Procurement Glossary
Missing parts management: definition & important aspects for buyers
Missing parts management helps companies to avoid production downtime due to missing components and thus ensures delivery capability in volatile times. This overview provides a structured overview of the most important methods and tools for Procurement in order to proactively identify and effectively manage supply bottlenecks.
Missing parts management in a nutshell:
Missing parts management is a systematic process for identifying, preventing and eliminating material and parts bottlenecks in the supply chain. For Procurement , this is an essential tool for ensuring production capability and avoiding costly production interruptions.
Example: An automotive supplier implements an early warning system that automatically triggers an alarm for critical components if the stock level falls below 5 days' reach, which has reduced the number of production-critical missing parts by 75% within 6 months.
Introduction to missing parts management
Missing parts management is an essential component of modern production and logistics control. It deals with the systematic recording, analysis and avoidance of missing parts in the production process. In times of global supply chains and just-in-time production, the effective management of missing parts is becoming increasingly important. Well-structured missing parts management makes a significant contribution to ensuring production continuity and helps to avoid costly production interruptions. In this guide, you will learn the most important principles, methods and strategies of missing parts management as well as its significance for operational practice.
What is missing parts management?
Missing parts management refers to the systematic planning, management and control of missing or scarce materials and components in the procurement and production process. The aim is to identify material bottlenecks at an early stage and take proactive measures to avoid production downtime and meet delivery deadlines. Information from requirements planning, stock levels and supplier communication is used to ensure a continuous supply of materials.
Core elements of missing parts management
Significance for Procurement
In Procurement , missing parts management is of central importance to ensure the company's ability to deliver and avoid costs caused by production interruptions. Effective missing parts management enables buyers to minimize risks, stabilize the supply chain and increase customer and internal stakeholder satisfaction. It also supports the optimization of ordering processes and helps to increase efficiency throughout the entire procurement process.
Missing parts management: from a reactive approach to predictive analytics
Missing parts management is of central importance in modern production in order to keep supply chains stable and avoid interrupting production processes. Traditionally, a response to missing parts was only made once they had already led to problems. However, in view of complex global supply networks, there is a need to identify missing parts at an early stage and act proactively. Digitalization opens up new opportunities to move from reactive to predictive missing parts management.
Old: Reactive missing parts management
Traditional approach: In traditional missing parts management, companies react to missing parts as soon as they disrupt the production process. They are often identified by manual reports from production or regular stock analysis. Tools such as simple ERP systems or spreadsheets are used for tracking. However, this method is time-consuming and error-prone. There is a lack of real-time information and forecasting capabilities, which can lead to rush purchases, increased costs and production downtime.
New: Predictive analytics in missing parts management
Predictive analytics: The modern approach uses advanced data analysis and AI in Procurement to anticipate missing parts in advance. By processing large volumes of data from ERP systems, supplier information and external data sources, patterns and risk analysis can be identified at an early stage. Real-time monitoring and forecasting models make it possible to identify potential bottlenecks and initiate countermeasures before production stoppages occur. This improves responsiveness, reduces costs and increases the reliability of the supply chain.
Practical example: Implementation at an electronics manufacturer
An international electronics manufacturer used predictive analytics in its missing parts management. By analyzing real-time data and historical supplier performance, the company was able to identify potential missing parts at an early stage. Within a year, the number of missing parts was reduced by 35%, production downtime was cut by 50% and on-time delivery increased by 20%. In addition, urgent procurement costs were reduced by 40%, resulting in significant cost savings.
Conclusion on missing parts management
Missing parts management is an indispensable tool for modern companies to avoid supply bottlenecks and ensure production continuity. Success is based on a combination of proactive monitoring, efficient supplier management and digital solutions. Only through a systematic approach and the use of modern technologies can companies identify material bottlenecks at an early stage and take targeted countermeasures. This not only ensures competitiveness, but also minimizes costly production downtime and increases customer satisfaction.
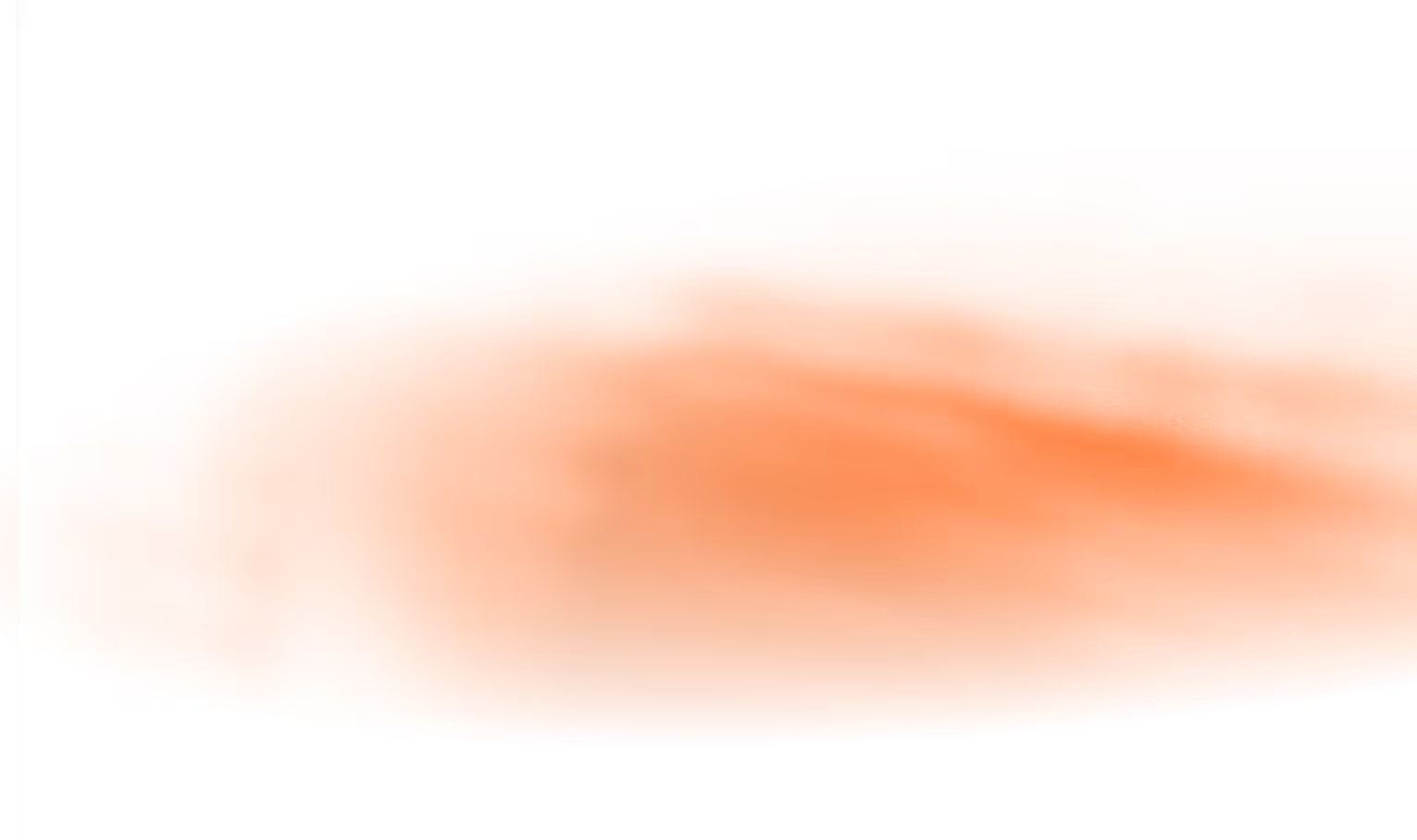
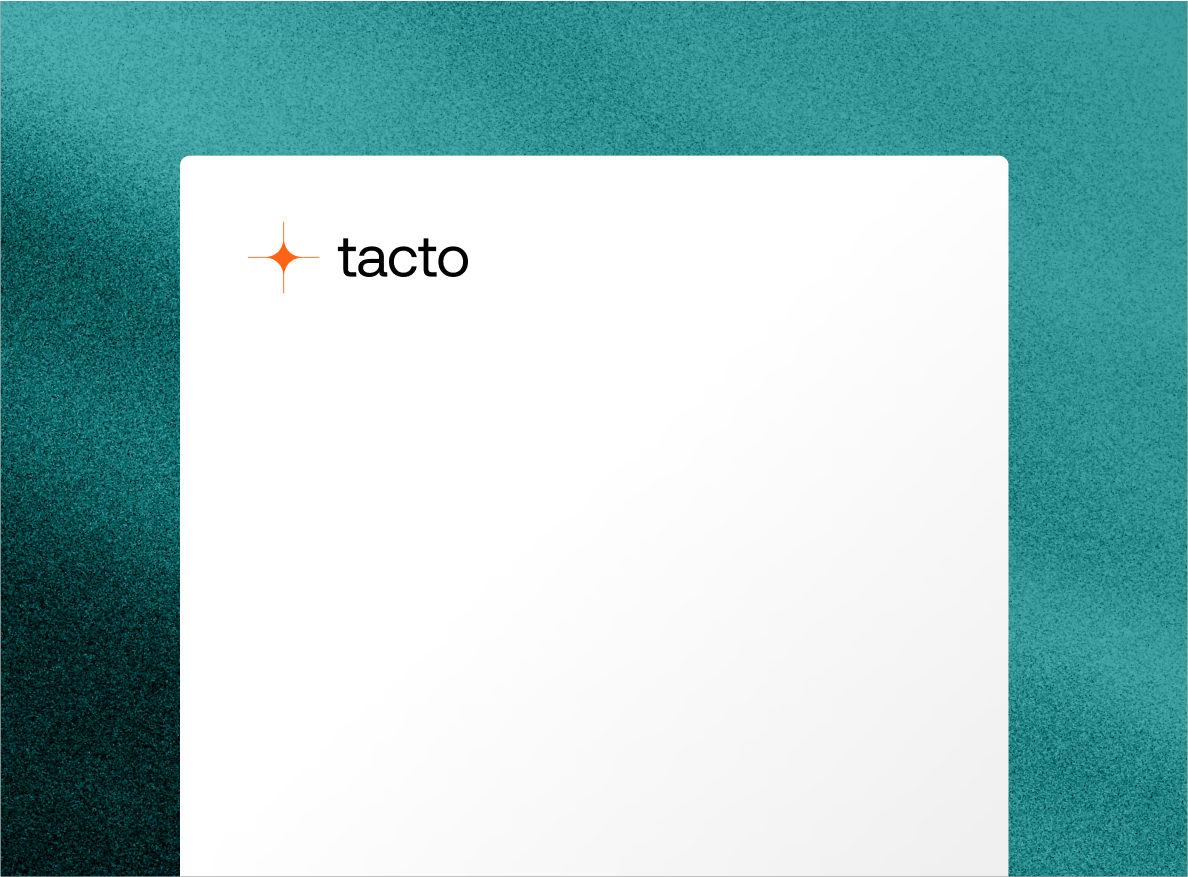