Procurement Glossary
Capacity planning: definition & important points for buyers
Capacity planning enables companies to make optimum use of their resources and identify bottlenecks at an early stage, allowing them to sustainably increase their competitiveness. This structured overview shows how Procurement ensures security of supply and realizes cost savings through strategic capacity planning.
Capacity planning in a nutshell:
Capacity planning is the systematic determination and coordination of available and required resources for a defined period of time. It is essential for Procurement in order to match supplier capacities with its own requirements and identify potential bottlenecks at an early stage.
Example: An automotive supplier plans its production capacity of 10,000 parts per month with three main suppliers, whereby supplier A provides 50%, supplier B 30% and supplier C 20% of the capacity in order to ensure a continuous supply even with seasonal fluctuations of ±20%.
Capacity planning in purchasing controlling
Capacity planning is a fundamental part of operational management and plays a decisive role in the success of a company. It deals with the optimal use and distribution of available resources such as personnel, machinery and equipment. At a time when efficiency and profitability are becoming ever more important, strategic capacity planning is becoming increasingly important. It enables companies to optimize their production and service processes and avoid both overcapacity and bottlenecks. In this guide, you will learn the most important principles, methods and tools of modern capacity planning as well as their practical application in day-to-day business.
What is capacity planning?
Capacity planning is the process of optimally utilizing resources to meet the demand for products or services. In Procurement , this refers to the planning and management of suppliers' production capacities to ensure that they can meet the required demand in a timely and efficient manner. Effective capacity planning avoids bottlenecks, optimizes delivery times and ensures delivery capability.
Core elements of capacity planning
Significance for Procurement
Capacity planning is essential for Procurement in order to ensure a stable supply chain. It makes it possible to identify bottlenecks at an early stage and take proactive countermeasures. By working closely with supplier management on capacity planning, risk management can be minimized, delivery times shortened and costs reduced. This contributes significantly to competitiveness and customer satisfaction.
Capacity planning: from static planning to agile capacity planning
Capacity planning is crucial for the efficient use of resource management and the fulfillment of customer requirements. Building on the theoretical foundation, it is clear that traditional methods are reaching their limits, especially in times of volatile markets and increasing complexity. There is therefore an urgent need for a transformation towards more flexible and dynamic approaches to meet current challenges.
Old: Static capacity planning
Traditional approach: Static capacity planning is based on fixed time intervals, often annually or quarterly, and uses historical data to analyze future capacity requirements. In practice, manual procedures and simple spreadsheets are used. This approach is characterized by low flexibility; changes in demand could only be taken into account with a delay. The lack of adaptability often led to overcapacity or bottlenecks, resulting in inefficient use of resources and increased costs.
New: Agile Capacity Planning
Agile Capacity Planning: The modern approach uses real-time data and advanced technologies to make capacity planning more flexible and responsive. By integrating ERP systems, IoT devices and AI in Procurement, forecasts are constantly updated. This enables faster adaptation to market changes and optimizes resource utilization. Practical benefits include reduced stock levels, shorter delivery times and increased customer satisfaction. This enables companies to work more efficiently and generate competitive advantages.
Practical example: Manufacturing industry
A medium-sized mechanical engineering company implemented Agile Capacity Planning to react to short-term order fluctuations. The introduction of an AI-supported planning tool enabled production capacities to be adjusted on a daily basis. Within six months, the production control by 25%, while throughput times were reduced by 30%. The on-time delivery rate increased to 98%, which led to a significant increase in customer satisfaction.
Conclusion on capacity planning
Capacity planning is an indispensable tool in modern Procurement that ensures security of supply through systematic demand analysis and close supplier cooperation. Successful implementation requires precise forecasts, strategic supplier diversification and digital technologies. Only through proactive capacity management can companies avoid bottlenecks, optimize costs and secure their long-term competitiveness.
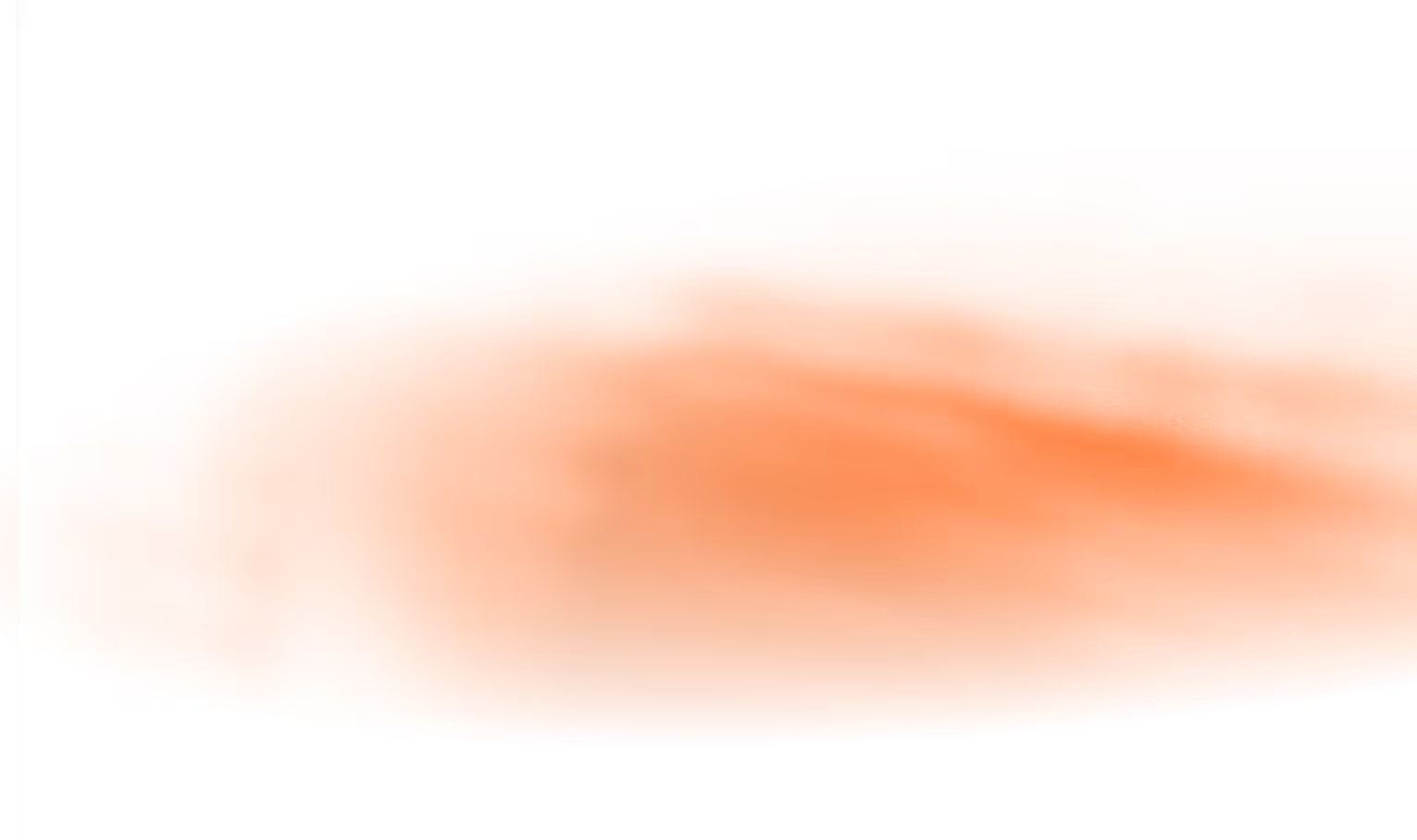
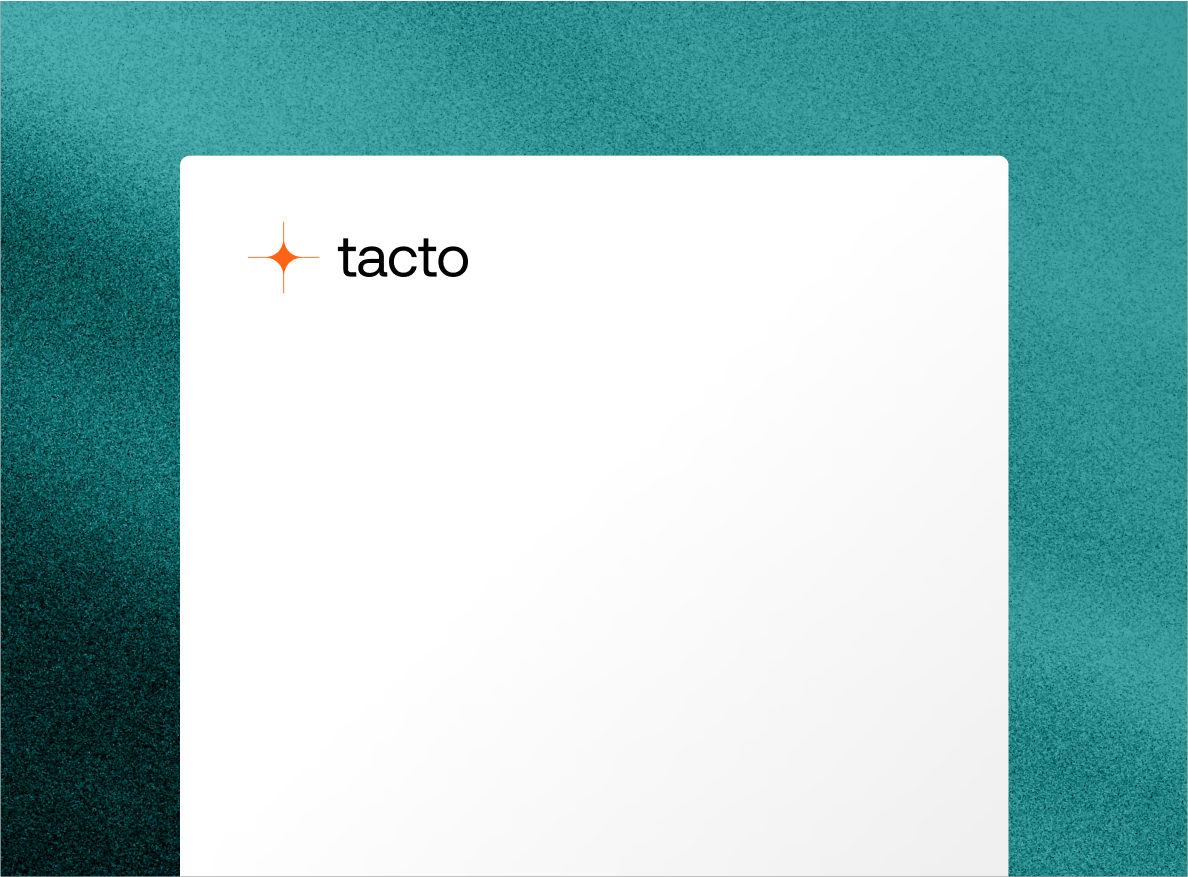