Procurement Glossary
Optimal order quantity: core concept for cost-efficient Procurement
The optimum order quantity forms the mathematical foundation for efficient inventory management by precisely determining the most economical order size, in which storage and order costs are in perfect balance, thus ensuring maximum cost savings with simultaneous delivery capability.
What is the optimum order quantity?
The optimum order quantity (Economic Order Quantity, EOQ) describes the most economically advantageous order quantity at which the sum of order and inventory costs is minimized. It enables companies to find the perfect balance between excessively frequent orders with high process costs and excessively large inventories with high capital commitment.
- Central control instrument for cost-efficient procurement
- Mathematical optimization model to minimize total costs
- Equalization between ordering costs and warehousing costs
- Basis for economic procurement decisions in operational Procurement
Contents
1.
What is the optimum order quantity? (Definition and theoretical principles)
2.
Cost components of the optimum order quantity (order costs and inventory costs)
3.
Practical application and calculation example (use cases and sensitivity analysis)
4.
Digitalization and modern approaches (advantages of digital solutions and integration into procurement processes)
5.
Integration into strategic supply chain management (interaction with other SCM concepts)
Theoretical principles of the optimum order quantity
The concept of the optimal order quantity is based on the realization that order costs fall as the order quantity increases, while inventory costs rise. This opposing cost trend leads to a minimum total cost for a certain order quantity - the optimum order quantity.
The theoretical basis for the calculation was developed by Ford W. Harris back in 1913. Karl Andler took this up and popularized the concept in German-speaking countries, which is why the calculation formula is also known in German as "Andler'sche Formel".
The Andler formula: Mathematical basis of the calculation
The optimum order quantity is calculated using the Andler formula:
q = √((2 × annual requirement × order costs) / (cost price per unit of measure × storage cost rate))
Whereby:
- q = optimum order quantity in units
- Annual requirement = annual requirement in units
- Order costs = costs per order in euros
- Cost price = price per unit in euros
- Storage cost rate = percentage share of annual storage costs in the value of goods
Cost components of the optimum order quantity
A thorough understanding of the relevant cost components is essential in order to precisely determine the optimum order quantity. These can be divided into two main categories: Ordering costs and inventory costs.
Order costs
The order costs include all costs incurred when initiating and processing an order, regardless of the quantity ordered. They are fixed in terms of quantity but variable in terms of transaction.
- Personnel costs: working time for determining requirements, selecting suppliers, comparing offers and processing orders
- Communication costs: telephone, e-mail and system costs
- Inspection and quality costs: incoming goods inspections and quality assurance
- Administrative costs: documentation, archiving and auditing
- System costs: Proportionate costs for ERP and procurement systems
Storage costs
The storage costs increase proportionally with the order quantity and the storage period. They are quantity-variable and time-dependent.
- Capital commitment costs: opportunity costs of the capital tied up in inventories
- Occupancy costs: rent, depreciation, energy and maintenance costs for storage space
- Personnel costs: Wage and salary costs for warehouse staff
- Insurance costs: Premiums for warehouse insurance
- Impairment costs: shrinkage, spoilage, obsolescence and loss of value of stored goods
- Handling costs: storage and retrieval, stock checks and inventories
Factors influencing the optimum order quantity
The optimum order quantity is influenced by numerous factors that must be taken into account in the calculation and practical application.
Fluctuations in demand
In practice, demand is rarely constant. Seasonal fluctuations, market developments or unexpected events can have a significant impact on demand. Advanced demand forecasting models and regular adjustments to the optimum order quantity are therefore essential.
Volume discounts
The classic Andler formula does not take quantity discounts into account. In practice, however, larger order quantities can lead to lower purchase prices. This requires a modified calculation in which the savings from volume discounts are compared with the higher inventory costs.
Storage capacities
Limited storage capacity can restrict the theoretically optimal order quantity. In this case, companies must weigh up the optimum order quantity against the available storage capacity or consider investing in additional storage space.
Product life cycle
For products with short life cycles or a high risk of obsolescence, the risk of depreciation must be weighted more heavily. This generally leads to smaller optimal order quantities.
Practical application and calculation example
The theoretical principles of the optimum order quantity are best illustrated using a concrete example. Let us consider a medium-sized production company that requires 24,000 units of a purchased part each year.
Example: Calculation of the optimum order quantity
Initial data:
- Annual requirement: 24,000 pieces
- Order costs: 100 € per order
- Cost price: 20 € per piece
- Storage cost rate: 25% per year
Calculation with the Andler formula:
q = √((2 × 24.000 × 100) / (20 × 0,25))
q = √(4.800.000 / 5)
q = √960.000
q = 980 pieces
With an optimum order quantity of 980 units, this results in:
- Number of orders per year: 24,000 / 980 = 24.5 orders
- Order costs per year: 24.5 × 100 € = 2,450 €
- Average stock level: 980 / 2 = 490 units
- Storage costs per year: 490 × € 20 × 0.25 = € 2,450
- Total costs: € 2,450 + € 2,450 = € 4,900
This example illustrates the equilibrium principle of the optimum order quantity: with the optimum order quantity, the annual order costs and inventory costs are exactly the same.
Sensitivity analysis
To illustrate the effects of different order quantities on total costs, we consider a sensitivity analysis:
- For 490 units (50% of the optimum quantity): Ordering costs: €4,900, storage costs: €1,225, total costs: €6,125 (25% higher)
- For 980 units (optimum quantity): Ordering costs: €2,450, storage costs: €2,450, total costs: €4,900
- For 1,960 units (200% of the optimum quantity): Ordering costs: €1,225, storage costs: €4,900, total costs: €6,125 (25% higher)
This analysis shows: If the order quantity deviates from the optimal quantity, the total costs increase. Interestingly, if the order quantity is larger than the optimal quantity, the costs increase significantly less for a 5% increase in total costs compared to an order quantity that is too small. This explains why, in practice, slightly larger order quantities than the theoretically optimal ones are often chosen.
Limits and criticism of the classic EOQ model
The traditional model of the optimal order quantity is based on simplified assumptions that do not always apply in complex practice. A critical examination of these limitations is essential for purchasing experts.
Simplified assumptions
- Constant demand: In reality, demand often fluctuates seasonally or due to market changes.
- Constant delivery time: Delivery times can be influenced by numerous external factors.
- Constant costs: Both ordering and storage costs can change over time.
- Infinite storage capacity: The available storage space is limited in practice.
- One-off, complete delivery: In many cases, partial deliveries or just-in-time deliveries are made.
Extensions to the classic model
To overcome the practical limitations, various extensions to the EOQ model have been developed:
- Dynamic EOQ models: consideration of fluctuating demand and variable costs
- Volume discount models: Integration of staggered prices for larger order quantities
- Subsequent delivery models: consideration of partial deliveries and limited production capacities
- Multi-product EOQ models: Optimization for multiple products with shared resources
- Stochastic models: Consideration of uncertainties in demand and delivery time
Digitalization and modern approaches
Digitalization has revolutionized the practical application of the optimal order quantity. Modern ERP and SRM systems enable dynamic and precise calculation in real time, taking numerous influencing factors into account.
Advantages of digital solutions
- Automated calculations: SRM systems perform complex calculations of the optimum order quantity automatically and reduce manual errors.
- Real-time data integration: Current demand figures, stock levels and cost data are taken into account in real time.
- Dynamic adjustment: If requirements, costs or other parameters change, an automatic recalculation takes place.
- Advanced algorithms: Modern systems take into account complex factors such as quantity discounts, delivery time risks and fluctuations in demand.
- Predictive analytics: AI-based forecasts improve demand forecasting and optimize order quantities.
Implementation in digital procurement processes
In modern procurement processes, the optimum order quantity is not viewed in isolation, but integrated into a holistic digital workflow:
- Demand recording through intelligent forecasts and automated reporting points
- Dynamic calculation of the optimum order quantity, taking current parameters into account
- Automated order triggering when reorder levels are reached
- Supplier integration for transparency and shorter response times
- Continuous optimization through machine learning and data analysis
Integration into strategic supply chain management
The optimal order quantity is not an isolated concept, but a central component of holistic supply chain management. It is important for purchasing managers to place order quantity optimization in a strategic context.
Interaction with other SCM concepts
- Just-in-time (JIT): JIT concepts traditionally aim for smaller order quantities with more frequent deliveries, which can contradict the classic EOQ model. Modern approaches combine JIT principles with optimized order quantities.
- Vendor Managed Inventory (VMI): With VMI, the supplier assumes responsibility for inventory, whereby optimum order quantities can serve as control parameters.
- ABC/XYZ analysis: The classification of articles according to value and demand forecast accuracy enables a differentiated application of the optimum order quantity for different article groups.
- Bullwhip effect minimization: Stable, optimal order quantities can help to reduce inventory fluctuations in the supply chain.
Strategic added value for Procurement
The consistent application of the optimum order quantity offers significant strategic advantages for the purchasing department:
- Cost reduction: minimization of total costs from procurement and warehousing
- Capital release: reduction of capital tied up in inventories
- Process optimization: standardization and increased efficiency in operational Procurement
- Planning reliability: increased transparency and improved forecasts
- Supplier relationships: Reliable ordering rhythms strengthen partnership and delivery reliability
Conclusion and recommendations for action
Despite its theoretical origins, the optimal order quantity remains a powerful tool for modern strategic Procurement. The greatest benefit comes from the critical application of the concept, taking into account company-specific framework conditions and integration into digital procurement processes. Professional procurement managers should consider the optimal order quantity as one of their central control instruments, the potential of which is further enhanced by digitalization.
Recommendations for purchasing managers:
- Critical analysis of cost structures: Carry out a detailed analysis of the actual ordering and warehousing costs in order to clarify the calculation basis.
- Differentiated application: Apply the optimal order quantity differentiated for different article groups, based on ABC/XYZ classification and strategic importance.
- Drive digitization forward: Invest in powerful SRM systems with dynamic order quantity calculation and continuous optimization.
- Change management: Promote understanding of the concept of optimal order quantity at all levels of the company and overcome departmental silos.
- Regular review: Evaluate the effectiveness of your order quantity strategies periodically and adjust parameters promptly in the event of changes in the market or supply chain.
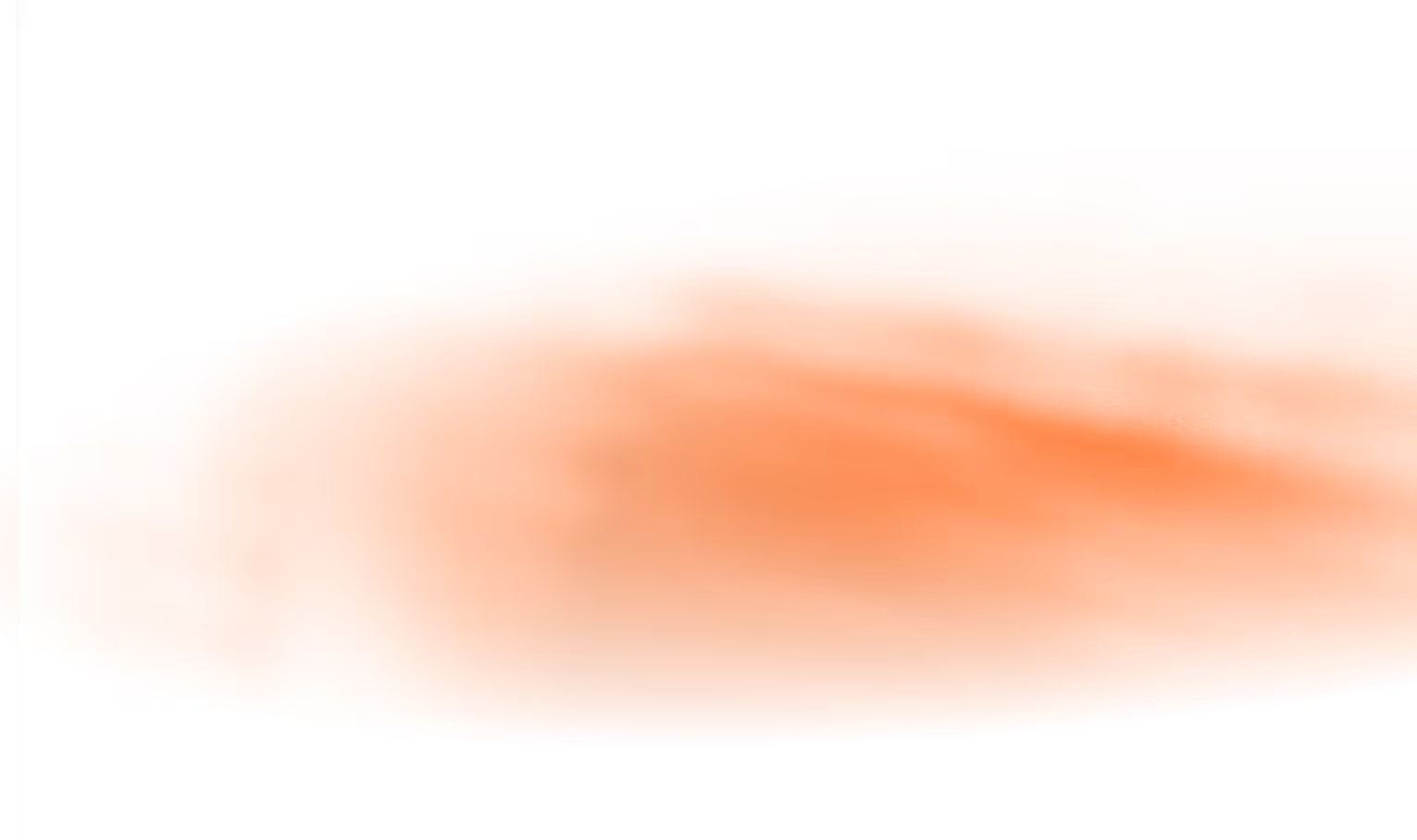
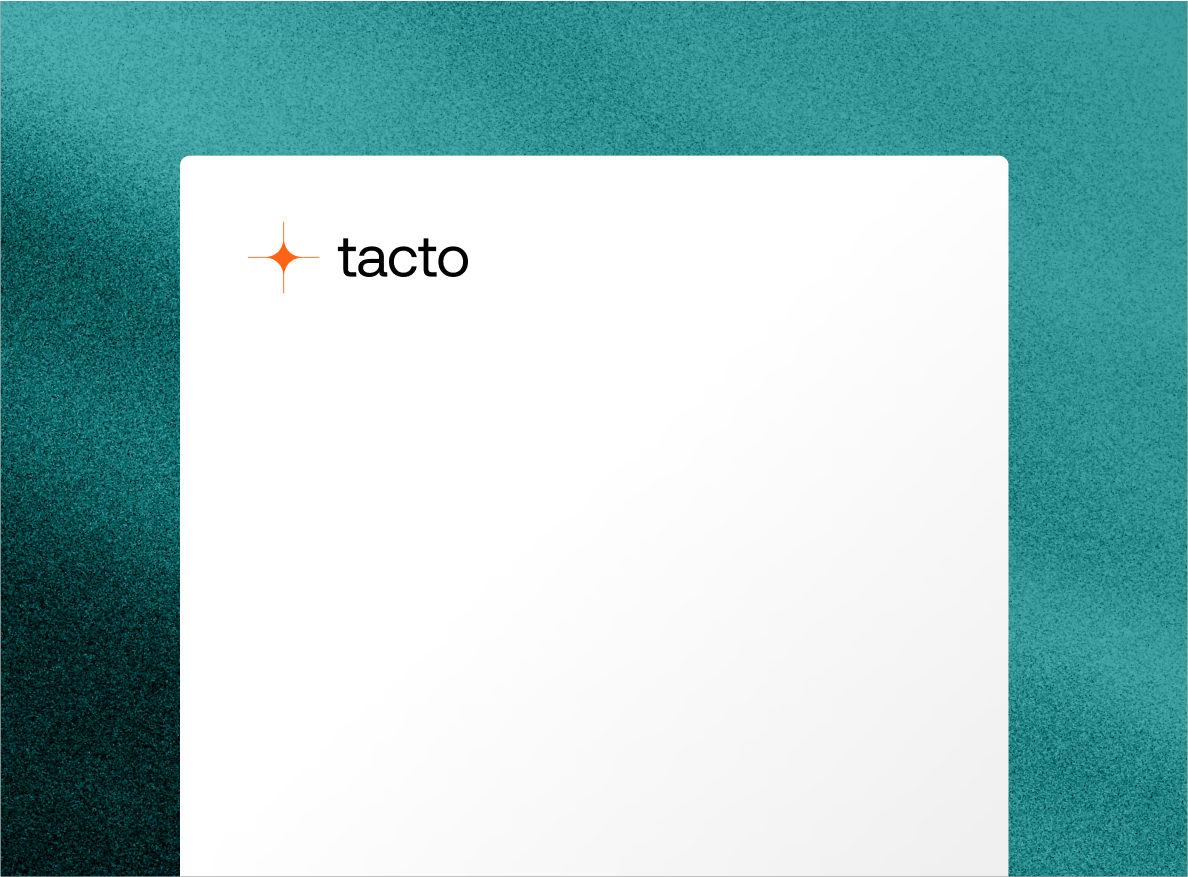