Procurement Glossary
Bottleneck analysis: definition & important aspects for buyers
Bottleneck analysis identifies and eliminates bottlenecks in processes and supply chains in order to sustainably increase efficiency and throughput. This structured overview shows how Procurement uses systematic bottleneck analyses to ensure security of supply and tap into optimization potential.
Bottleneck analysis in a nutshell:
A bottleneck analysis systematically identifies bottlenecks in processes or supply chains that limit the overall throughput. For Procurement , this enables the early detection of critical supply bottlenecks and the development of targeted countermeasures to ensure delivery capability.
Example: An automotive supplier identifies through a bottleneck analysis that the delivery time of a critical electronic component has increased from 6 to 12 weeks and subsequently increases the safety stock from 2 to 4 weeks in order to avoid production interruptions.
Bottleneck analysis: An introduction
Bottleneck analysis, also known as bottleneck analysis, is an important tool in modern process management. It is used to identify and eliminate bottlenecks in production and business processes that hinder or slow down the entire workflow. In today's world, where efficiency and optimization play an ever greater role, the systematic analysis of bottlenecks is becoming increasingly important. This introduction provides an overview of the basic concepts of bottleneck analysis, its areas of application and the methods used to identify and eliminate bottlenecks in various operational contexts.
What is the bottleneck analysis?
Bottleneck analysis is a strategic tool in procurement management that aims to identify and eliminate bottlenecks in the supply chain. By analyzing procurement processes, resource allocation and supplier performance, potential bottlenecks that could affect the production flow or delivery capability can be identified. The aim is to ensure security of supply and minimize operational risks.
Core elements of the bottleneck analysis
Significance for Procurement
Bottleneck analysis is essential in procurement in order to identify and avoid supply bottlenecks at an early stage. By taking proactive measures, buyers can increase security of supply, prevent production downtime and strengthen the company's competitiveness. An effective bottleneck analysis also supports the development of procurement strategies and the diversification of the supplier portfolio.
Bottleneck analysis: from manual risk detection to proactive predictive analytics
Building on the understanding of bottleneck analysis as a strategic tool in Procurement , the need to identify bottlenecks at an early stage and take targeted countermeasures is becoming apparent in practice. Traditional methods are reaching their limits due to the increasing complexity of global supply chains. There has therefore been a shift towards data-driven, proactive approaches in order to increase supply security and effectively manage risk management.
Old: Traditional bottleneck analysis
Traditional approach: Traditional bottleneck analysis was based on manual processes and experience. Purchasing departments conducted periodic assessments, used simple spreadsheets and relied on personal communication with suppliers. Information about supply bottlenecks was often not recognized until they had already occurred. Limited data transparency led to delayed response times and increased safety stock as a security measure. Challenges such as unforeseen delivery failures or quality problems were difficult to anticipate, leading to production interruptions and increased costs.
New: Predictive analytics
Predictive analytics: Modern approaches rely on predictive analytics to proactively identify bottlenecks. By integrating real-time data from ERP systems, supplier portals and external market data, this method enables a comprehensive analysis of potential risks. Artificial intelligence and machine learning recognize patterns and trends that indicate future bottlenecks. Practical benefits include increased forecasting accuracy and faster decision-making. This enables companies to take countermeasures at an early stage, evaluate alternative sources of supply and optimize strategic stock levels. This leads to a reduction in procurement risks and more efficient use of resources.
Practical example: Application in the electronics industry
A global electronics manufacturer implemented predictive analytics in its procurement process. By evaluating supplier data, market forecasts and internal inventory figures, the company was able to identify potential shortages of rare earths six months in advance. Concrete measures such as the development of strategic partnerships and the diversification of the supplier portfolio led to a 40% reduction in the delivery failure rate. At the same time, warehousing costs were reduced by 15%, resulting in annual savings of over EUR 2 million.
Conclusion on the bottleneck analysis
Bottleneck analysis is an indispensable tool in modern procurement management. It enables bottlenecks to be identified at an early stage, minimizes supply risks and strengthens the company's strategic position. The systematic application and integration of new technologies such as AI and predictive analytics will further increase its importance for successful supply chain management. However, the correct interpretation of the analysis results and the consistent implementation of suitable countermeasures remain crucial for success.
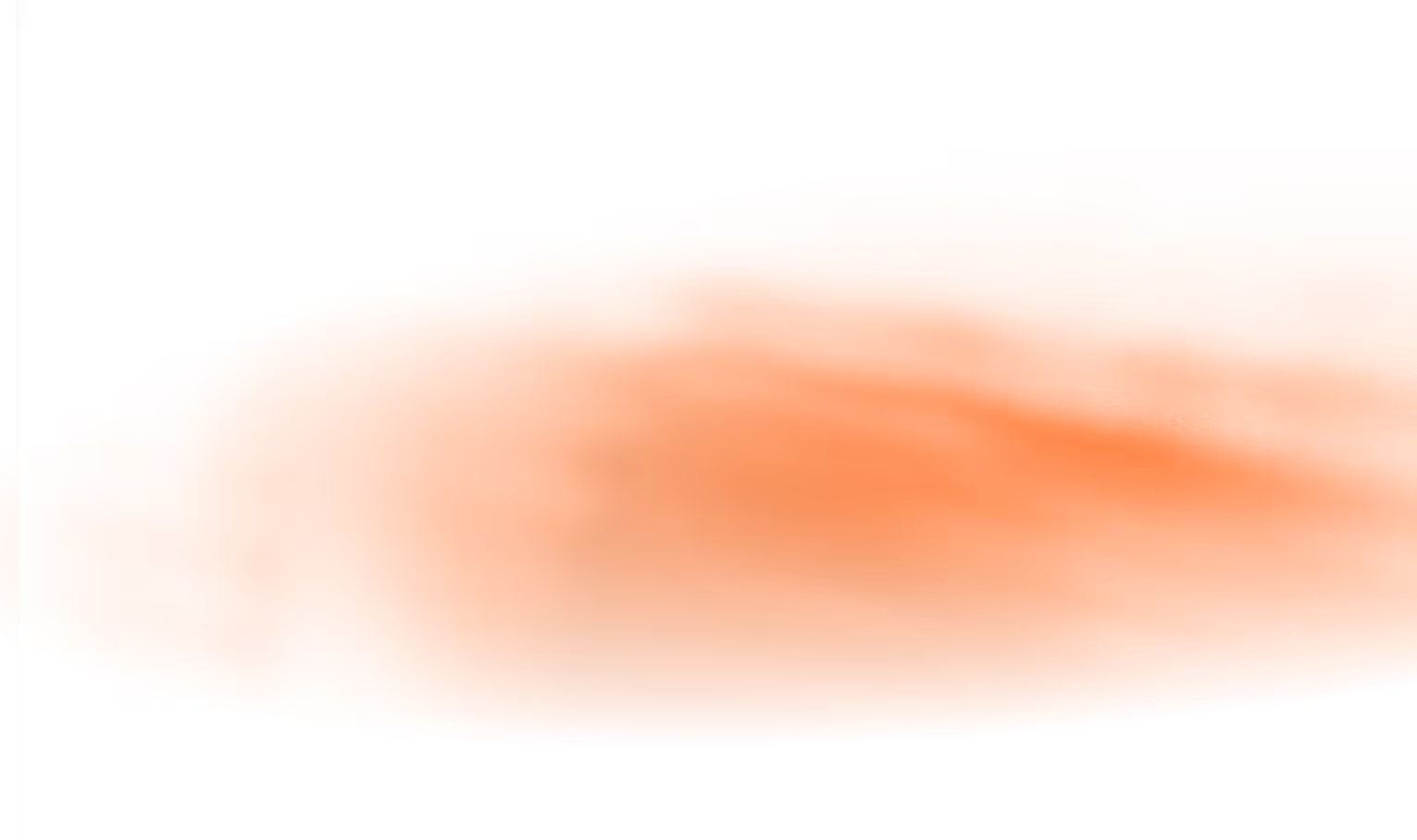
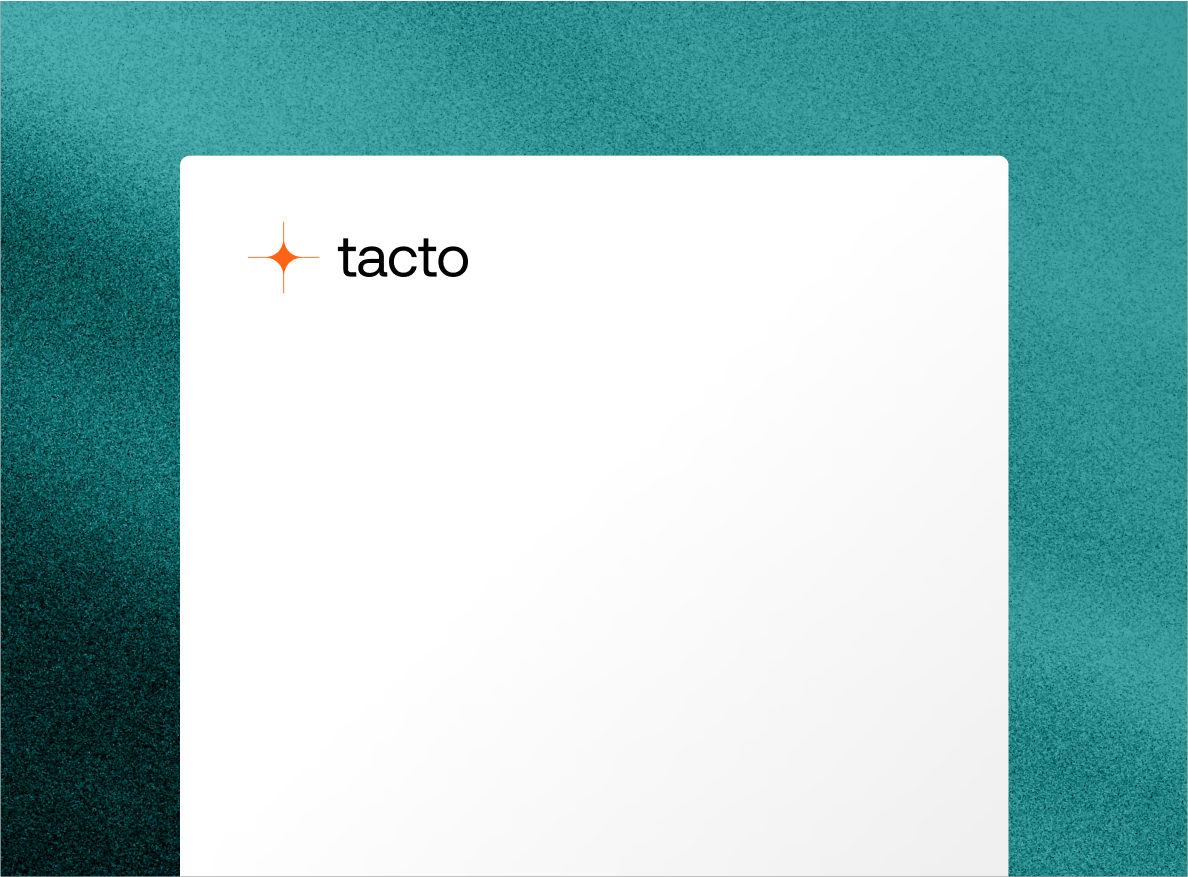