Procurement Glossary
Order process optimization: definition and important aspects for buyers
The optimization of ordering processes increases efficiency in Procurement and at the same time reduces costs and lead times in companies. This structured overview shows you how you can professionalize your ordering processes through systematic improvements and achieve measurable success.
Order process optimization in a nutshell:
Order process optimization describes the systematic analysis and improvement of all activities in the procurement process, from the identification of requirements to the settlement of invoices. For Procurement , this enables shorter throughput times, reduced process costs and a higher quality of procurement processes.
Example: By introducing a digitalized order workflow with automatic requirement notification and electronic invoice processing, an automotive supplier reduced the processing time of its orders from an average of 5 days to 1.5 days and lowered the process costs per order from 85 to 32 euros.
Order process optimization: An introduction
Order process optimization is an important part of modern supply chain management and aims to improve the efficiency and effectiveness of procurement processes in companies. At a time when global supply chains are becoming ever more complex and cost pressure is constantly increasing, the systematic optimization of ordering processes is becoming increasingly important. By implementing suitable strategies and using modern technologies, companies can streamline their ordering processes, shorten lead times and reduce costs. This guide provides a comprehensive overview of the various aspects of ordering process optimization, from the analysis of existing processes to the successful implementation of improvement measures.
What is order process optimization?
Order process optimization refers to the systematic improvement of all steps within the purchasing process in order to increase efficiency, reduce costs and minimize errors. By analyzing and redesigning workflows, companies can speed up the procurement process, conserve resources and optimize cooperation with suppliers. The aim is to make the entire process as efficient and transparent as possible, from determining requirements to ordering and checking incoming goods.
Core elements of order process optimization
Significance for Procurement
Optimizing the ordering process is essential for Procurement , as it directly influences the efficiency and costs of procurement. An optimized process makes it possible to react more quickly to requirements, reduce stock levels and negotiate better conditions with suppliers. It also promotes transparency and traceability of all ordering processes, which supports compliance and risk minimization within the company.
Order process optimization: From manual Procurement to e-procurement
In today's globalized and digitalized economy, order process optimization is a decisive factor for the success of companies. Building on the theoretical foundations, it shows how important efficient procurement processes are for cost savings and competitiveness. In practice, the shift from traditional to modern methods is leading to significant improvements. There is a growing need to transform outdated manual processes and replace them with digital solutions in order to fully exploit efficiency potential.
Old: Manual ordering process
Traditional approach: In the traditional ordering process, requirements are often recorded manually and forwarded to the purchasing department by paper form or e-mail. The order is entered into the system manually and communication with suppliers is done by phone or fax. This process is time-consuming and prone to errors such as duplicate orders or incorrect quantities. Manual data transfer leads to media disruptions and there is a lack of transparency and real-time information. In addition, approval processes are often slow, which leads to delays and increased stock levels.
New: E-Procurement
E-procurement: The modern approach integrates electronic procurement systems that digitize and automate the entire ordering process. Requirement notifications are recorded directly in the system and automatically forwarded for approval using preconfigured workflows. Orders are transmitted electronically to supplier management, and feedback such as order confirmations or shipping notifications are seamlessly integrated into the system. E-procurement reduces order processing time by up to 60% and process costs can be cut by 30%. The real-time availability of data enables better control and strategic decisions. In addition, the direct connection of suppliers increases transparency and strengthens relationships in supply chain management.
Practical example: Introduction of e-procurement at Müller GmbH
Müller GmbH, a medium-sized mechanical engineering company, was faced with the challenge of modernizing its manual ordering processes. By implementing an e-procurement system, the company was able to reduce the order processing time from an average of 4 days to just a few hours. Procurement process costs were reduced by 25% and transparency across all procurement processes was significantly increased. Errors in orders were reduced by 50% and stock levels were cut by 15% thanks to more precise requirements planning. The improved data situation also enabled more successful negotiations with suppliers, which led to further cost savings.
Conclusion on order process optimization
Order process optimization is an indispensable part of modern business processes. Systematic digitalization, standardization and automation can lead to significant increases in efficiency and cost savings. Success depends largely on the consistent implementation of core elements, the integration of digital systems and the involvement of all stakeholders. Future technologies such as AI and blockchain will continue to drive optimization opportunities and set new standards in procurement.
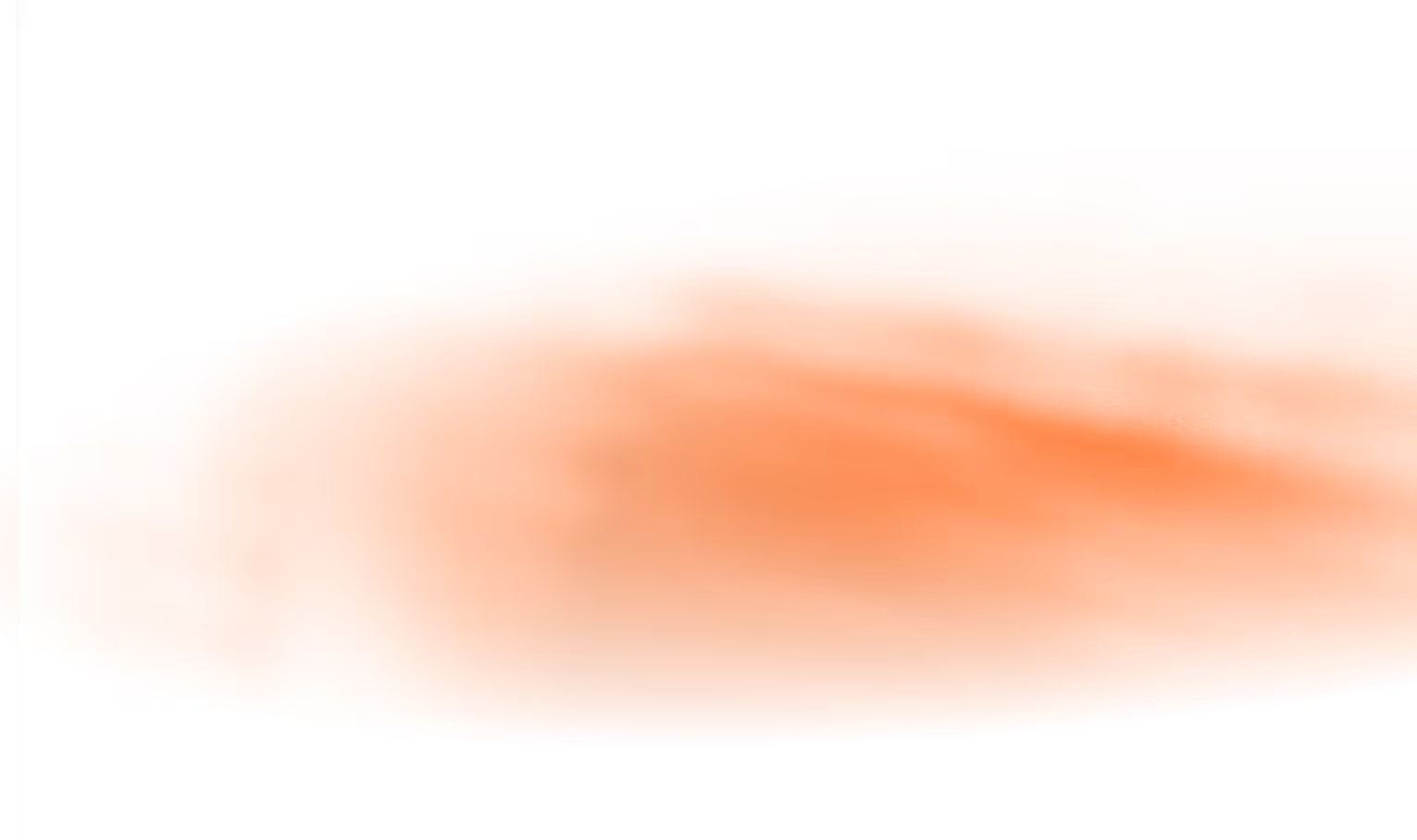
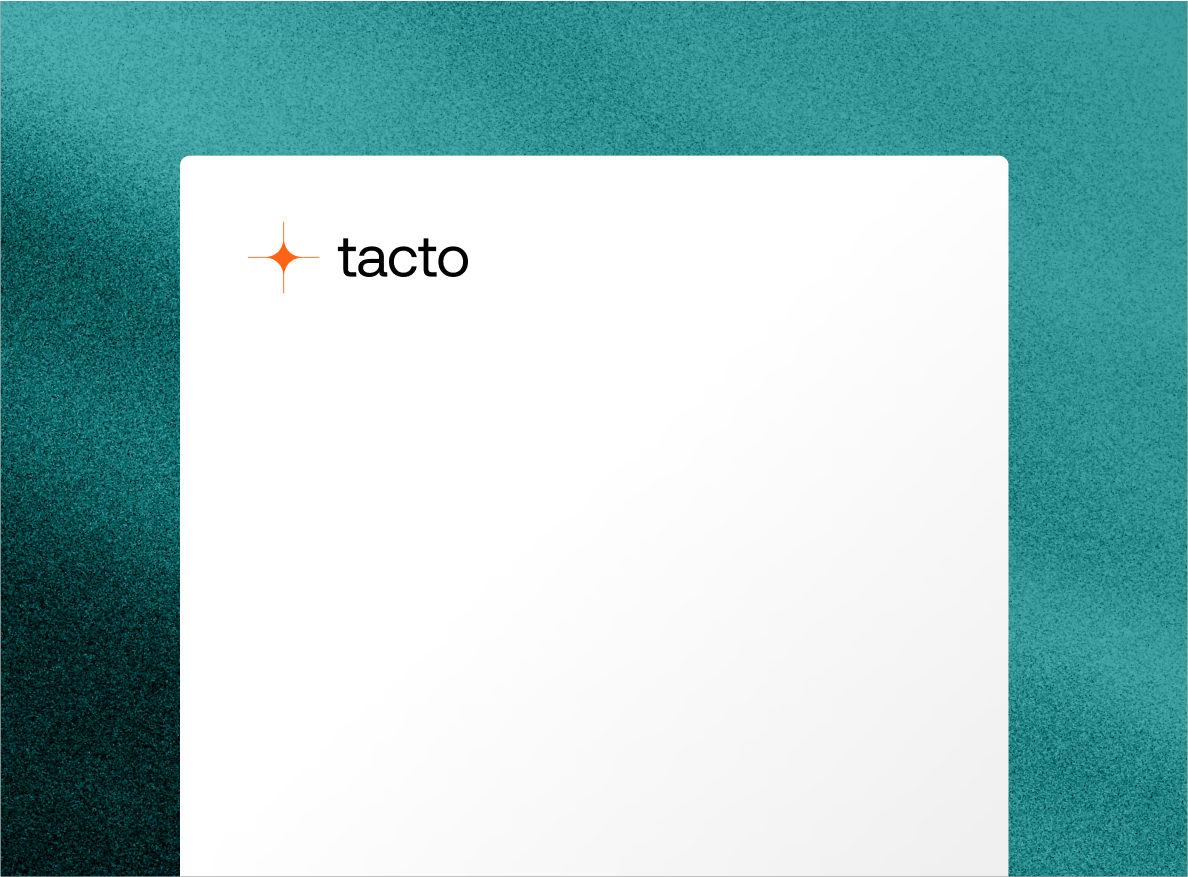