Procurement Glossary
Quality locks: definition & important aspects for buyers
As important control points, quality gates control the success of the project and systematically ensure quality in all project phases. This structured overview shows how Procurement can use quality gates as an effective tool for minimizing risk and optimizing processes in procurement.
Quality Gates in a nutshell:
Quality gates are defined control and decision points in projects or processes at which predefined quality criteria must be checked. In Procurement , they ensure systematic quality control in strategic procurement projects and guarantee that all critical requirements are met before the transition to the next project phase.
Example: When selecting a new supplier for electronic components, three quality gates were implemented: after the pre-selection (Gate 1), after the audit (Gate 2) and after the sample delivery (Gate 3), with each gate requiring specific criteria such as certifications, quality standards and delivery performance with a minimum fulfillment of 85%.
Introduction to Quality Gates
Quality gates are important control and decision points in project management and product development. They serve as systematic checkpoints at which the progress of the project and the quality of the results are evaluated on the basis of defined criteria. These 'quality doors' enable companies to identify problems at an early stage and make the necessary corrections. In today's world, where quality and efficiency play an increasingly important role, quality gates have become an indispensable tool of modern quality management. In this guide, you will learn how quality gates work, what advantages they offer and how they can be successfully implemented.
What are quality gates?
Quality gates are defined control points within the procurement or development process at which the quality of products, services or processes is checked before they move on to the next phase. These systematic checks serve to ensure that all requirements and standards are met in order to identify and rectify errors at an early stage. By implementing quality gates, the entire process becomes more efficient and it is ensured that the end products meet the quality requirements.
Core elements of quality gates
Importance of quality gates in Procurement
In the procurement process, quality gates play a decisive role in ensuring quality and efficiency. They enable purchasers to identify and address potential problems with suppliers or products at an early stage. This leads to a reduction in risk management, costs and delays. In addition, quality gates promote adherence to compliance guidelines and strengthen relationships with reliable suppliers by establishing clear expectations and feedback mechanisms.
Quality Gates: From Traditional Quality Inspections to Integrated Quality Gates
The use of quality gates has become a central element in the quality assurance agreement in recent years. While traditional quality inspections often only take place at the end of a production process, quality gates enable early and continuous monitoring of quality requirements. This is particularly important in order to identify and rectify errors in good time before they have cost-intensive consequences. The transformation from traditional quality controls to integrated quality gates is therefore a decisive step towards increasing efficiency and ensuring competitiveness.
Old: Traditional quality tests
Traditional approach: In traditional quality inspections, products or services are usually checked for conformity with the specified standards at the end of the manufacturing process. This final inspection is often based on random inspections and manual testing procedures. The data is recorded in paper form or in isolated systems, which makes evaluation and traceability difficult. A key feature of this approach is the reactive handling of complaints management, which are only recognized after production control has been completed. This leads to increased error costs, delays and a lack of transparency in quality management.
New: Integrated quality gates
Quality gates: The modern approach relies on integrated quality gates, which are implemented as proactive control points in the various phases of the production and procurement process. Through the integration of digital technologies and real-time data
Conclusion on the implementation of quality gates
Quality gates are indispensable control points in the modern purchasing process that systematically ensure quality and compliance. Thanks to clearly defined criteria, standardized inspection procedures and digital support, they enable early error detection and risk minimization. The success of quality gates depends largely on their efficient integration into existing processes and consistent digitalization. Despite initial challenges during implementation, the long-term benefits of improved product quality, optimized supplier relationships and increased process efficiency outweigh the risks.
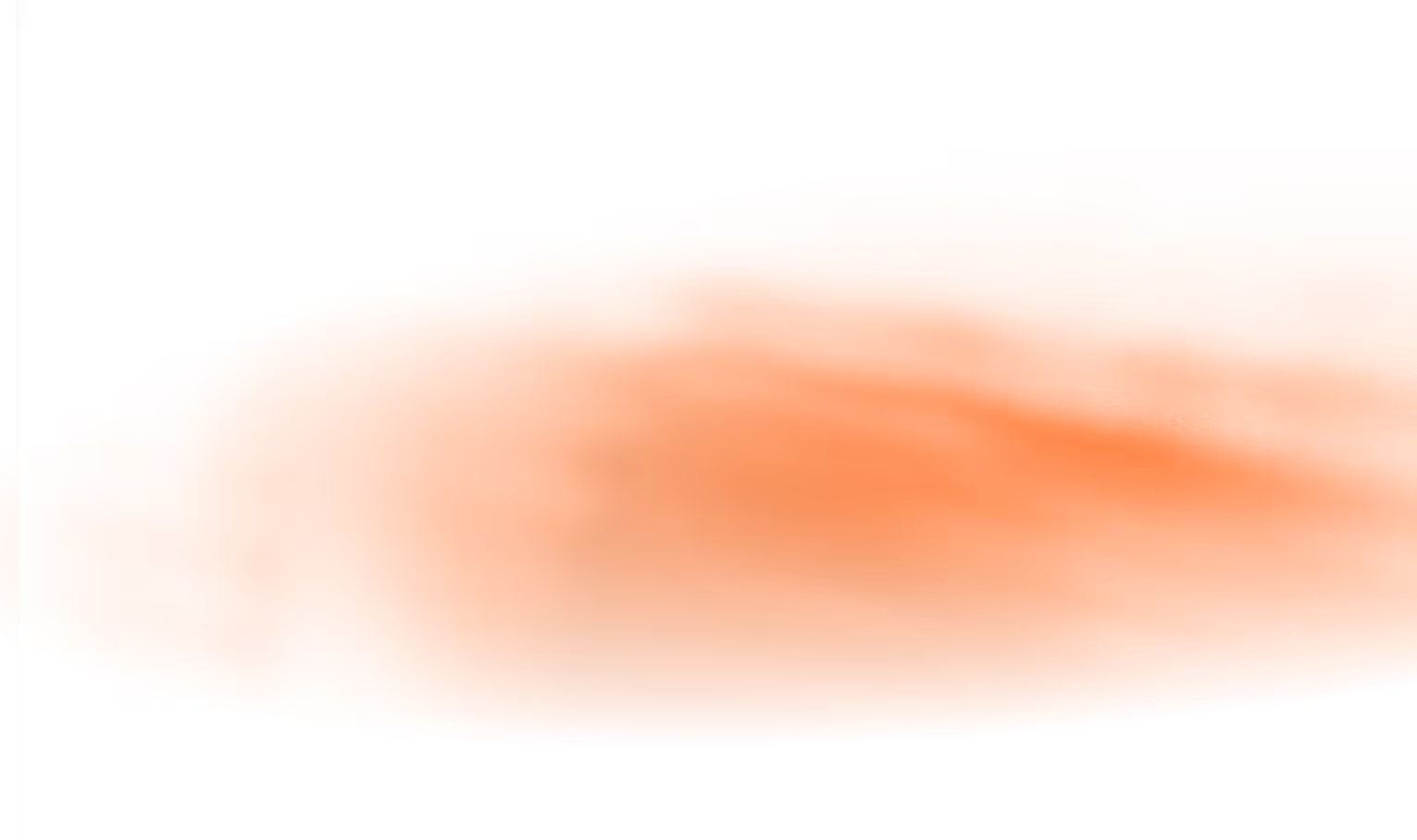
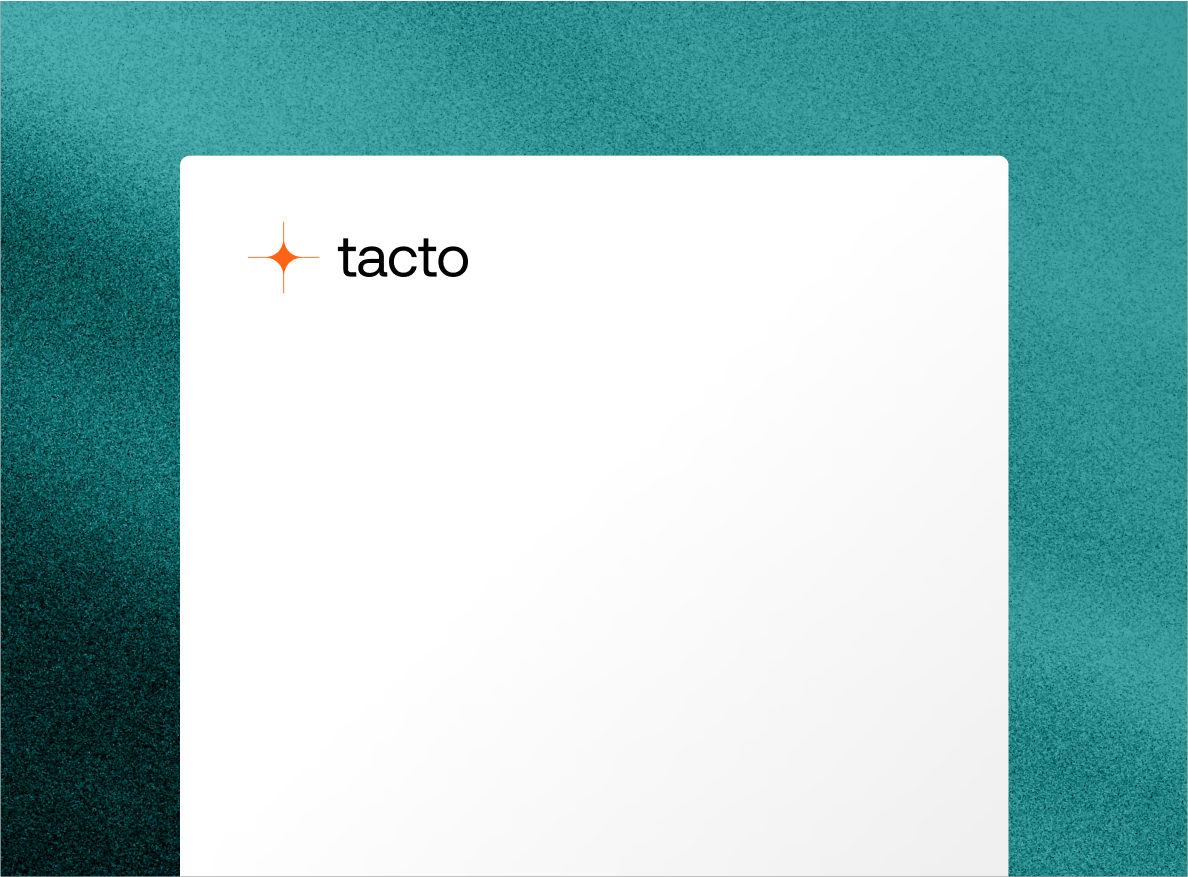