Procurement Glossary
Delivery service level: definition & important aspects for buyers
The delivery service level measures the quality and reliability of supplier relationships and is therefore a key performance indicator for evaluating security of supply. This structured overview shows you how you can use the delivery service level as a strategic management tool in Procurement and thus optimize the performance of your supply chain.
Delivery service level in a nutshell:
The delivery service level describes the percentage of deliveries completed on time and in full in relation to the total number of all deliveries. For Procurement , this KPI is essential for evaluating supplier performance and ensuring a stable supply.
Example: An automotive supplier achieves a delivery service level of 98.5% by receiving a total of 985 deliveries on time and in full out of 1,000 deliveries in the first quarter of 2023, while 15 deliveries have deviations.
Introduction to purchasing controlling: delivery service level
The delivery service level is a key performance indicator in supply chain management and logistics that measures the quality and reliability of a company's delivery performance. It indicates how well a company is able to meet customer requirements in terms of delivery time, delivery quantity and delivery quality. In today's highly competitive business environment, a high delivery service level is crucial for customer satisfaction and long-term business success. This introduction will explore the various aspects of delivery service levels, how they are calculated and their importance in modern business management.
What is the delivery service level?
The delivery service level is a key figure that indicates the extent to which a company can fulfill its customers' orders in full and on time. It measures the ability to deliver the desired quantity of a product to the right place at the right time. A high delivery service level is an indicator of efficient logistics and customer-oriented processes.
Core elements of the delivery service level
Significance for Procurement
In Procurement , the delivery service level is a key criterion when evaluating suppliers. A high delivery service level has a direct impact on end customer satisfaction and supply chain efficiency. By monitoring this key figure, buyers can identify potential bottlenecks at an early stage, optimize stock levels and strategically select suppliers.
Delivery service level: from manual recording to real-time analysis
The delivery service level is a key indicator of supply chain performance and has a direct impact on customer satisfaction. Traditionally, it was recorded manually, which was time-consuming and error-prone. In an increasingly digitalized world, however, there is a need to optimize this process and respond more quickly to deviations. The transformation to digital methods enables more precise and efficient monitoring of the delivery service level.
Old: Manual measurement of the delivery service level
Traditional approach: In the past, delivery service level data was often collected manually from various sources. Employees collected information from delivery bills, orders and demand analysis and entered it into spreadsheets. The evaluation was usually carried out monthly or quarterly, which led to delays in identifying problems. In addition, manual data entry was prone to errors and inconsistent data, which impaired the reliability of the analyses. The time required meant that companies could only react to delivery deviations to a limited extent and were unable to avert potential effects on production or customer service in good time.
New: real-time monitoring with advanced analytics
Real-time analytics: Modern companies rely on digital technologies and real-time analyses to continuously and precisely monitor the delivery service level. By integrating ERP systems, SCM software and IoT sensors, delivery data is automatically recorded and analyzed in real time. Risk management and machine learning algorithms analyze patterns and predict potential delivery bottlenecks or delays. This enables proactive measures to be taken, such as adjusting order quantities or rerouting deliveries. Real-time monitoring not only improves the accuracy of the data, but also increases flexibility and reaction speed within the supply chain. As a result, companies can significantly increase their delivery service level and boost customer satisfaction.
Practical example: Increasing the delivery service level in the electronics industry
An electronics manufacturer implemented a real-time tracking system to monitor its delivery service level. Thanks to automated data collection and the use of advanced analytics, the delivery service level rose from 90% to 99% within six months. At the same time, the stock levels reduced by 20% as the improved transparency in the supply chain enabled more accurate demand forecasting. The company benefited from reduced costs and higher customer satisfaction as delivery dates were met more reliably.
Conclusion on supplier evaluation
The delivery service level is an essential key figure for evaluating logistics efficiency and customer satisfaction. Its systematic recording and optimization enables companies to improve their supply chains, reduce costs and achieve competitive advantages. By using modern technologies and strategic supplier management, companies can achieve a high delivery service level and secure it in the long term.
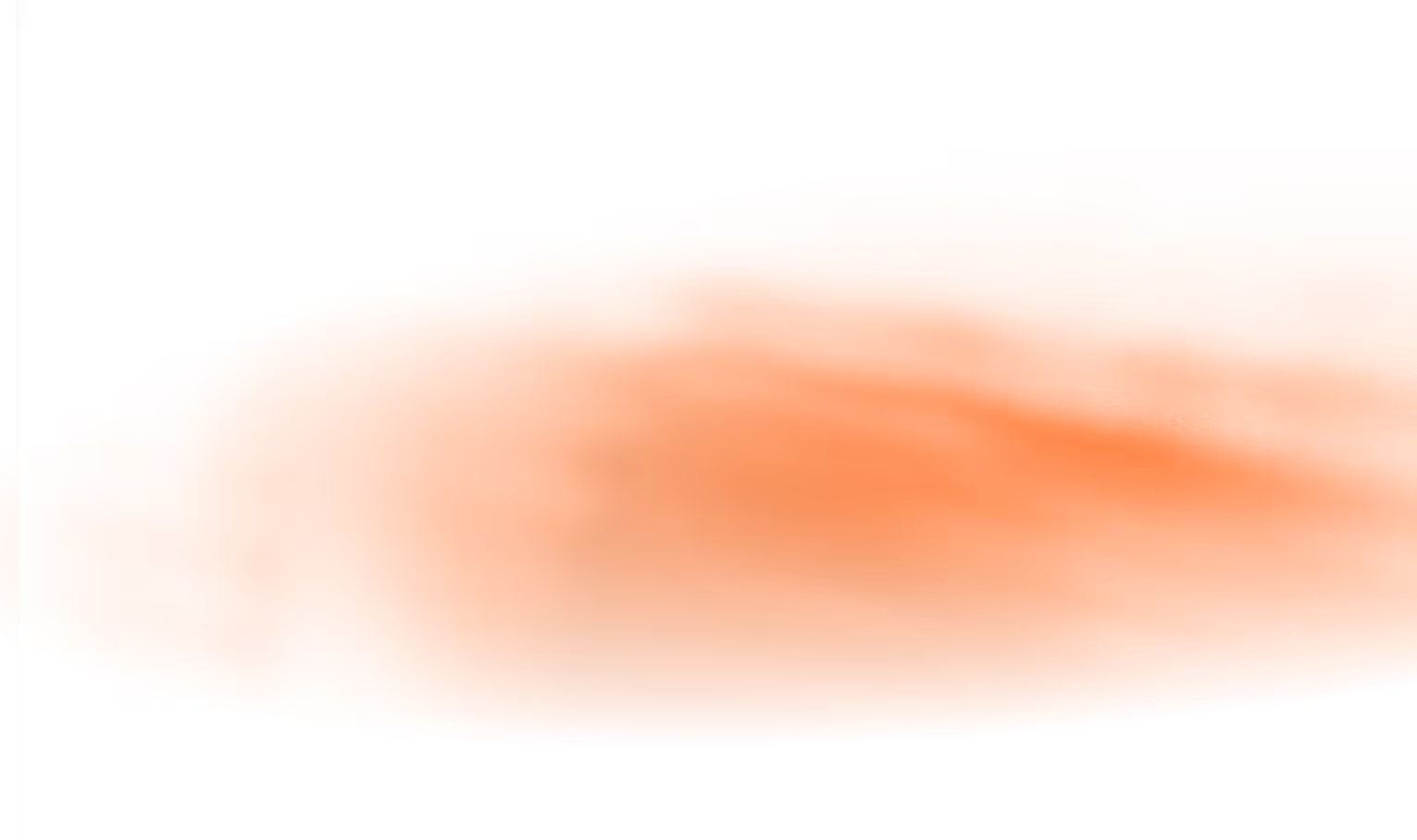
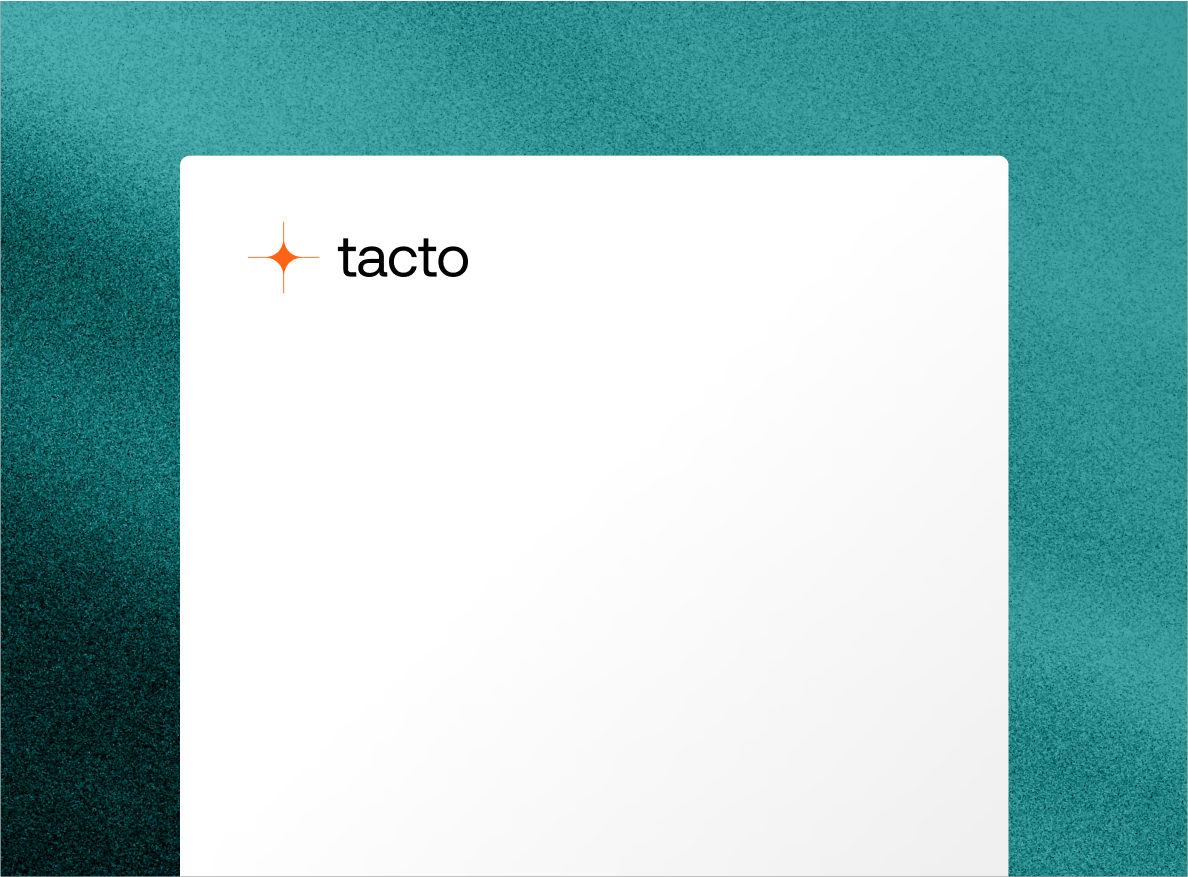