Procurement Glossary
Material requirements planning: definition and important aspects for purchasers
Material Requirements Planning (MRP) supports companies in providing the right material requirements at the right time and in the right place, thus creating the basis for efficient production. This structured overview shows you how to make optimum use of MRP in Procurement , thereby reducing costs and avoiding supply bottlenecks.
Material Requirements Planning in a nutshell:
Material Requirements Planning (MRP) is a computer-aided system for calculating material requirements and optimum ordering times based on parts lists, stock levels and production plans. For Procurement , it enables precise, timely procurement and prevents both material bottlenecks and excessive stock levels.
Example: An automotive supplier uses MRP to determine the exact requirement of 4,000 microchips, 2,000 circuit boards and 6,000 housing parts for the production of 1,000 control units per week and to procure these in good time, taking into account the delivery times (6 weeks for microchips, 3 weeks for circuit boards).
Introduction to Material Requirements Planning
Material requirements planning (MRP) is a fundamental concept in modern production management and logistics. It represents a systematic approach to planning and controlling material flows in production companies. By precisely calculating material requirements, order quantities and order times, MRP enables efficient warehousing and optimized production processes. At a time when resource efficiency and just-in-time production are becoming increasingly important, material requirements planning is becoming more and more important. This guide provides a comprehensive overview of the principles, methods and practical applications of MRP in the modern business environment.
What is Material Requirements Planning (MRP)?
Material Requirements Planning (MRP) is a systematic process for planning and controlling material requirements in production companies. It ensures that the required materials are available in the right quantity and at the right time to guarantee a smooth production process. MRP takes into account production plans, bills of materials, stock levels and delivery times to enable purchasers to accurately forecast requirements.
Core elements of material requirements planning
Significance for Procurement
MRP plays a decisive role in Procurement for efficient material supply and cost optimization. Precise demand planning enables buyers to better bundle orders, take advantage of volume discounts and reduce stock levels. MRP helps to avoid overstocking and minimize the risk of material shortages, which directly contributes to increasing the company's productivity and competitiveness.
Material requirements planning: from manual planning to digital requirements determination
Building on the theoretical foundations of Material Requirements Planning (MRP), it becomes clear how essential precise materials management is for efficient production processes. In practice, companies are faced with the challenge of avoiding material bottlenecks while keeping stock levels low. Traditional planning methods are often not sufficient to meet these requirements, which is why a shift towards modern, digital solutions is necessary.
Old: Manual material planning
Traditional approach: In traditional, manual material planning, requirements were often determined on the basis of empirical values and static Excel tables. Production plans were created on the basis of historical data without taking sufficient account of dynamic market requirements. This led to overstocks or material bottlenecks, as updates were time-consuming and often lagged behind actual requirements. The lack of integration between departments made communication difficult and caused inefficiencies throughout the process.
New: Material Requirements Planning (MRP)
Material Requirements Planning: The modern implementation of MRP revolutionizes material requirements planning through the use of computer systems that process production control, parts lists and stock levels in real time. MRP enables dynamic adaptation to current market conditions and customer orders. Automated determination of requirements and order processing speeds up processes and reduces error rates. Companies benefit from lower stock levels, optimized supply chains and increased responsiveness to changes in demand, leading to overall cost reductions and increased efficiency.
Practical example: Electronics production
A leading manufacturer of electronic components was faced with the challenge of ensuring its ability to deliver despite short-term fluctuations in orders. By introducing an MRP system, the company was able to reduce its inventory by 30% and at the same time increase on-time delivery to 98%. Automated demand planning enabled a faster response to customer orders, reduced lead times by 20% and resulted in annual cost savings of over €2 million. These improvements strengthened the market position and significantly increased customer satisfaction.
Conclusion on material requirements planning
Material Requirements Planning (MRP) is an indispensable tool for modern production companies. It enables precise material requirements planning, optimizes stock levels and reduces procurement costs. Despite challenges such as market dynamics and system complexity, new technologies such as AI and machine learning offer promising opportunities for further development. The success of MRP depends largely on data quality, system integration and effective supplier management.
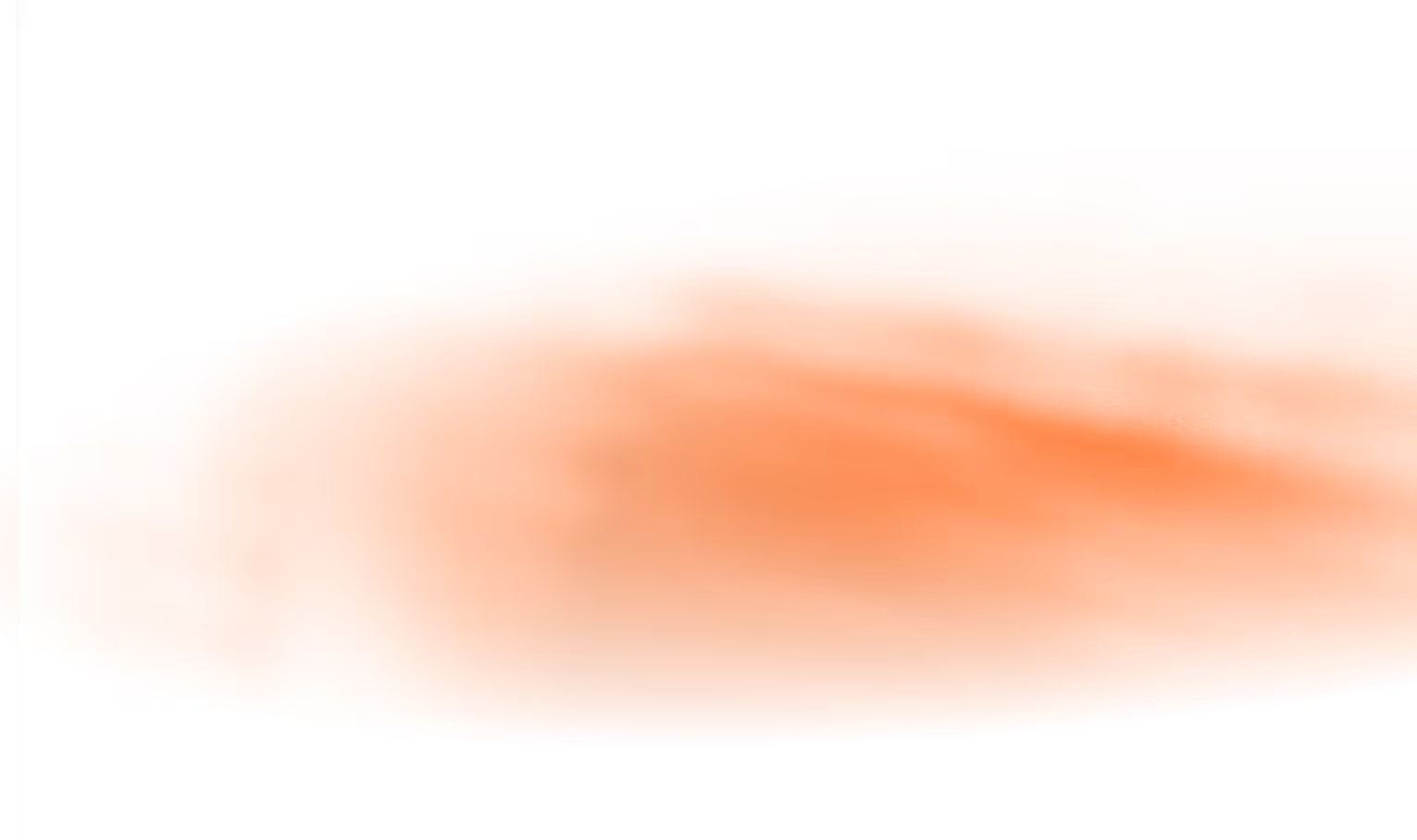
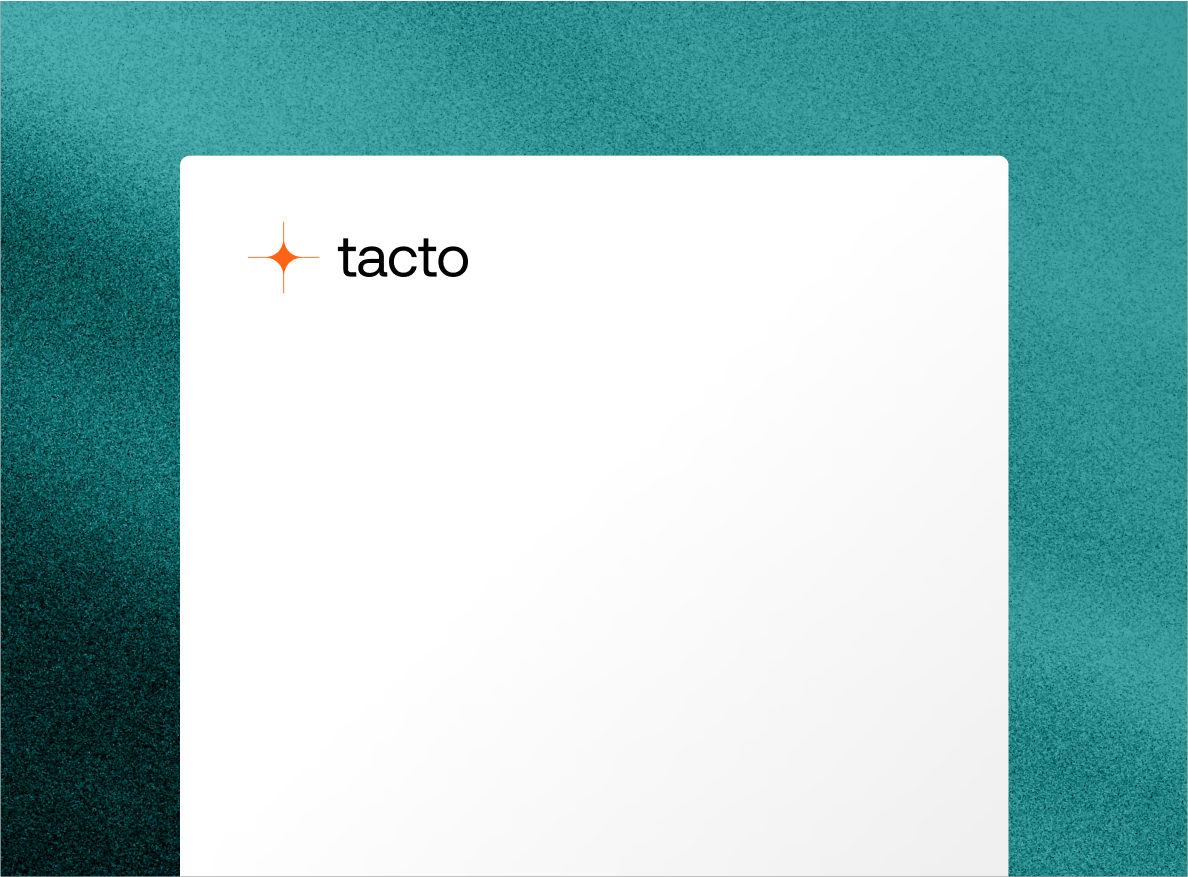