Procurement Glossary
Supplier risk: definition & important aspects for buyers
Supplier risks jeopardize the security of supply and can have a massive impact on a company's success. This structured overview shows you the most important risk factors and provides tried-and-tested methods for effective risk management in Procurement.
Supplier risk in a nutshell:
Supplier risk describes the danger of disruptions or failures in the supply chain due to financial, operational or external factors on the supplier side. Systematic management of these risks is essential for Procurement in order to ensure security of supply and minimize potential damage to the company.
Example: An automotive manufacturer identifies a high risk of default at a critical electronics component supplier due to poor financial ratios and develops a dual sourcing strategy within 6 months, allowing production to continue without interruption in the event of the supplier's subsequent insolvency.
Supplier risk: effective management for stable procurement
Supplier risk is a key challenge for companies in today's globalized business world. It describes the potential dangers and uncertainties that can arise from working with suppliers. From delivery failures and quality defects to compliance violations - the range of possible risks is diverse and can have a significant impact on business activities. Effective supplier risk management is therefore essential for maintaining stable supply chains and ensuring competitiveness. This overview highlights the most important aspects of supplier risk and presents strategies for risk identification, assessment and minimization.
What is supplier risk?
Supplier risk refers to the potential dangers and uncertainties that can arise from working with suppliers. These risks can include financial losses, interruptions in the supply chain, quality problems or reputational damage. Reasons for this can include supplier defaults, insolvencies, political unrest or breaches of compliance guidelines. Understanding supplier risk is crucial in order to take proactive measures to manage risk and ensure security of supply.
Core elements of supplier risk management
Significance for Procurement
In Procurement , the management of supplier risks is essential to ensure the continuity of business processes and avoid financial losses. A proactive approach makes it possible to identify disruptions at an early stage and take countermeasures. This enables buyers to keep supply chains stable, control costs and build long-term relationships with reliable partners.
Supplier risk: from manual risk management to integrated supplier risk management
Building on the theoretical foundation, the effective management of supplier risk is crucial in practice. In a globalized economy with complex supply chains, unforeseen risks can have a significant impact on business performance. Traditional approaches to risk analysis are reaching their limits, highlighting the need for modern, integrated solutions.
Old: Manual supplier risk management
Traditional approach: Traditionally, companies have managed supplier risk through manual processes and periodic assessments. Risk assessment was often based on personal relationships and subjective assessments, supported by simple tools such as spreadsheets. Information was updated sporadically, resulting in outdated data. This approach was time-consuming and inefficient as it did not allow for real-time monitoring. In addition, the ability to react to acute risks was limited, which could lead to unexpected supply bottlenecks and quality problems.
New: Integrated Supplier Risk Management
Supplier risk management: Modern companies are implementing digital solutions for integrated supplier risk management. By using specialized software, data from various sources is aggregated and analyzed in real time. Key innovations include the use of big data and artificial intelligence to predict potential risks. This allows companies to act proactively instead of just reacting to events. Practical benefits include increased transparency along the entire supply chain, faster decision-making processes and the ability to mitigate risks at an early stage. This leads to a more stable supply and long-term cost savings.
Practical example: Implementation at an electronics manufacturer
A global electronics manufacturer implemented an integrated supplier risk management system. Through the real-time monitoring of over 500 supplier selection worldwide, potential risks were identified at an early stage. This enabled the company to react to the impending insolvency of a key supplier and find alternative sources in good time. This prevented production stoppages and saved an estimated 10 million euros in potential losses. In addition, the supplier evaluation by 15% through continuous monitoring and feedback.
Conclusion on supplier risk assessment
Supplier risk management is an indispensable part of modern procurement strategies. The systematic identification, assessment and management of risks enables companies to make their supply chains robust and future-proof. By using digital technologies and preventative measures, companies can identify disruptions at an early stage and take effective countermeasures. The key to success lies in the continuous further development of risk management processes and the skilful balance between risk minimization and economic efficiency.
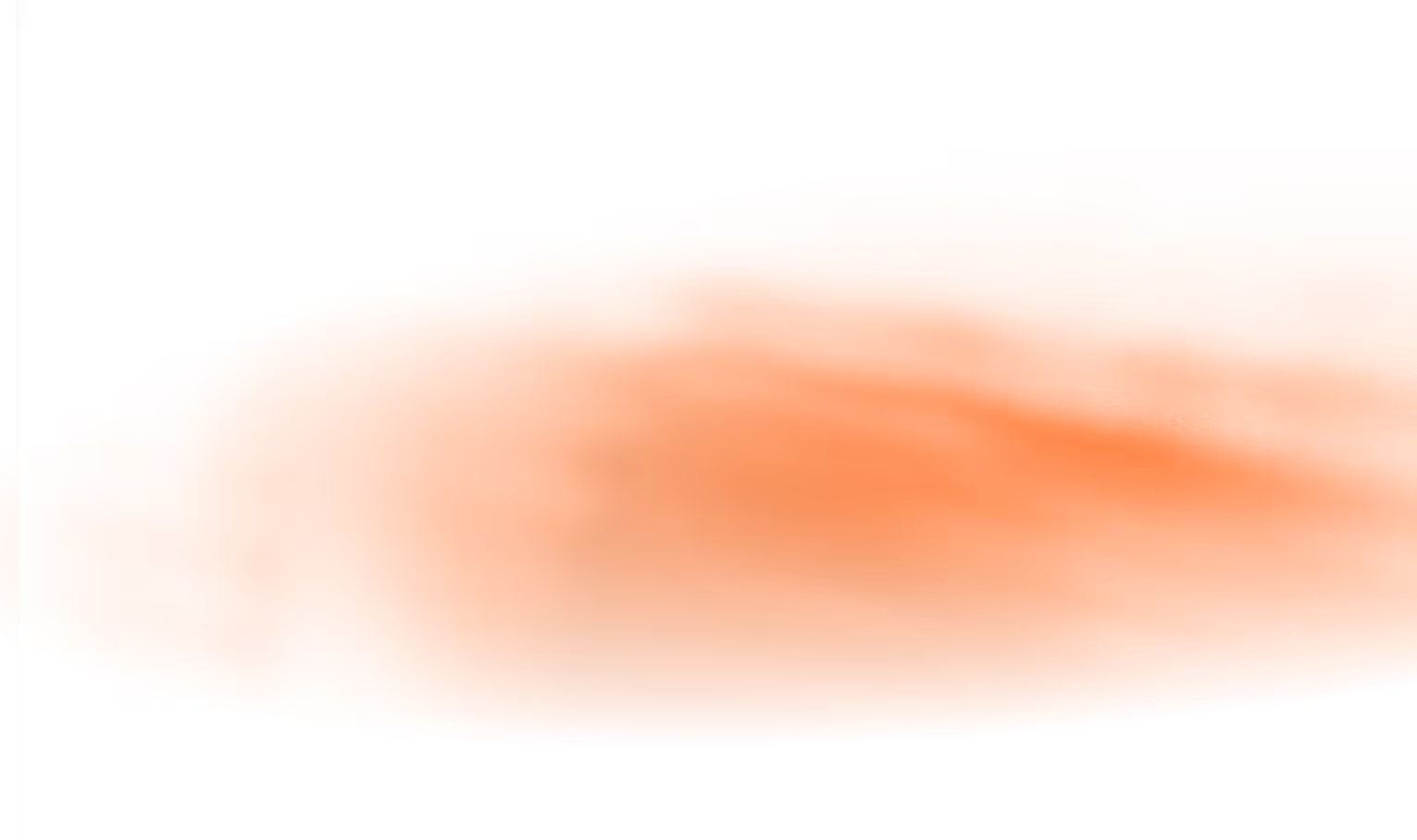
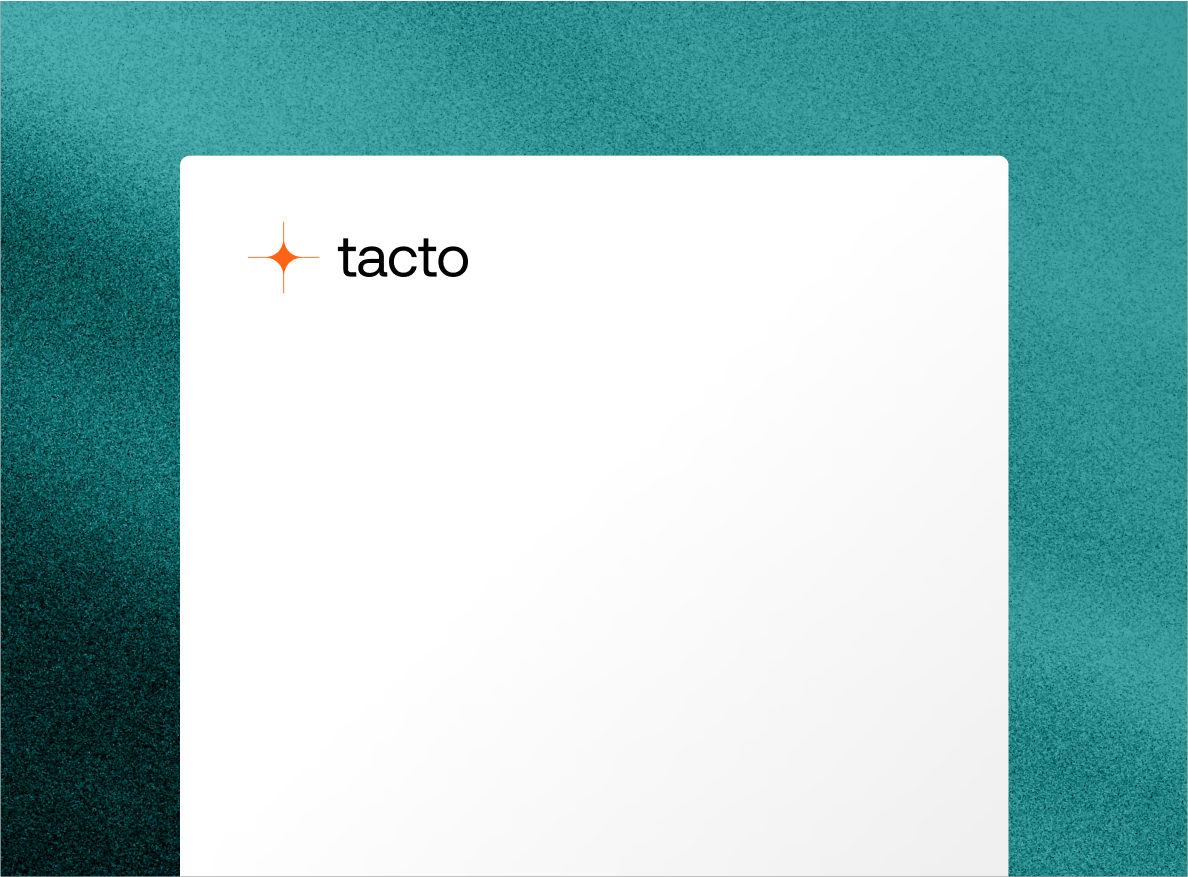