Procurement Glossary
NAME: Definition & important points for buyers
Critical materials are becoming increasingly strategically important for companies due to supply bottlenecks, geopolitical tensions and the green transformation. This structured overview shows how Procurement can increase security of supply and secure competitive advantages through systematic management of critical materials.
Critical materials brought to the point:
Critical materials are raw materials or components that are essential for production and at the same time have a high supply risk, whether due to limited availability, geopolitical factors or market concentration. Their systematic identification and management is of strategic importance for Procurement in order to ensure security of supply and competitiveness.
Example: An electronics manufacturer identifies rare earths as a critical material, as 85% of global production comes from a single region, and subsequently develops a dual-sourcing strategy with a 6-month stockpile and the qualification of recycling suppliers as an alternative source of supply.
Introduction to purchasing controlling: Critical materials
Critical materials are raw materials and substances that are of great importance for industrial production but are classified as particularly supply-critical due to various factors. The availability of these materials is often jeopardized by geopolitical tensions, limited deposits, concentration of production in a few countries or complex supply chains. In recent years, the importance of critical materials has increased significantly, particularly due to the transformation towards sustainable technologies and digitalization. This introduction highlights the most important aspects of critical materials, their economic relevance and the associated challenges for companies and society.
What are critical materials?
Critical materials are raw materials, components or products whose availability is crucial to a company or industry and where disruptions in supply chain resilience can have a significant impact on production and business operations. These materials are often characterized by limited resources, few alternative suppliers or high dependence on specific geographic regions. Identifying such materials is essential in order to recognize risks at an early stage and take strategic measures to secure supply.
Core elements of critical materials
- Rare availability: Materials that are only available in limited quantities or are difficult to mine
- High supplier dependency: limited number of suppliers or monopolies on the market
- Strategic importance: Indispensability for the production of core products or services
- Risky origin: Procurement from politically or economically unstable regions
Significance for Procurement
Control over critical materials plays a central role in procurement management. Buyers must ensure that these materials are always available in order to avoid production downtime and maintain the company's competitiveness. This requires proactive risk management, diversification of the supplier base and close cooperation with strategic partners.
- Security of supply: ensuring a continuous supply of materials despite market uncertainties
- Risk minimization: Identification and reduction of procurement risks through diversification
- Cost control: avoidance of price peaks through long-term contracts and market analysis
- Strategic partnerships: Building relationships with suppliers for better negotiating positions
Critical materials: From traditional risk management to strategic criticality management
Building on the theoretical understanding of critical materials, it is clear that global networking and the growing complexity of supply chains bring with them new challenges. The practical importance lies in minimizing security of supply and ensuring continuity of production. A change from the traditional, reactive approach to a proactive and strategic approach is therefore essential in order to meet the increased requirements.
Old: Traditional risk management
Traditional approach: In traditional risk management, critical materials were often managed through simple procurement strategies. Companies relied on existing supplier relationships and reactive measures in the event of disruptions. Typical tools included basic supplier evaluation and the maintenance of safety stock to mitigate supply shortages. Key characteristics of this approach were limited market visibility and a lack of long-term strategies. This led to challenges such as unexpected price increases, delivery delays and increased vulnerability to global market changes.
New: Strategic Criticality Management
Strategic Criticality Management: This modern approach integrates strategic planning and management of critical materials into company processes. By using advanced analytics and digital platforms, companies gain deeper insights into their supply chains. Innovation points are the diversification of the supplier portfolio, the implementation of early warning systems and collaboration with suppliers for technological developments. Practical benefits include a reduction in supply risks, better cost control and increased flexibility. This enables companies to react proactively to market changes and increase their competitiveness.
Conclusion on the security of supply of critical materials
Dealing with critical materials requires systematic and forward-looking management. By combining risk diversification, strategic partnerships and innovative technology solutions, companies can strengthen their security of supply in the long term. The development of recycling concepts and alternative materials in particular will become increasingly important in the future. Only those who actively tackle these challenges and invest in future-proof solutions will be able to remain competitive in the long term.
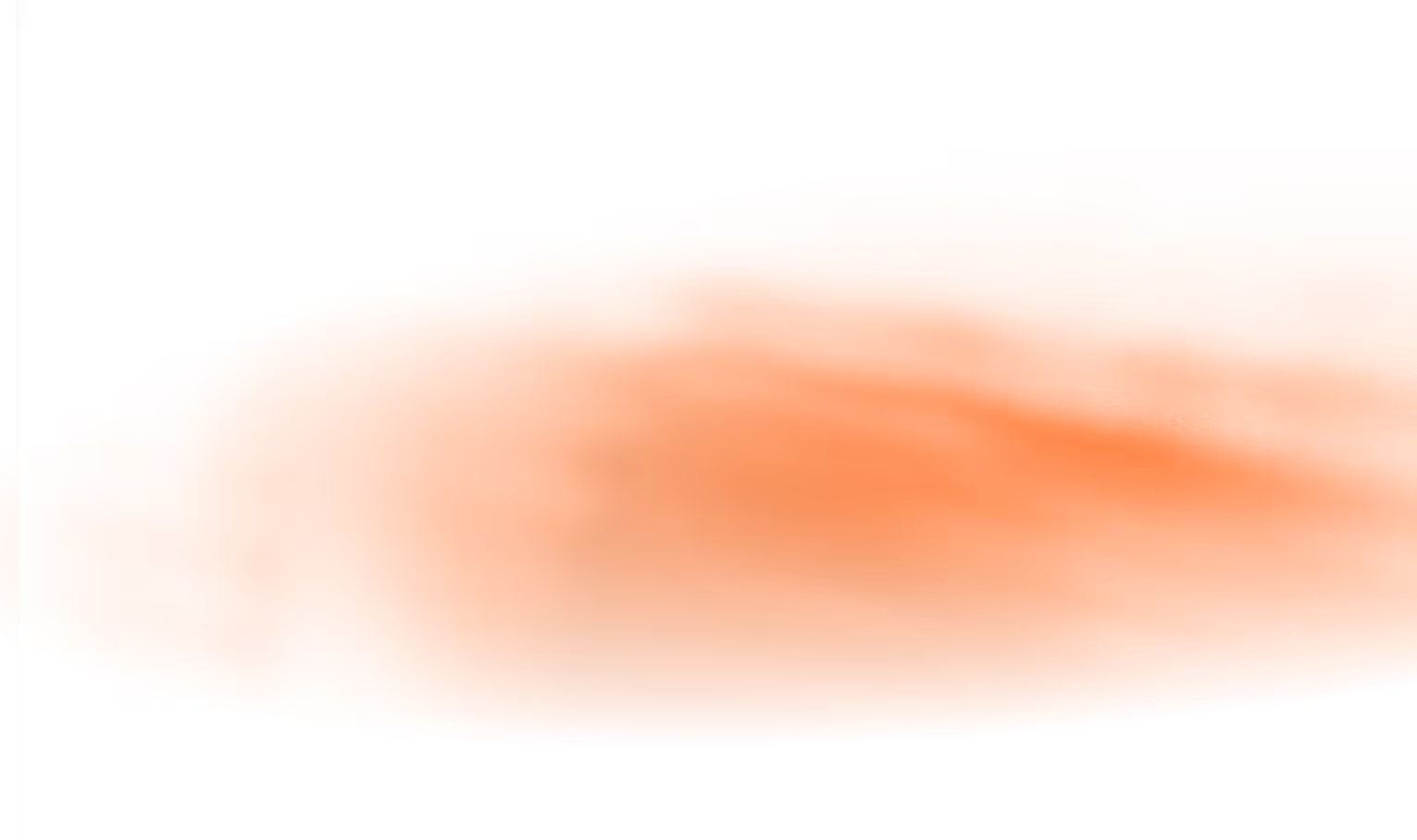
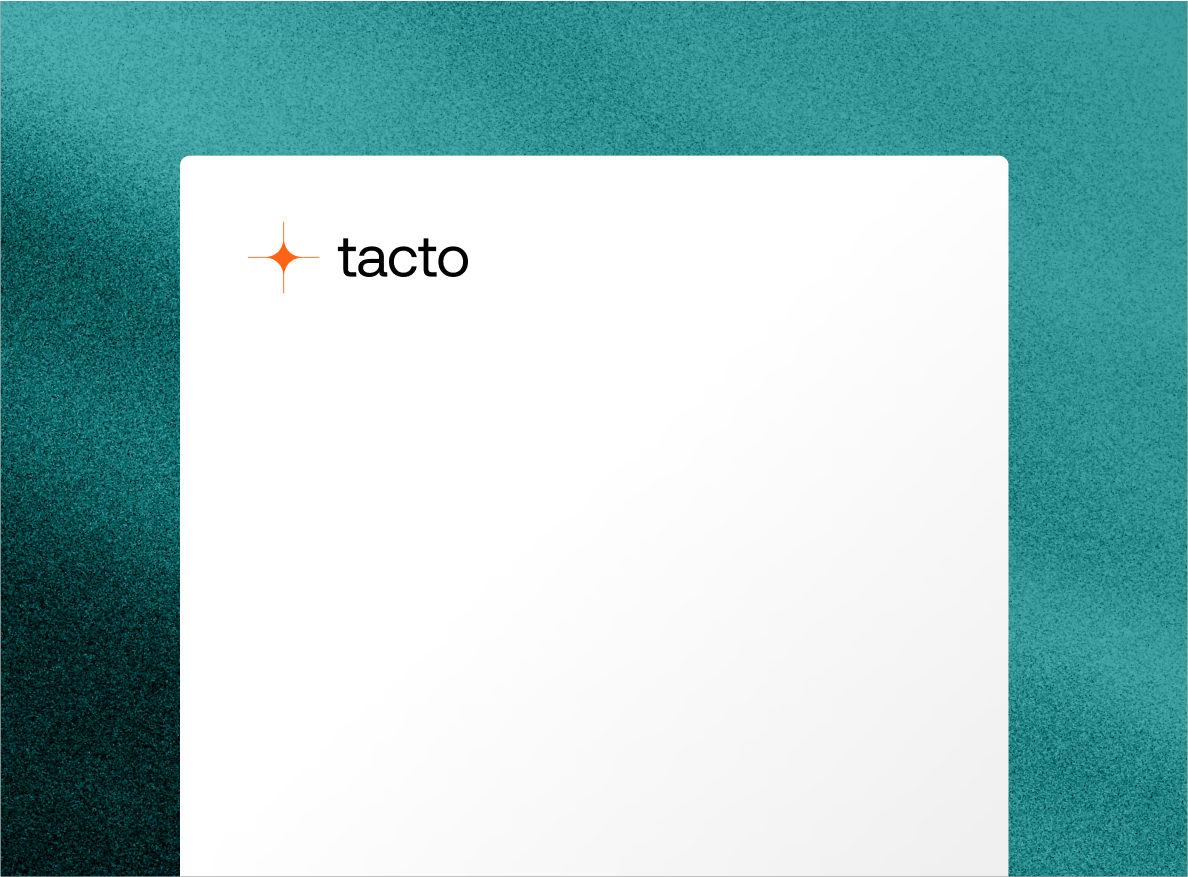