Procurement Glossary
Definition & important aspects for buyers
As a central reference work, a parts catalog creates transparency across the entire range of parts and enables efficient management of all technical and commercial information. The following overview shows how you can use a systematic catalog structure to optimize Procurement processes and identify potential savings.
Parts catalog in a nutshell:
A parts catalog is a structured database that centrally records and categorizes all relevant information on a company's parts, components and materials. For Procurement , it enables efficient management of the parts range, standardized procurement processes and the avoidance of duplicates.
Example: By introducing a digital parts catalog with 50,000 classified components, an automotive supplier reduces the number of redundant parts by 15% and achieves a reduction in process time when searching for parts from an average of 12 minutes to 2 minutes per process.
Parts catalog - An introduction
The parts catalog is a fundamental tool in the technical field and in industrial production. It serves as a systematic compilation of all available parts, components and materials used in a company. A well-structured parts catalog enables efficient management of the parts range, simplifies ordering processes and contributes to standardization. In this introduction, you will learn about the most important aspects of the parts catalog, from its basic structure and its importance in production to modern digital catalog solutions and their implementation in day-to-day business.
What is a parts catalog?
A parts catalog is a systematically structured collection of information about spare parts, components and materials used in a company. It serves as a central reference tool for purchasers, technicians and maintenance personnel to quickly and efficiently identify the required parts, view their specifications and place orders. By using a parts catalog, procurement processes can be accelerated and errors in parts selection reduced.
Core elements of a parts catalog
Significance for Procurement
In Procurement , the parts catalog plays a decisive role in optimizing procurement processes. The central availability of all relevant parts information allows orders to be placed more efficiently and delivery times to be shortened. The parts catalog also enables better cost control and contributes to standardization within the company.
Parts catalog: From paper-based lists to the Electronic Parts Catalog
The parts catalog is an indispensable tool for efficient materials management in companies. Traditionally, parts catalogs were managed manually, which was associated with considerable effort and potential for error. In view of the increasing complexity and dynamism of procurement logistics, there is a growing need for modern solutions. The transformation to digital systems enables optimized parts management and makes a significant contribution to competitiveness.
Old: Paper-based parts catalog
Traditional approach: In the past, parts catalogs were kept as physical documents, often in the form of folders or printed directories. Employees updated the data manually, which was time-consuming and carried a high risk of error. The procurement and identification of parts was carried out by tediously searching through these documents. In addition, information was often out of date as changes were not entered in real time. The limitations of this approach resulted in inefficient processes, increased costs due to incorrect orders and limited transparency regarding existing inventory management.
New: Electronic Parts Catalog
Electronic Parts Catalog: Modern companies rely on digital solutions such as the Electronic Parts Catalog. This digital parts catalog integrates seamlessly into existing ERP and merchandise management systems and provides a central platform for all parts information. Key innovations include real-time updates, search functions with filter options and the integration of CAD data and specifications. Improvements can be seen in the rapid availability of up-to-date information, reduced incorrect orders and optimized stock levels. In addition, the digital catalog supports collaboration with supplier management through automatic ordering processes and direct communication tools.
Practical example: Introduction at an automotive supplier
A leading automotive supplier implemented an Electronic Parts Catalog to manage its more than 50,000 items more efficiently. Digitization reduced search times for parts by 60%. The error rate for orders fell by 35% and warehousing costs were reduced by 20%. At the same time, internal communication between Procurement, warehouse and production improved significantly. The company benefited from a faster time-to-market and was able to make its processes more agile, which led to an increase in customer satisfaction.
Conclusion on parts catalog design
Parts catalogs are indispensable tools for an efficient and error-free purchasing process. They not only optimize procurement through centrally available information and standardized processes, but also reduce costs and processing times. Despite the challenges of data maintenance and system integration, the advantages clearly outweigh the disadvantages. With increasing digitalization and AI integration, parts catalogs are becoming even more valuable for strategic purchasing management and sustainable process optimization.
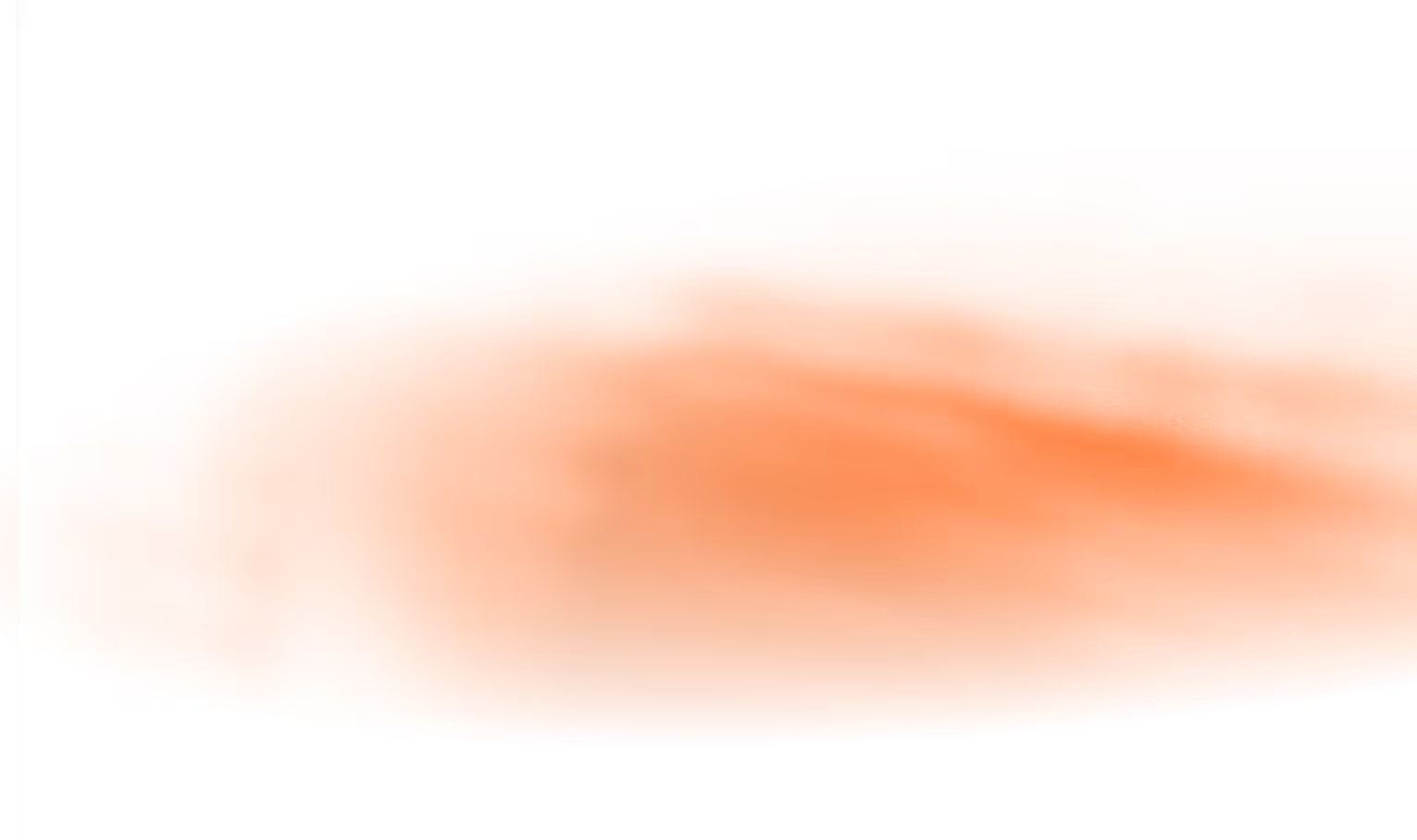
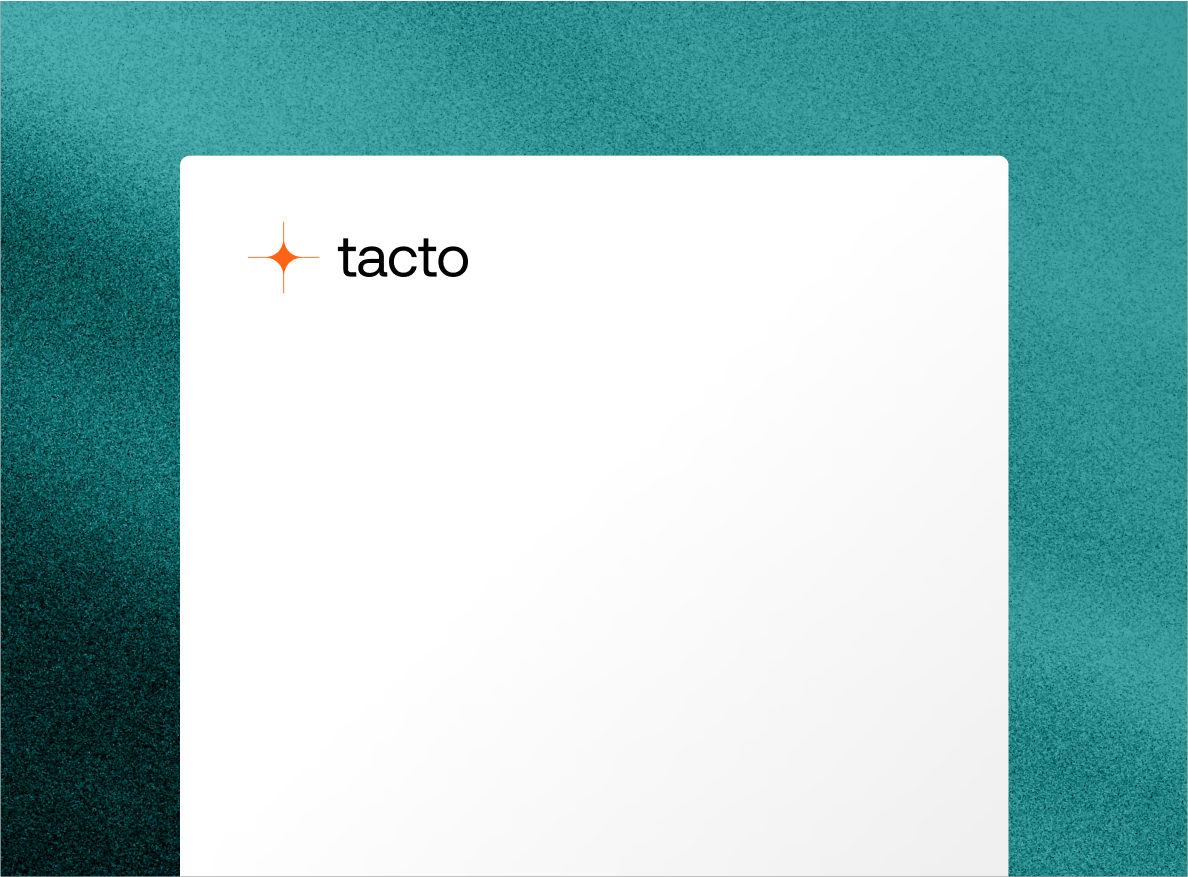