Procurement Glossary
Sampling: definition and important aspects for buyers
Sampling enables companies to monitor the quality of incoming goods efficiently and cost-effectively without having to check every single part. This structured overview shows you how you can use the right sampling strategy to reduce inspection costs and at the same time optimally manage the quality risk in Procurement .
Sampling in a nutshell:
A random sample inspection is a statistical procedure for quality control in which only a defined part of a quantity of goods is inspected according to specified criteria. For Procurement , this enables efficient quality assurance while minimizing the time and cost of incoming goods inspections.
Example: For a delivery of 10,000 screws, 200 pieces are randomly selected and tested according to the AQL standard (Acceptable Quality Level), whereby the entire delivery is accepted if a maximum of 3 defective parts are in the random sample.
Sample testing in purchasing controlling
Sampling is an important statistical method for quality control in industrial production and other areas of quality assurance. With this method, it is not the entirety of all units of a production or a process that is inspected, but only a representative subset. This systematic approach makes it possible to make reliable statements about the quality of the population at a reasonable cost. Sampling has established itself as a cost-efficient and time-saving alternative to full inspection and is now an indispensable tool in modern quality management. In this guide, you will learn about the most important principles, methods and areas of application of sampling.
What is sampling?
Sampling is an inspection method in which only part of a total quantity is inspected in order to draw conclusions about the whole. In procurement, this means that not all delivered products or documents are fully inspected, but the quality inspection of the entire delivery is assessed on the basis of selected samples. This method makes it possible to work more efficiently and conserve resources without significantly compromising the reliability of the inspection.
Core elements of sampling
Importance of sampling in Procurement
In the procurement process, random sample testing is an important tool for quality assurance agreements and risk minimization. By carrying out targeted spot checks, buyers can ensure that suppliers comply with the agreed quality standards without having to check each item individually. This saves time and money and helps to make supply chain resilience more efficient.
Sampling: from manual checks to automated quality monitoring
In many companies, random sample testing forms the backbone of quality assurance. Based on statistical methods, it makes it possible to draw conclusions about the overall quality of a batch from the inspection of just a few units. In practice, however, companies are faced with the challenge of converting traditional manual processes into modern, efficient quality inspection in order to meet the increasing demands for speed and precision.
Old: Manual spot check
Traditional approach: In traditional sampling, employees are trained to perform manual inspections based on set criteria. Sample selection is often random and inspectors use physical checklists to document errors and defects. This process is time-consuming and prone to human error. In addition, the data is often not recorded digitally, which makes subsequent analysis and tracking difficult.
New: Statistical Process Control (SPC)
Statistical Process Control (SPC): Modern quality control relies on automated systems and statistical process control. Data is continuously collected by integrating sensors and measuring devices directly into the production control system. This data flows in real time into software solutions that use algorithms to detect deviations from the target status. This enables companies to react proactively to quality problems before faulty products even arise. The use of SPC makes it possible to increase process capability and simultaneously cut costs by reducing rework and rejects.
Practical example: Introduction of SPC in an automotive supplier
A medium-sized automotive supplier implemented Statistical Process Control in its production of precision components. By using intelligent measuring systems, the error rate was reduced by 30%. The response time to quality deviations was reduced from an average of 8 hours to almost real time. In addition, the manual inspection effort was reduced by 50%, which led to an increase in efficiency and lower process costs. process costscosts of 200,000 euros per year.
Conclusion on sampling
ConclusionSample testing is an indispensable tool in modern quality management. It enables efficient quality control with simultaneous cost optimization. The success of this method depends largely on the correct statistical implementation and careful definition of the test parameters. With the advent of digital technologies and AI-supported systems, random sample testing is becoming even more precise and reliable, further minimizing quality risks. The balance between inspection effort and quality assurance remains crucial.
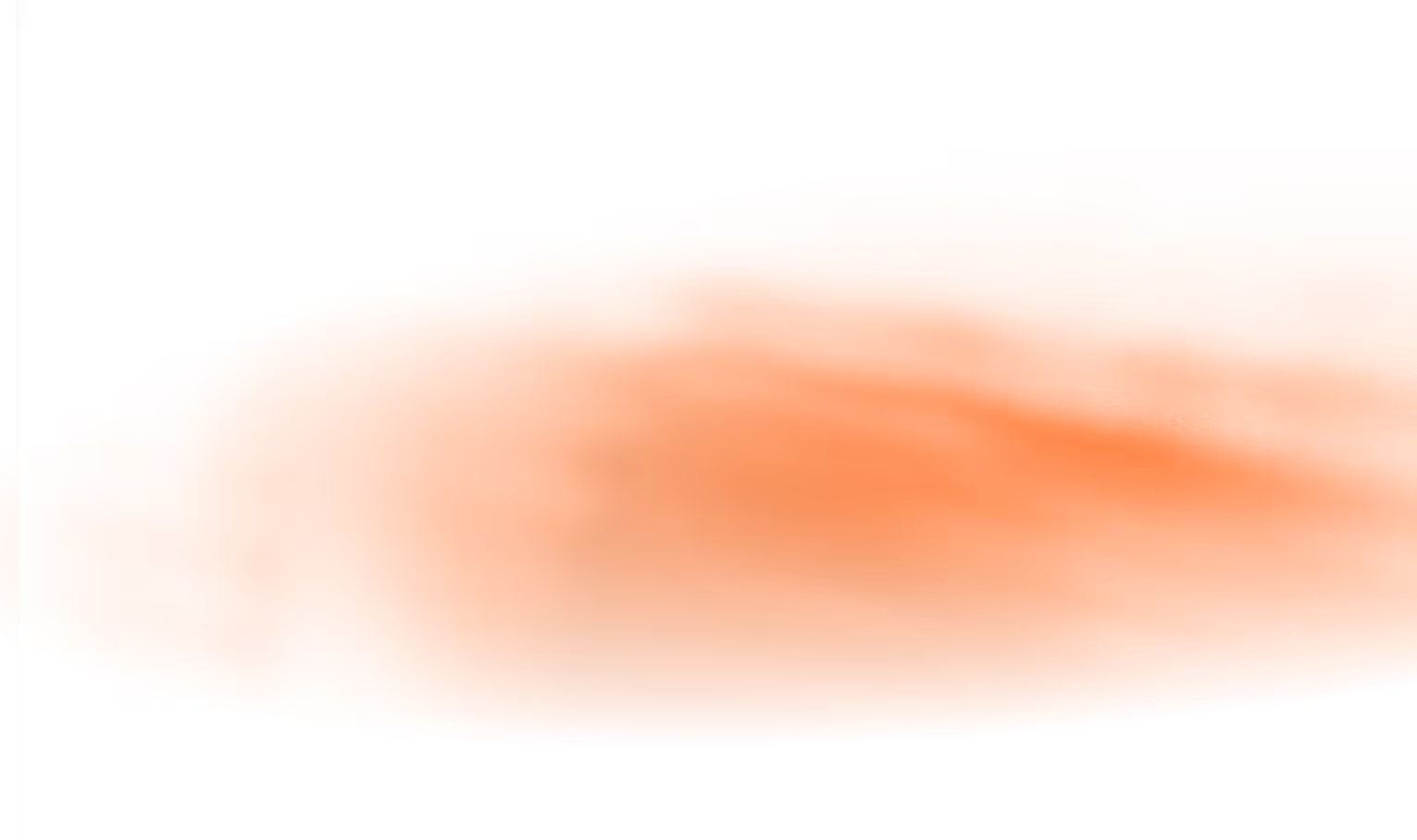
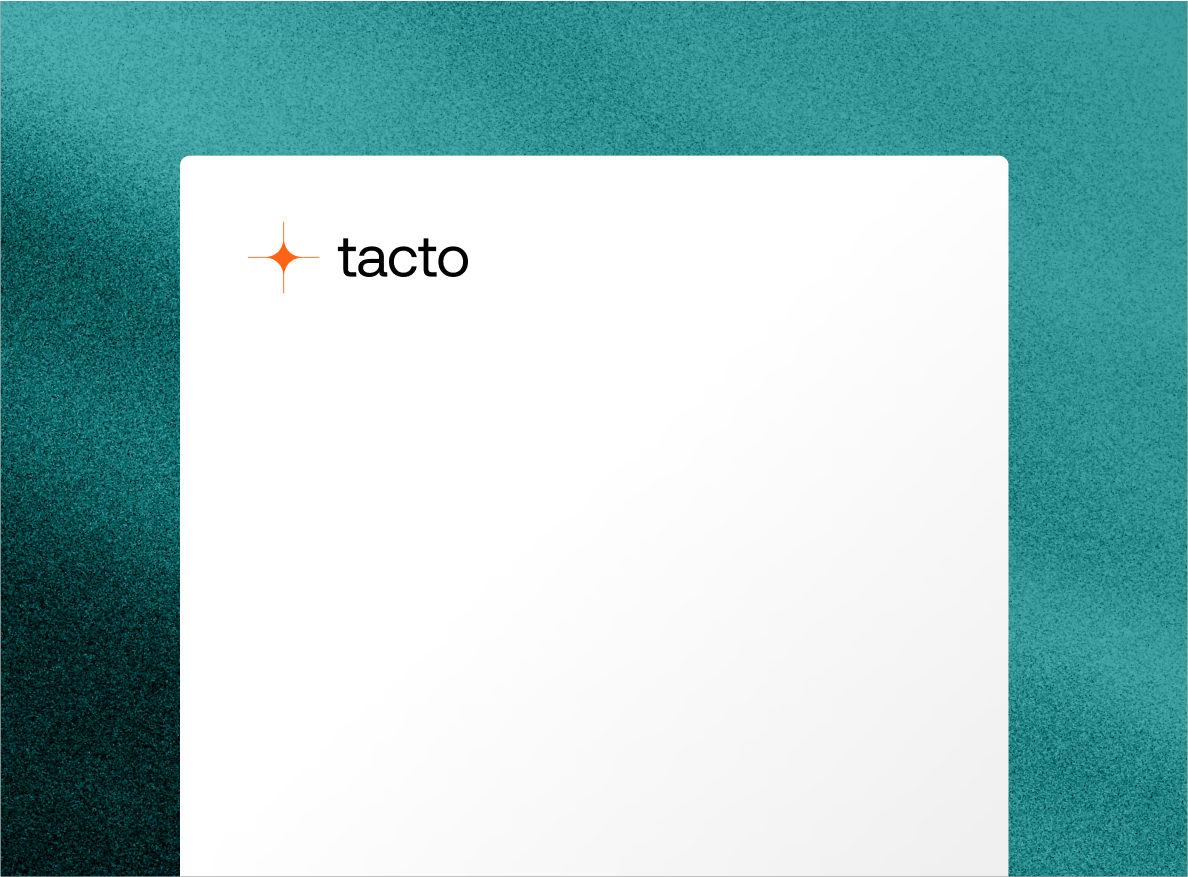