Procurement Glossary
Quality management in Procurement: definition & important aspects for buyers
Quality management in Procurement not only ensures product quality, but also creates sustainable competitive advantages through optimized supplier relationships and reduced error costs. The following overview systematically shows the most important tools and methods for successful quality management in Procurement and how you can use them profitably in your daily work.
Quality management in a nutshell:
Quality management encompasses all systematic measures to ensure and continuously improve product and process quality along the entire supply chain. This is essential for Procurement , as it optimizes the selection and evaluation of suppliers and reduces quality costs through preventative measures.
Example: An automotive supplier implements a Supplier Quality Management System that reduces the defect rate for purchased components from 2.5% to 0.8% within 12 months through monthly quality audits and a 100-point evaluation system.
Quality management in procurement
Quality management in Procurement is an essential building block for the sustainable success of a company. It encompasses all systematic measures and processes that contribute to ensuring the quality of purchased materials, products and services. In an era of global supply chains and increasing customer requirements, quality management in Procurement is becoming increasingly important. Effective quality management helps to minimize risks, optimize costs and increase customer satisfaction. In this guide, you will learn about the most important principles, methods and tools of quality management in Procurement as well as their practical implementation in day-to-day business.
What is quality management in Procurement?
Quality management in Procurement encompasses all activities and processes aimed at ensuring and continuously improving the quality of procured goods and services. It combines the principles of quality management with the specific requirements of procurement to ensure that the products supplied meet the defined quality standards and thus contribute to the company's added value.
Core elements of quality management in Procurement
Significance for Procurement
Quality management is of crucial importance in Procurement , as it directly influences product quality, customer satisfaction and ultimately the company's success. Effective quality management can reduce costs caused by faulty products, increase process efficiency and establish long-term partnerships with reliable suppliers.
Quality management in Procurement: From a reactive quality approach to supplier quality management
Building on the central role of quality management in Procurement for ensuring quality inspection and customer satisfaction, its practical implementation is becoming increasingly important in modern procurement. Traditionally, quality management focused on the inspection of incoming goods and only reacted after defects occurred. However, with the growth of global supply chains and increasing quality requirements, a change is needed. The transformation to proactive approaches that incorporate supplier development and the use of modern technologies is crucial to ensure quality standards throughout the supply chain.
Old: Reactive quality management
Traditional approach: In traditional quality management in Procurement , the focus is on the final inspection of the delivered goods. Companies carry out spot checks and visual inspections of incoming goods to identify quality defects. Tools such as manual checklists and paper documentation are used. This reactive approach often reveals quality problems late, leading to production delays, increased costs due to rework and potential supply bottlenecks. There is also a lack of systematic supplier management and involvement, which makes it difficult to sustainably improve supplier performance.
New: Supplier Quality Management
Supplier Quality Management: The modern approach to quality management in Procurement shifts the focus to proactive and integrated strategies. By implementing Supplier Quality Management (SQM), suppliers become partners in quality optimization. Digital platforms and real-time data analysis enable continuous monitoring of supplier performance. Innovations such as automated quality checks, predictive analytics and collaborative improvement programs help to identify and resolve potential problems at an early stage. This leads to a reduction in error costs of up to 30%, shorter delivery times and increased product quality.
Practical example: Automotive industry
A leading car manufacturer integrated a supplier quality management system that involves close collaboration with its suppliers. Through regular audits, joint quality indicators and the use of real-time monitoring tools, the error rate of supplied parts was reduced by 40%. In addition, the time to market for new models was reduced by 15%. The improved quality led to a measurable increase in customer satisfaction and enabled annual cost savings of over 20 million euros through reduced warranty services and returns.
Conclusion on supplier evaluation
Quality management in Procurement is an indispensable component of successful procurement processes. Systematic supplier qualification, continuous monitoring and strategic further development of quality standards form the foundation for long-term competitiveness. Increasing digitalization and the use of modern technologies are opening up new opportunities to make quality processes more efficient and identify risks at an early stage. Companies that actively utilize these developments and integrate them into their quality strategies will be able to operate successfully on the market in the future.
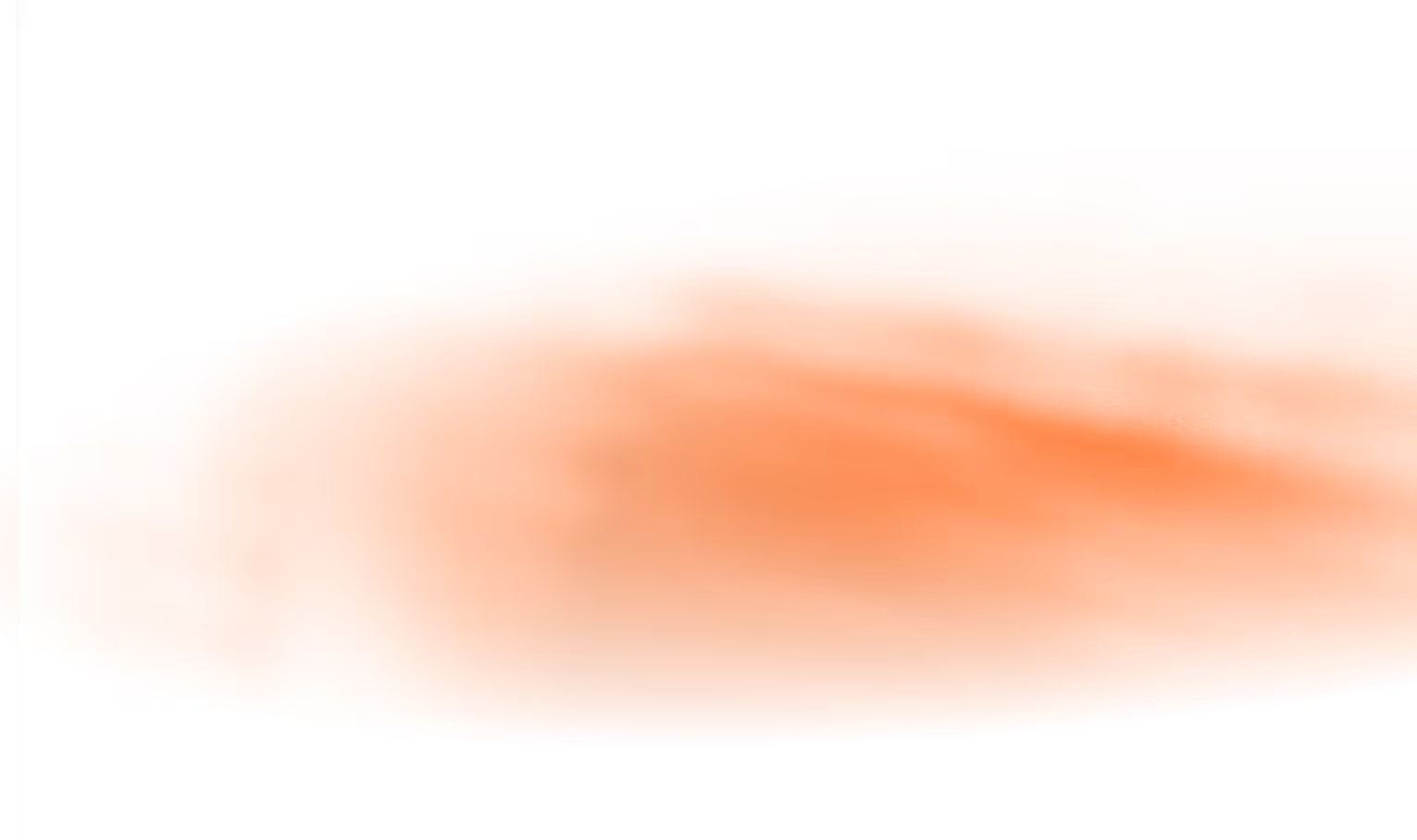
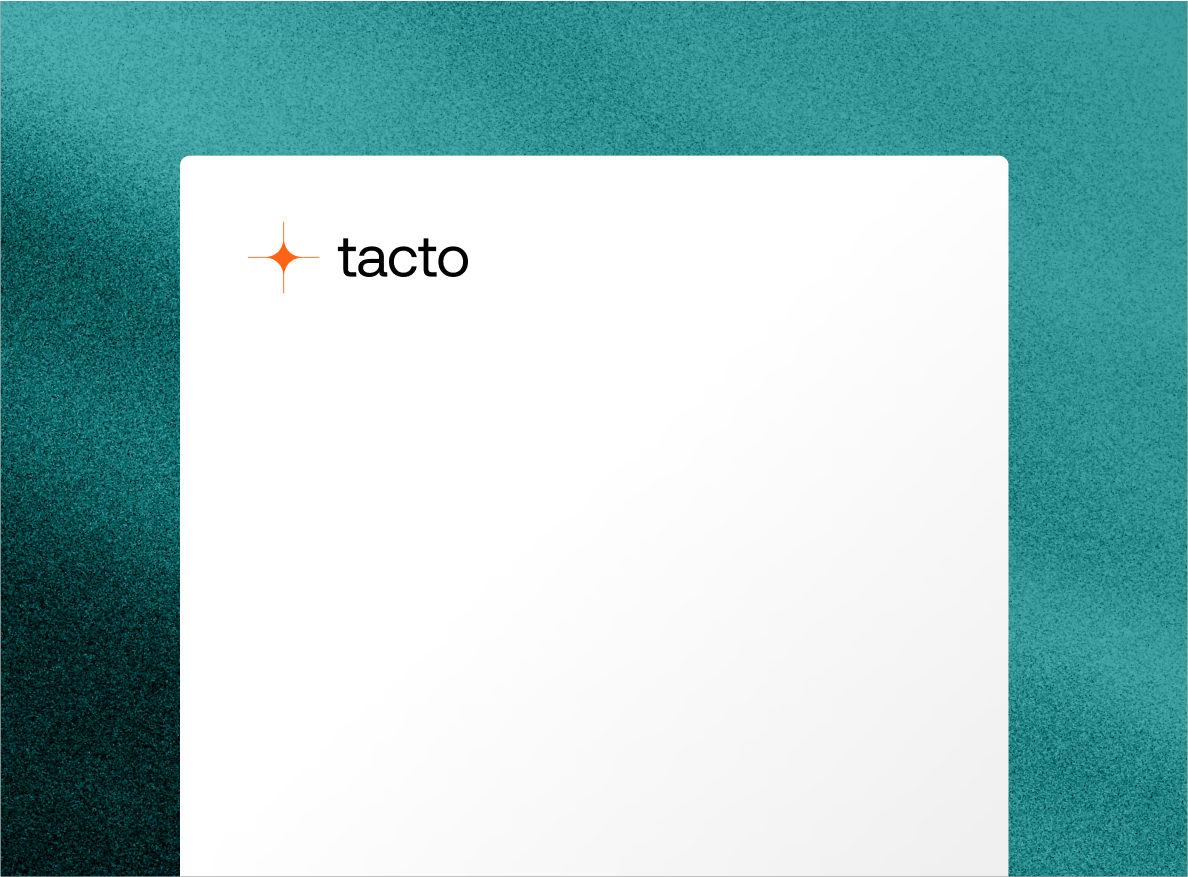