Procurement Glossary
Onshoring: definition & important points for buyers
Onshoring is becoming increasingly important for companies as a strategic option for strengthening supply chains and reducing dependencies. This structured overview shows you the most important aspects and opportunities of onshoring for a future-proof Procurement strategy.
Onshoring in a nutshell:
Onshoring describes the relocation back to the home country of production and procurement activities that were previously outsourced abroad. For Procurement , this means realigning the procurement strategy with a focus on domestic suppliers in order to minimize supply chain risks and benefit from shorter transport routes.
Example: A German automotive supplier relocates its electronic component production from Asia back to Germany in 2023, reducing transportation time from 8 weeks to 5 days, while reducing supply chain complexity by 60%.
Introduction to onshoring
Onshoring is becoming increasingly important in today's globalized business world. It describes the process of relocating production and service activities back to a company's home country after they have previously been relocated abroad. This strategic decision is made by many companies in response to changing economic conditions, rising transportation costs, quality requirements and geopolitical uncertainties. In this guide, we look at the key aspects of onshoring, its pros and cons and the factors that companies need to consider when making the decision to relocate.
What is onshoring?
Onshoring refers to the relocation of production and service processes from abroad back to a company's home country. In contrast to offshoring, where business activities are outsourced abroad, onshoring aims to operate closer to the domestic market, better comply with quality standards and shorten supply chain resilience. This strategy enables companies to react more quickly to local market conditions and optimize costs by reducing logistics.
Core elements of onshoring
Significance for Procurement
Onshoring is becoming increasingly relevant in procurement management as it minimizes risks in the supply chain and increases security of supply. By being close to suppliers, buyers can react more flexibly to market changes and avoid bottlenecks. Onshoring also enables more intensive collaboration with local partners, promotes innovation and supports sustainable procurement strategies by reducing transportation emissions.
Onshoring: From offshoring to local production
Building on the theoretical understanding of onshoring, its practical implementation is becoming increasingly important for companies. Globalized supply chains and the associated risk management have shown that a return to local production sites offers strategic advantages. The need to respond flexibly to market changes and ensure security of supply is driving the shift from traditional offshoring practices to modern onshoring strategies.
Old: Offshoring
Traditional approach:
In the past, many companies relied on offshoring by outsourcing production and services to countries with lower labor costs. In practice, this meant relocating production facilities to Asia or Eastern Europe in order to achieve cost savings. Tools such as global ERP systems and international logistics networks were used to manage the complex processes. However, long delivery times, quality problems and cultural differences led to considerable challenges. In addition, risks increased due to political instability and currency fluctuations, which limited the agility of the companies.
New: Onshoring
Onshoring:
The modern onshoring approach relies on the relocation of production processes back to the home country or nearby regions. By investing in automation and modern production technologies, cost disadvantages compared to offshore locations can be reduced. Proximity to the market enables faster response times and individualized products. In practical terms, companies benefit from reduced transportation costs, lower inventory costs and improved quality control. In addition, government incentives and the increasing importance of sustainability make onshoring more attractive.
Practical example: Automotive industry in Germany
A leading German car manufacturer decided to relocate the production of an important component from Asia back to Germany. By using Industry 4.0 technologies and robot-assisted manufacturing, production costs were reduced by 15%. Delivery times were reduced by 50%, which led to optimized warehousing and faster market launches. Quality defects were reduced by 30% and CO2 emissions were significantly reduced due to shorter transportation routes. This onshoring project not only strengthened the company's competitiveness, but also contributed to regional economic development.
Conclusion on onshoring
Onshoring is proving to be an important strategic option for companies that want to optimize their supply chains and minimize risks. Despite higher production costs in Germany, the advantages such as shorter delivery times, better quality control and increased security of supply outweigh the disadvantages. Success depends largely on careful supplier selection and well thought-out cost management. Especially in times of global uncertainty, onshoring offers a valuable approach for sustainable and resilient procurement strategies.
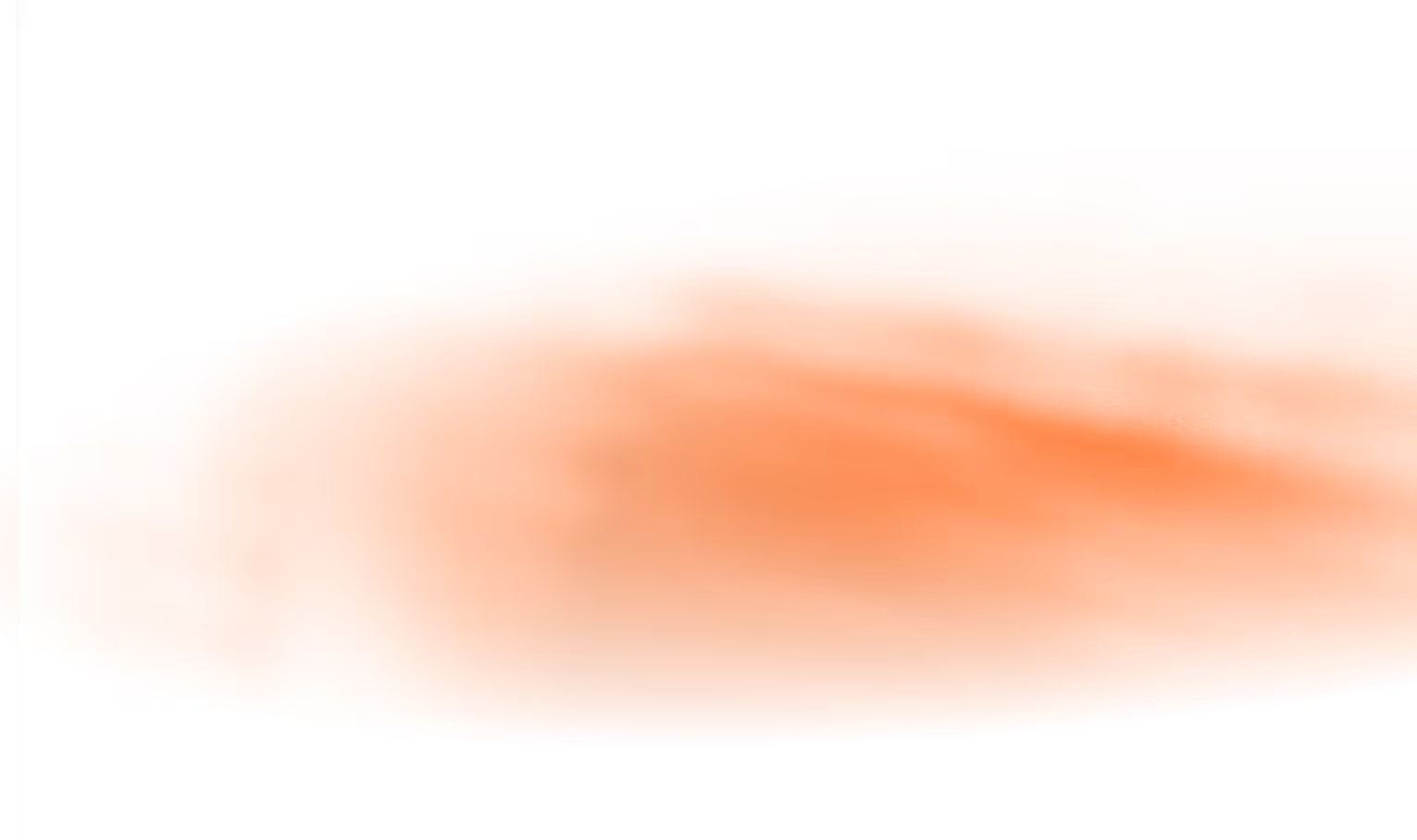
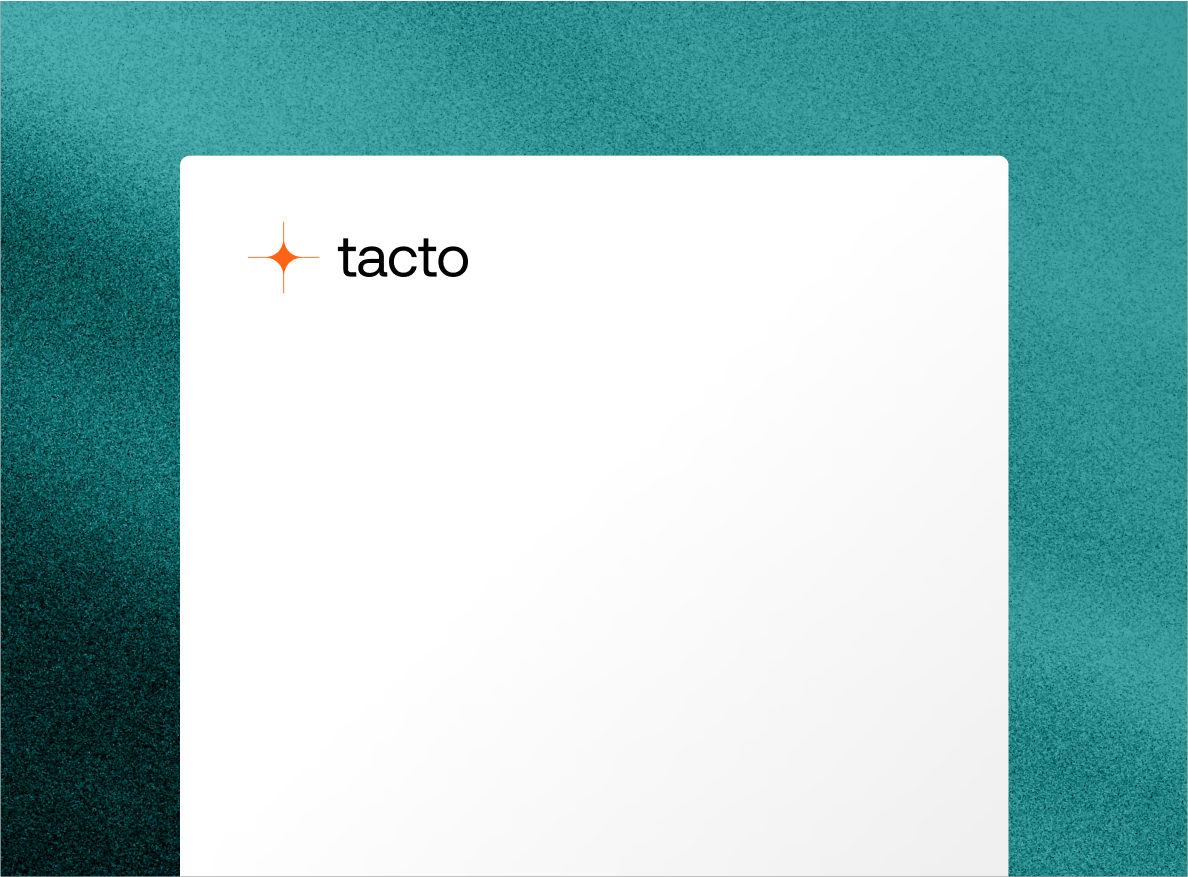