Procurement Glossary
Quality assurance agreement: definition & important aspects for buyers
A quality assurance agreement creates binding standards between supplier and buyer and thus minimizes quality risks in the supply chain. The following overview shows how you, as a buyer, can optimize this important instrument and use it successfully in practice.
Quality assurance agreement in a nutshell:
A quality assurance agreement (QAA) is a legally binding contract between the customer and supplier that defines specific quality requirements, test procedures and responsibilities. For Procurement , it is a key instrument for safeguarding product quality and minimizing quality risks in the supply chain.
Example: An automotive supplier concludes a QAA with its plastic parts supplier that stipulates a maximum error rate of 50 ppm, 100% incoming inspection of initial samples, quarterly quality audits and a 24-hour response time in the event of quality problems.
Quality assurance agreement: An introduction
The quality assurance agreement (QAA) is an essential instrument in modern quality management and in the cooperation between companies and their suppliers. It represents a binding contract that clearly regulates the quality requirements, measures and responsibilities between the contracting parties. At a time when product quality and process reliability are becoming increasingly important, the QAA is gaining in significance. It serves as the basis for transparent and efficient cooperation and helps to minimize quality risks and guarantee standards. In this guide, you will learn all the important aspects of the design, implementation and significance of quality assurance agreements in the modern economy.
What is a quality assurance agreement?
A quality assurance agreement (QAA) is a contractual agreement between a company and its suppliers or service providers. It specifies the quality standards and requirements that apply to the products or services to be supplied. By clearly defining quality criteria, test procedures and responsibilities, the QAA ensures that the products supplied meet the agreed standards and thus guarantees customer satisfaction.
Core elements of a quality assurance agreement
Significance for Procurement
In Procurement , the quality assurance agreement plays a central role in ensuring quality standards along the supply chain. It enables buyers to minimize risks by ensuring that suppliers keep their quality promises. The QAA creates the basis for long-term cooperation based on trust, which leads to cost savings and process optimization. It also helps to reduce complaints and increase customer satisfaction.
Quality assurance agreement: from rigid contracts to agile quality management
The quality assurance agreement is a key instrument in the interaction between companies and their supplier management to ensure high standards and consistency in product quality. In practice, however, traditional approaches have often led to inefficient processes and communication gaps. With increasing demands and complex global supply chains, there is an urgent need for more flexible and efficient methods. This change is driving the evolution from rigid contracts to agile, integrated quality processes.
Old: Rigid quality assurance processes
Traditional approach: Traditionally, quality assurance agreements were created as detailed, often static documents that defined exact specifications, inspection plans and responsibilities. Communication between companies and suppliers was mainly via email or paper documents, which slowed down the exchange of information and increased the risk of errors. Quality inspectionswere carried out at fixed intervals and deviations were often only detected late. This method was characterized by high administrative effort, low flexibility in the event of changes and delayed response times to quality problems. In addition, the lack of real-time data led to inefficient decision-making processes and increased production costs.
New: Integrated quality management
Quality assurance integration: Modern approaches rely on integrated quality management in which companies and suppliers are closely networked via digital platforms. Quality assurance agreements are made dynamic and adaptable through the use of real-time data, cloud computing and collaborative software solutions. Processes such as automatic quality monitoring, immediate feedback in the event of deviations and joint problem solving are standard. Innovation steps such as AI in Procurement and machine learning enable proactive quality improvements and predictions of potential problems. This leads to higher product quality, faster response times and reduced costs due to fewer rejects and rework.
Practical example: Implementation in medical technology
A medical technology company has revolutionized its quality assurance management by introducing a digital portal. Suppliers were integrated into a common system that enabled real-time tracking of quality indicators. The number of quality incidents was reduced by 40% within a year. Automated notifications and shared workflows enabled problems to be resolved 60% faster on average. In addition, the improved needs analysishelped to proactively identify weak points, which led to a 25% increase in overall process efficiency. This integrative approach not only strengthened product quality, but also the partnership-based relationship with suppliers.
Conclusion on the quality assurance agreement
Quality assurance agreements are indispensable instruments of modern purchasing that ensure product quality and minimize risks through clear standards and processes. They not only create transparency in the supplier relationship, but also form the basis for long-term partnerships and continuous improvements. With increasing digitalization, QAAs are constantly evolving and offer new opportunities for efficient quality management along the entire supply chain.
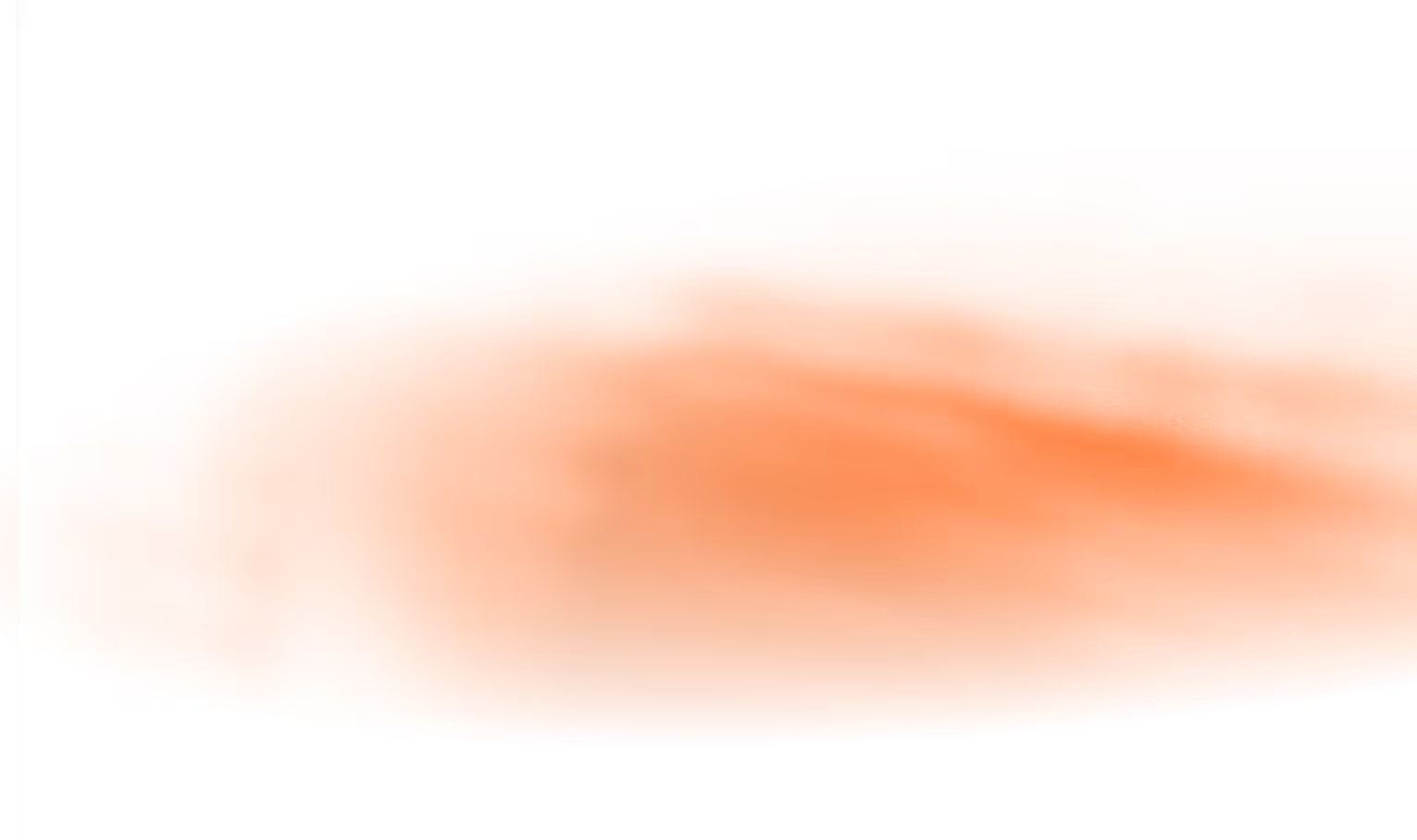
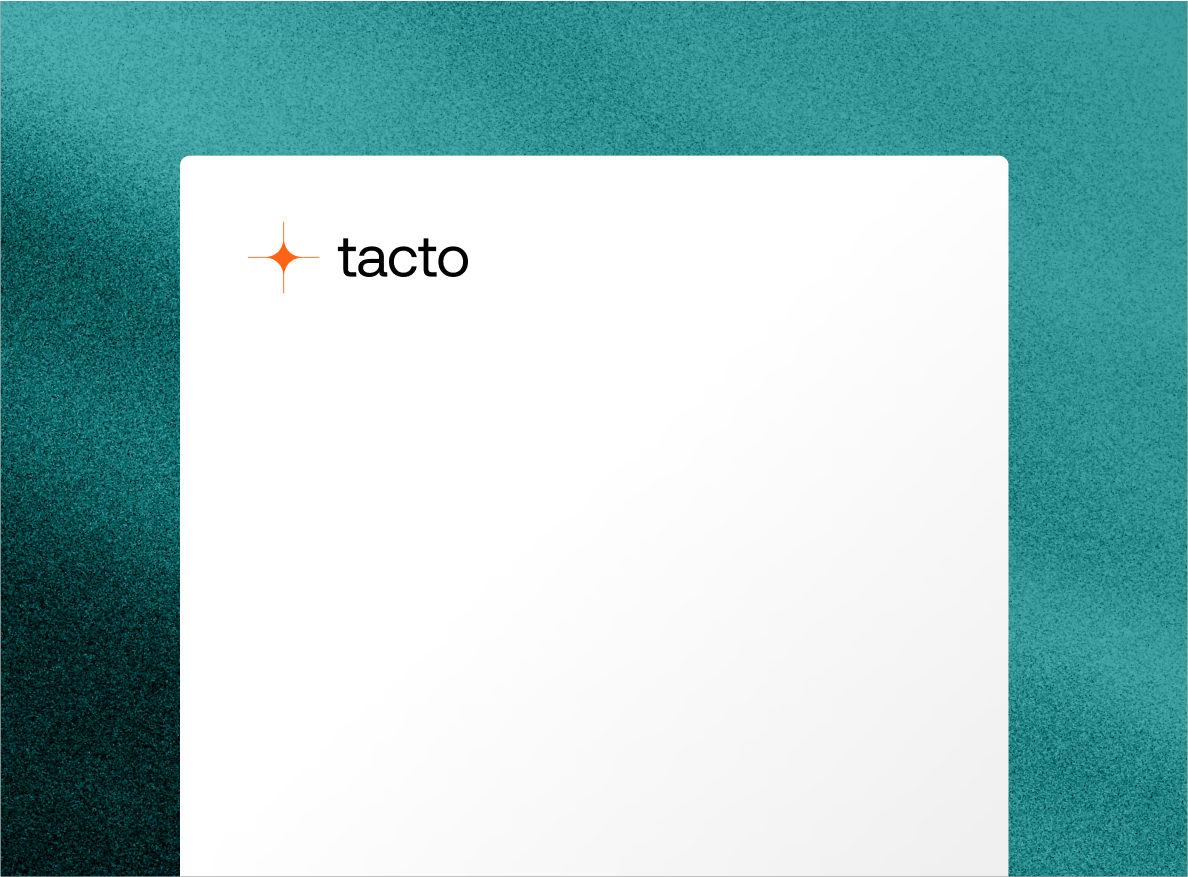