Procurement Glossary
Risk classes: Definition and important aspects for buyers
The systematic classification of suppliers and materials into risk classes helps companies to identify risks at an early stage and take targeted countermeasures. This structured overview shows how you can effectively manage your procurement risks and sustainably safeguard your supply chain by classifying them correctly.
Risk classes in a nutshell:
Risk classes are standardized categories for classifying suppliers or materials according to their risk potential for the company. In Procurement , they enable the systematic prioritization of risk management measures and the definition of corresponding control and monitoring mechanisms.
Example: A car manufacturer classifies its 2,500 suppliers into four risk classes (A to D), whereby the 150 A suppliers are classified as critical and are subject to quarterly audits and monthly monitoring, while D suppliers are only audited annually.
Risk classes in purchasing controlling
Risk classes are a fundamental concept in risk management and the financial world. They are used to systematically categorize and assess various risks in order to enable effective risk management. The classification of risk classes helps companies, investors and financial institutions to better assess potential dangers and take appropriate measures to minimize risk. In this introduction, we will take a closer look at the different types of risk classes, their importance for risk management and their practical application in different areas of the economy.
What are risk classes?
Risk classes are categories that are used to systematically classify risks. They are used to identify and evaluate potential sources of danger and to take suitable risk management measures. In procurement, risk classes help to classify suppliers and procurement processes according to their risk potential and thus make risk management more effective.
Core elements of risk classification
Importance of risk classes in Procurement
In the procurement environment, risk classes are essential in order to secure supplier relationship management and procurement processes. Classification enables companies to identify potential disruptions at an early stage and act proactively. This increases security of supply, reduces potential financial losses and strengthens the resilience of the entire supply chain.
Risk classes: From manual risk assessment to data-driven risk management
Building on the theoretical basis of risk classes in Procurement , it is crucial in practice to systematically identify and assess risks. This enables companies to recognize potential disruptions in the supply chain at an early stage and act proactively. In view of increasing global networking and complexity, there is a growing need to switch from traditional methods to modern approaches in order to work more efficiently and precisely.
Old: Manual risk assessment
Traditional approach: In traditional practice, risks were often assessed through manual processes and subjective assessments. Buyers relied on personal experience, simple checklists and occasional supplier audits. Tools such as Excel spreadsheets were used to gather information, but the data lacked depth and timeliness. This method was time-consuming and prone to human error. In addition, changes in the market or at suppliers could often not be recorded quickly enough, which led to unexpected supply bottlenecks and quality problems.
New: Data-driven risk management
Data-driven risk management: Modern approaches integrate digital technologies and large volumes of data to enable comprehensive and up-to-date risk analysis. By using specialized software solutions, data on supplier evaluation, market trends and geopolitical risks is continuously collected and analyzed. Artificial intelligence and machine learning help to identify patterns and make predictions. This leads to faster decision-making processes, greater forecasting accuracy and the ability to proactively manage risks. Practical benefits include reduced delivery failures, improved quality standards and increased transparency along the entire supply chain.
Practical example: Implementation in the electronics industry
A globally active electronics manufacturer introduced a data-driven risk managementsystem that analyzes real-time data from over 1,000 suppliers. Through automated risk classification, the company was able to accelerate the identification of critical risk sources by 50%. As a result of improved risk management, delivery delays were reduced by 35% and quality defects fell by 25%. These improvements led to cost savings of over 5 million euros annually and strengthened the company's competitiveness in the global market.
Conclusion on risk classification
Risk classes are an indispensable tool in modern procurement management. They enable a structured assessment of supplier risks and form the basis for effective preventative measures. By systematically applying risk classes, companies can make their supply chains more robust and identify potential disruptions at an early stage. With the use of new technologies such as AI and predictive analytics, risk classification is becoming increasingly precise and dynamic, which further increases security of supply.
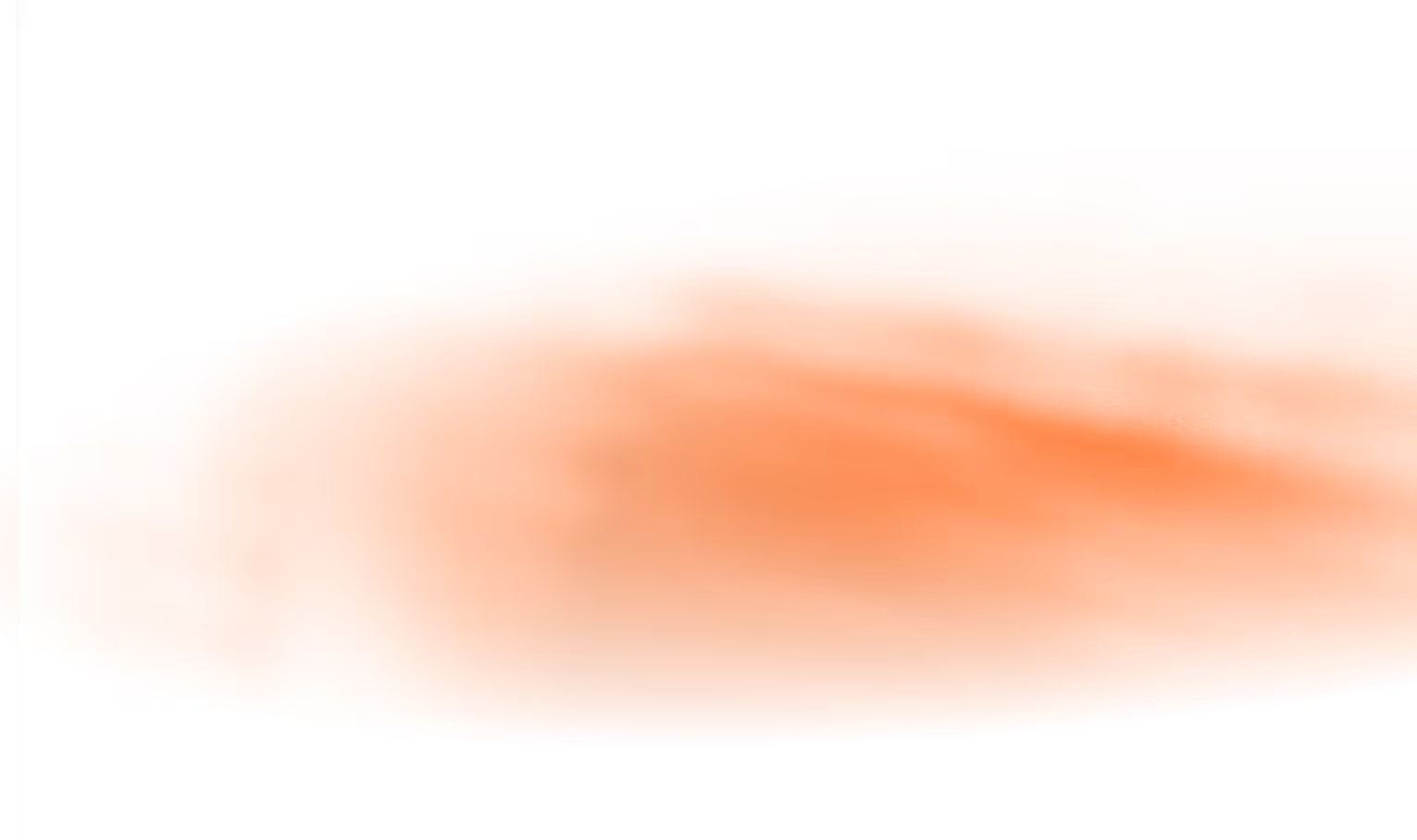
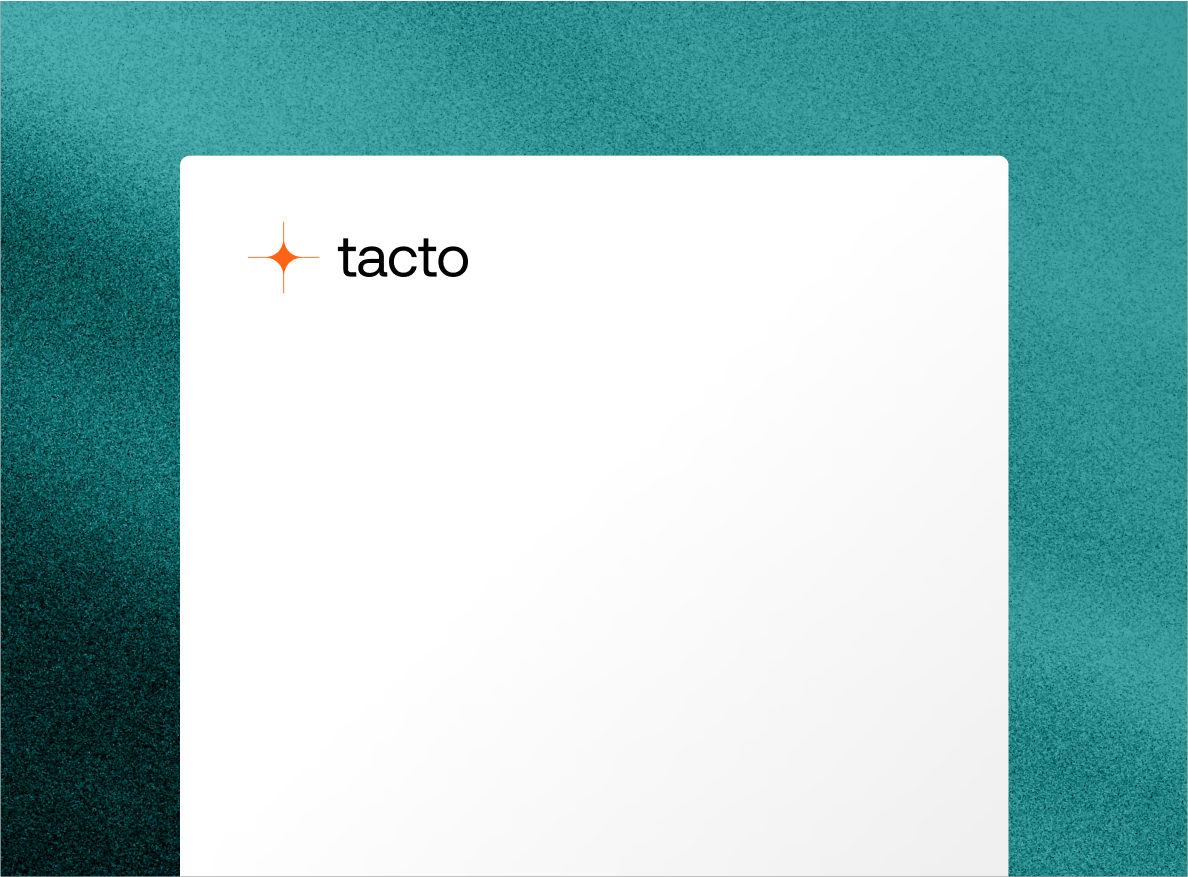