers or internal production stages to replenish.
Core components are:
- Kanban signals (physical cards, digital triggers)
- Containers with defined batch sizes
- Replenishment times as a critical control parameter
Introduction to the Kanban system
Historical development and Toyota production system
Taiichi Ohno developed Kanban in response to the inefficiencies of mass production. While Western manufacturers focused on large batch sizes, Toyota prioritized the reduction of muda (waste):
- JIT deliveries to avoid warehousing costs
- Autonomous control loops for the decentralization of decisions
- Visual control for real-time transparency
One breakthrough was the decoupling of production stages using Kanban cards - instead of centralized planning, each stage controls its own output based on the consumption of the downstream stage.
Pull principle vs. push principle in procurement
In the push system, scheduling is based on forecast requirements, which leads to excess stock when demand drops. Kanban inverts this logic:
Kanban push system (pull)
Control pulse Forecast consumption
Stock level High (buffer) Low
Flexibility Low High
Throughput times Long Short
Studies show that Kanban increases inventory turnover by 30-50% while at the same time reducing the risk of shortages by 60%.
Implementation in procurement
System design and critical parameters
Successful implementation requires the specification of:
1. batch sizes: At 200 pieces/day and 3 days delivery time plus 1 day buffer: 200 × (3+1) = 800 pieces
2. signal types:
- Transport Kanban: Initiates material transport between warehouse and point of consumption
- Production Kanban: Triggers internal post-production
- Supplier Kanban: Automated ordering from external partners
3. digital Kanban solutions: Modern systems replace physical cards with:
- RFID chips in containers
- IoT sensors for fill level detection
- Cloud-based order automation with EDI interfaces
Case study: Automotive supplier reduces C-parts costs by 22%
A global supplier implemented a two-stage Kanban for 5,000 C-parts (screws, seals):
- Level 1: In-plant supermarkets with 24-hour replenishment
- Stage 2: External consignment warehouse at suppliers with 72h delivery window
Results after 12 months:
- Stocks ↓ from 18 to 6 days
- Ordering costs ↓ 45% due to automation
- Missing parts ↓ 78%
- Total cost savings: 680,000 €/year
Digital transformation of Kanban systems
From paper to AI-driven forecasting
Traditional Kanban systems reach their limits with high variant diversity. E-Kanban solutions address these through:
- Real-time dashboards with stock forecasts via machine learning
- Dynamic batch size adjustment based on market indicators
- Blockchain-based supplier networks for transparent capacity planning
One example is the KanbanBOX platform, which:
- Suppliers integrated in 12 languages
- Automatic conversion of consumption data into orders
- Multi-animal supply chains synchronized
ROI of digital Kanban systems
A McKinsey study shows that digital Kanban implementations achieve the following effects:
- Litigation costs (-35 %)
- Order accuracy (+90 %)
- Supplier response time (-60 %)
- Storage capacity utilization (+40 %)
Critical success factors and risks
Organizational requirements
- Cross-functional teams from Procurement, logistics and production
- Training programs for skills development
- KPI system with a focus on stock turnover and delivery reliability
Typical implementation errors
- Over-complex control loops: More than three Kanban stages increase the susceptibility to faults
- Static lot sizes: Ignoring seasonality leads to stock shortages
- Lack of supplier involvement: 73% of failed projects neglect supplier development
Future prospects and fields of innovation
Kanban 4.0: Integration into the Smart Factory
- Predictive Kanban: Predicting consumption using digital twins
- Autonomous logistics robots: Self-ordering AGVs (Automated Guided Vehicles)
- AI-based exception management: Automated escalation in the event of delivery bottlenecks
Siemens is a pioneer in electronics manufacturing:
- Uses energy consumption data to forecast demand
- Adjusts supplier capacities in real time
- 98% delivery reliability achieved with 30% lower safety stocks
Conclusion and recommendations for action
Kanban systems are not a panacea, but they are an indispensable tool for purchasing managers who:
- Systematically reduce storage costs
- Strengthening supplier relationships through collaborative planning
- Building resilience against market turbulence
Concrete steps for implementation:
- Start pilot project with 5-10 high-volume C-parts
- Evaluate digital Kanban tools with ERP interface
- Conduct supplier workshops for capacity planning
- Continuous improvement via monthly PDCA cycles
As the example of the automotive supplier shows, savings of 20-30% in procurement costs are realistic - provided that the system is understood as a strategic management tool and not as an operational quick-fix solution. In times of volatile markets, Kanban thus becomes a survival strategy for manufacturing companies.
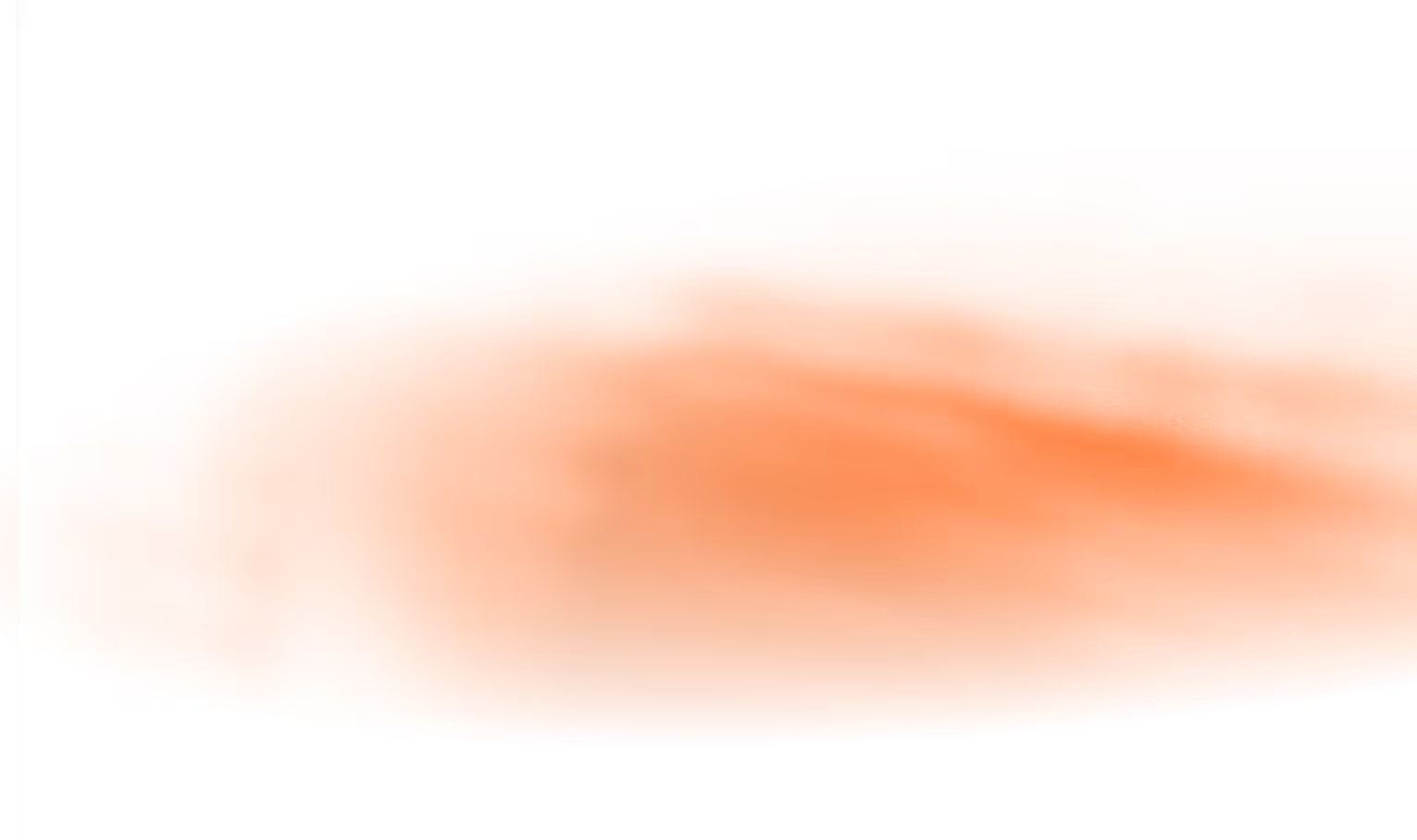
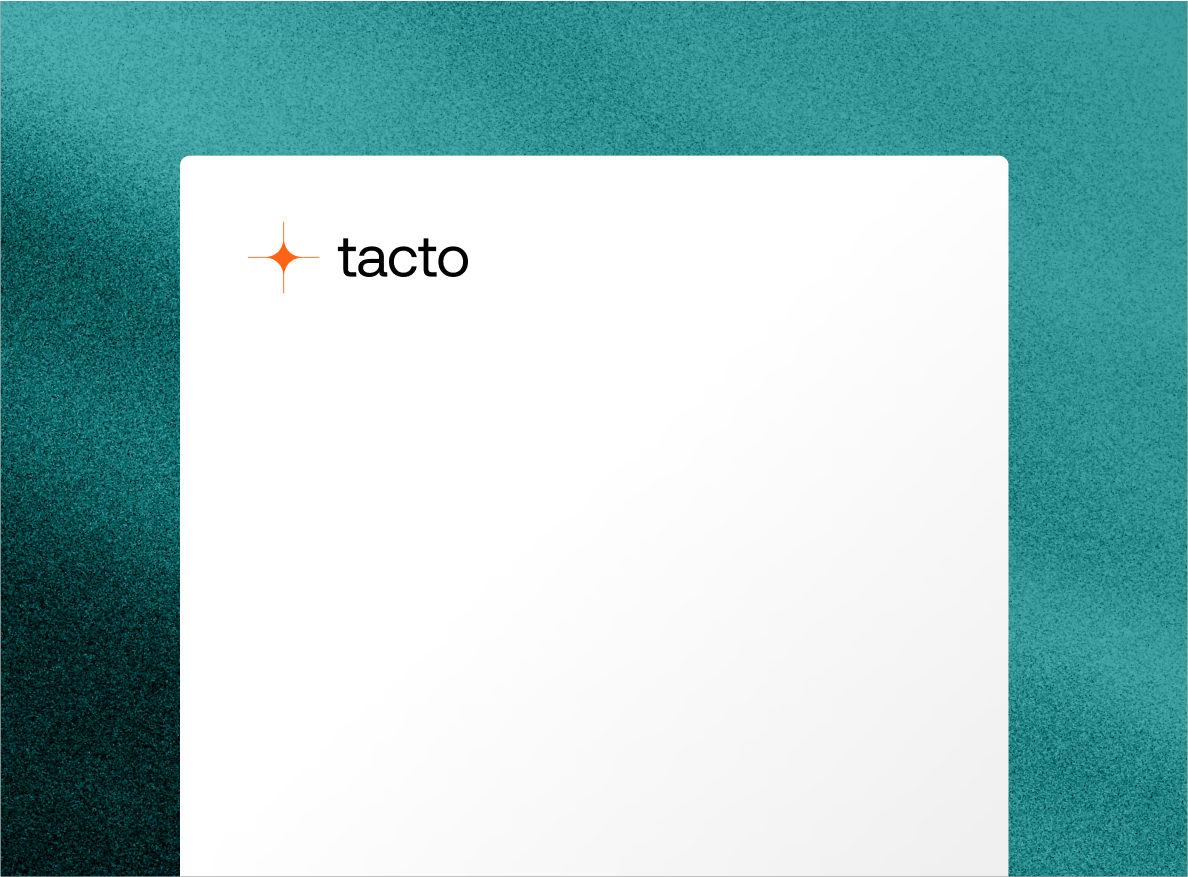