Procurement Glossary
Delivery concepts: Definition and important aspects for buyers
Delivery concepts optimize the entire value chain through efficient planning and control of incoming goods processes. This structured overview shows how Procurement can reduce costs and increase security of supply through the right choice and design of delivery concepts.
Delivery concepts in a nutshell:
Delivery concepts are systematic plans and agreements between supplier and customer on the type, timing and modalities of goods delivery. For Procurement , they are a strategic tool for optimizing logistics costs, inventories and process efficiency in the supply chain.
Example: An automotive supplier implements a just-in-sequence delivery concept in which seat covers are delivered exactly 4 hours before installation in the correct production sequence, which reduces warehousing costs by 35% and increases assembly efficiency by 20%.
Delivery concepts: An introduction
In modern logistics and supply chains, delivery concepts are of crucial importance for the smooth flow of goods movements. They form the foundation for efficient and cost-saving material supply in companies. A well thought-out delivery concept not only coordinates incoming goods, but also optimizes the entire supply chain from the supplier to the end consumer. This introduction looks at the various aspects of delivery concepts, from classic methods to innovative just-in-time and just-in-sequence solutions, which are becoming increasingly important in modern Industry 4.0.
What are delivery concepts?
Delivery concepts are strategic plans and methods that define how goods and materials are transported and delivered from the supplier to the company. They include the design of delivery processes, the selection of suitable means of transportation, the definition of delivery times and the determination of delivery quantities. The aim is to design the material flow efficiently, reduce costs and ensure a smooth supply to production.
Core elements of delivery concepts
Significance for Procurement
Delivery concepts are of great importance for Procurement , as they directly influence the efficiency and flexibility of the supply chain. By implementing suitable delivery concepts, costs can be reduced, inventories optimized and delivery times shortened. They also enable closer cooperation with suppliers and help to minimize risk by increasing security of supply and avoiding bottlenecks.
Delivery concepts: From traditional delivery methods to just-in-time strategies
The efficient design of delivery concepts plays a decisive role in modern procurement logistics. Based on the theoretical principles of delivery concepts, the practical implementation is of great importance for companies. Traditional delivery methods are reaching their limits in the face of increasing demands for flexibility and cost optimization. There is therefore an urgent need to integrate innovative approaches in order to optimize the material flow and remain competitive.
Old: Traditional delivery methods
Traditional approach: In traditional delivery concepts, materials were often ordered and stocked in large quantities. Deliveries were made according to fixed schedules, regardless of actual demand. Typical tools were manual ordering systems and simple stock management. These methods led to high stock levels, tied-up capital and limited flexibility. Challenges such as excess stock, outdated goods and high warehousing costs were the result, which significantly limited the ability to react to market changes.
New: Just-in-time and Kanban systems
Just-in-time: Modern delivery concepts rely on demand-oriented delivery strategies such as just-in-time (JIT) and Kanban systems. By working closely with suppliers and using digital technologies, materials are delivered exactly when they are needed. Innovative elements such as real-time data exchange, automated ordering processes and flexible transport planning optimize the material flow. The practical benefits are significant reductions in stock levels, lower warehousing costs and increased adaptability to changes in demand. Companies benefit from leaner processes and increased efficiency in the supply chain.
Practical example: Automotive industry
A leading car manufacturer implemented a just-in-time delivery concept in its production. By integrating suppliers into the in-house planning system, materials were delivered in sync with production. This enabled a 60% reduction in stock levels and a 35% reduction in storage costs. The production control increased and throughput times were reduced by 20%. Overall, this led to annual savings of over 10 million euros and a significantly improved ability to respond to market requirements.
Conclusion on the optimization of delivery concepts
Supplier consignment is an effective delivery concept for optimizing the supply chain. By shifting the capital commitment to the supplier and withdrawing as required, storage costs are significantly reduced. Despite the challenges of IT integration and contract design, the benefits such as increased flexibility and improved liquidity outweigh the disadvantages. Modern technologies such as IoT and AI will further increase the efficiency of consignment warehouses and enable new business models.
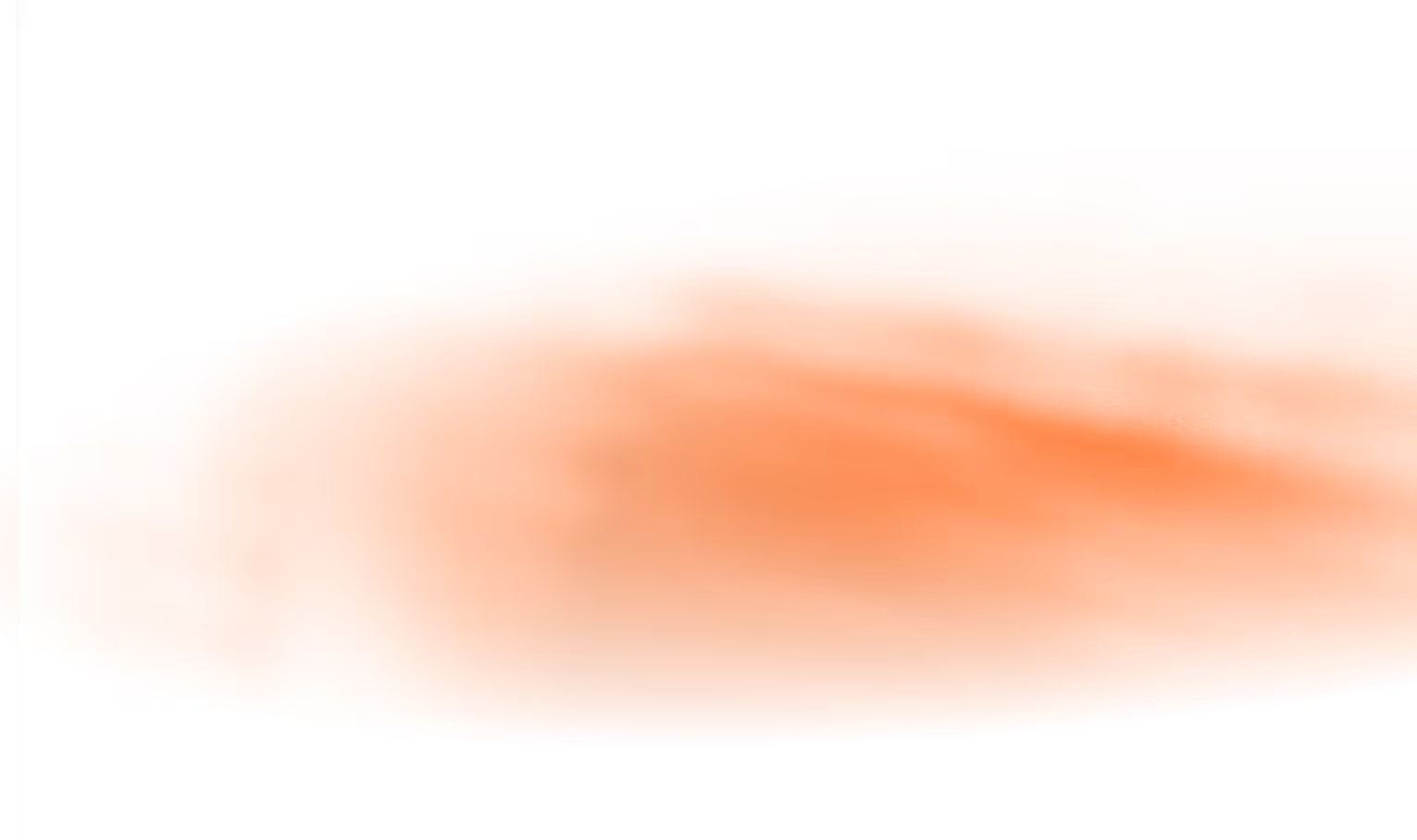
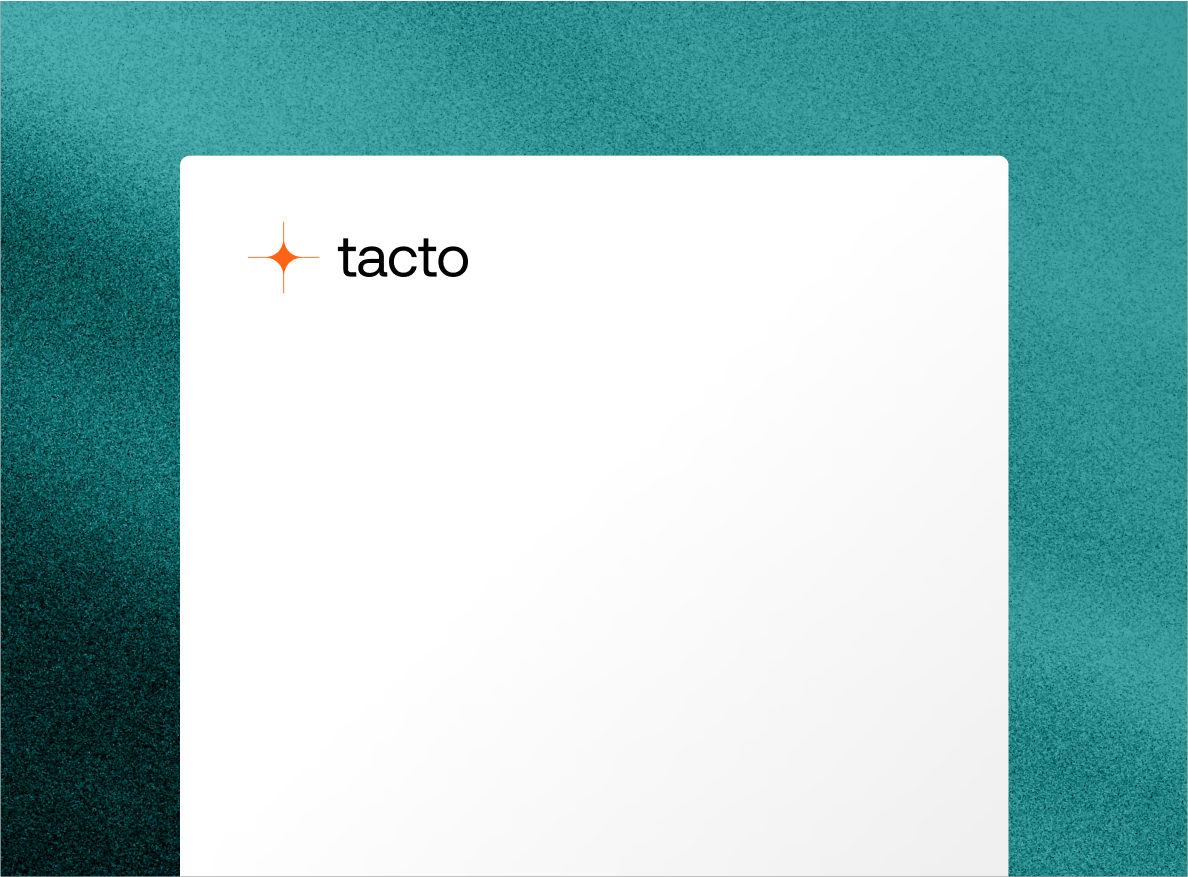