Procurement Glossary
Framework supply agreement: When does a framework supply agreement make sense?
A framework supply agreement creates the basis for long-term and efficient cooperation between buyer and supplier by defining the key conditions for recurring procurement transactions. This structured overview shows you how you can reduce process costs and increase security of supply at the same time through clever contract design.
Framework supply agreement in a nutshell:
A framework supply agreement is a contractual agreement between the purchaser and supplier for recurring deliveries of goods at fixed conditions over a defined period of time. For Procurement , this ensures stable prices, guaranteed availability and reduced process costs thanks to simplified order processing.
Example: An automotive supplier concludes a 24-month framework agreement with its steel supplier for the delivery of 1,000 tons of sheet steel per year at a fixed price of €900/ton, with monthly call-offs of at least 50 tons.
What is a framework supply agreement?
A framework supply agreement is a long-term contract between a buyer and a supplier that sets out the general conditions for future deliveries. It defines the framework conditions such as prices, payment terms, delivery times and quality standards, without specifying the concrete quantities and delivery dates.
Conditions and contents of a framework supply agreement
A carefully drafted framework supply agreement is the foundation for a successful and long-term business relationship between buyer and supplier. It defines the general terms and conditions under which future deliveries will take place, thus minimizing potential risks and ambiguities. The key elements of such a contract include
- Contract term: A clear definition of the validity period is crucial. It determines the period over which the agreed conditions apply. A precise term creates planning security for both parties and enables a strategic alignment of the business relationship.
- Price conditions: The determination of prices and any price change clauses forms the core of the contract. This is where the costs for the delivered goods are determined and mechanisms for price adjustment clauses, for example in the event of market fluctuations or currency fluctuations, are agreed. Transparent price conditions prevent misunderstandings and financial discrepancies.
- Terms of delivery: This section regulates the details of the delivery of goods. This includes delivery times, delivery locations and the chosen delivery method. Clear delivery service levels ensure that products are delivered on time and to the right place, which is essential for maintaining production processes and supply chains.
- Terms of payment: Agreeing payment terms and methods ensures financial stability and liquidity on both sides. Whether prepayment, payment on account or special payment terms - precise payment terms prevent payment arrears and promote a trusting relationship.
- Quality standards: Defining the required quality of goods and the corresponding test procedures ensures that the delivered products meet the agreed specifications. By defining quality criteria and acceptance processes, complaints can be reduced and satisfaction increased.
- Termination conditions: Conditions under which the contract can be terminated provide legal certainty. Notice periods, possible reasons for early termination and consequences in the event of a breach of contract are set out here. This protects both parties from unexpected termination of the business relationship and enables orderly processing in the event of termination.
A comprehensive framework supply agreement that covers all these points in detail forms the basis for stable and efficient cooperation. It allows both parties to focus on their core competencies while providing legal and operational clarity. By taking these conditions and contents into account, the contract becomes an instrument that promotes trust, minimizes risks and paves the way for a successful long-term partnership.
Master supply agreement: from traditional contract to digital supplier relationship management
The framework supply agreement has been a key instrument for long-term business relationships and efficient procurement processes for decades. Despite its importance, traditional methods of contract management often reach their limits, particularly in terms of flexibility and transparency. However, advancing digitalization offers new approaches for structuring framework supply agreements in line with the times and optimizing collaboration with suppliers.
Old: Traditional framework supply agreement
Traditional approach: In conventional practice, framework supply contracts are usually created and managed manually. Contract terms are recorded in writing, and adjustments often require time-consuming negotiations and documentation. Communication is mainly by email or telephone, which can lead to loss of information and inconsistencies. Manual processing of call-offs within the contractual framework is prone to errors and makes it difficult to keep track of delivery quantities, prices and delivery times. There is also a lack of real-time data for informed decision-making, which limits risk management.
New: Digital Supplier Relationship Management (SRM)
Supplier relationship management: Modern companies integrate framework supply contracts into digital SRM systems to automate and improve contract management. Contract data is recorded centrally via electronic platforms and is accessible to all parties involved in real time. Automatic notifications in the event of contract changes, impending extensions or price changes increase transparency and responsiveness. In addition, integrated analysis tools enable the evaluation of supplier ratings and contract usage. This leads to more efficient processes, reduces administrative effort by up to 30% and promotes proactive management of supplier relationships.
Practical example: Optimization in the manufacturing industry
A medium-sized company in the manufacturing industry implemented a digital SRM system to manage its framework supply contracts. By automating the contract processes, the time required to conclude and amend contracts was reduced by 40%. Real-time data enabled better planning of material requirements, which led to a 15% reduction in stock levels. In addition, supplier reliability improved by 25% as communication processes and call-offs were made more efficient. Overall, the company achieved cost savings of over 500,000 euros per year and significantly increased its competitiveness.
Conclusion: When does a framework supply agreement make sense?
A framework supply agreement is particularly useful for companies that have a regular requirement for certain goods or raw materials and want to rely on long-term business relationships. The fixed conditions and planning security can reduce costs and make procurement processes more efficient. The framework supply agreement offers considerable advantages, particularly if stability in the supply chain, consistent quality standards and close cooperation with suppliers are desired. Nevertheless, each company should check individually whether the long-term commitment and the specified conditions are compatible with its own flexibility requirements and market conditions. Overall, the framework supply agreement is a strategic instrument which, if used correctly, can lead to sustainable success in procurement.
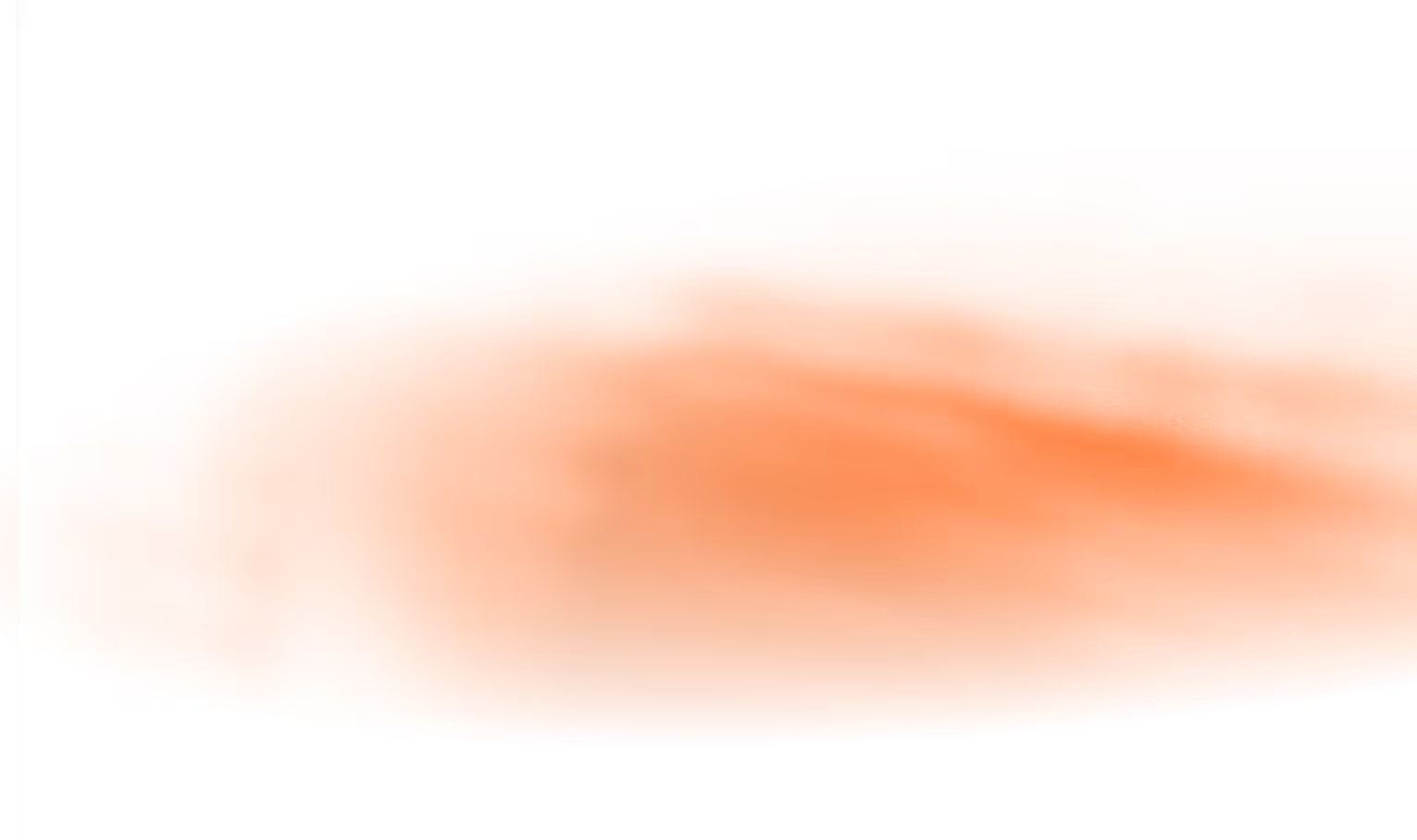
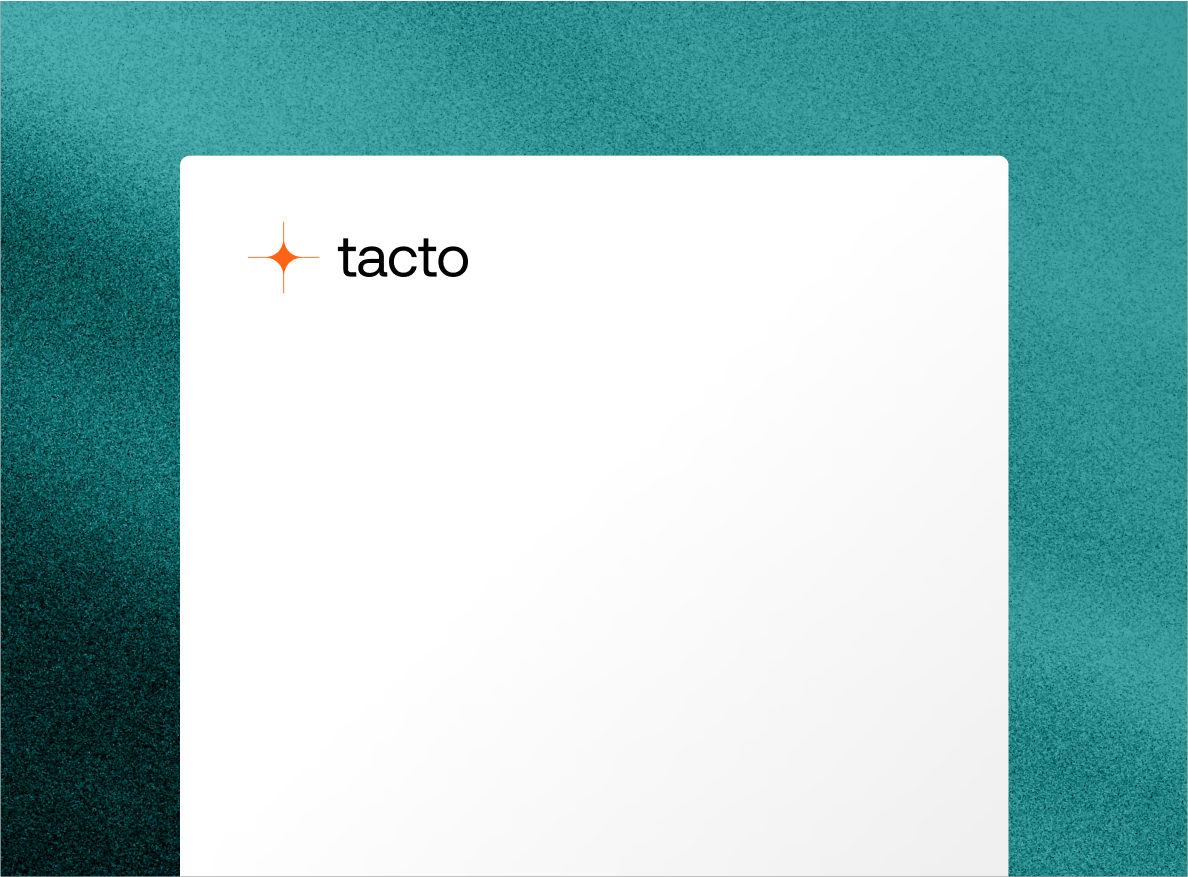