Procurement Glossary
Supplier integration: definition & important aspects for buyers
The systematic integration of suppliers into your own business processes demonstrably increases efficiency, quality and innovative strength along the entire value chain. This structured overview shows how Procurement can generate real competitive advantages and minimize risks through targeted supplier integration.
Supplier integration in a nutshell:
Supplier integration describes the systematic integration of strategic suppliers into a company's own business processes and development activities. For Procurement , this enables improved collaboration, shorter development times and optimized supply chain processes through early coordination and joint planning.
Example: A car manufacturer involves its main supplier for vehicle electronics in the development of a new model 18 months before the start of production, which shortens the development time by 4 months and reduces production costs by 15%.
Supplier integration: a key factor in purchasing controlling
Supplier integration is a strategic approach in modern supply chain management that is becoming increasingly important. It describes the process of closely integrating suppliers into a company's business processes with the aim of optimizing value chains and generating competitive advantages. Through successful supplier integration, companies can not only increase their efficiency, but also tap into innovation potential and strengthen their market position. This paper examines the various aspects of supplier integration in detail, from the basics to practical implementation strategies.
What is supplier integration?
Supplier integration refers to the strategic integration of suppliers into a company's business processes. The aim is to achieve efficiency increases, cost reductions and innovative advantages through close cooperation with selected suppliers. Suppliers are involved in process optimization, development and production processes at an early stage in order to jointly develop optimal solutions and secure competitive advantages.
Core elements of supplier integration
Significance for Procurement
For the Strategic Partnership, supplier integration plays a crucial role in shaping efficient and resilient procurement. Close cooperation can reduce costs, raise quality standards and shorten delivery times. Integration also enables better coordination with market requirements and promotes innovation through the joint development of new products or services.
Supplier integration: from traditional collaboration to digital partnership
Supplier integration has evolved from a simple business relationship to a strategic partnership. Building on its theoretical importance, it provides companies with practical benefits in the form of increased efficiency and innovation. In a globalized and digitalized economy, close integration with suppliers is essential to remain competitive. There is an urgent need to move from traditional methods to modern approaches to collaboration.
Old: Traditional supplier relationship
Traditional approach: In the traditional model, the relationship with suppliers was mainly transactional. Information was exchanged manually via telephone, fax or e-mail, which led to delays and communication errors. Planning and development were carried out separately, without joint coordination or integration of business processes. The lack of transparency and real-time data made it difficult to manage the supply chain efficiently. This often led to increased stock levels, longer delivery times and less flexibility in the face of market changes.
New: Digital Supplier Integration
Digital supplier integration: The modern approach relies on digital technologies for in-depth networking with suppliers. The integration of IT systems using EDI or cloud-based platforms enables real-time data exchange. Suppliers are included in internal planning, joint demand analysis and production plans are created. This improves transparency along the supply chain and reduces inefficiencies. Companies benefit from faster response times, reduced administrative effort and cost savings. Studies show that digital supplier integration can shorten delivery times by up to 30% and reduce inventories by 20%.
Practical example: Automotive supplier
A leading automotive supplier implemented a digital supplier supplier portalto involve its partners in production planning in real time. The close networking enabled supply bottlenecks to be identified at an early stage and solutions to be developed jointly. Within a year, the number of production downtimes was reduced by 50%. Stock levels were reduced by 25%, which led to considerable cost savings. In addition, the joint development platform accelerated the time to market for new products by 15%, enabling the company to significantly strengthen its competitive position.
Conclusion on supplier integration
Supplier integration is an essential component of modern corporate management that goes far beyond traditional supplier relationships. By strategically integrating suppliers into core processes, companies can not only reduce costs and increase quality, but also accelerate innovation and secure competitive advantages. Despite initial challenges and investments, the long-term benefits of successful integration outweigh the costs. In times of increasing digitalization and global networking, successful supplier integration is becoming a decisive success factor for sustainable companies.
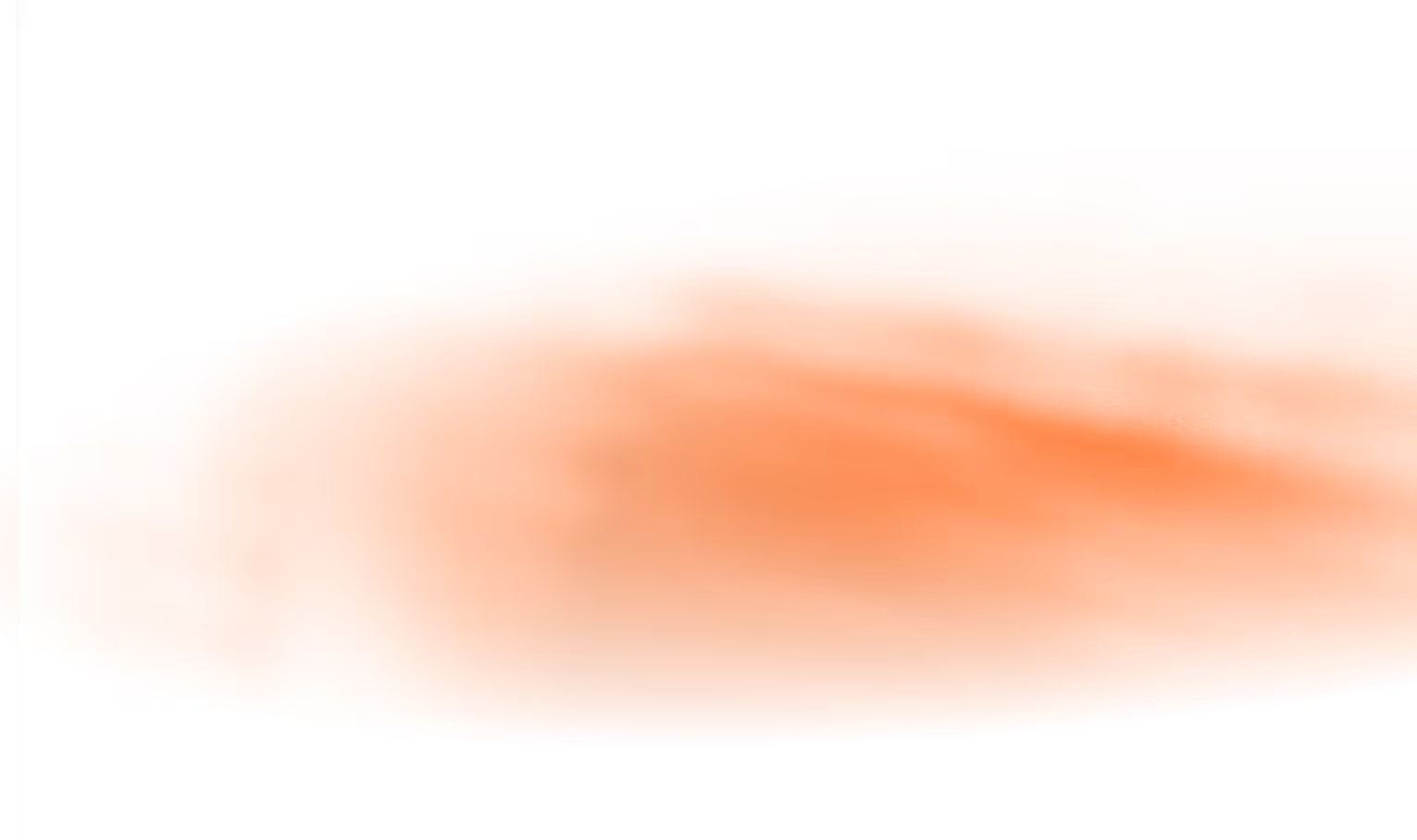
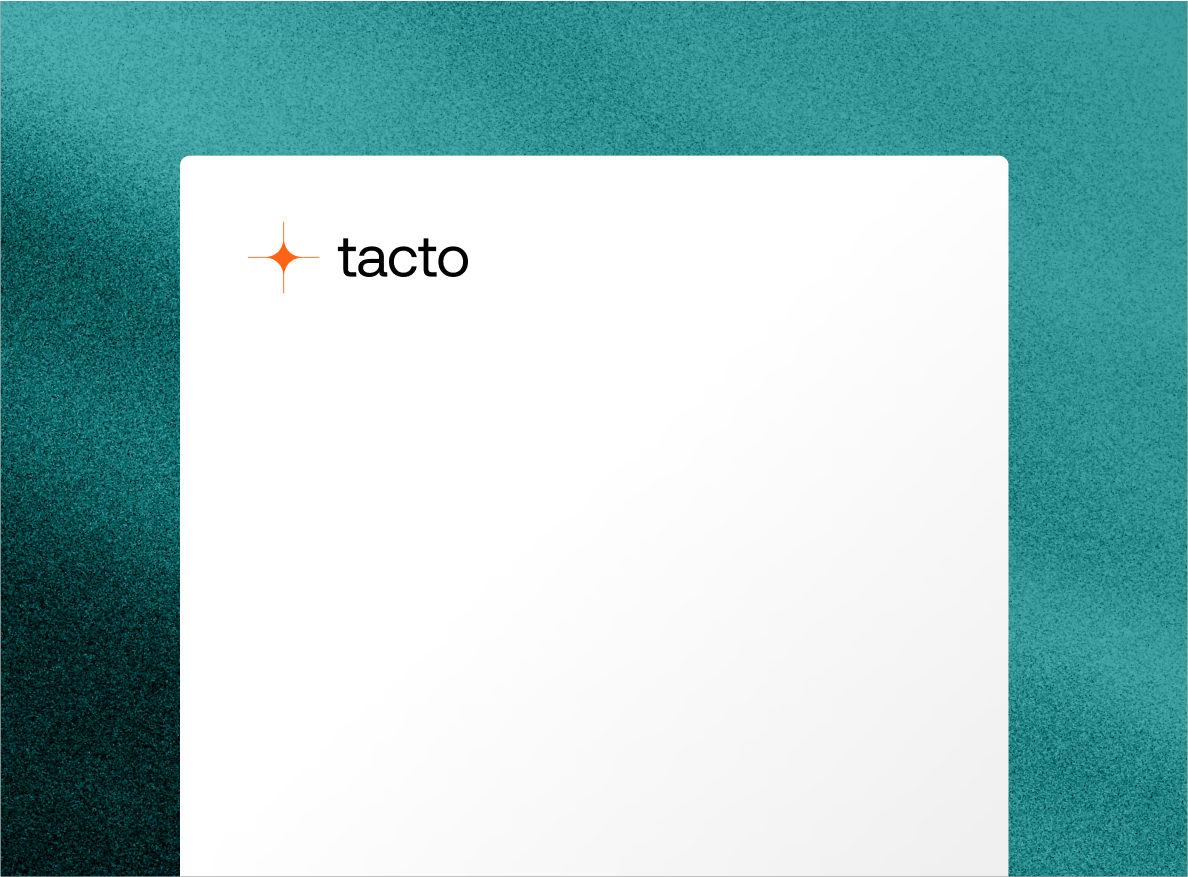