Procurement Glossary
Replenishment lead time: definition and important aspects for buyers
The replenishment lead time significantly determines the availability of materials and has a direct influence on stock levels, delivery capability and capital commitment. This structured overview shows how you can make your procurement processes more efficient and reduce costs by optimizing replenishment times.
Replacement time in a nutshell:
The replenishment lead time describes the period between the order being triggered and the ordered goods being available in the warehouse. For Procurement , it is a critical parameter for optimizing inventory planning and avoiding supply bottlenecks.
Example: When procuring electronic components from Asia, the replenishment time is 12 weeks, consisting of 2 weeks production time, 8 weeks sea transportation and 2 weeks for customs clearance and internal transportation.
Introduction to purchasing controlling: replenishment lead time
Replenishment lead time is a fundamental parameter in logistics and supply chain management. It describes the period between the order being triggered and the actual receipt of goods in the company. This period is of crucial importance for materials management and production planning, as it has a direct influence on inventory management and security of supply. In today's fast-paced business world, where just-in-time delivery and optimized inventory management are becoming increasingly important, effective management of replenishment lead time plays a key role in a company's success. In this article, we look at the different aspects of replenishment lead time and its importance for modern businesses.
What is the replacement time?
The replenishment lead time in Procurement the period between ordering a material or product and its arrival in the warehouse. It includes all steps of the procurement process, from determining requirements to ordering, delivery and storage. Understanding the replenishment lead time is crucial in order to place repeat orders in good time and avoid supply bottlenecks.
Core elements of the replacement period
Significance for the procurement process
Knowing the replenishment lead time is essential for effective procurement planning. It makes it possible to optimally set order times in order to minimize stock levels and at the same time ensure delivery readiness. By taking replenishment lead times into account, companies can avoid cost-intensive rush orders, keep production processes stable and ensure customer satisfaction through on-time deliveries.
Replenishment time: from static planning to agile procurement
In practice, replenishment lead time is a key factor for the efficiency of the supply chain and the competitiveness of a company. It has a significant influence on warehousing, production planning and the ability to meet customer requirements promptly. However, traditional methods for determining replenishment lead times reach their limits in a dynamic market environment. Modern companies therefore rely on innovative approaches to make their procurement processes more agile and efficient.
Old: Static replenishment planning
Traditional approach: In traditional procurement, replenishment lead time was treated as a constant and predetermined variable. Companies used historical data and average delivery times to plan reorder point procedures and safety stock levels. This was often done manually or with simple spreadsheets, without taking current market developments into account. This was characterized by high stock levels, long lead times and a lack of flexibility in the event of fluctuations in demand. Challenges arose in particular from unexpected delivery delays, which led to production bottlenecks or excess stock.
New: Dynamic replenishment lead time optimization
Agile supply chain management: Modern procurement management relies on dynamic models that integrate real-time data and advanced forecasting methods. By using ERP systems and digital platforms, companies can continuously adapt replenishment times to current market conditions. Technologies such as artificial intelligence and machine learning enable precise prediction of delivery times and requirements. This leads to reduced stock levels, shorter delivery times and increased responsiveness to changes in demand. In addition, close collaboration with suppliers improves transparency and efficiency along the entire supply chain.
Practical example: Optimization in the electronics industry
An electronics manufacturer implemented a cloud-based procurement system that is networked with its suppliers in real time. By analyzing sales data and supplier capacities, the replenishment time was reduced by 40%. Inventory levels were reduced by 35%, while product availability increased by 20%. In addition, the introduction of just-in-time deliveries enabled flexible adaptation to market trends, which led to a 15% increase in sales within one year.
Conclusion on the replacement time
Replenishment lead time is a key success factor in modern procurement management. It enables precise planning of material procurement, optimizes stock levels and ensures the continuous supply of production. Digital technologies and strategic supplier management allow replenishment lead times to be continuously optimized. Companies that manage their replenishment lead times effectively gain an important competitive advantage and can react flexibly to market requirements.
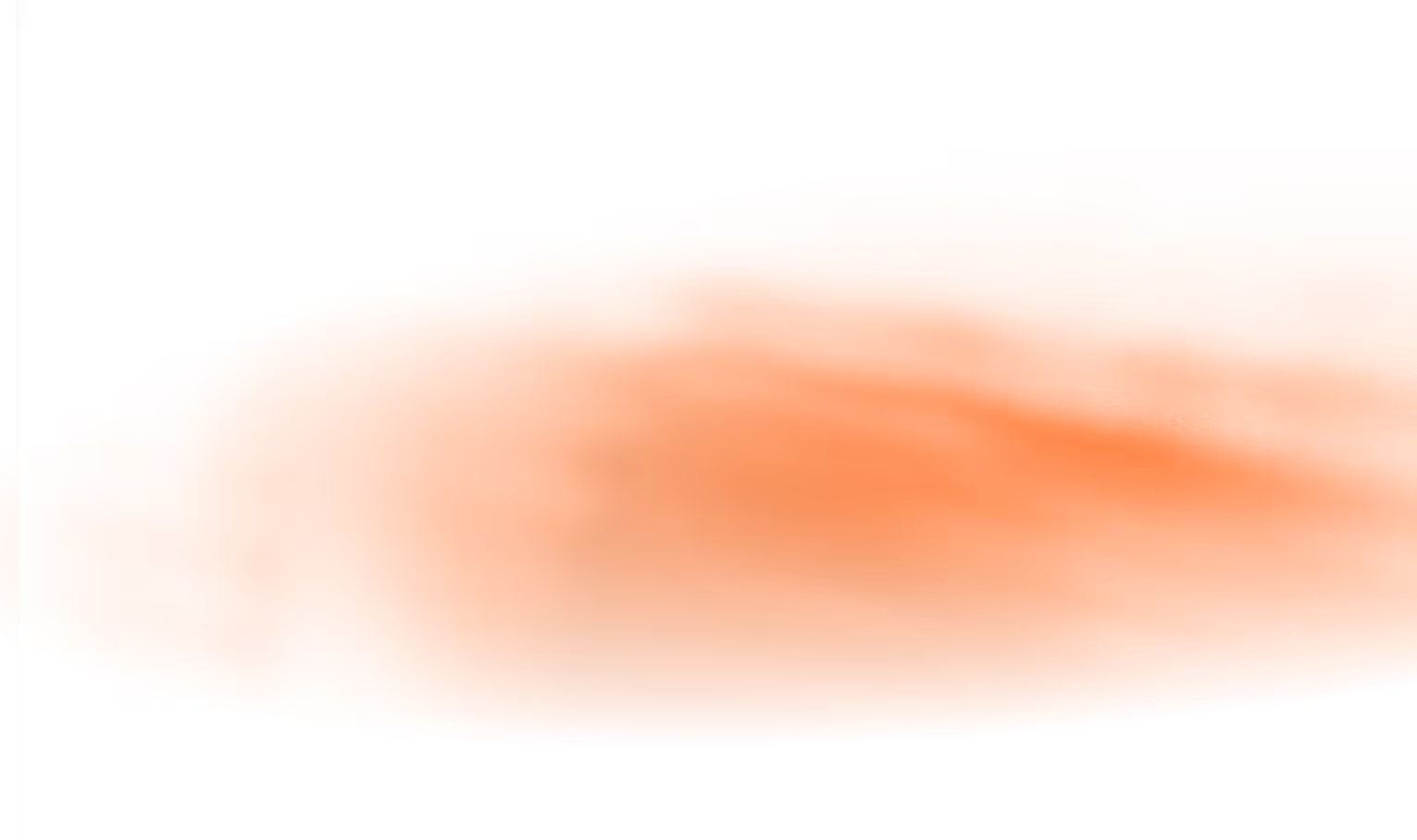
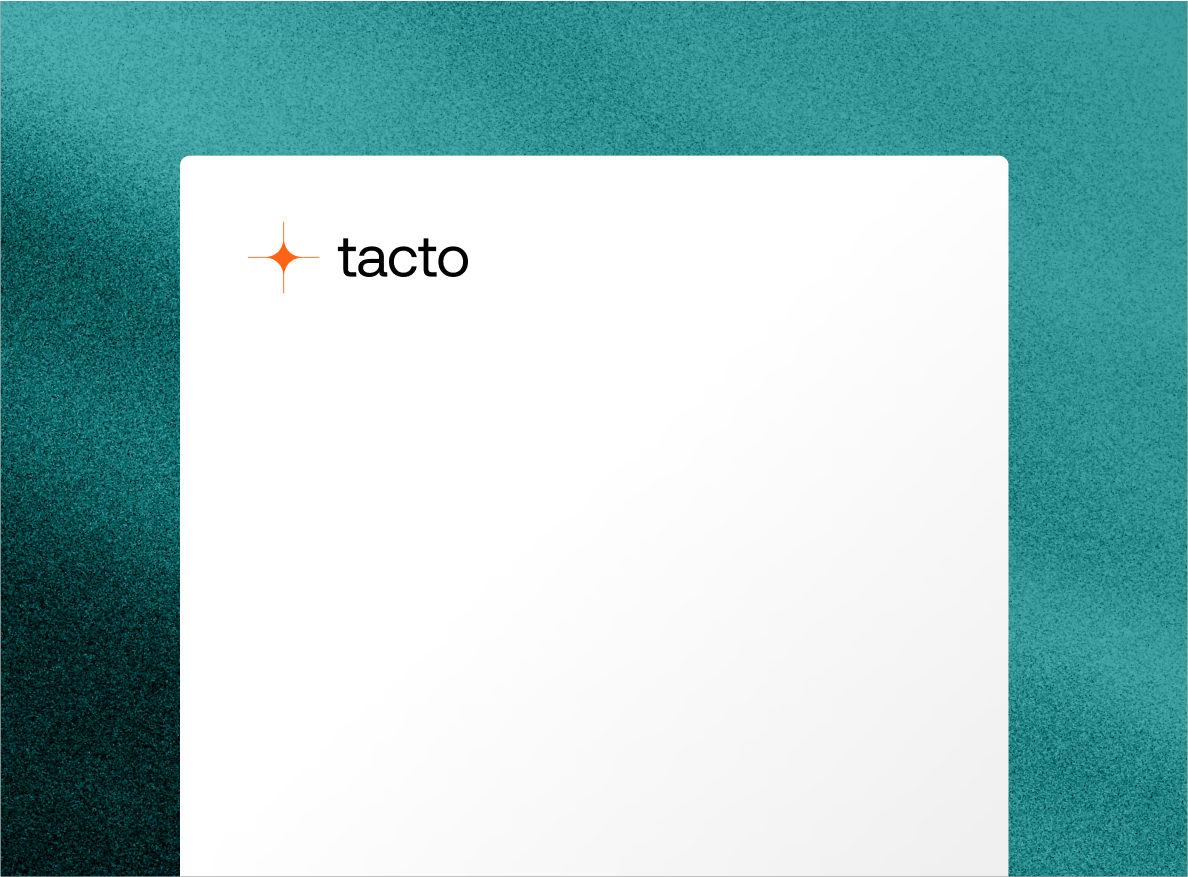